Share this
Sustainable 3D Printing: Create and Use Recycled Filament
by Louis Rinaldo on Aug 30, 2023 2:10:30 PM
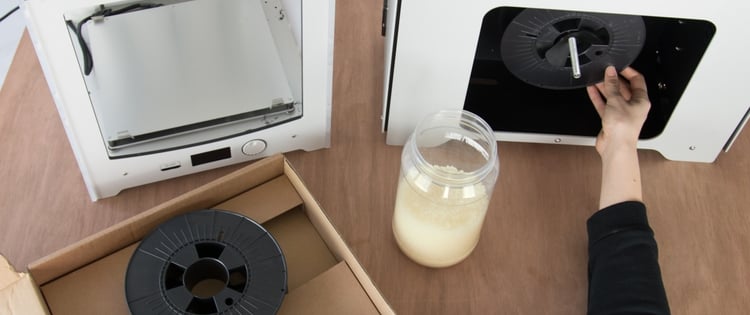
The 3D printing industry is increasingly embracing sustainability, with recycled filament emerging as a key player in reducing environmental impact. In fact, it is estimated that as much as 30% of plastic used in 3D printing becomes waste. By transforming this waste plastic into high-quality FDM filament, we can significantly cut down on plastic pollution while also enjoying cost savings. In this blog, we explore the journey of recycled plastic in sustainable 3D printing and how it contributes to a greener future.
Sustainability in 3D printing is more than a trend—it's a necessity. As global plastic production reaches unprecedented levels, the need for eco-friendly solutions has never been greater. Over 400 million tons of plastic waste is generated each year, and only about 9% of it is recycled. The rest ends up in landfills, incinerated, or polluting the environment. Recycled 3D filament plays a crucial role in this shift, offering a viable alternative to virgin plastics. By adopting sustainable practices, companies can not only reduce their carbon footprint but also position themselves as leaders in the growing green economy.
Understanding Filament
Before we dive deeper into the process, it is essential to understand what filament is. Filament is the raw material used in FDM (Fused Deposition Modeling) 3D printers. FDM is the most common 3D printing method used for creating physical objects from digital models. The filament used in this process is typically made of thermoplastic materials, such as PLA (Polylactic Acid) and ABS (Acrylonitrile Butadiene Styrene), or PETG (Polyethylene Terephthalate Glycol). It is also important to understand the characteristics of different thermoplastics. PLA, for instance, is biodegradable and made from renewable resources like corn starch or sugar cane. However, ABS is petroleum-based, stronger, and more flexible but emits fumes when melted. PETG is a variant of PET, it is glycol-modified for extra durability and is considered food-safe, but it can be sensitive to moisture. Knowing these properties will help you decide what type of plastic to recycle and how to handle them during the 3D printing process.
Filament comes in spools of various colors and thicknesses, typically with a diameter of 1.75mm or 2.85mm. During the 3D printing process, the filament is heated and extruded through a nozzle onto a build plate, layer by layer, to create a 3D object. The build plate and the nozzle move in a coordinated fashion, guided by the printer’s software, to create the desired shape.
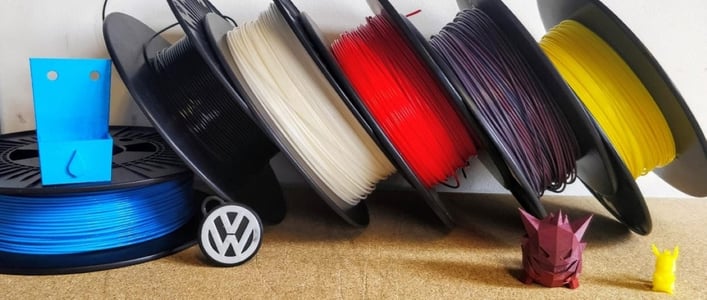
Recycling Plastics into Filament
Not all plastics are suitable for filament recycling. Plastics with a clear recycling symbol (usually with a number) are better candidates. For example, PET, commonly found in plastic bottles; PLA, often used in disposable tableware; and ABS, frequently used in hard plastic items, can be recycled into filament. It’s important to research and identify the types of plastics that can be effectively recycled in your setup.
Remarkably, this process allows us to give a second life to a variety of everyday items. Imagine transforming discarded plastic bottles, old production plastics, or even failed 3D prints into brand-new objects. This not only contributes to a reduction in waste but also enables creativity and innovation.
At 3devo, we have developed our own Plastic Shredder and Filament Maker that streamline this process, transforming plastic waste into valuable recyclable filament. These innovative tools empower individuals and businesses to contribute to environmental sustainability by recycling and reusing plastics that would otherwise end up in landfills.
Different plastics have different melting temperatures and characteristics. PLA, for example, typically extrudes at temperatures between 180-220°C, whereas ABS extrudes at higher temperatures, usually between 220-250°C. Therefore, it is important to sort the plastics by type before shredding and extruding them into filament. The filament maker from 3devo has precision temperature control to ensure the plastics are melted at the correct temperature, preventing degradation of the material.
The diameter of the filament is also crucial for successful 3D printing. Most 3D printers use filament with a diameter of 1.75mm or 2.85mm. The 3devo Filament Maker allows you to precisely control the diameter of the filament during the extrusion process, ensuring it is consistent throughout the spool. A variation in diameter, even as small as 0.05mm, can lead to under-extrusion or over-extrusion, affecting the print quality.
Recycled filament offers numerous advantages, from reducing environmental impact to cutting costs.
- Environmental Benefits: By using recycled materials, we divert plastic from landfills and oceans, promoting a circular economy.
- Cost Savings: Recycled filament is often more affordable than virgin materials, making it ideal for large-scale production.
- Material Versatility: Recycled filament can be customized to meet specific project requirements, offering flexibility without compromising quality.
While using recycled filament has its challenges, innovative solutions are emerging. For example, the process of recycling SLS powder into 3D printing filament, as detailed in our blog on SLS powder recycling, highlights how even powder waste from MJF technology can be repurposed effectively. A prime example of successful recycling is showcased in our case study with AZ3D, where they utilized recycled MJF powder to create new, high-quality filament, demonstrating the potential for closed-loop recycling in 3D printing.
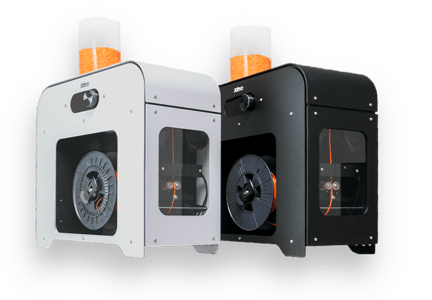
Getting Started: The Testing Phase
As you prepare to 3D print something with recycled filament, we advise you to start by testing a small 3D print first. Extruding filament from recycled plastics may yield slightly different properties compared to conventional filament. By conducting a trial run, you can begin to understand how the recycled filament behaves, ensuring you're well-prepared for 3D printing your desired objects.
It is advisable to use a caliper to measure the filament diameter at multiple points along its length to ensure consistency. Also, perform a bend test by bending the filament at a 90-degree angle. A good-quality filament will bend without breaking. If the filament snaps, it may indicate that the material is too brittle or that it was extruded at an incorrect temperature. Here are some other aspects of this you need to understand:
Embracing the Experimentation Phase
Just as filament extrusion involves a degree of experimentation, so does 3D printing. It's important to approach this phase with an open mind and patience. Remember, the path to perfection is often paved with trial and error. Don't be disheartened if your initial prints don't meet your expectations. Embrace the learning process and relish the joy of creating, even among the occasional challenges.
Understanding Filament Texture
Before you dive into 3D printing, take a moment to assess your filament's texture. Consistency is key; your filament should exhibit an even and round texture throughout its length. Inconsistencies in texture can lead to printing issues. If you notice any irregularities, consider revisiting the filament extrusion process. Our material expert, Timo, has shared insights into achieving optimal filament extrusion in a helpful video guide that you can check out at the end of this blog.
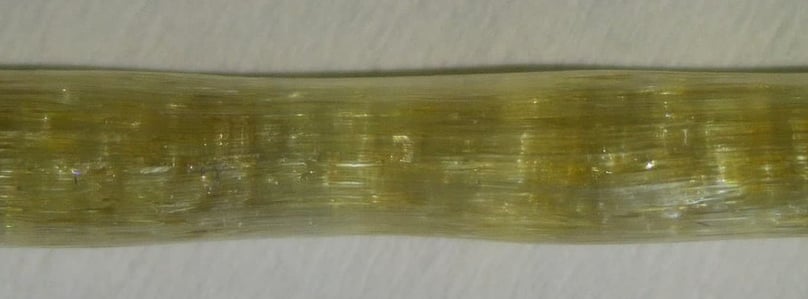
Temperature and Printing Settings
Achieving successful 3D prints heavily relies on accurate temperature and printing settings. Different plastic materials respond uniquely to heat; finding the optimal balance is crucial. Setting the temperature too high can lead to uneven melting, resulting in subpar print quality. Leverage online resources to identify the appropriate settings for your chosen recycled filament.
The optimal printing temperature may vary slightly depending on the 3D printer and the specific characteristics of the recycled filament. For example, the optimal printing temperature for commercial PLA filament is usually between 190-220°C. Still, recycled PLA may require a slightly higher or lower temperature due to impurities or changes in material properties during recycling. It is advisable to start with a temperature in the middle of the range and then adjust it in 5°C increments until the optimal temperature is found.
The layer height and print speed also play a crucial role in the success of a 3D print. A lower layer height will result in a smoother finish but will increase the print time. A higher print speed can lead to under-extrusion and poor layer adhesion. Therefore, finding the right balance between layer height, print speed, and temperature for the specific recycled filament you are using is very important. Also, note that the optimal settings for recycled filament may vary from those of commercial filament, as the recycled filament may contain impurities or have slightly different properties.
Transform Plastic Waste into Your Own Recycled Filament
Contribute to environmental sustainability, reduce waste, and unleash your creativity by transforming plastic waste into your own recycled filament.
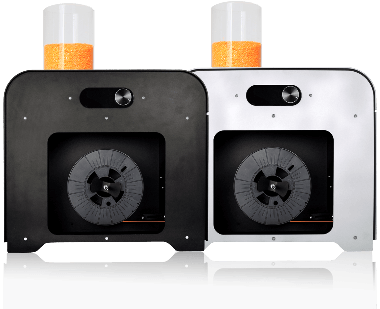
Filament Storage
Once the filament is made, it is essential to store it properly to maintain its quality. The filament is hygroscopic, meaning it absorbs moisture from the air. This is especially true for PLA and PETG. Absorbed moisture can lead to poor print quality and can cause the filament to become brittle. Therefore, storing the filament in a dry, cool place, preferably in a sealed bag with desiccant, is advisable. Before printing, it is also advisable to dry the filament in a filament dryer or an oven at a low temperature (e.g., 50°C for PLA) for several hours to remove any absorbed moisture.
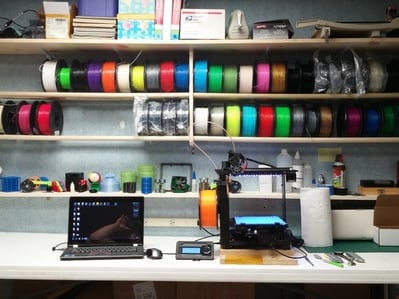
Begin 3D printing
Armed with a test print, a solid understanding of filament texture, an experimental mindset, and calibrated temperature settings, you're now ready to embark on your 3D printing adventure. Remember, the 3D printing community is a supportive and collaborative space. Sharing your creations on social media is gratifying and provides an opportunity to connect with fellow enthusiasts. Don't forget to tag us – we're genuinely excited to witness your innovative endeavors.
Selecting Your First Project
Choosing your first project is an exciting moment. Start with something simple and functional, as this will allow you to focus on the printing process rather than the intricacies of a complex design. When choosing your first project, consider the properties of the recycled filament. Some materials are more brittle and may not be suitable for functional parts that need to withstand stress. Others may have a lower melting point and may not be suitable for objects that will be exposed to high temperatures. Use your knowledge of the material properties to select a suitable project for your recycled filament.
Monitoring the Print
It's important to closely monitor the print, especially during the initial layers, as this will set the foundation for the rest of the print. Make necessary adjustments if you observe any warping or adhesion issues. Most 3D printers come with software that allows you to make real-time adjustments to settings such as temperature and print speed.
In addition to monitoring the initial layers, it is also important to monitor the entire print. Some common printing issues to look out for include warping, where the corners of the print lift off the build plate; stringing, where thin strands of filament form between parts of the print; and layer separation, where the layers of the print do not adequately adhere to each other. Each of these issues can be addressed by adjusting the printer settings, such as the bed temperature, print speed, or retraction settings.
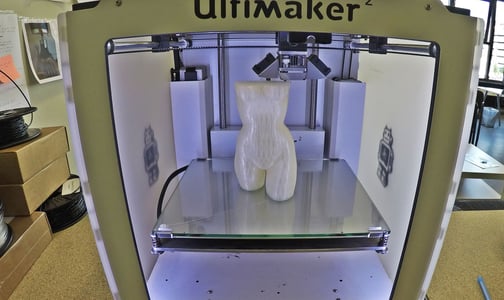
Post-Printing Process
Once the printing is complete, carefully remove the print from the build plate. Some prints may require additional post-processing, such as sanding, painting, or assembling multiple parts. Take your time during this stage to ensure a high-quality finish.
Reflect and Improve
After completing your first print, take some time to reflect on the process. What went well? What could be improved? Make notes of any adjustments that need to be made to the printer settings or the filament extrusion process. Each print is a learning opportunity; you will gain more confidence and expertise with each print.
In addition to reflecting on the printer settings and filament extrusion process, it is also important to consider the source material. Did the recycled filament contain too many impurities? Was it sufficiently dry before extrusion? Did the mixed plastic types affect the filament properties? These considerations will help you refine your recycling and 3D printing process for future projects.
Remember, practice makes perfect. The more you print, the more you will learn about the nuances of your 3D printer and the characteristics of the recycled filament. And most importantly, have fun! 3D printing is not only a rewarding and environmentally friendly hobby but also a gateway to endless creativity and innovation.
Future Developments
As the 3D printing industry embraces sustainability, future trends like bio-based filaments, enhanced 3D printing recycling technologies, and closed-loop systems are becoming increasingly prominent. 3devo's Filament Makers are designed to adapt to these innovations, allowing users to experiment with new materials such as algae-based polymers and refined recycling processes. By integrating these advancements with 3devo's technology, innovators can stay at the forefront of sustainable manufacturing, ensuring consistent quality and expanding the possibilities of eco-friendly 3D printing.
3devo Filament Makers allow (and encourage!) users to experiment with new materials and incorporate cutting-edge recycling technologies into their workflows effortlessly.
Conclusion
In conclusion, the journey towards sustainable 3D printing is one filled with challenges and learning opportunities. From understanding the types of plastics that can be recycled to shredding, extruding, and finally printing with the recycled filament, each step is crucial and requires attention to detail. We have learned the importance of testing and experimentation, the need for careful monitoring of the print, and the value of post-processing and reflection. As we move forward, let us remember the importance of this work. By recycling plastics and turning them into valuable filament, we are not only reducing waste but also contributing to a more sustainable and innovative future. Let us continue experimenting, learning, and sharing our knowledge with the community. Together, we can make a difference.
Frequently Asked Questions (FAQs)
Not all plastics are suitable for filament recycling. Plastics with a clear recycling symbol (usually with a number) are better candidates. Plastics like PET, PLA, ABS, and others can be recycled into filament. However, it's important to research and identify the types of plastics that can be effectively recycled in your setup.
Printing with recycled filament may present some challenges, such as adhesion issues, variations in layer bonding, or differences in print quality. These challenges can be addressed through experimentation, adjusting printing settings, and refining the filament extrusion process. Patience and persistence are key.
Yes, temperature settings for recycled filament might differ from those of conventional filament due to variations in material properties. It's recommended to start with manufacturer-recommended settings and then fine-tune them based on your printing experience. Online resources and community forums can provide valuable insights.
Yes, it's possible to mix recycled filament with virgin filament. However, keep in mind that the properties and characteristics of the resulting print might vary depending on the ratio of recycled to virgin filament. Experimentation will help you find the right balance for your specific projects.
Yes, failed 3D prints can be recycled into filament, aligning with the philosophy of minimizing waste. However, it's important to ensure that the failed prints are made from recyclable plastics and are free from contaminants that could affect the quality of the filament.
Absolutely, specialized equipment is essential for successfully recycling plastic waste into 3D printing filament. If you're in search of efficient and professional solutions for plastic shredding and filament making, we are pleased to introduce you to our GP20 Plastic Shredder and Filament Extruder.
Our GP20 Plastic Shredder is meticulously engineered to optimize the shredding process, transforming plastic waste into shreds suitable for filament extrusion. Simultaneously, our Filament Maker is designed to convert those shreds or plastic pellets into high-quality recycled filament. Both pieces of equipment are crafted with precision and innovation, making them indispensable tools for your journey toward creating recycled filament. With user-friendly features and robust performance, they ensure your plastic waste is effectively processed and converted into recycled filament, a topic we've extensively covered in this blog.
As you embark on your sustainable 3D printing adventure, our GP20 Plastic Shredder and Filament Maker stand as testaments to our commitment to empowering individuals and businesses with the tools necessary to positively impact the environment. Discover how this innovative duo can revolutionize your approach to filament recycling and enhance your contribution to a greener future.
Begin Your Journey Towards Sustainable 3D Printing
Start by transforming plastic waste into recyclable material with our efficient and innovative shredder, designed to empower your filament recycling journey.
.jpg?width=865&height=500&name=GP20-Shredder-Hybrid-1%20(2).jpg)
Explore More on Sustainable 3D Printing Materials
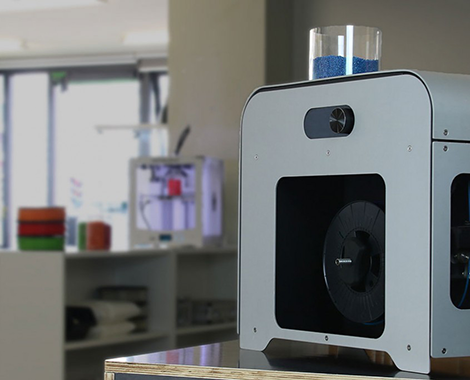
Recycle Plastic Waste
Transform plastic waste into quality 3D printing filament and join our mission for responsible innovation with 3devo's complete recycling solution.
%20-%20instasize.png?width=800&height=640&name=which-plastics-are-recyclable%20(1)%20-%20instasize.png)
Which Plastics are recyclable?
Understand different plastic types and their recyclability to make informed decisions on selecting the right material for your needs.
%20-%20instasize%20(1).png?width=800&height=640&name=PETG-e1494958102567%20(1)%20-%20instasize%20(1).png)
How to recycle PET into Filament?
Discover how PET plastic is transformed into eco-friendly 3D printing filaments on our dedicated Recycling PET page.
Share this
- March 2025 (1)
- January 2025 (1)
- December 2024 (2)
- November 2024 (3)
- October 2024 (4)
- September 2024 (2)
- August 2024 (3)
- July 2024 (6)
- June 2024 (3)
- May 2024 (2)
- April 2024 (1)
- March 2024 (1)
- January 2024 (1)
- November 2023 (2)
- October 2023 (5)
- September 2023 (2)
- August 2023 (1)
- July 2023 (1)
- May 2023 (1)
- December 2022 (3)
- August 2022 (1)
- June 2022 (1)
- May 2022 (2)
- April 2022 (2)
- March 2022 (7)
- February 2022 (2)
- January 2022 (3)
- December 2021 (3)
- November 2021 (3)
- October 2021 (2)
- September 2021 (3)
- August 2021 (3)
- July 2021 (2)
- June 2021 (1)
- March 2021 (1)
- October 2020 (1)
- June 2020 (1)
- May 2020 (1)
- April 2020 (4)
- November 2019 (1)
- July 2019 (2)
- June 2019 (1)
- May 2019 (1)
- March 2019 (1)
- November 2018 (1)
- September 2018 (1)
- January 2018 (1)
- October 2017 (1)
- September 2017 (1)
- July 2017 (1)
- June 2017 (1)
- May 2017 (1)
- January 2017 (1)
- December 2016 (3)
- November 2016 (2)
- October 2016 (1)
- May 2016 (2)
- August 2015 (2)
- July 2015 (1)