Share this
HDPE: Combining with Additives and Polymers for Better Results
by Louis Rinaldo on Sep 16, 2024 5:18:29 PM
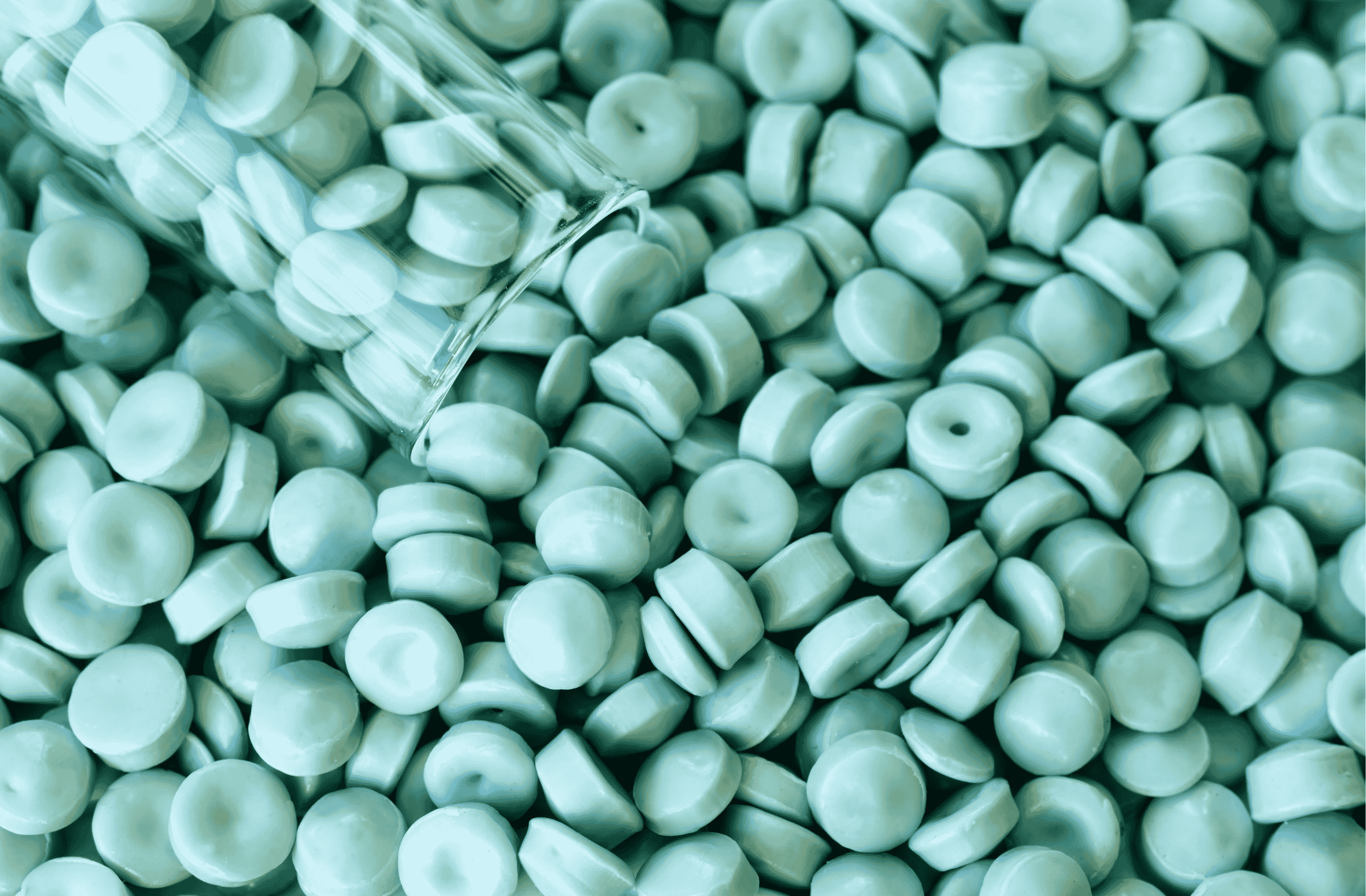
In a previous blog post, The Versatility of HDPE Filament for 3D Printing, we highlighted the versatility of HDPE (High-Density Polyethylene) filament in 3D printing, especially focusing on its strength, flexibility, and chemical resistance. However, like many high-performance polymers, HDPE comes with its unique set of challenges, particularly its high crystallization rate, which can make extrusion and 3D printing tricky.
In this post, we’ll take a deeper dive into how HDPE’s behavior can be modified by incorporating different additives and polymers to suit specific end applications, while also addressing some of the issues inherent in its crystallization process.
The Crystallization Challenge of HDPE
HDPE is widely used across industries due to its excellent mechanical properties and chemical resistance. However, it is notorious for its high crystallization rate, which can complicate extrusion processes. When we talk about polymers like HDPE, we refer to their molecular chains, which are long and can either be amorphous (disorganized) or crystalline (aligned in a structured, dense format). The key challenge with HDPE is that it forms crystalline structures quickly during the cooling process.
In the extruder, HDPE is fully melted and exists in an amorphous state. But once it exits the nozzle and begins to cool, its molecular chains start to align into a crystalline structure. This results in significant shrinkage, as crystalline structures take up less space than amorphous ones. The shrinkage can lead to issues like cross-sectional ovality and warping in 3D prints, especially during uneven cooling.
As mentioned in the previous blog, HDPE is a valuable material in many industries due to its wear resistance. However, in the context of 3D printing and extrusion, the crystallization process is a major obstacle. While it’s theoretically possible to prevent crystallization through rapid cooling (quenching), this approach is not feasible for 3D printing or small-scale extrusion, both of which typically rely on air cooling. Therefore, alternative methods are needed to address this issue.
Tackling the Crystallization Problem with Additives
One effective solution to counter HDPE’s crystallization and shrinkage problems is to incorporate additives. When we combine HDPE with non-deformable additives, we create a composite material with improved dimensional stability. A composite consists of two parts: the polymer matrix (HDPE) and the filler (additive). These additives don’t melt or chemically react with the HDPE but act as stabilizers within the matrix.
Additives like carbon fiber or PTFE (polytetrafluoroethylene) can be used as mechanical fillers. These materials retain their shape during the cooling process, preventing excessive shrinkage. Since they don’t crystallize or shrink the way HDPE does, they help maintain the composite’s overall shape and structure. By incorporating more of these fillers, the resulting composite becomes increasingly stable during cooling.
For example, carbon fiber additives in HDPE can significantly reduce the warping and shrinkage typically associated with extrusion and 3D printing. The additive acts as a counterbalance to HDPE’s natural tendency to shrink, ensuring a more dimensionally stable end product.
However, while additives can solve the crystallization problem, they also present some challenges. Adding too much filler can affect the material’s properties, potentially making it less flexible or chemically resistant. This is particularly important in industries like healthcare, where the chemical properties of the material may be critical. For instance, adding carbon fiber may enhance HDPE's mechanical properties but could alter its chemical inertness, which is essential in medical applications.
Moreover, the inclusion of additives can complicate the extrusion process. The polymer matrix and filler must be thoroughly mixed to ensure even distribution, and the extrusion parameters may need to be adjusted to account for the altered material properties.
Blending HDPE with Other Polymers
Another effective approach for managing HDPE’s crystallization behavior is blending it with other types of polyethylene. HDPE belongs to a family of polyethylene materials, each with its own characteristics. By blending HDPE with polymers that have lower crystallization rates, we can improve its processability without compromising its core properties.
The most common members of the polyethylene family include:
- HDPE (High-Density Polyethylene): Known for its strength and low cost, but challenging due to its high crystallization rate.
- LDPE (Low-Density Polyethylene): With longer, more disordered molecular chains, LDPE crystallizes less readily and is easier to process.
- LLDPE (Linear Low-Density Polyethylene): Similar to LDPE but more flexible, making it ideal for films (sheets).
- UHMWPE (Ultra-High Molecular Weight Polyethylene): This material has very long molecular chains and a uniquely high crystallinity. However, its special nature makes it less relevant for general extrusion applications.
Blending HDPE with LDPE or LLDPE can reduce its crystallization rate and make it easier to extrude. Since these materials have overlapping thermal processing windows, they are compatible with each other in extrusion processes. By combining them, we create a polymer blend that retains the desirable properties of HDPE (strength, durability) while mitigating the challenges of shrinkage and crystallization.
However, for successful blending, the polymers must have similar viscosities. Viscosity is a key property in extrusion, as it determines how easily the molten material flows through the extruder. If HDPE and LDPE or LLDPE have significantly different viscosities, they won’t mix properly, leading to uneven extrusion and inconsistent material properties. To avoid this, a pre-compounding step, such as twin-screw extrusion, can be used to homogenize the blend before filament production begins.
Particle size and shape are also important considerations in polymer blending. Inconsistent feedstock can lead to uneven mixing in the extruder, resulting in poor material properties and extrusion issues. Ensuring that the polymers are similarly sized and shaped will help achieve a smooth, even blend.
Applications of HDPE Blends and Composites
When considering the application of HDPE and its blends, it’s important to balance processability with the specific requirements of the end product. For some applications, dimensional stability and resistance to warping are paramount, while for others, flexibility, chemical resistance, or even cost may be more critical.
For example, in the automotive industry, HDPE composites with carbon fiber or other additives may be used to create lightweight, high-strength parts that resist deformation under heat. However, in industries like healthcare or packaging, where chemical inertness and low cost are priorities, pure HDPE or blends with LDPE may be more suitable.
One notable trade-off in blending HDPE with additives or other polymers is the potential increase in cost. HDPE is widely regarded as one of the most affordable and accessible plastics, but enhancing it with specialized additives or complex blends can raise the price significantly. In some cases, this added cost is justified by the improved performance of the material. In other cases, it may be more cost-effective to use an unmodified form of HDPE or blend it with a cheaper, more readily available polymer.
For industries with strict material requirements, such as medical device manufacturing, the impact of additives or blending on the material’s properties must be carefully considered. For example, while adding PTFE might reduce shrinkage, it could alter the chemical properties of the HDPE, making it unsuitable for applications requiring sterilization or chemical resistance.
Conclusion: Customizing HDPE for Diverse Applications
HDPE is a versatile polymer with applications across many industries, but its high crystallization rate can present challenges during extrusion and 3D printing. By incorporating additives or blending it with other polymers, these challenges can be mitigated, allowing HDPE to be tailored for specific applications. Whether you need improved dimensional stability, flexibility, or chemical resistance, there are multiple ways to customize HDPE’s properties.
Choosing the right combination of additives and polymers depends on the specific needs of your project. The application will dictate the performance requirements, cost considerations, and processing parameters. By understanding HDPE’s behavior and how it interacts with other materials is key to making informed decisions that improve both the production process and the final result. Our experienced team is available to offer guidance and share their knowledge, helping you find the best approach for your project.
Start Your Project
If you're ready to explore your options, schedule a call with our team to get started.
Frequently Asked Questions (FAQs)
HDPE filament is highly valued in 3D printing due to its combination of strength, chemical resistance, and durability. These properties make it a go-to material for industries like automotive, packaging, and construction, where parts need to withstand significant wear and exposure to harsh conditions. However, HDPE is known for being tricky to work with because of its high crystallization rate, which can cause shrinkage and warping during printing. With the right approach—such as using additives or blends to adjust its behavior—it’s possible to unlock HDPE’s full potential and make it an excellent choice for various 3D printing applications.
When comparing HDPE to common materials like PLA or ABS, HDPE stands out for its durability and resistance to chemicals and environmental stress. PLA, while easy to print, lacks the toughness HDPE offers, while ABS provides some strength but can be less chemically resistant. The challenge with HDPE is that it has a much higher crystallization rate, which can lead to issues like shrinkage and warping during the cooling process. This makes HDPE less forgiving for novice printers. However, by carefully controlling the cooling or mixing it with other polymers, you can manage these issues and achieve more stable, precise prints.
HDPE is ideal for applications that require high durability, impact resistance, and chemical stability. For example, in the automotive industry, HDPE is used for creating durable parts that can handle exposure to fuels and oils. In packaging, it’s often chosen for containers that need to resist moisture and chemicals. HDPE’s versatility also makes it useful in construction, where materials need to withstand physical stress and environmental exposure. However, the specific requirements of your project, such as flexibility or chemical resistance, will dictate whether HDPE is the best choice for your application.
Shrinkage and warping are common challenges when printing with HDPE due to its high crystallization rate. To reduce these issues, one effective method is to blend HDPE with other polymers, like LDPE (Low-Density Polyethylene), which has a lower crystallization rate. You can also incorporate additives that stabilize the material during the cooling process, helping to maintain the shape and dimensional accuracy of your print. Our team of customer success managers can help you navigate these options, offering insights on the best additive or blending strategy for your specific printing setup.
Yes, we understand that investing in a filament maker can be a big commitment, which is why we offer flexible leasing and subscription models for the Filament Makers. This allows you to get started with HDPE filament production without the need for large upfront costs. Whether you're focused on experimenting with new materials or scaling up production, the leasing model gives you access to our advanced equipment while maintaining financial flexibility. Additionally, our customer success team will be available to assist you throughout the entire process, from setting up the machine to optimizing your material output.
Our new project partnership model goes beyond simply providing equipment—it’s designed to support you at every step of your material development journey. Instead of just selling machines, we work closely with you, offering tailored guidance from our in-house materials specialists and customer success managers. Whether you’re facing challenges with HDPE’s crystallization or exploring ways to blend HDPE with other polymers, our team is here to help. This partnership approach ensures that you not only have the right tools but also the expert support needed to achieve your project goals efficiently and successfully.
Yes, HDPE is highly recyclable and can be reprocessed into new filament for 3D printing. In fact, recycling HDPE is a great way to reduce waste and lower costs in your production process. Many companies are adopting HDPE recycling to create sustainable printing workflows. Our Filament Maker machines are designed to work with recycled materials, including HDPE, ensuring that you can maintain high-quality filament production while contributing to sustainability efforts. If you're new to recycling HDPE for 3D printing, our team can guide you through the process, from material preparation to extrusion settings, so you can get the best results from recycled filament.
If you're ready to begin developing custom HDPE filament, the first step is to book a call with our team. We’ll work with you to understand your project requirements, whether you're focusing on specific material properties, additives, or processing conditions. Our customer success managers and material specialists will help you identify the best combination of additives and polymer blends, set up your Filament Maker ONE or Filament Maker TWO, and fine-tune the production process to meet your goals. With our support, you’ll be able to confidently develop HDPE filament tailored to your specific applications.
3devo’s Filament Makers come with several advanced features that enhance HDPE filament production. Advanced temperature sensors provide precise control over the extrusion temperature, allowing for consistent and high-quality filament production. The integrated cooling system ensures uniform cooling of the filament, preventing warping and ensuring dimensional accuracy. Customizable settings allow for adjustments to extrusion speed, temperature, and other parameters to optimize filament production.
Share this
- March 2025 (1)
- January 2025 (1)
- December 2024 (2)
- November 2024 (3)
- October 2024 (4)
- September 2024 (2)
- August 2024 (3)
- July 2024 (6)
- June 2024 (3)
- May 2024 (2)
- April 2024 (1)
- March 2024 (1)
- January 2024 (1)
- November 2023 (2)
- October 2023 (5)
- September 2023 (2)
- August 2023 (1)
- July 2023 (1)
- May 2023 (1)
- December 2022 (3)
- August 2022 (1)
- June 2022 (1)
- May 2022 (2)
- April 2022 (2)
- March 2022 (7)
- February 2022 (2)
- January 2022 (3)
- December 2021 (3)
- November 2021 (3)
- October 2021 (2)
- September 2021 (3)
- August 2021 (3)
- July 2021 (2)
- June 2021 (1)
- March 2021 (1)
- October 2020 (1)
- June 2020 (1)
- May 2020 (1)
- April 2020 (4)
- November 2019 (1)
- July 2019 (2)
- June 2019 (1)
- May 2019 (1)
- March 2019 (1)
- November 2018 (1)
- September 2018 (1)
- January 2018 (1)
- October 2017 (1)
- September 2017 (1)
- July 2017 (1)
- June 2017 (1)
- May 2017 (1)
- January 2017 (1)
- December 2016 (3)
- November 2016 (2)
- October 2016 (1)
- May 2016 (2)
- August 2015 (2)
- July 2015 (1)