The one desiccant dryer
for filament making.
Meet the Vismec DW14 dehumidifying dryer.
Compact, energy-efficient and high-performance dryer with honeycomb technology, optimal for drying thermoplastics used for producing filament.
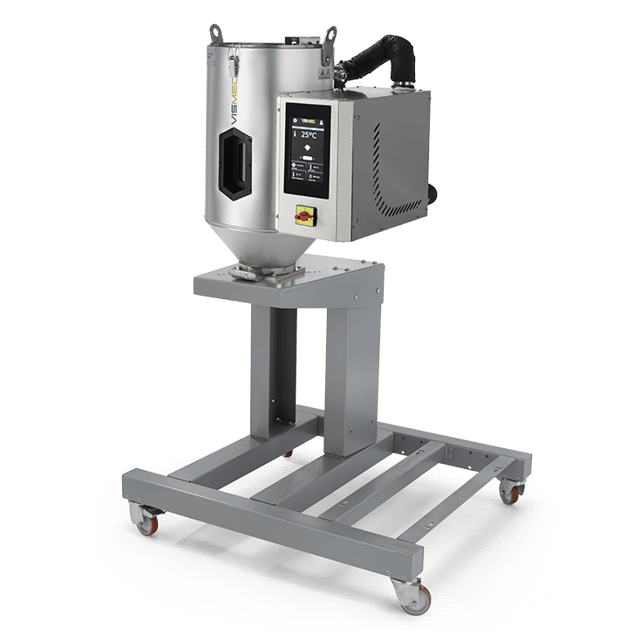
Key Features of the Desiccant Dryer
Honeycomb Technology
Programmable Timer
Schedule the drying to start at any time, allowing you to start production at your convenience.
Material Pre-Sets
The dryer includes a list of common thermoplastic settings, with pre-set times and temperatures.
Material Protection
Repairability
Compact, modular system with tool-free access for easy cleaning, maintenance, and material changes.
The New Generation of Desiccant Dryers
The desiccant wheel dryer is a far more efficient, more compact and less maintenance-requiring desiccant dryer. Traditional dehumidifying dryers use a large volume of molecular sieves in pellet form composed by at least 30% of clay, which tends to degrade very easily over time.
The desiccant wheel employs a different approach, where the pure molecular sieve is applied to a synthetic substrate, rolled into a cylindrical honeycomb structure and covered by a steel protection.
The dryer requires minimal maintenance, consistently maintains a stable dew point, does not require cooling water or air connections, and takes up little floor space.
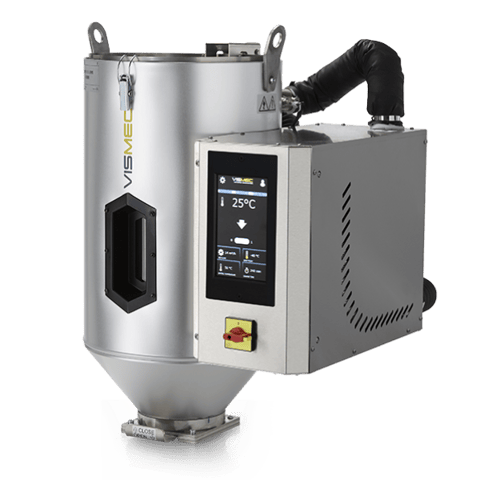
How It Works
The desiccant wheel is rotating driven by a step motor through 3 main sections:
- Drying: In the first section the humid process air coming from the material hopper through a return air filter is dried in two stages and the dry air is returned by the process blower through a heating chamber to the material in the drying hopper.
- Regeneration: Parallel to that a part of the turning wheel is in regeneration with its own dedicated heat chamber and regeneration blower.
- Cooling: In the cooling section a part of the wheel is cooled down before it returns back into the drying process.
Perfect for Filament Extruding
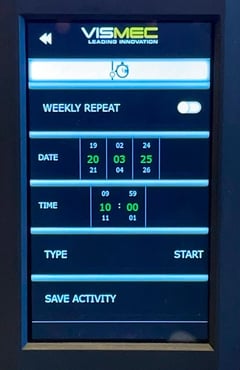
Programmable Timer
The Vismec Dryer DW14 is equipped with a programmable weekly timer, allowing you to schedule the dryer to begin heating and drying. This way the material is ready when production needs to start.
You can also configure when the dryer should stop and start cooling down. This not only ensures a smooth transition between the drying phase and the production phase, but also helps maintain the efficiency of the dryer.
With the programmable weekly timer, you optimize the drying process and ensure everything is ready for production at the right time.
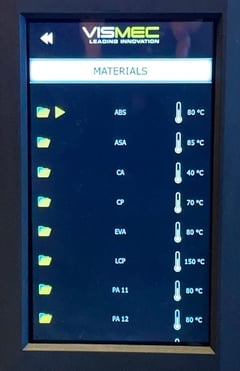
Material Pre-Sets
The Vismec Dryer DW14 allows you to set drying parameters manually or automatically by selecting a material from its built-in preset list. This list includes commonly used thermoplastics, each with recommended drying times and temperatures.
Operators can also customize these presets by assigning specific airflow, dew point, and temperature values to each material. This helps ensure optimal drying conditions every time, reducing preparation time and preventing moisture-related extrusion issues.
By using material presets, you streamline the drying process—an essential step for producing consistent, high-quality filament.
Advanced Drying
Honeycomb Technology
Thanks to this cutting-edge technology, there is no longer need for loose molecular grains within the system that dry out over time and contaminate the plastic granulate by crushing. Instead, the honeycomb dryer utilizes directly attached molecular material, eliminating the need for unnecessary clay for heating.
This has several advantages for the drying process:
- The moist process air can now regenerate the at much lower temperatures.
- It ensures a stable process, avoiding the fluctuations that occur with a traditional twin tower dryer.
- It only needs replacement when it is actually worn out, contrary to a twin tower dryer.
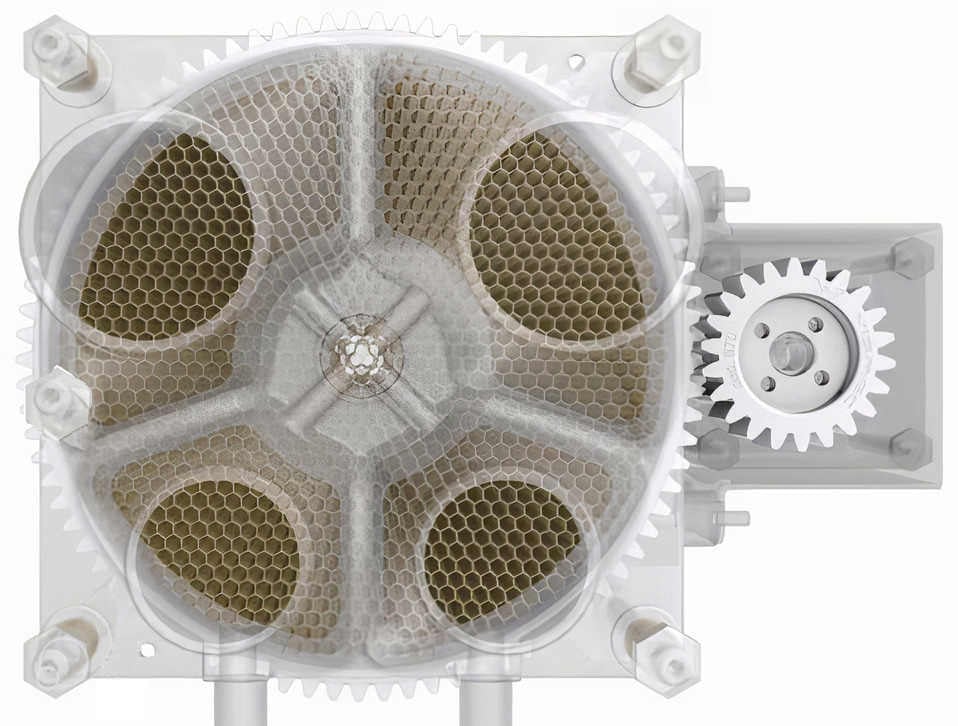
SMART Mode
This function accomplishes two key objectives: firstly, it optimizes energy consumption, and secondly, it prevents the raw material from overdrying. This is done by monitoring the temperatures at both the entry and exit points. When a 20 degree difference between these temperatures is detected, the SMART mode will automatically decrease the process air, thereby reducing the energy usage of the process blower, which is the main energy consumer aside from regeneration.
Material Protection Management
This feature is particularly useful for temperature-sensitive materials. Besides decreasing the process airflow, it also reduces the temperature to avoid overdrying. This not only guarantees further energy savings but, most importantly, plastic is protected from excessive heat.
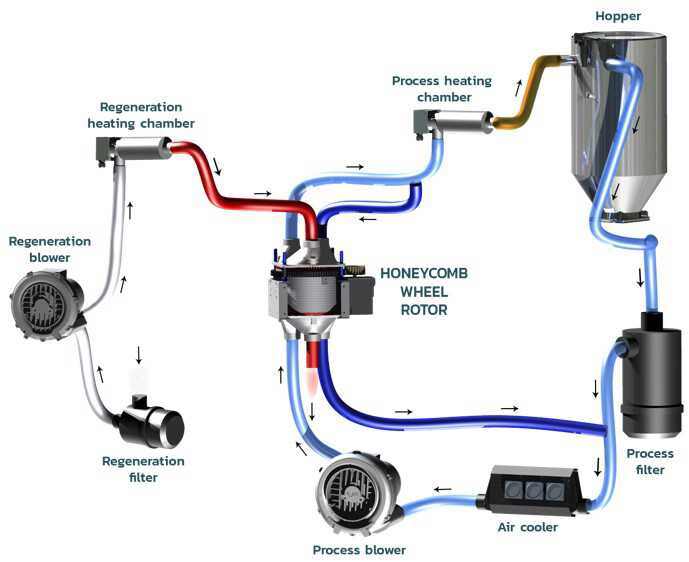
More Details
Constant and adjustable dew point of down to -40°C
Energy saving up to 40% and more
No need of compressed air or cooling water connections
Dryer is removable to allow easier maintenance
Ability to set up custom material recipes
Drying temperatures up to 185°C
Automatically or manually adjustable process air flow
Visual and acoustic alarm, with a weekly timer function
Protects the material from over drying and degradation
Automatic adaption of the drying process to the production needs
Prevents undried material from reaching the production machine
5 Years warranty on the desiccant wheel
Optional Add-ons
- Integrated or external portable dew point sensor
- Bio-material version for drying temperatures below 50°C
- Automatic throughput control in combination with the HALO
- Integration in the Vismec Supervision system 4.0 to operate from a PC, tablet or smart phone or other external management systems
- Filter sensor to prevent filter clogging
- Clean room version for medical and pharma applications
- Remote control
- Various mobile and stationary frames with and without castors
- Selection of suction boxes with different outlets and diameters
- Integrated brushless conveying system “feeding kit”
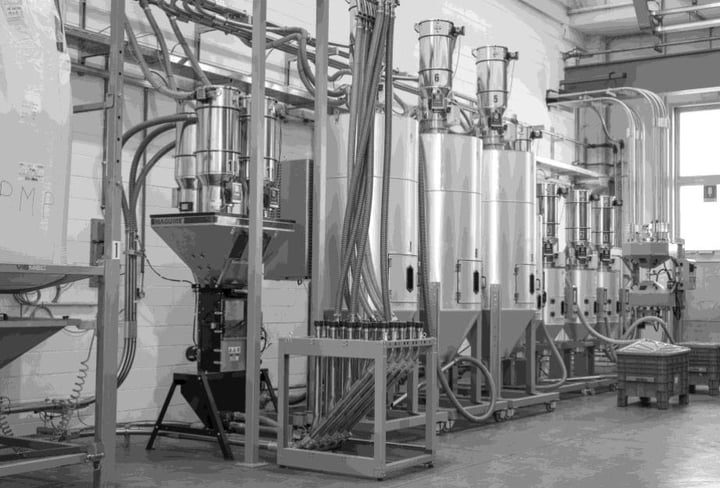
Specifications
Dryer and Hopper Combinations - Dimensional Table
Throughput Table
[h]
Indications given for free flowing materials in granules at min. and max. drying time.
Enhance your filament extrusion process.
Whether you're processing recycled plastics, engineering-grade polymers, or bio-based materials, the DW14 ensures your filament is ready for high-performance 3D printing applications.
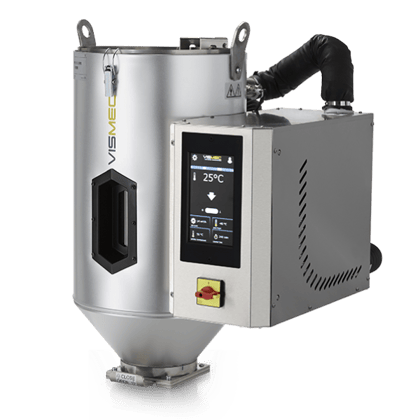
Vismec Dryer DW14 FAQ
A desiccant dryer is an industrial drying system that removes moisture from hygroscopic materials using a desiccant material like silica gel or molecular sieves. These dryers are commonly used in filament extrusion to prevent moisture-related defects such as bubbling, brittleness, and inconsistent extrusion quality.
A desiccant wheel dryer is a more advanced type of desiccant dryer that uses a rotating honeycomb desiccant wheel instead of loose desiccant beads.
The honeycomb desiccant wheel technology provides more consistent drying, lower energy consumption (up to 40% savings), and reduced maintenance compared to traditional two-tower dryers.
Yes, drying your thermoplastic material before extrusion is essential to produce high-quality filament. The Vismec Dryer DW14 ensures that your thermoplastics are free from moisture, preventing bubbles, degradation, and inconsistent extrusion. Without proper drying, your filament may suffer from poor mechanical properties, surface defects, and diameter inconsistencies.
If you want to know if your project is feasible, book a meeting with a material specialist here.
The Vismec Dryer DW14 is a compact, high-performance desiccant wheel dryer. It is designed for efficient drying of thermoplastic material, using honeycomb desiccant wheel technology to ensure stable moisture removal while reducing energy consumption.
dehumidifying
Yes, you can buy the Vismec Dryer DW14! The estimated delivery time is around 8 weeks. If you would like to enquire about the Vismec Dryer DW14 feel free to book a meeting with our Extrusion Specialists and we will give you all the details.
Yes, you can use the Vismec Dryer DW14 to dry plastic granulate produced by the GP20 Plastic Shredder. The GP20 shreds plastic into granulate smaller than 4mm, perfectly suitable for drying in the DW14.
Our Blog
Stay up to date with what is new in our industry, learn more about the upcoming products and events.
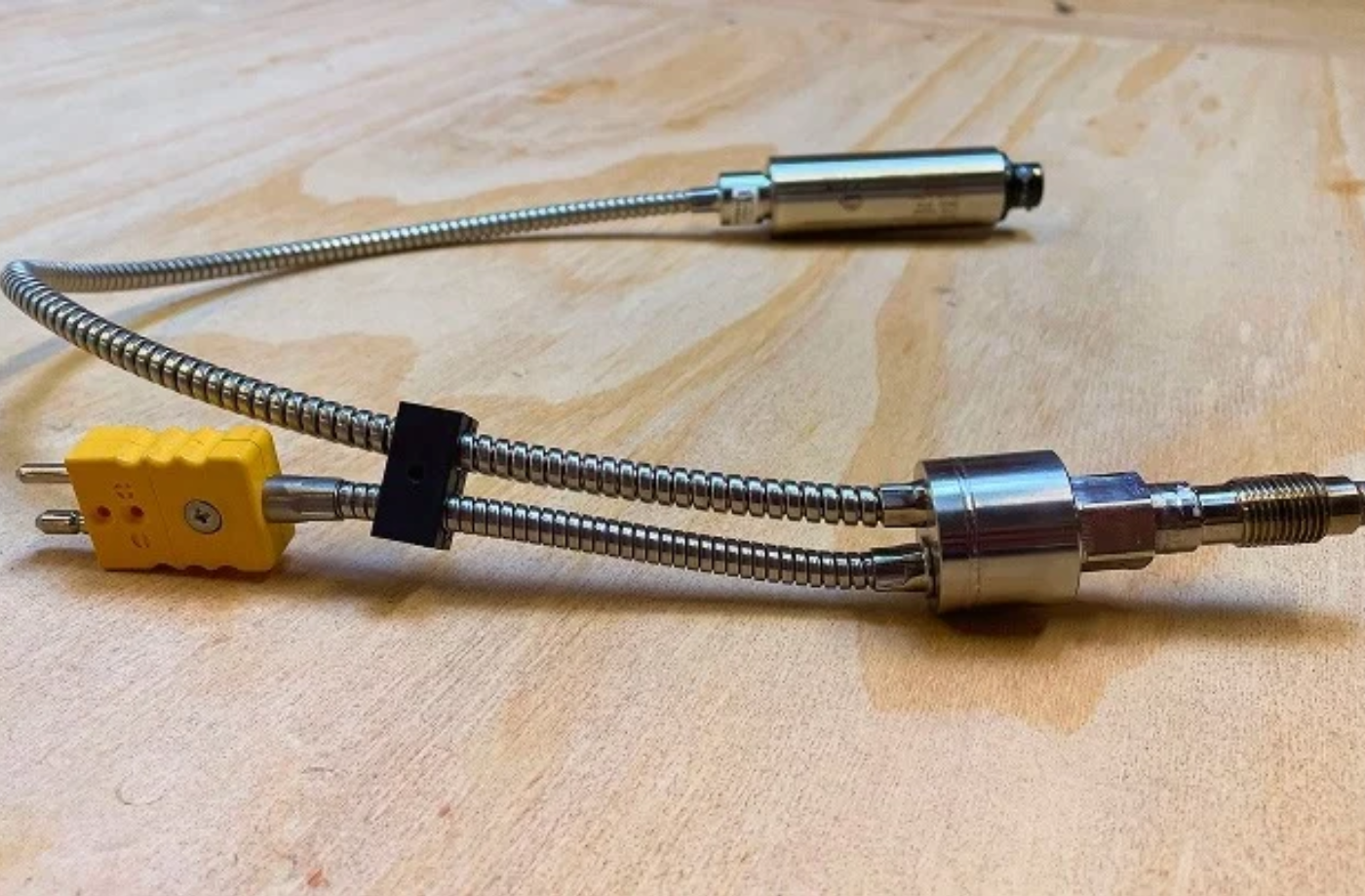
How We're Developing a Pressure Sensor for the Extrusion Process
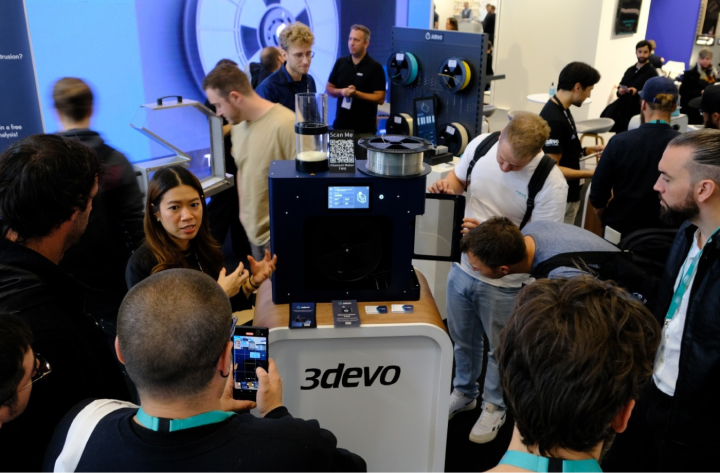
Filament Maker TWO vs. Alternatives: Compare Filament Extruders
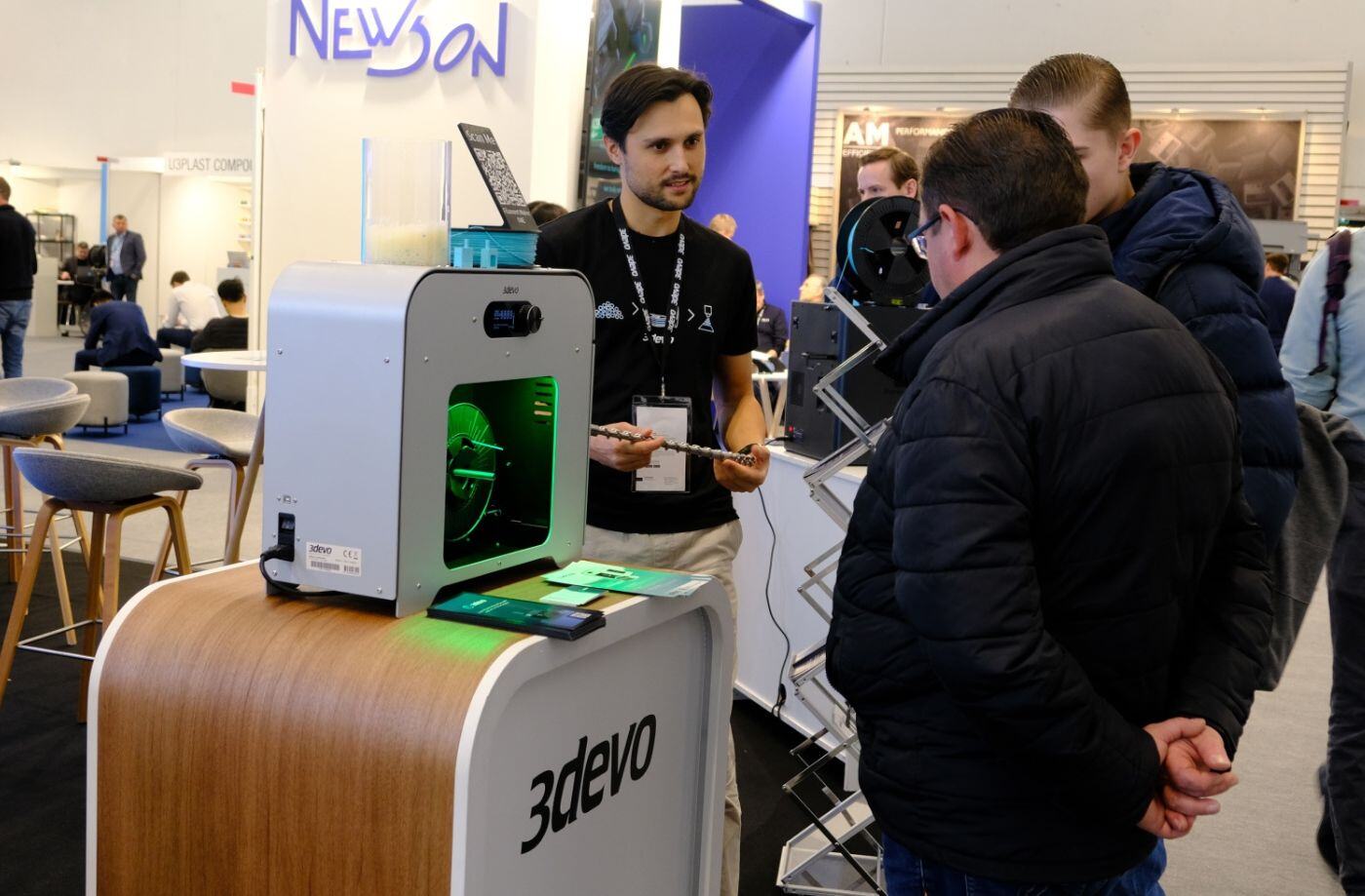
3devo 2024 Highlights: Reflecting on a Year of Growth and Change
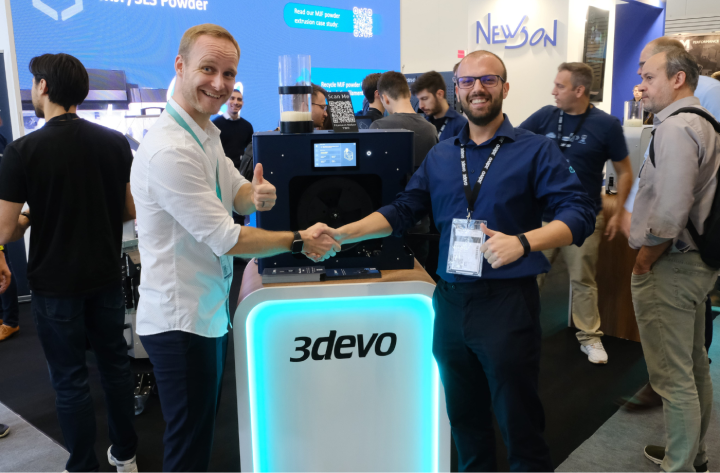
Gauging our Impact in Filament-Making: Formnext 2024 Recap
Need a starting point?
We provide material analysis, tailored workshops and dedicated support to guide you to success.