Filament Recycler
The 3D printing community urgently needs to recycle excess plastic from failed prints and reuse filaments. At 3devo, we offer a comprehensive filament recycler solution that converts plastic waste into premium 3D printing filament. Our technology empowers innovators and businesses to embrace sustainability by transforming discarded plastic into reusable filament. This process promotes a circular economy and reduces environmental impact. Whether recycling failed prints, outdated prototypes, or other plastic items, 3devo provides the tools to turn waste into valuable resources.
Close the Loop with Our Filament Recycler Solution
Preventing plastic waste from entering nature requires closing the loop. At 3devo, we offer a complete desktop solution based on the circular economy concept, enhancing the value of waste. From design to production, we have developed machines to recycle plastic and transform it into 3D printing filament, delivering a smart, cost-effective, and adaptive solution for 3D production.
Our solution includes the GP20 Plastic Shredder, which transforms plastic into granules. These granules can then be processed by our Filament Makers. The Filament Maker ONE creates customized filament reels, and this year, we will release the Filament Maker TWO, offering a faster and more sustainable solution. This streamlined ecosystem encourages the widespread reuse of plastics, promoting sustainable and environmentally friendly practices.
Filament Recycling Systems
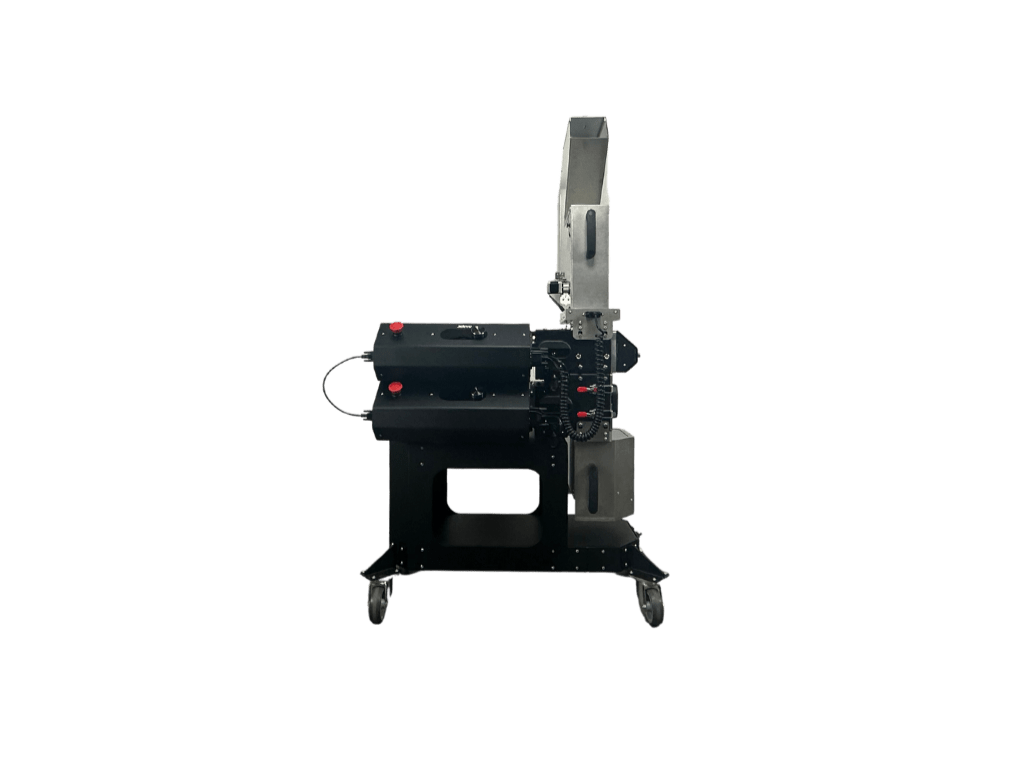
Plastic Shredder
The GP20 Plastic Shredder efficiently recycles plastics into granulate-size material with smart, customizable features and integrated safety, perfect for any industry.
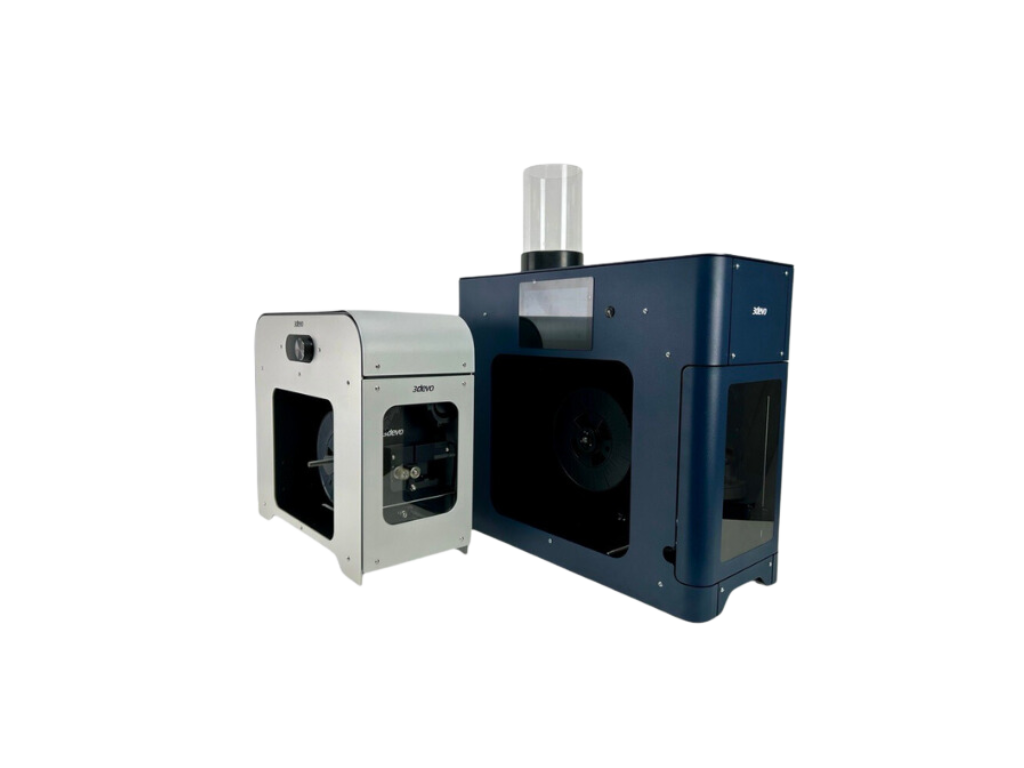
Filament Makers
The Filament Makers from 3devo empower limitless innovation, allowing you to create custom 3D printing filaments with precision, versatility, and ease—perfect for research, prototyping, and material development.
Transform Your Plastic Waste into High-Quality Filament
Recycling undesired prints and plastic waste with our cutting-edge filament-making solution helps reduce waste and supports sustainable practices. Here’s how our solution can benefit you:
Complete In-House Solution
Our advanced system includes the GP20 Plastic Shredder to turn plastic waste into granules, and our Filament Makers to transform these granules into high-quality filament. This integrated approach ensures a seamless recycling process, empowering you to create custom filaments tailored to your specific needs.
Comprehensive Plastic Waste Recycling
Transform not just old prints, but all types of plastic waste from your company, industry, or research facility into new 3D printing material. Our solution converts various plastic waste types into valuable resources, promoting sustainability and reducing clutter.
Achieve Superior 3D Printing Quality
Take your 3D printing to the next level with our system, which allows you to produce high-quality, customized filaments that meet your specific requirements. This enhances the quality and performance of your projects, ensuring optimal results.
Expert Guidance and Collaboration
Our in-house material specialists and customer success team are dedicated to helping you reach your goals. The chance to test your materials, including MFI (Melt Flow Index) testing, before purchasing the machine. This ensures compatibility and optimal performance, elevating your 3D printing capabilities.
The Complete Recycling Workflow
Our streamlined process guides you through converting plastic waste into new filament:
Shred
Begin by shredding your plastic waste with the Plastic Shredder.
- Efficiently reduces various types of plastic waste,
including failed prints and outdated prototypes. - Turns waste into small, manageable granules.
- Prepares the material for the next step in the recycling process.
- Designed for consistent performance.
- Easy to operate and maintain.
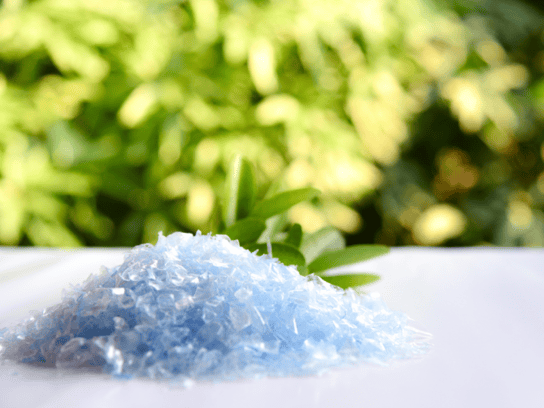
Dry (optional)
Ensure the shredded material is dry before extrusion.
- Remove any moisture to prevent defects in the filament.
- Use a suitable drying process to maintain material integrity.
- Enhances the quality of the final filament.
- Helps maintain consistent extrusion performance.
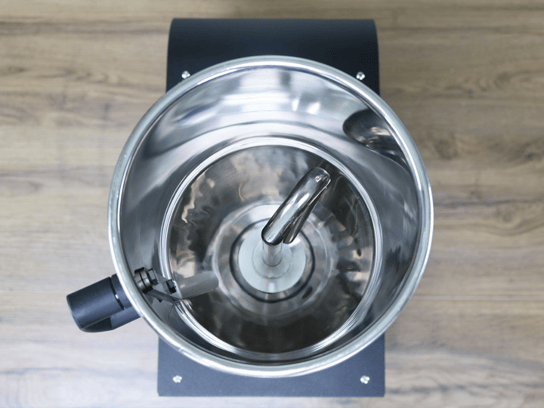
Extrude
Next, use our Filament Makers to convert the shredded plastic granules
into high-quality filament.
- Filament Maker ONE and the upcoming Filament Maker TWO
precisely control temperature and extrusion parameters. - Ensures consistent diameter and quality of the filament.
- Transforms waste into valuable filament for 3D printing.
- Allows customization of filament properties to meet specific needs.
- User-friendly interface for easy operation.
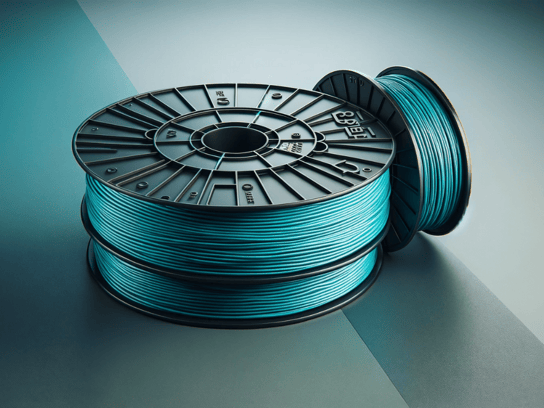
Finally, utilize the recycled filament in your 3D printer.
- Supports sustainable manufacturing.
- Reduces plastic waste and lowers material costs.
- Enables cost-effective and environmentally-friendly 3D printing projects.
- Produces high-quality prints with consistent results.
- Contributes to a circular economy by reusing plastic waste.
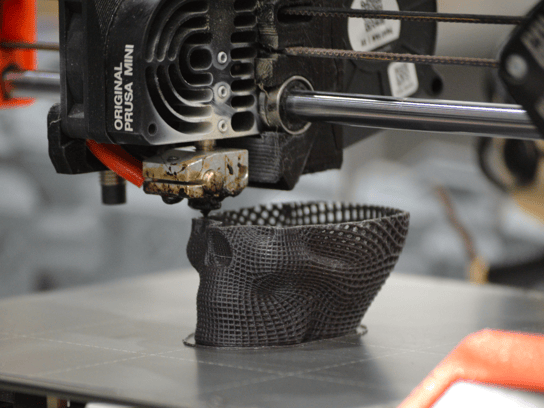
Interactive Education for Scholars and Innovators
Revolutionize the way education is delivered with Filament Makers. Dive into the world of hands-on learning where students and researchers alike can actively participate in the creation of custom filaments, delve into the exploration of material properties, and contribute to environmental sustainability by recycling plastic waste. This immersive approach not only elevates educational outcomes but also cultivates a culture of innovation and ecological responsibility in academic environments.
%20(2)%20(1).jpg?width=6240&height=3512&name=Educator%20Blog%20pic%201%20(1)%20(2)%20(1).jpg)
Prototyping for Industry
Elevate your industrial prototyping process with our Filament Makers ONE and TWO. These machines allow for rapid iteration and small batch production, enabling quick testing and validation of new designs. By facilitating a more efficient evaluation of materials and designs, they significantly cut down on the time and expenses typically associated with conventional manufacturing techniques.
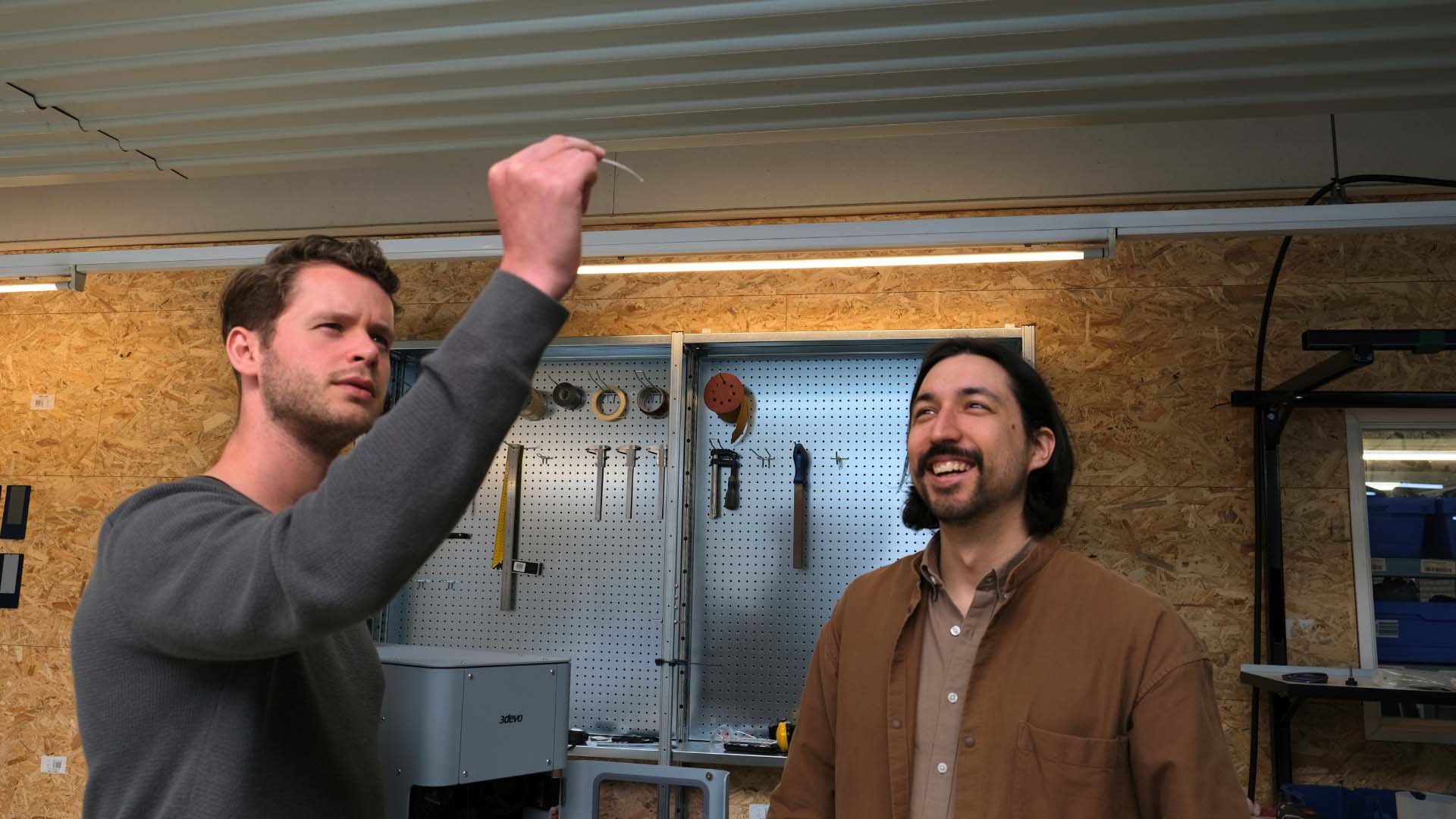
Sustainable Manufacturing
Enhance eco-friendly practices in production by transforming plastic waste into filaments with the innovative use of our Filament Makers. This process reduces environmental impact and supports a circular economy by reusing materials and minimizing waste.
-min.png?width=1920&height=1080&name=Filament%20Makers%20Page%20(1920%20x%201080%20px)-min.png)
Frequently Asked Questions
A filament recycler, such as the GP20, converts plastic waste into high-quality filament. The process involves shredding plastic into granules, which are then dried (optional) and extruded into new filament using specialized machines.
The 3devo solution helps reduce plastic waste by transforming discarded plastic into reusable filament. This process starts with the GP20 shredding plastic waste into flakes. These flakes can then be dried to remove moisture, ensuring high-quality filament production. Finally, the dried flakes are fed into filament makers, which precisely control temperature and extrusion parameters to produce consistent, high-quality filament. By converting plastic waste into valuable resources, the 3devo solution promotes a circular economy, reduces environmental impact, and supports sustainable manufacturing practices.
Yes, the 3devo solution handles various types of plastic waste, including failed prints, outdated prototypes, and other plastic items from different sources.
3devo provides support through in-house material specialists and a customer success team. Customers can test their materials, including MFI (Melt Flow Index) testing, before purchasing to ensure compatibility and optimal performance.
Using a filament recycler like the GP20 Plastic Shredder reduces plastic waste, lowers material costs, and supports sustainable practices. It also allows the production of high-quality, customized filaments that enhance the quality and performance of 3D printing projects.
Read more about Filament Recycling
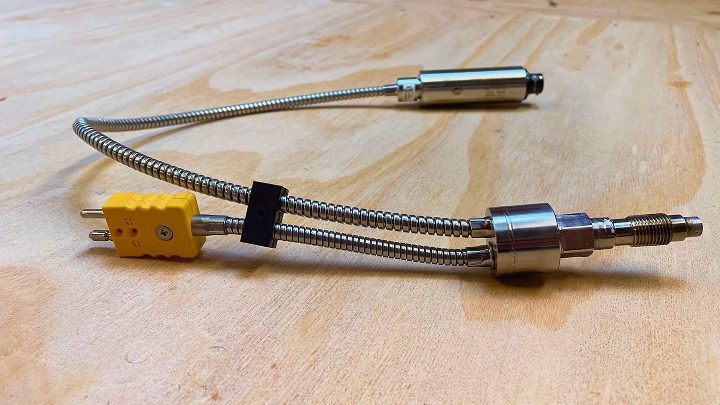
How We're Developing a Pressure Sensor for the Extrusion Process
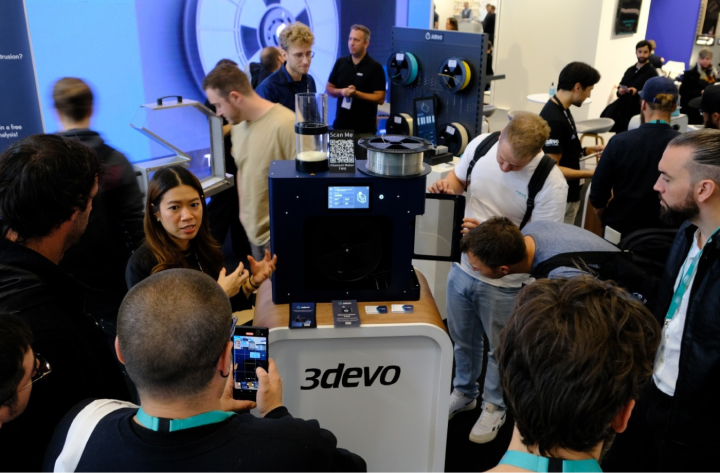
Filament Maker TWO vs. Alternatives: Compare Filament Extruders
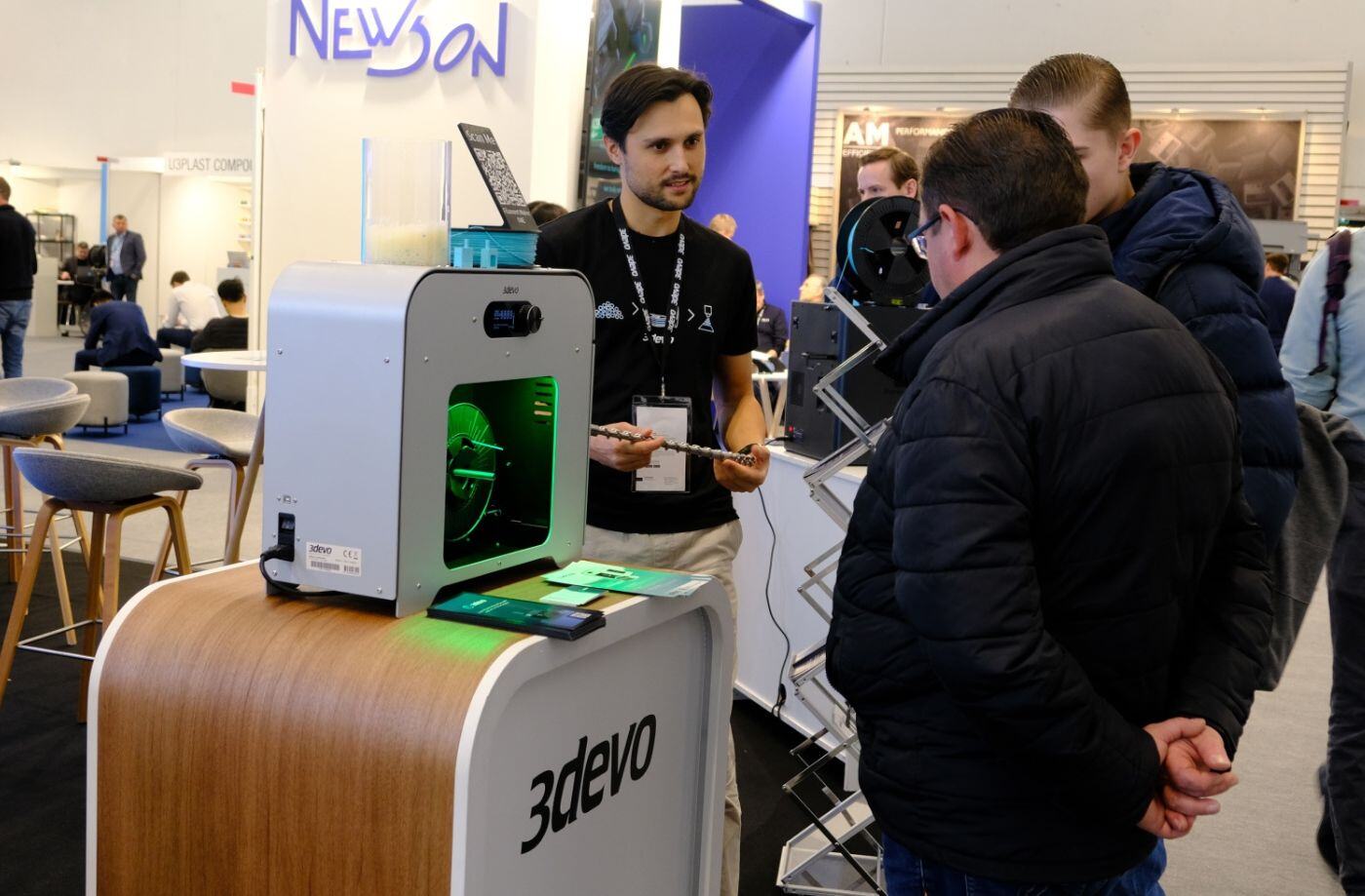
3devo 2024 Highlights: Reflecting on a Year of Growth and Change
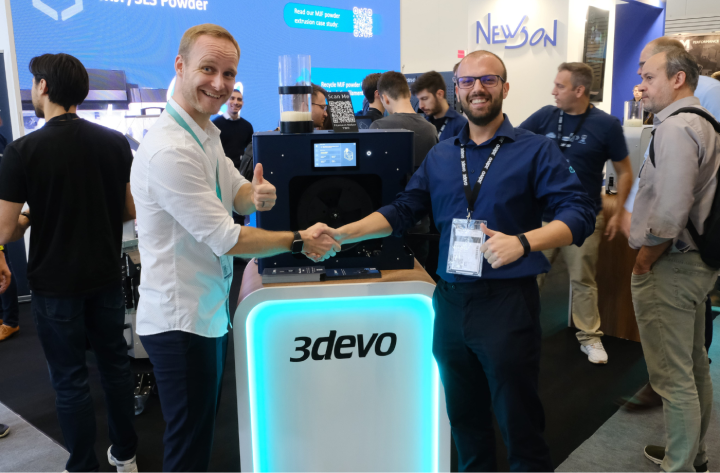