Share this
8 Things Our 3devo Colleagues Want You to Know About Our Plastic Shredder
by Ellie Pritchard on Aug 21, 2024 1:59:31 PM
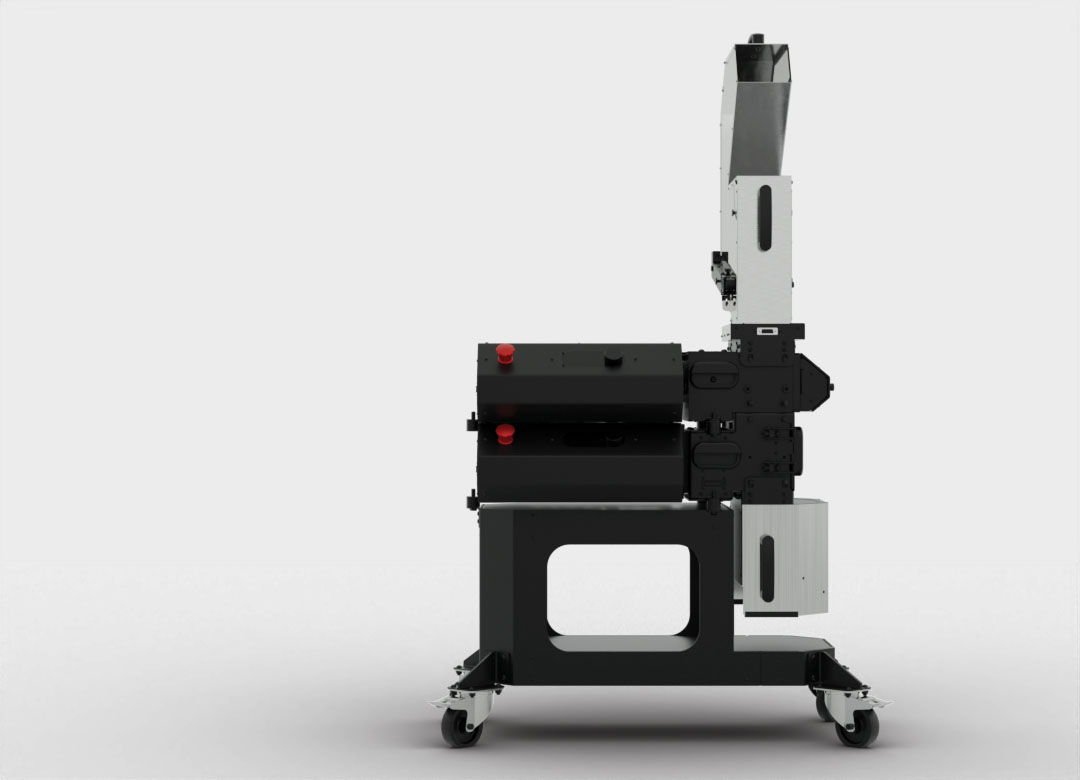
At 3devo, we’ve developed a comprehensive solution for transforming plastic waste into valuable resources, with our GP20 Plastic Shredder playing a pivotal role in the preparation of this process. By breaking it down into manageable particles, the shredder ensures the material is ready for further processing into FDM filament using a filament extruder, such as our Filament Makers.
Here at 3devo HQ, each of our colleagues interacts with our machines in a different way, offering unique perspectives on how they work. To gather the most useful insights about our Plastic Shredder, we spoke with team members from our Production, R&D, Customer Service, and Marketing departments. Here are six key things our colleagues want you to know about the GP20 Shredder, and how it enhances your filament-making process.
What is the GP20 Plastic Shredder and Why Is It Essential?
At 3devo, we’ve engineered the GP20 Plastic Shredder as a vital part of your recycling and filament-making process. This robust machine is designed to efficiently break down plastic waste into small, manageable particles, preparing it for further processing into high-quality FDM filament using our Filament Maker ONE or Filament Maker TWO. Whether you’re looking to recycle old 3D prints or transform discarded plastic from various sources, the GP20 Shredder enables you to create a closed-loop, sustainable production system that supports both innovation and environmental responsibility.
1. Multiple Blade Configurations
Production Engineer, Thomas
As a member of our Production Team, Thomas builds the machines ready to be shipped out to customers. Being so familiar with the make-up and components of the GP20 Shredder & Granulator, Thomas began to test alternative configurations of the various blade-types we produce.
“We usually send out the shredder with a standard blade configuration, which is great for processing small- to mid-sized objects,” Thomas explains. “But for many customers, they need to shred larger or oddly shaped items. That’s where the blade modularity becomes really useful.”
With 14 blades, our plastic shredder offers combinations of 2, 3, and 7 teeth blades to cater to a range of shredding requirements. For example, Thomas has devised a configuration which is perfect for shredding large plastic items that would otherwise spend time bouncing around above the blades. Keep an eye out for our next blog post, where we’ll dive into the different shredder blade configurations and how they can enhance your project. With this combination of blades, Thomas shows us how the teeth grab a round-bottomed plastic bottle within seconds, pulling the material down into the granulator efficiently. “The end result is that the shredded material comes out much finer, meaning it will dry faster and can be processed very easily in the Filament Makers.”
Thanks to the accessibility of the machine, customers are able to change the blade configurations themselves. But Thomas advocates for a more proactive approach: “If a customer lets us know the size and type of material they’re intending to shred, then we can already suggest and implement an optimized blade configuration in the machine before shipping it out to them. It’s simple enough for the customer to swap out the blades when they want to change material, but if we install the optimal combination already, then the shredder is essentially ready to plug-and-play.”
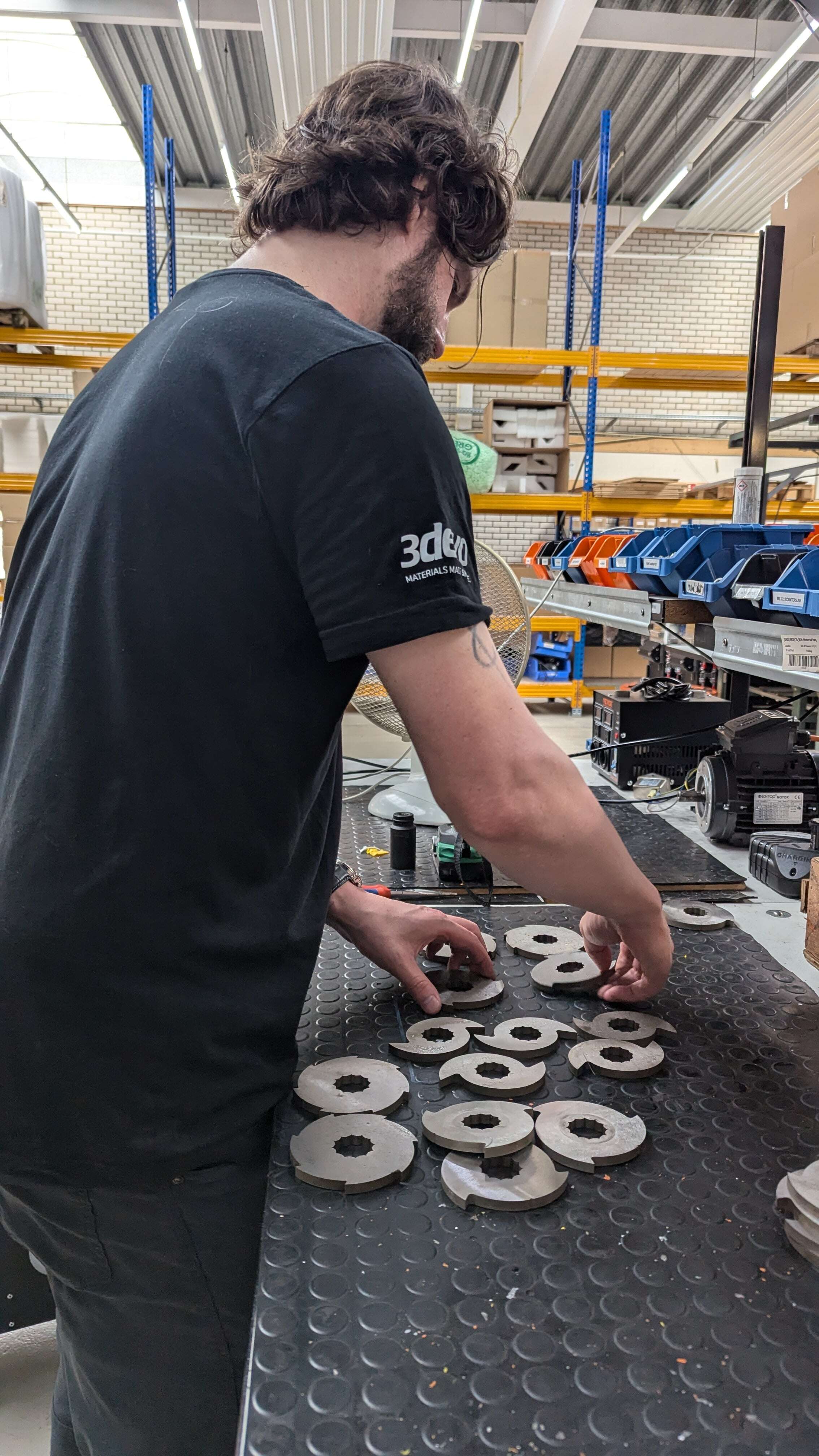
2. Intuitive Interface
UX Designer, Gigi
The user experience of our machines is one of our major priorities. It is up to our in-house UX Designer Gigi to monitor the impact of design decisions on how a customer experiences the equipment. Her focus lies on how intuitive and straightforward our machines are for our customers to use.
One of the key things that she has learned from customer feedback about our Plastic Shredder & Granulator is the value of a detailed interface. "Users of other shredders often mention ambiguous indicator lamps that signal an issue without specifying the problem," Gigi notes. "In contrast, our shredder features an LED screen that provides clear error messages, allowing users to address issues promptly without unnecessary troubleshooting."
This design choice aims to streamline operations, reducing downtime and ensuring a smoother user experience.
3. Reliable Insights
UX Designer, Gigi
Gigi also points out a critical difference between the GP20 and some other shredders on the market: “Another interesting point is that some plastic shredders inadvertently melt the material during the process. This not only causes blockages but also renders the shredded material unusable.”
The GP20 is designed specifically to avoid such issues. “Our shredder operates at optimal speeds and temperatures, ensuring that the plastic remains intact and doesn’t reach melting point during shredding. This means the material is processed cleanly and remains in a condition suitable for further use, whether it’s for recycling into new filament or other applications,” Gigi explains.
By addressing these common pain points, the Shredder is designed to be both efficient and user-friendly, minimizing frustration and maximizing productivity.
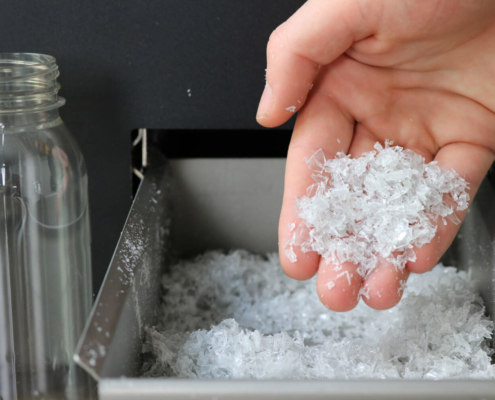
4. Easy to Empty
UX Designer, Gigi
Shredded plastic material can be messy and difficult to gather, so Gigi reminds us of the specially designed container where it collects.
“We designed the container shape to make it simple for users to remove the shredded material without any hassle,” Gigi says. The container includes a small removable plate, secured with four screws. This design allows users to easily access and remove the shredded particles without having to detach the entire container.
“It ensures that no shredded particles can exit the shredder by accident, keeping everything contained and minimizing waste,” Gigi adds. This setup not only makes the process more efficient but also ensures that users don’t lose any valuable material during the emptying process.
5. Safety Features
Customer Support Agent, Anastasia
Another valuable perspective comes from our 3devo Customer Service team. Anastasia is one of our Customer Support Agents; her direct contact with our customer base gives her a first-hand insight into their experiences with our machines.
As one would expect with a large industrial-grade shredder, there are various safety features present on our GP20 machine. In particular, Anastasia often handles conversations with users about the interlocking components: “We have sliders and clamps on most of the larger parts of the machine, such as the hopper. If any one of these is not securely connected, then the shredder will not start.” This eliminates the risk of blades being exposed whilst running. “It is also impossible for the machine to start without the container bin attached – which obviously prevents shredded material from spilling out onto the ground.”
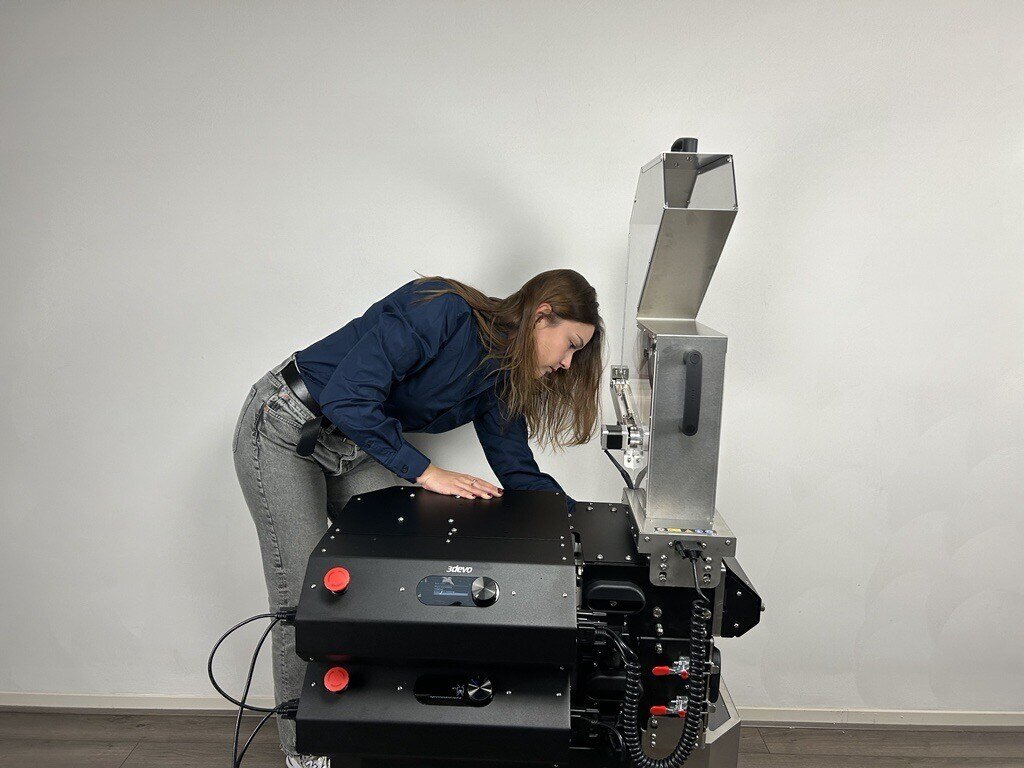
6. Accessible Maintenance & Modular Components
R&D Engineer, Jelle
Jelle, our R&D Engineer behind the design of the GP20 Shredder, emphasizes the importance of modularity not just in the blade configurations but also in the machine’s key internal components.
The Plastic Shredder is designed for easy maintenance and thorough cleaning, thanks to its modular components. “One feature is the granulator rotor, which can be removed with just one bolt,” Jelle explains. This allows users to perform more thorough cleanings, so the shredder operates more efficiently and without contamination between different materials.”
Another convenient aspect of the GP20’s design is the easily removable scraper combs positioned next to the shredder blades. These combs are critical in preventing material build-up and ensuring smooth operation. By making them easy to remove, Jelle’s design ensures that maintenance is hassle-free, further extending the machine’s lifespan and performance. This modularity was a crucial factor for customers like Gary Gillespie and the Spokane Public Schools District, who valued the ability to ship individual components for maintenance rather than the entire machine, significantly reducing downtime and costs. You can read more about how this feature benefited Mr Gillespie and his students in our recent Case Study.
-min.jpeg?width=2016&height=1512&name=shared%20image%20(1)-min.jpeg)
7. Processing Hardened Materials
Account Manager, Kyriakos
One of our Account Managers, Kyriakos, has also put the GP20 to the test by searching for the upper limit of what the machine can process in terms of hardened materials. By conducting tests with customer samples, Kyriakos found that (with a careful approach) the blades are capable of shredding even complex materials such as combined PEEK and carbon fiber. “The material is processable, but the shape and density of the parts significantly affect the shredder's ability to process them,” he explains. “Dense parts are more challenging due to the very high fiber concentration, so we don’t recommend trying to shred those.” For smaller parts of this same material, however, the shredder makes light work.
Our team’s extensive experience with these machines means we can offer professional advice on how different materials are likely to behave when processed. By consulting with us before you begin, you can save valuable time and money, ensuring that your shredding process is both efficient and effective from the start.
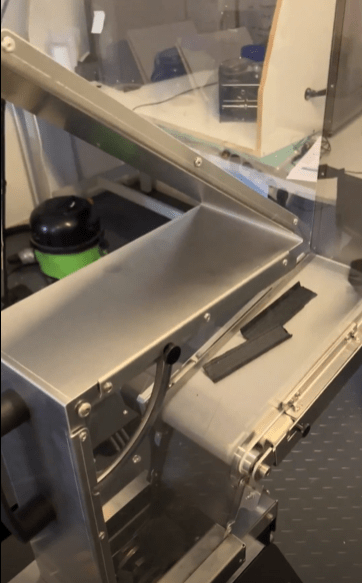
8. Integration with Other 3devo Products
Marketing Coordinator and SEO Specialist, Gabriela
Gabriela emphasizes the importance of the GP20 Shredder in creating a complete recycling system when paired with our Filament Maker ONE or Filament Maker TWO. "By integrating the GP20 Shredder with either of our Filament Makers, users can efficiently convert plastic waste, old 3D prints or more into custom filament, creating a closed-loop process that’s both sustainable and cost-effective," she explains. This system not only reduces waste but also empowers users to recycle materials from various sources, such as collecting discarded plastic waste to create usable filament.
"Combining our Filament Extruders with our Plastic Shredder allows you to innovate while keeping sustainability at the forefront," Gabriela adds. This holistic approach ensures that every step of your workflow supports both environmental responsibility and creative freedom.
Conclusion
The GP20 Shredder is more than just a powerful machine—it's a critical component in your in-house recycling process, designed with versatility, user-friendliness, and safety in mind. From customizable blade configurations to easy maintenance and the ability to handle even challenging materials, the GP20 offers the reliability and efficiency that innovators need to stay ahead.
At 3devo, we’re proud of the thoughtful engineering that goes into every aspect of our products, and the GP20 Shredder is no exception. Our team’s insights demonstrate how this machine can seamlessly integrate into your workflow, enhancing your ability to turn plastic waste into valuable resources.
Whether you’re already using our Filament Maker or just starting to explore the benefits of in-house recycling, the GP20 Shredder is an investment that will pay off in increased productivity and reduced waste. If you’re ready to take your recycling capabilities to the next level, we’re here to help you get started.
Discover the GP20 Plastic Shredder
Explore the full list of features available with our in-house plastic recycler.
Frequently Asked Questions (FAQs)
The GP20 Shredder is designed to handle a wide range of plastics, including common materials like ABS, PLA, PET, and more. It’s also capable of processing tougher materials, such as PEEK combined with carbon fiber, though we recommend consulting with us for specific guidance on more challenging materials.
Changing the blade configuration is straightforward and can be done by following the user manual. The GP20 offers multiple configurations to handle different shredding needs. If you prefer, we can pre-configure the blades based on the materials you intend to process before shipping the shredder to you.
The GP20 Shredder is equipped with several safety features, including interlocking components that prevent the machine from starting if any part is not securely connected. Additionally, the shredder will not operate unless the container bin is attached, ensuring that shredded material doesn’t spill out.
The GP20 Shredder is designed with ease of maintenance in mind. Key components, like the granulator rotor, can be removed with just one bolt, allowing for thorough cleaning. The removable scraper combs also make it simple to maintain optimal performance and prevent material buildup.
Yes, the GP20 is capable of processing larger and irregularly shaped items. With customizable blade configurations, the shredder can be optimized to handle a variety of material sizes and shapes, ensuring efficient shredding.
The GP20 Shredder features an LED interface that provides clear error messages, making it easy to identify and resolve issues. If you need further assistance, our Customer Service team is available to help troubleshoot and guide you through the process.
Absolutely! The GP20 Shredder is compact yet powerful, making it an excellent choice for both small-scale and larger operations. Its flexibility and user-friendly design ensure that it can meet the needs of a variety of environments.
Share this
- August 2024 (3)
- July 2024 (6)
- June 2024 (3)
- May 2024 (2)
- April 2024 (2)
- March 2024 (1)
- January 2024 (1)
- November 2023 (2)
- October 2023 (5)
- September 2023 (2)
- August 2023 (1)
- May 2023 (1)
- January 2023 (1)
- December 2022 (3)
- August 2022 (1)
- June 2022 (1)
- May 2022 (2)
- April 2022 (2)
- March 2022 (7)
- February 2022 (2)
- January 2022 (3)
- December 2021 (3)
- November 2021 (3)
- October 2021 (2)
- September 2021 (3)
- August 2021 (3)
- July 2021 (2)
- June 2021 (1)
- March 2021 (1)
- October 2020 (1)
- June 2020 (1)
- May 2020 (1)
- April 2020 (4)
- November 2019 (1)
- July 2019 (2)
- June 2019 (1)
- May 2019 (1)
- March 2019 (1)
- November 2018 (1)
- September 2018 (1)
- January 2018 (1)
- October 2017 (1)
- September 2017 (1)
- July 2017 (1)
- June 2017 (1)
- May 2017 (1)
- January 2017 (1)
- December 2016 (3)
- November 2016 (2)
- October 2016 (1)
- May 2016 (2)
- August 2015 (2)
- July 2015 (1)