Share this
Researching 3D Printing Polymers and Materials
by Gabriela Greste on Apr 19, 2024 4:58:06 PM
Introduction
3D printing offers a direct path to prototype and manufacture parts rapidly and cost-effectively. Selecting the appropriate 3D printing process is important, but the choice of materials plays a crucial role in achieving the desired mechanical properties, functionality, and appearance of the final part.
This guide focuses on the most popular available plastic and additive materials for 3D printing, comparing their characteristics and applications and providing a structured approach to selecting the right material for specific project requirements.
Understanding Polymers: The Building Blocks of Filament
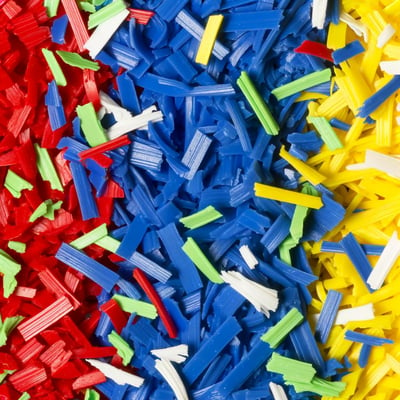
Polymers, the primary substance in filament creation, are large molecules composed of repeating units called monomers. This structure imparts polymers with their characteristic properties, such as strength, flexibility, and resistance to chemicals and temperatures.
Polymers are classified into two major categories: thermoplastics and thermosetting plastics. Thermoplastics soften when heated, making them suitable for 3D printing applications due to their ability to be reshaped and reused. On the contrary, thermosetting plastics harden permanently after curing and do not remelt, which limits their use in filament production for 3D printing.
Discovering the Perfect Material
The Polymer Pyramid is an invaluable tool for selecting the right material for your project. Understanding the properties of each tier within the Polymer Pyramid is crucial to finding the perfect material suitable for your desired results and application. Whether you're looking for materials with specific resistance properties, flexibility, or environmental sustainability, our Filament Maker empowers you to experiment and discover the perfect polymer for your innovative projects.
The Polymer Pyramid: Navigating Material Selection
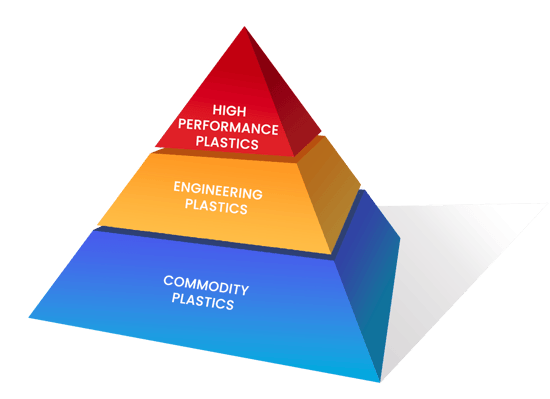
The Polymer Pyramid categorizes plastics into three tiers based on their properties and suitability for different applications:
1. Commodity Plastics: These materials offer a cost-effective solution with adequate strength for various applications. Examples include Polyethylene (PE), Polypropylene (PP), and Polystyrene (PS). While they're affordable and easy to work with, their applications are somewhat limited by their lower resistance to temperature and chemicals.
They are ideal for educational purposes, prototyping, and non-functional models due to their ease of printing and low cost. However, their relatively lower resistance to heat and chemicals limits their use in functional parts. For commodity plastics, standard desktop 3D printers, which are reliable and offer good print quality without high costs, are excellent choices.
2. Engineering Plastics: Positioned in the middle of the pyramid, these materials offer a balance between performance and cost. Notable materials include Polyamide (PA or Nylon), Acrylonitrile Butadiene Styrene (ABS), and Polycarbonate (PC). Engineering plastics are characterized by their enhanced mechanical and thermal properties, making them suitable for more demanding applications. However, they can be more challenging to process and may require specific conditions for optimal 3D printing results.
With better mechanical properties and heat resistance, engineering plastics are suited for functional parts that require durability, such as gears, hinges, and casings. Their increased stiffness and strength come with a higher melting point, which might necessitate printers with advanced features, such as heated beds and enclosed chambers suited for creating functional prototypes and parts.
3. High-Performance Plastics: At the top of the pyramid, high-performance plastics boast exceptional durability, heat resistance, and chemical stability. This category includes Polyether Ether Ketone (PEEK) and Polyphenylene Sulfide (PPS), which are used in the most demanding industrial applications, including aerospace and medical implants. The trade-off for these superior properties is a higher cost and more complex processing requirements.
These materials are the choice for cutting-edge applications. They can withstand extreme conditions, including high temperatures and aggressive chemicals. For high-performance plastics, 3D printers designed for industrial applications with capabilities for high-temperature extrusion are necessary. These printers ensure precision and strength in parts that meet stringent requirements.
Turn any Thermoplastic into 3D Filament
There are endless ways to combine thermoplastics and additives — but the real key to unlocking their potential is having the right tool. The Filament Maker TWO helps researchers and R&D engineers turn their ideas into functional filament, whether you're testing recycled blends or developing something completely new.
Thermoplastic Materials for Creating 3D Printing Filament
Filament dictates not only the print's appearance but also its functional properties. Among the options, a few stand out for their popularity and versatility. Let's dive into the details of these materials, shedding light on why they might be the perfect choice for your next project.
%20-%20instasize.png?width=500&height=400&name=MicrosoftTeams-image%20(40)%20-%20instasize.png)
Polylactic Acid, or PLA, is beloved in the 3D printing community for good reason. Derived from renewable resources like corn starch or sugarcane, PLA is biodegradable under industrial composting conditions, offering a greener alternative to its petroleum-based counterparts. Ideal for detailed prints, PLA comes in a vibrant array of colors and blends, making it as versatile as it is environmentally friendly. While its lower resistance to heat may limit its use in functional parts, its affordability and ease of use make PLA a go-to for prototypes, educational projects, and decorative items.
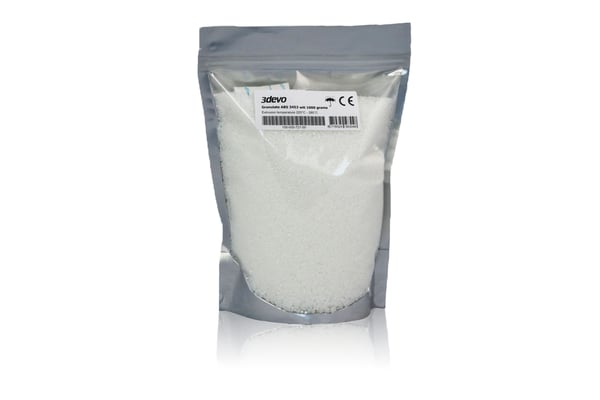
Acrylonitrile Butadiene Styrene (ABS) is a stalwart in the world of 3D printing. Known for its strength, durability, and slight flexibility, ABS can withstand higher temperatures than PLA, making it suitable for more functional applications. Despite its many benefits, ABS does require a higher printing temperature and a heated bed to prevent warping, along with good ventilation during printing due to the fumes it emits. Its ability to be smoothed with acetone post-printing allows for a professional finish, positioning ABS as a favorite for automotive components, consumer electronics, and toys.
%20-%20instasize.png?width=500&height=400&name=MicrosoftTeams-image%20(15)%20-%20instasize.png)
PETG combines the best of both PLA and ABS, offering strength, flexibility, and heat resistance with very low shrinkage and warping. Its clarity and potential for food-safe applications make it a unique choice in the filament market. Although PETG is recyclable, it's not biodegradable. However, its versatility and environmental friendliness compared to ABS make it an attractive option for packaging, medical devices, and household items.
.jpg?width=533&height=400&name=MicrosoftTeams-image%20(58).jpg)
Thermoplastic Polyurethane, or TPU, is renowned for its elasticity and impact resistance, opening up a world of possibilities for 3D printing flexible, durable items. From automotive parts to medical devices and consumer goods, TPU's applications are vast. Its flexibility does come with challenges, requiring a direct drive extruder and careful printing settings to achieve the best results. Despite these hurdles, TPU remains a sought-after material for projects requiring a blend of flexibility, durability, and wear resistance.
- Nylon
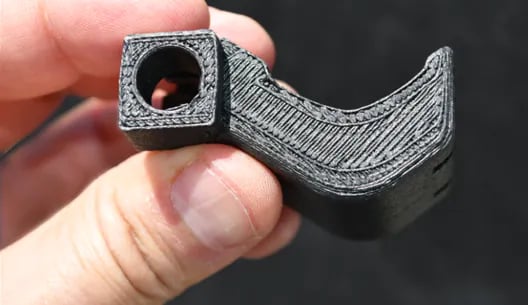
Nylon, or Polyamide, is a staple in industries requiring high strength, durability, and resistance to wear and chemicals. This engineering polymer absorbs moisture, which can affect its properties but also makes it flexible. Nylon's high printing temperature and need for a dry filament before printing reflect its industrial-grade qualities. While it may not be the most environmentally friendly option due to its limited recyclability, Nylon's performance in functional parts under mechanical stress is unmatched.
%20-%20instasize.png?width=500&height=400&name=MicrosoftTeams-image%20(9)%20-%20instasize.png)
Polyether Ether Ketone (PEEK) represents the pinnacle of 3D printing filaments, offering exceptional thermal stability, chemical resistance, and mechanical properties. Its high cost and the need for specialized printing equipment may place it beyond the reach of hobbyists, but for applications in aerospace, medical implants, and high-performance automotive components, PEEK is unrivaled. Its recyclability, combined with its ability to withstand extreme environments, makes it a material of choice for cutting-edge projects.
- Polycarbonate (PC)
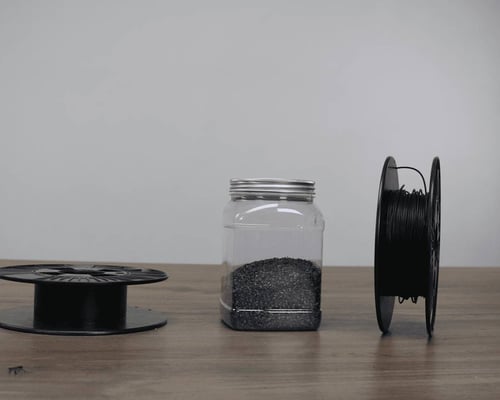
Polycarbonate stands as a beacon of strength and clarity in the filament family, revered for its impact resistance and exceptional durability. PC's ability to withstand high temperatures and its inherent transparency make it an ideal choice for applications demanding both visual and structural quality. Its utility spans across protective gear, automotive components, and even models requiring a glass-like clarity. However, the high printing temperatures required for PC, along with its sensitivity to moisture, necessitate a level of expertise and preparation. While recyclable, the environmental footprint of PC is something to consider, advocating for mindful use and recycling practices.
Specialty Filaments
1. Wood Filament
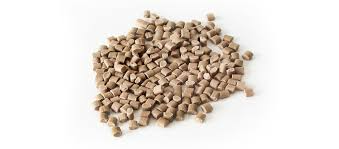
Blending the biodegradability of PLA with organic wood fibers, wood filament offers an eco-friendly solution for those looking to infuse a natural aesthetic into their prints. This unique material allows enthusiasts to create objects with the tactile feel and scent of wood, complete with the ability to be stained, sanded, or carved post-printing. Perfect for artistic creations, educational models, and decorative items, wood filament adds an element of warmth and authenticity to projects. Though it requires careful handling to prevent nozzle clogging, its sustainable credentials and distinctive finish make it a cherished choice among eco-conscious creators.
Wood filament typically combines 20-40% wood particles with 60-80% PLA, making it both biodegradable and capable of utilizing waste wood from other industries. The addition of wood enhances the filament's stiffness and rigidity but also increases its brittleness, which can lead to challenges in load-bearing applications. Despite these mechanical limitations, wood filament prints exhibit minimal warping and shrinkage, making them well-suited for detailed and decorative pieces.
For optimal printing results, a hardened steel nozzle and a slightly larger diameter are recommended to manage the abrasive nature of wood particles and avoid clogs. The filament should be stored in a dry, airtight container to prevent moisture absorption, which can affect print quality. Although not suitable for food-related applications due to its porosity and potential chemical exposure, wood filament remains a popular choice for its unique finish and reduced environmental impact compared to traditional 3D printing materials.
2. Metal Filament
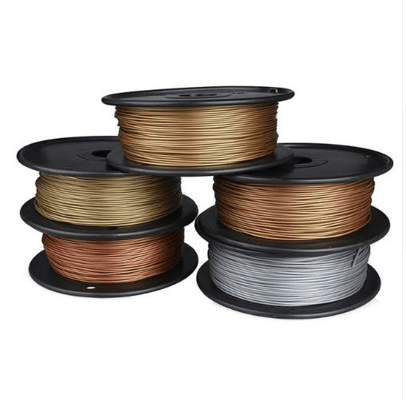
Metal filament combines the practicality of PLA with the aesthetic and structural qualities of real metal powders such as bronze, copper, or stainless steel, creating a unique composite material that enables the production of metallic-looking prints. These prints can be polished, patinated, or aged to replicate authentic metallic effects. This makes metal filament ideal for producing intricate items like jewelry, figurines, and custom hardware, transforming basic objects into stunning pieces of art. Although the filament's additional weight and abrasiveness require a printer that can handle its unique characteristics, the results are unmatched in their visual appeal and realism.
The use of metal filament, often referred to as bound metal deposition (BMD) or metal deposition modeling (MDM), has surged in popularity for applications ranging from small replacement parts to heat sinks and even injection molds. Previously accessible only through high-cost industrial methods, metal filament now allows for the creation of solid metal parts at a fraction of the cost and without the need for complex safety measures associated with traditional metal 3D printing. This shift has made metal 3D printing accessible to a broader range of professionals, democratizing the ability to produce metal parts using desktop-size 3D printers.
However, printing with metal filament is not without its challenges. It typically involves a multi-step process including debinding and sintering, where the polymer is first removed in a solvent and the part is then sintered to fuse the metal particles, resulting in a nearly solid metal object. This process not only alters the mechanical properties of the printed parts but also their density and structural integrity. Despite these complexities, metal filament remains a compelling option due to its cost-effectiveness and the detailed, high-quality results it can achieve, particularly for non-critical metal components.
3. Conductive Filaments
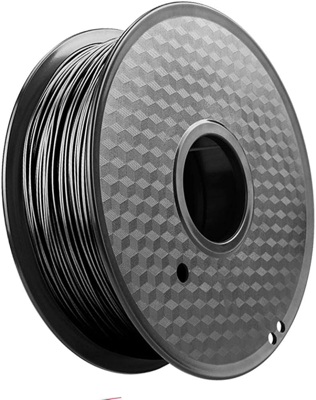
Conductive filaments blend traditional 3D printing materials with conductive additives like carbon nanotubes or graphene, enabling the creation of functional electronic components directly from a 3D printer. These filaments are perfect for educational projects, DIY innovations, and advanced prototyping.
Recent research, including studies using 3devo's Composer Filament Maker, has shown that adding small percentages of conductive additives such as Multiwall Carbon Nanotubes (MWCNTs) significantly enhances filament properties. For example, a 5% MWCNT mix not only increases electrical conductivity but also improves mechanical and thermal performance, making it ideal for durable and functional applications in areas like flexible electronics and medical devices.
With tools like 3devo's Composer Filament Maker, innovators can precisely tailor the material blends to achieve desired conductivity levels efficiently and cost-effectively. This capability supports the development of specialized filaments that push the boundaries of what's possible with 3D printing technology.
4. Carbon Fiber Filament
Carbon fiber filament enhances 3D printing with its superb strength-to-weight ratio, making it a premium choice for engineering applications where durability and lightness are crucial. By integrating carbon fibers into a polymer matrix, such as nylon or PLA, this filament offers increased rigidity and decreased weight compared to its base materials. These properties are highly sought after in sectors such as automotive, aerospace, and robotics, where high performance and precision are paramount.
In 3D printing, carbon fiber filament can be used in two forms: chopped fiber, which is mixed throughout the filament to provide enhanced strength and stiffness, and continuous fiber, which offers additional reinforcement for critical load-bearing applications. Both types are known for reducing the shrinkage and warping associated with high-temperature printing, making carbon fiber an excellent material for creating complex, durable parts.
Despite its many advantages, carbon fiber filament requires specific handling due to its abrasive nature. It can wear out standard nozzles quickly, so a hardened steel nozzle is recommended for printing. Additionally, the material's stiffness and fiber composition can lead to nozzle clogging if not managed properly. To overcome these challenges, maintaining optimal printing temperatures and using a direct drive extruder can help minimize issues and ensure high-quality prints.
Innovating with Biomaterials in 3D Printing
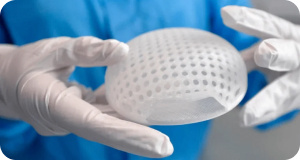
3devo specializes in the extrusion of biomaterials for 3D printing, providing tools that meet the demands of medical engineering applications. Biomaterials, essential in medical device manufacturing, range from dental braces to implants and are designed for either integration with or absorption by biological systems.
The 3devo Filament Maker is engineered to produce high-quality filaments from thermoplastics combined with bioceramics and other additives. This technology particularly benefits bone tissue engineering, where scaffolds are fabricated to facilitate bone cell growth and eventual tissue regeneration.
Our focus is on creating filaments that are biocompatible and offer mechanical properties comparable to natural bone, essential for implants that support the body’s healing process. The advanced capabilities of our Filament Extruders allow for precise control over the material properties, enabling the production of medical-grade filaments that are reliable for professional use.
Keep an eye out for our in-depth blog post on May 21st, where we will dive into the intersection of biomaterials and 3D printing technology.
The Art of Material Recycling and Custom Filament Creation
3devo doesn't just stop at offering a range of compatible materials; we also champion the cause of sustainability through material recycling. Transform your plastic waste into valuable 3D printing filaments, and explore the endless possibilities of creating custom filaments with unique colors, additives, or properties.
The Future of 3D Printing: Expanding Horizons with 3devo
Our commitment to innovation is not just about today but also about shaping the future. The Filament Maker TWO series, with its enhanced features and capabilities, is set to redefine the standards of desktop filament extrusion. From research and development to creating bespoke materials for specific applications, 3devo is your partner in every step of the journey towards innovation.
Conclusion: Empowering Innovators Across the Globe
As we conclude this guide on selecting the right 3D printing materials, it's evident that the choice of polymer greatly influences the final product's properties and capabilities. From the versatility of commodity plastics to the robustness of high-performance polymers, understanding the Polymer Pyramid is key to achieving the desired outcome in any 3D printing project. The 3devo Filament Maker stands as a testament to the innovation in the field, offering the ability to produce custom filament tailored to precise project specifications.
Moreover, the sustainable approach of recycling plastics into new filament not only reflects the commitment to the environment but also opens up a realm of customization in material properties. As we move forward, 3devo continues to break new ground, particularly with the upcoming Filament Maker TWO series, designed to push the boundaries of desktop filament extrusion further.
Innovation in 3D printing materials is an ongoing journey, with each advancement offering a deeper understanding and greater possibilities. We invite you to stay engaged with us as we explore new materials, processes, and applications in the dynamic world of 3D printing. Join us on May 21st for an in-depth exploration of biomaterials in 3D printing, and let's continue to transform the future, one layer at a time.
Share this
- March 2025 (1)
- January 2025 (1)
- December 2024 (2)
- November 2024 (3)
- October 2024 (4)
- September 2024 (2)
- August 2024 (3)
- July 2024 (6)
- June 2024 (3)
- May 2024 (2)
- April 2024 (1)
- March 2024 (1)
- January 2024 (1)
- November 2023 (2)
- October 2023 (5)
- September 2023 (2)
- August 2023 (1)
- July 2023 (1)
- May 2023 (1)
- December 2022 (3)
- August 2022 (1)
- June 2022 (1)
- May 2022 (2)
- April 2022 (2)
- March 2022 (7)
- February 2022 (2)
- January 2022 (3)
- December 2021 (3)
- November 2021 (3)
- October 2021 (2)
- September 2021 (3)
- August 2021 (3)
- July 2021 (2)
- June 2021 (1)
- March 2021 (1)
- October 2020 (1)
- June 2020 (1)
- May 2020 (1)
- April 2020 (4)
- November 2019 (1)
- July 2019 (2)
- June 2019 (1)
- May 2019 (1)
- March 2019 (1)
- November 2018 (1)
- September 2018 (1)
- January 2018 (1)
- October 2017 (1)
- September 2017 (1)
- July 2017 (1)
- June 2017 (1)
- May 2017 (1)
- January 2017 (1)
- December 2016 (3)
- November 2016 (2)
- October 2016 (1)
- May 2016 (2)
- August 2015 (2)
- July 2015 (1)