Share this
13 Useful 3D Printing Filaments
by 3devo on Feb 8, 2022 11:58:00 AM
The Top Materials You Didn't Know Could Extrude Into 3D Printing Filament
Our customers are always looking to expand the repertoire of polymeric filament materials with which they can 3D-print their products. The only thing which can be a deterrent to this is the fact that not every polymer is 3D-printable. Not yet anyway. Plus, experimenting with new 3D printing materials to test their printability and filament-making ability is a painstaking process. Luckily for us, we happen to enjoy this process and love to share our experiences with extruding new filament materials. This article describes our experiences with thirteen materials that we have successfully converted into 3D printing filament.
Bio Polyethylene (Bio PE)
Bio PE is a bioplastic that is synthesized from ethanol produced through microbial fermentation of glucose. This material has properties similar to conventional PE, but it is considerably more expensive.
We have performed extensive experiments to extrude a Bio PE-based material into 3D printer filament. The exact material we tested was Bio PE SHD 7255 LSL, with 20% thermomechanical pulp (TMP) and 6% malleated polyethylene. While we were able to extrude this polymer successfully on our Composer 450 filament maker, it was not without its challenges. It heats up quickly, and the TMP particles tend to tear the material. Thankfully, rapid fan cooling and low temperatures worked wonders and helped us succeed in this mission.
Extruded Spool of Bio PE Filament
Polyaryletherketone (PAEK)
PAEKs are a family of semicrystalline thermoplastic polymers that have good thermal stability, impeccable mechanical properties, and high chemical resistance. On the flip side, PAEK thermoplastics tend to be more expensive than most other alternatives. They also demand high temperatures for molding and extrusion, something that we handled firsthand during our experimentation.
Extruding PAEK at 380°C using the Composer 450 filament extruder resulted in the formation of air bubbles in the filament. A slightly lower extrusion temperature of 370°C helped improve the quality but led to nozzle lip build-up. Opting for a higher front heater temperature helped decrease this build-up, but the filament surface was still a bit rough. Nevertheless, we are confident that future experimentation will yield 3D printing filaments of even better quality.
Polyether ether ketone (PEEK)
PEEK, a member of the PAEK family, has been a highly-sought-after plastic since a long time. This is because of its excellent mechanical properties, high thermal and chemical stability and exceptional resistance to water and radiation. It is no wonder PEEK is so commonly used in the aerospace, automotive and medical sectors.
In our filament-making experiments, it was a challenge to find an optimal temperature to extrude PEEK filament. Go too high and the material’s crystallinity will suffer heat damage. Go too low and your 3D printing filament will be rough. Plus, PEEK’s melting point is pretty high (343°C), which is another reason why you cannot lower the temperature too much. With extensive experimentation, we found the right temperature to extrude PEEK into a functional 3D printing filament. Luckily for us, PEEK exhibited a steady flow and cooled rapidly upon extrusion. This made it possible for us to easily extrude PEEK filaments of two different diameters (1.75 mm and 2.85 mm).
PEEK Pellets and extruded filament
Of course, these were our first-ever experiments with PEEK, wherein we used our first-generation filament maker – the NEXT 1.0 Advanced filament extruder. In the years since, we have graduated to using our latest filament maker, the Precision 450. We have also streamlined the PEEK extrusion process by dividing our experiments into three stages. At the preparation and transitioning stage, we determined that PEEK extrusion requires a two-step transitioning given its high melting point. The next stage involved finding the correct settings for extrusion. The third and final stage was finetuning and spooling the extruded filament.
Polytherketoneketone (PEKK)
PEKK is another glorious member of the PAEK family of polymers. Like PEEK, it is highly stable at high temperatures and shows high chemical resistance. However, PEKK has superior compressive properties compared to PEEK. These properties make it a much-sought-after material in the aerospace, medical and military sectors. PEKK also flows very well on account of its slow rate of crystallization. This makes its extrusion into 3D printer filament very easy. Also, PEKK filament is usable with most 3D printers because its temperature requirements are less demanding than PEEK.
For our in-house extrusion testing of PEKK, we used the Kepstan® 6001 PF copolymer. With a single purging compound (transition material), we were able to take the PEKK copolymer to the 330-345°C temperature range. Ultimately, using our Composer 350 filament extruder, we were successful in producing spools of 2.85 mm thick PEKK filament.
Polyamide 12 (PA 12)
PA12 is a biocompatible, semi-crystalline polymer with high chemical resistance, wear resistance and impact strength.2Due to these properties, it is a commonly used material in the aerospace, automotive and electronics sectors.2 In 3D printing, PA12 has long found applications in selective laser sintering (SLS), where it is used as a powder. At 3devo, we took it a step forward and created Fused Deposition Modeling (FDM) filament spools out of it.
Using the Composer 450 filament maker, we were able to extrude PA12 into 3D printing filament without any issues. Moreover, the filament worked excellently with the Ultimaker 2+ 3D printer in our tests.
Polyetherimide (PEI)
PEI has amazing mechanical, chemical and electrical properties that make it a popular substitute for metals. Plus, its lower price makes it an excellent alternative for PEEK. Not surprisingly, PEI is quite popular for structural and electrical applications. Additionally, it is heat resistant and retains high mechanical strength even at high temperatures. These properties make it easily sterilizable in the autoclave and thus suitable for biomedical and food-related applications as well. It also helps that PEI is easier to process because of its amorphous nature.
In our experiments, we used PEI in the form of the Ultem 1010 resin. We were able to successfully extrude this filament material with our Composer 450. However, the tiniest bit of moisture can cause air bubbles to form in the extruded PEI filament. The same thing happens at extrusion temperatures over 370°C. At the same time, PEI’s stability at high temperatures meant that we could not decrease the extrusion temperature too much. Ultimately, we were able to determine the optimal temperature to extrude it into 3D printer filament without forming air bubbles.
Polyethylene Terephthalate (PET)
Since the 1970s, PET has been one of the most popular thermoplastic polymers. Its applications range from making food containers and bottles to shoes and sweaters to automotive parts. Some of the major reasons for its widespread usage are its light weight, low cost, good strength, non-toxicity, and recyclability. In fact, its recyclability made PET an excellent option for us to try and test for making 3D printing filament.
We used discarded PET bottles and a plastic shredder to get the material for our filament-making rendezvous. We used our Precision 350 Filament Extruder for this experiment, which turned out to be a raging success. We found that a heater temperature of 245°C worked the best for us, along with an extruder speed of 7 RPM and a cooling fan speed of 15%. One thing to note, however, is that with recycled PET, cleaning is absolutely vital, as is drying the shredded plastic. Also, different PET grades will extrude differently. So, you may have to experiment with your specific PET grade and extruder type to arrive at the right parameters.
3D printed parts made with PET and rPET (recycled PET)
Polyethylene Terephthalate Glycol-modified (PETG)
PETG is a PET copolymer, most often used in making packaging for cosmetic and food products. Like PET, PETG has good chemical and impact resistance. At the same time, it is less prone to cracking than PET because copolymerization with glycol hinders its crystallization. PETG is also more flexible and more heat resistant than PET.
At 3devo, we have not only extruded PETG filament from scratch, but also used it to 3D-print a variety of structures. In our experiments with PETG, we have found it to be a highly desirable material for extruding 3D printing filament. We attribute this ease of use to its excellent durability and mechanical characteristics.
Polycarbonate (PC)
PC is another thermoplastic polymer that is highly used in the construction, automotive, food packaging and electronics industries, among others. This is primarily because it has high impact and thermal resistances and a desirable mechanical strength, all while being lightweight.
Given its high demand in various industries, we have successfully managed to extrude PC into 3D printer filament. In our testing, we have noted that drying is fundamental to achieving good processability of PC. Generally speaking, drying at 110-120°C for 5 hours or more works well for most PC grades. If the precursor PC is not dry enough, the resulting 3D printing filament can be brittle and rough. Note that we used our Composer 350 filament maker to extrude PC filament, and it worked amazingly. Plus, the extruded filament gave a commendable performance as a 3D printing material.
Polyphenylene Sulfide (PPS)
PPS is a one-of-a-kind plastic that is resistant to heat, water, acids, bases, and even ultraviolet radiation. To add to that, it has high structural and thermal stability. All these properties make it a desirable material for the construction, electrical and automotive sectors.
Like almost any other material being processed for extruding 3D printer filament, PPS must be dried extensively beforehand. In our experiments, we have found that drying at 150°C or higher for 8 hours works well for PPS. Following this precursor step, we were able to successfully process and extrude PPS into 3D printing filament.
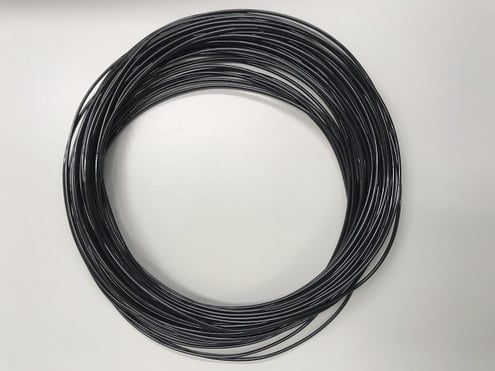
PPS 3D Printed Filament
Polystyrene (PS)
PS is a centuries-old thermoplastic that we see in various shapes and forms every day in our lives. It is quite inexpensive compared to many other polymers. Moreover, it has a high impact resistance and is a good electrical insulator. It does have a few disadvantages though, including its poor chemical resistance, low thermal stability, and high flammability.
Nevertheless, given that PS is constantly in high demand, we used our Composer 450 Filament Maker to extrude PS filament. The equipment’s cooling fan was a life-saver during the extrusion since it was crucial to keep the material from overheating. During 3D printing too, it was important to precisely control the heating or else the resulting structure came out warped. In our opinion, High Impact Polystyrene (HIPS) is the best form of PS for making 3D printing filament because it is quite strong and durable.
Polyvinyl Alcohol (PVA)
PVA, another thermoplastic polymer, is unlike any of the materials we have discussed thus far. PVA has high chemical and thermal stability, but is also environment-friendly and water-soluble.3 As such, it is used in surgical sutures and food packaging, as well as in the paper and textile industries.3 In the realm of 3D printing, it is most often used to create temporary support elements in 3D-printed structures.
Since it is water-soluble, PVA can get plasticized and undergo degradation with even the slightest exposure to moisture. Needless to say, it was a challenging task for us to extrude PVA into 3D printer filament. Challenging, but not impossible. Of course, we had to ensure that the PVA was completely dry before extrusion. Additionally, cleaning out the extruder nozzle to remove any PVA residue was a critical step in the process. With these precautions in place, we were able to extrude PVA filament using our Composer 350 filament maker. The extruded filament also performed nicely in our 3D printing trial.
Thermoplastic Polyurethane (TPU)
TPU is a unique polymer that brings together the best properties of rubber and thermoplastics in a single material. Its flexible nature, scratch resistance and durability make it a coveted material in the medical, aerospace, electrical and sports sectors. It comes in various types, each with a different hardness level.
In our experiments with this filament material, we used the TPU Shore 75A with the Composer 350 filament extruder. Extruding TPU was a difficult but ultimately fruitful journey. We spent a considerable amount of time finetuning the parameters to extrude a high-quality 3D printing filament from TPU. Thankfully, our subsequent 3D printing trial resulted in a flexible structure, just like we had hoped.
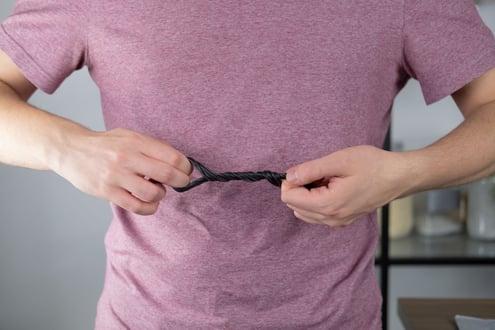
Highlighting the flexibility and strength of extruded TPU filament
Testing New Materials for Making 3D Printing Filament
As 3D printing finds applications in new industrial sectors, the demand for new 3D printing materials is going to skyrocket. Extruding 3D printing filaments from new or previously untested materials is, thus, going to be a mammoth task. This is why we are dedicated to sharing with you our experiences with new potential 3D printing filament materials. Follow this space for more updates on our trials and experiments.
Share this
- March 2025 (1)
- January 2025 (1)
- December 2024 (2)
- November 2024 (3)
- October 2024 (4)
- September 2024 (2)
- August 2024 (3)
- July 2024 (6)
- June 2024 (3)
- May 2024 (2)
- April 2024 (1)
- March 2024 (1)
- January 2024 (1)
- November 2023 (2)
- October 2023 (5)
- September 2023 (2)
- August 2023 (1)
- July 2023 (1)
- May 2023 (1)
- December 2022 (3)
- August 2022 (1)
- June 2022 (1)
- May 2022 (2)
- April 2022 (2)
- March 2022 (7)
- February 2022 (2)
- January 2022 (3)
- December 2021 (3)
- November 2021 (3)
- October 2021 (2)
- September 2021 (3)
- August 2021 (3)
- July 2021 (2)
- June 2021 (1)
- March 2021 (1)
- October 2020 (1)
- June 2020 (1)
- May 2020 (1)
- April 2020 (4)
- November 2019 (1)
- July 2019 (2)
- June 2019 (1)
- May 2019 (1)
- March 2019 (1)
- November 2018 (1)
- September 2018 (1)
- January 2018 (1)
- October 2017 (1)
- September 2017 (1)
- July 2017 (1)
- June 2017 (1)
- May 2017 (1)
- January 2017 (1)
- December 2016 (3)
- November 2016 (2)
- October 2016 (1)
- May 2016 (2)
- August 2015 (2)
- July 2015 (1)