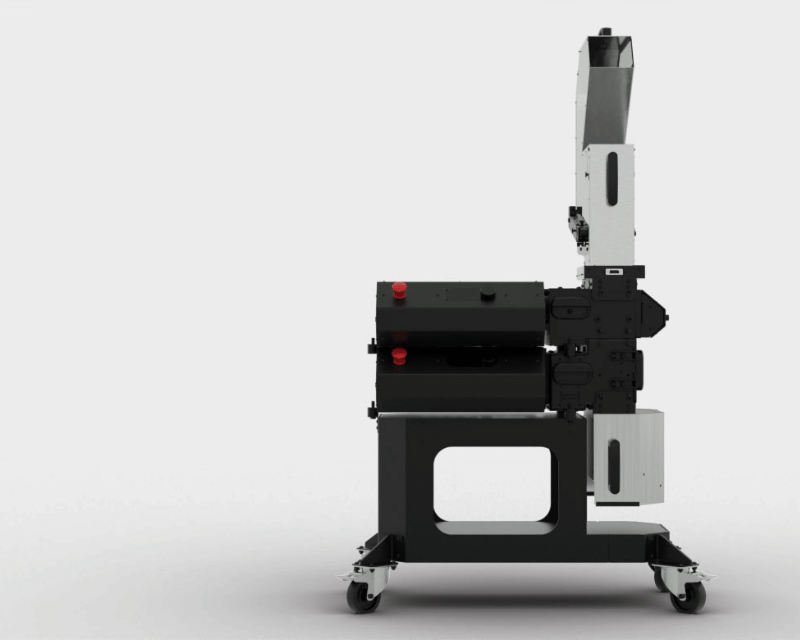
GP20 Plastic Shredder
Recycle plastic of any shape and size into granulate-size 3D printing material.
The GP20 combines a high-torque shredder with an integrated granulator to process plastic waste into uniform regrinds. Its modular setup and compact size offers flexibility for seamless integration into a wide range of material workflows and industries.
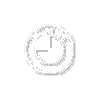
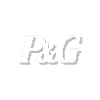
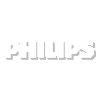
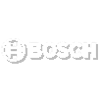
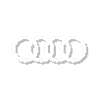
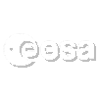
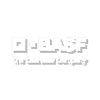
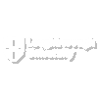
Key Features
High Precision
Swappable Blades
User Safety
Intuitive Design
Smart features, such as the intelligent feeding system, are powered by the machine's software.
Design of the GP20 Plastic Shredder
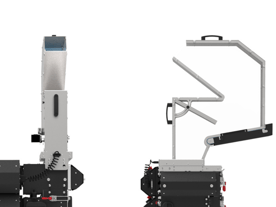
GP20 Hopper
The hopper is precisely designed for efficient and safe operation. Its robust design allows for smooth feeding of a variety of thermoplastics, making it ideal for high volume shredding jobs.
The optimised shape of the hopper minimises the risk of clogging, ensuring a smooth flow of materials into the shredder.
In addition, the plastic shredder has an intelligent feed system that automatically adjusts the feed rate for optimum performance.
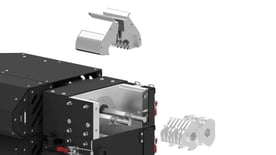
Shredder Unit
The shredder is engineered for precision and efficiency, making it an essential tool for recycling various thermoplastic materials. It features swappable blades with different numbers of teeth, allowing for efficient and effective cutting of plastics of various sizes.
With a total of 14 blades, the plastic shredder offers combinations of 2, 3, and 7 teeth blades to cater to specific shredding requirements.

Granulator Unit
The GP20 granulator is a highly efficient unit designed to grind plastic waste into uniform flakes. Featuring a 3-blade rotor and a 3.5mm filter screen, it ensures that the granulated material is of optimal size for filament production.
The blades provide consistent particle size, making the material ideal for further processing or direct reuse in the Filament Maker.
The granulator operates seamlessly with the shredder or as a standalone unit, offering flexibility and versatility in recycling operations.
GP20 Container
The container is designed to safely hold and transport crushed and granulated materials. Its design and easy-to-use locking mechanism ensures that materials are stored safely during processing.
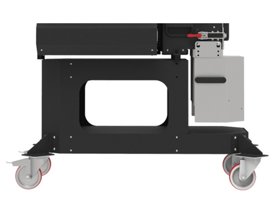
GP20 Trolley
The trolley is a convenient and mobile solution for transporting the shredder and the granulator unit. Designed with durable wheels and a sturdy frame, the trolley allows easy movement within your workspace.
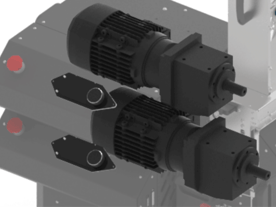
GP20 Motor
Both of the units are powered by two motor, each delivering 750 watts, for a combined total of 1500 watts.
One engine is dedicated to the shredder, while the other powers the granulator. This dual-engine configuration ensures that both units operate at optimal efficiency, providing consistent and reliable performance during brutal plastic recycling and production tasks.
Advanced Features
Dual Design
This dual design combines our intelligent plastic shredder with an integrated granulator, allowing you to focus on what you need. Recycling plastic of any shape and size into granulate-size 3D printing material. The functionality of the GP20 Plastic Shredder gives you the freedom and flexibility to incorporate it into any project within any industry.
Intelligent Settings
As the user, you can tailor the GP20’s settings specifically to your needs. The smart sensors work together to automate several manual operations:
- Smart Feeding: The material input belt automatically matches the processing speed of the GP20.
- Smart Troubleshooting: The knives can automatically reverse and continue to assure continuous processing.
- Smart Control: The temperature control sensor measures the processing temperature to eliminate material melting.
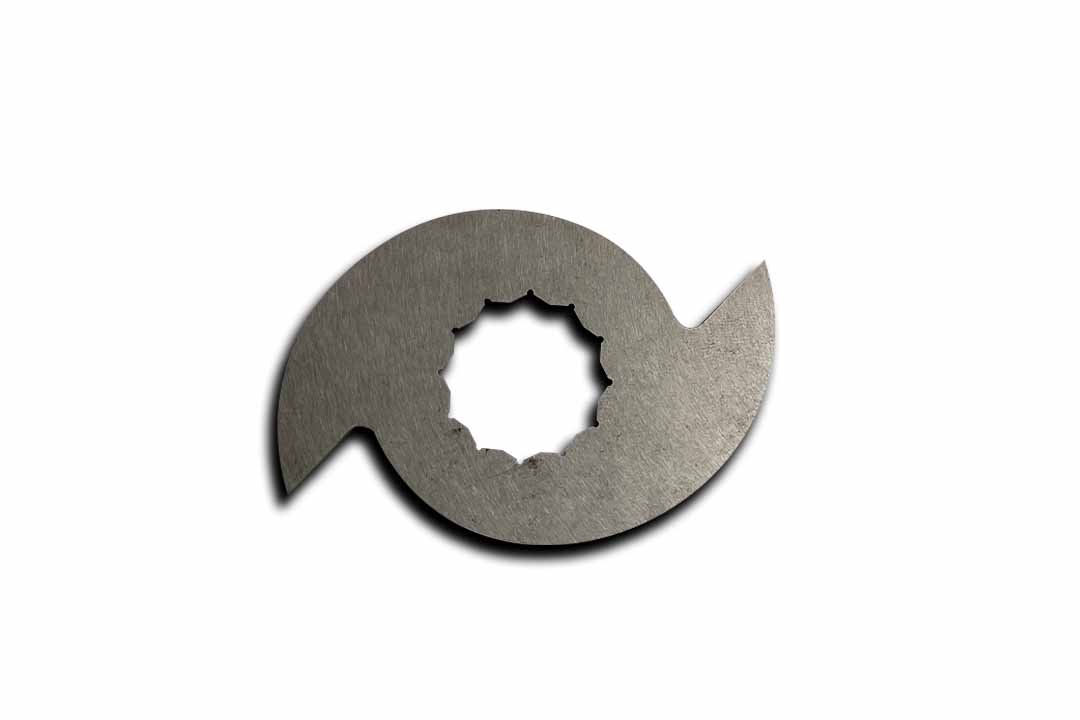
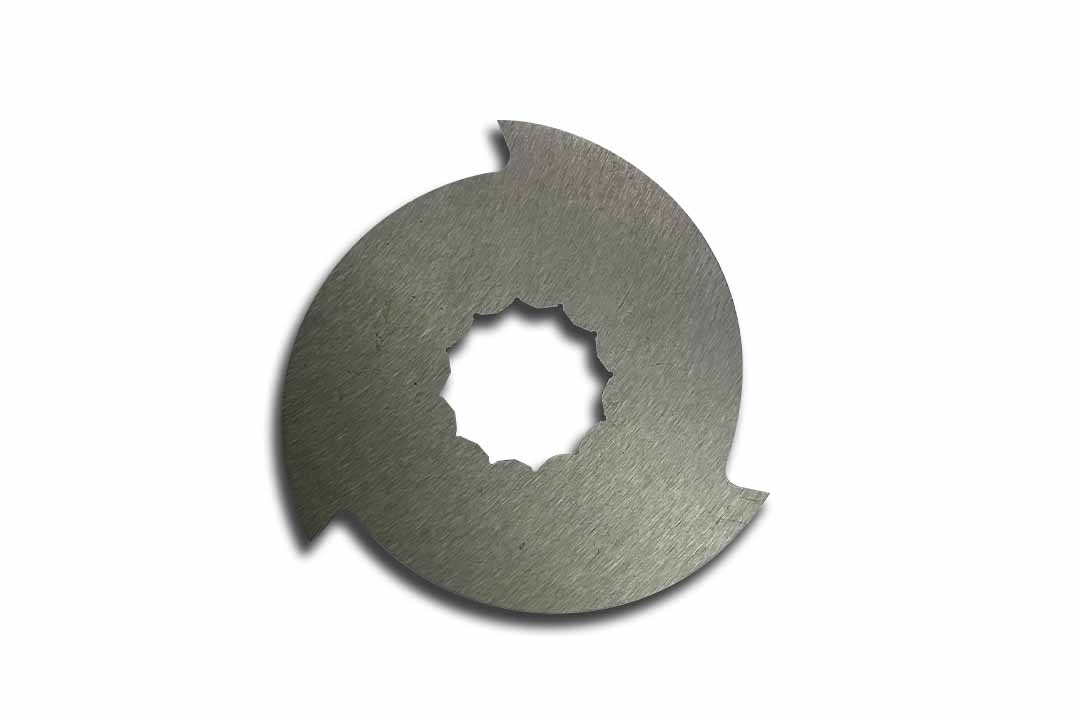
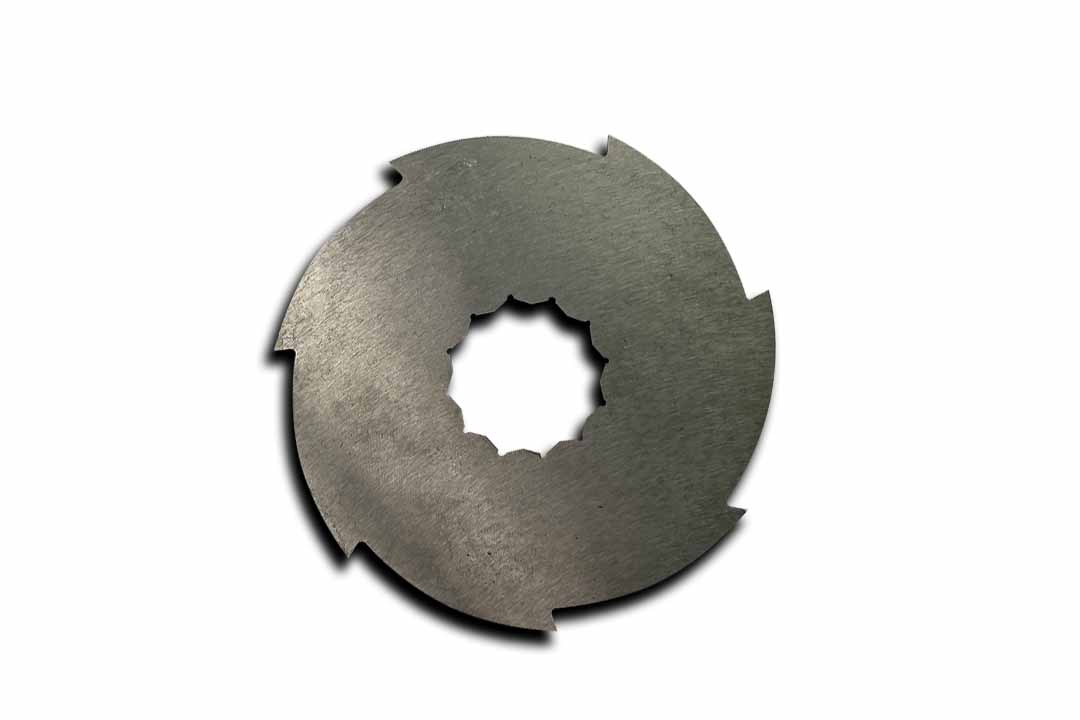
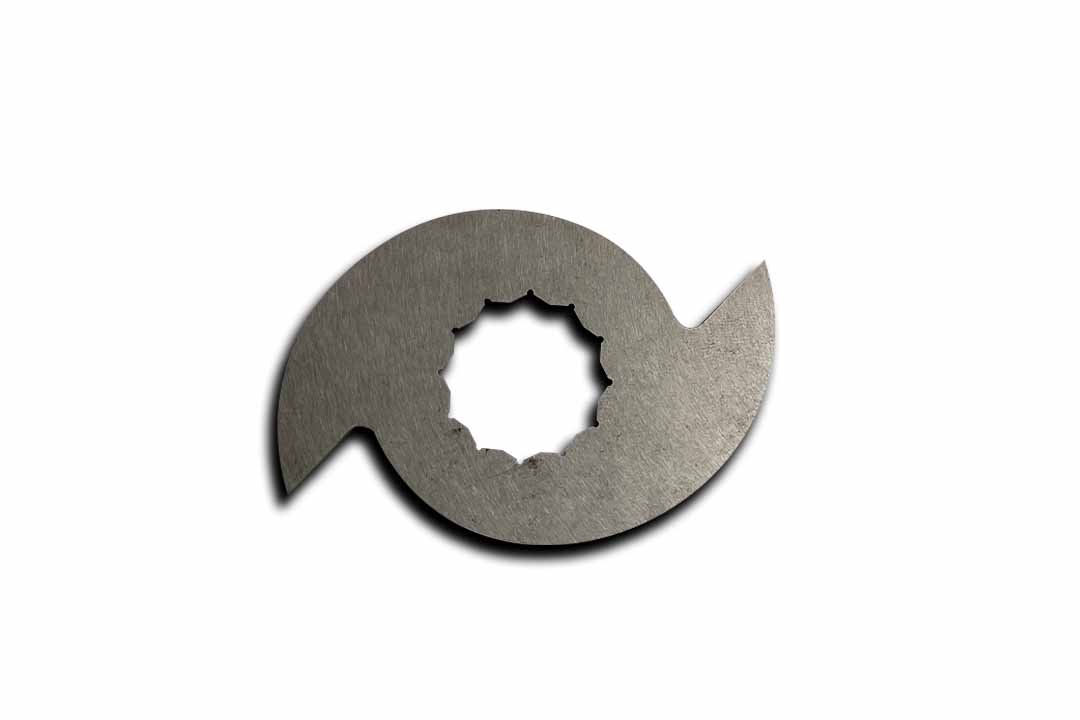
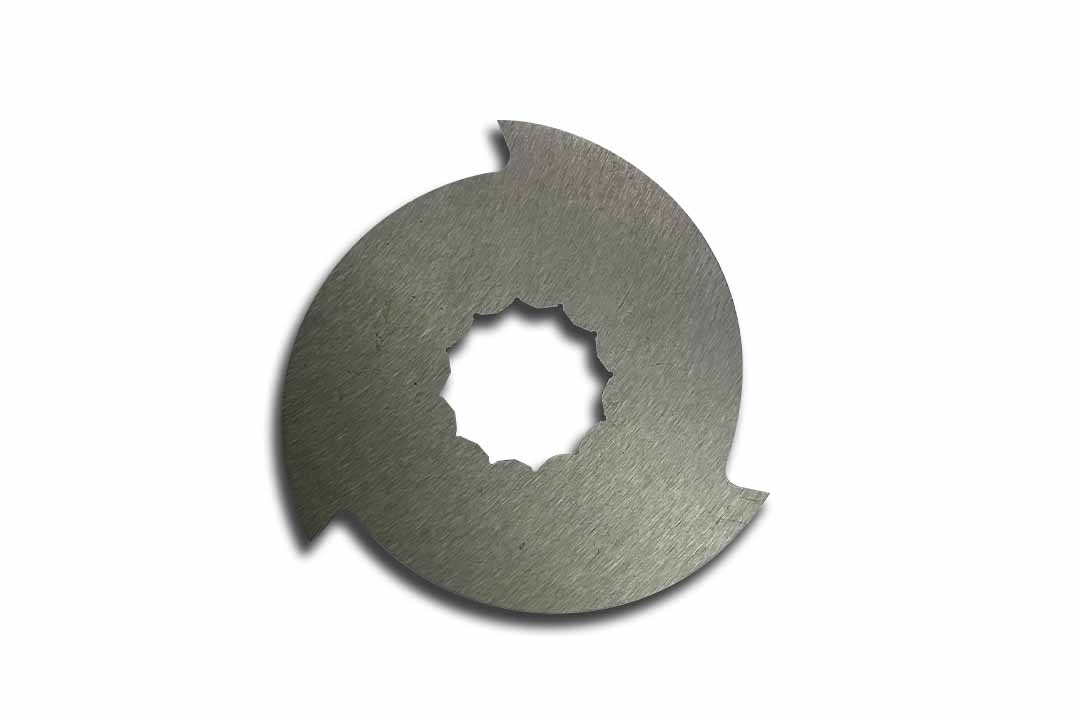
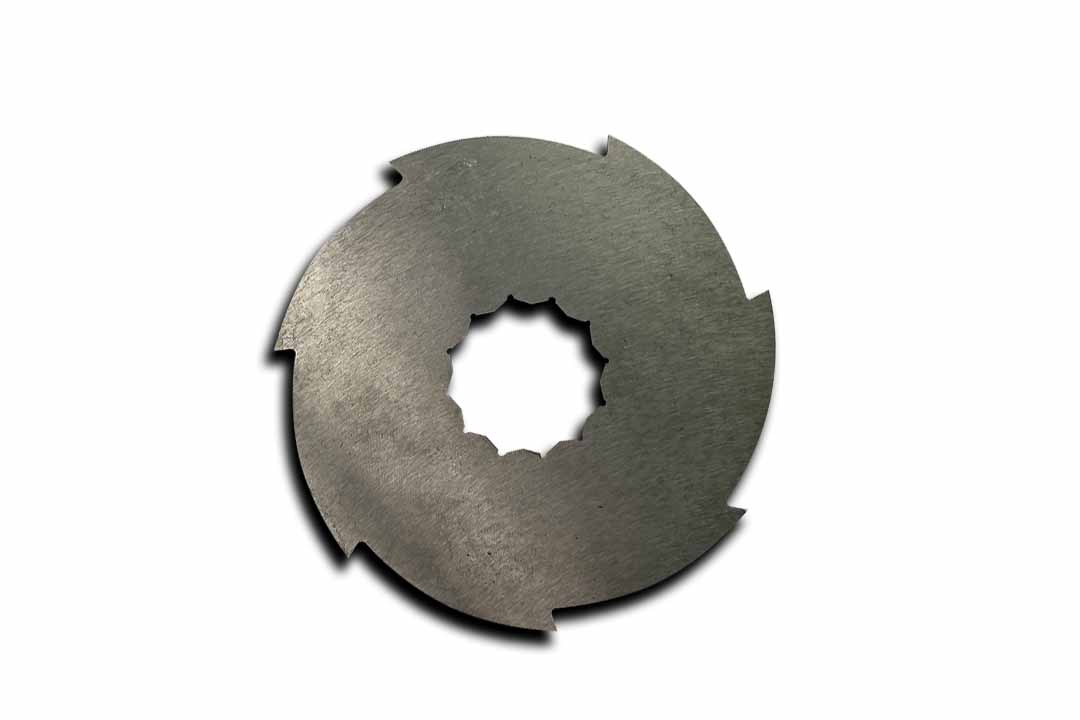
Different Blade Configurations
Enhance your GP20 Shredder's efficiency with our specialized blades. From light to heavy-duty tasks, choose the blade that fits your needs and achieve exceptional shredding performance:
- 2 Teeth Blades: Better grip for larger materials
- 3 Teeth Blades: Versatile Shredding
- 7 Teeth Blades: Heavy-duty shredding for tough materials
Compatible Materials
The GP20 Plastic Shredder is designed to handle a wide range of thermoplastics, making it suitable for a variety of recycling and manufacturing projects. Some of the materials you can use with the shredder:
PET
Commonly used in beverage bottles and food containers.
HDPE
Found in milk jugs, detergent bottles, and plastic bags.
PVC
Used in pipes, vinyl flooring, and medical equipment.
LDPE
Used in plastic bags, six-pack rings, and various containers.
PP
Found in packaging, textiles, and automotive parts.
PS
Used in disposable coffee cups and plastic food boxes.
PEEK
Used in aerospace, automotive, and medical applications.
Various plastics
Plastics like nylon, PC, and bioabsorbable materials.
Practical Applications
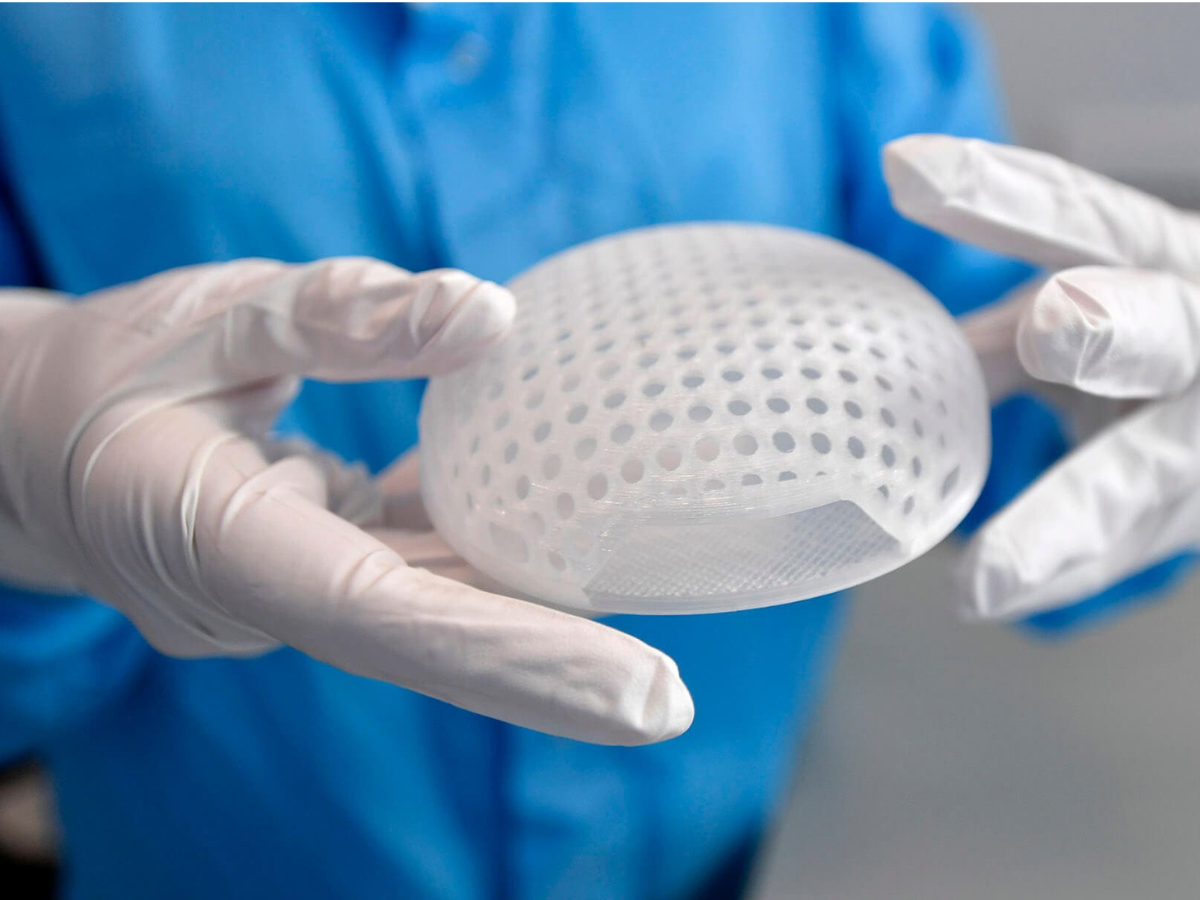
Lattice Medical Case Study
_compressed.png?width=3750&height=2813&name=GP20%20Product%20page%20pictures%20(10)_compressed.png)
Recycling Plastics Blog
_compressed.png?width=3750&height=2813&name=GP20%20Product%20page%20pictures%20(1)_compressed.png)
Explore More Case Studies
Specifications
AC 220-240V 50/60Hz
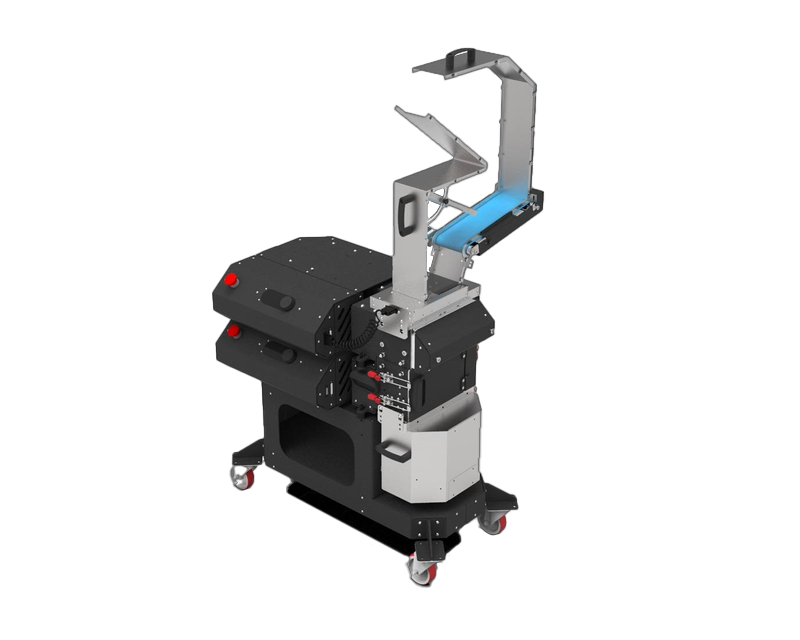
Your First Step Toward Circularity
The GP20 has become a go-to solution for innovators needing precise, small-batch plastic shredding. Whether you’re recycling waste prints or prepping materials for extrusion, this compact reclaimer delivers consistent results.
Ready to take control of your plastic processing? Let’s get started.