Share this
The Versatility of HDPE Filament for 3D Printing
by Gigi Palczer on Jul 2, 2024 10:39:36 AM
.png?width=800&height=640&name=HDPE%20Blog_pictures%20(2).png)
High-Density Polyethylene (HDPE) is gaining popularity in the 3D printing industry due to its excellent strength-to-density ratio and versatile properties. Here, we'll be delving into the characteristics of HDPE, its advantages for 3D printing, the process of creating HDPE filament using 3devo’s Filament Makers, and its practical applications.
What is HDPE?
HDPE is a thermoplastic polymer produced from the monomer ethylene. Renowned for its high tensile strength, durability, and chemical resistance, HDPE is suitable for various applications, including piping systems and plastic bottles. In 3D printing, the material's flexibility, impact resistance, and ease of processing make it extremely valuable.
Benefits of HDPE Filament
Strength and Durability:
HDPE's high impact resistance and tensile strength make it ideal for producing durable 3D printed parts that can withstand significant stress and strain. For example, in the automotive industry, HDPE is used to print car parts like fuel tanks and bumpers. These components need to endure constant mechanical stress and potential impacts, and HDPE's robust nature ensures they remain intact and functional over long periods.
Chemical Resistance:
HDPE exhibits excellent resistance to a wide range of chemicals, including acids and bases, making it suitable for applications exposed to harsh environments. For instance, in the chemical processing industry, containers and pipes made from HDPE can safely transport aggressive chemicals without degrading. This chemical resistance extends the lifespan of parts and reduces the need for frequent replacements, ensuring reliability in demanding conditions.
Lightweight:
Despite its strength, HDPE is relatively lightweight, beneficial for applications where weight reduction is crucial without compromising strength and durability. In the aerospace sector, for instance, printed HDPE can be used to create components that contribute to the overall weight reduction of aircraft. Lighter parts help improve fuel efficiency and reduce operating costs while maintaining the necessary structural integrity.
Flexibility:
HDPE's flexibility allows for creating parts that can endure bending and flexing without breaking, suitable for producing items such as containers and flexible joints. For example, HDPE is often used to print living hinges—thin, flexible sections connecting two rigid parts—commonly found in everyday items like caps and lids. These hinges need to flex repeatedly without snapping, and HDPE's flexibility makes it an excellent material choice for such applications.
Creating HDPE Filament with 3devo’s Filament Makers
3devo’s Filament Makers, including the Filament Maker ONE and Filament Maker TWO, are perfect for creating high-quality HDPE filament. These advanced machines handle various thermoplastics, ensuring consistent and precise filament production.
Filament Maker ONE:
Equipped to produce high-quality HDPE filament, the Filament Maker ONE offers precise temperature control, ensuring that the HDPE material is extruded at optimal conditions for consistent diameter and quality. A key benefit is that users are able to fine-tune extrusion settings, which is crucial when working with HDPE due to its relatively high melting point and tendency to shrink.
Filament Maker TWO:
Building on the capabilities of the Filament Maker ONE, the Filament Maker TWO includes advanced temperature sensors, an improved cooling system, and higher extrusion speeds, ensuring even greater control and efficiency. Its enhanced cooling system ensures that the filament solidifies quickly and uniformly, preventing common issues like warping or uneven diameter that can occur with HDPE. Additionally, the higher extrusion speeds mean that users can produce more filament in less time, increasing overall productivity without sacrificing quality.
Benefits of 3devo Filament Makers for Recycling HDPE
3devo’s Filament Makers are not just about producing new filament, but also about recycling and repurposing existing HDPE materials. Here’s how they help users make the most of their plastic waste:
-
Versatility in Material Handling: Both the Filament Maker ONE and TWO are champions when it comes to handling recycled HDPE. They make it possible to transform plastic waste into fresh, usable filament, supporting green initiatives and cutting down on the need for new plastic. Imagine turning old bottles and containers into brand-new, high-quality filament!
-
Precision and Consistency: With advanced temperature control and monitoring systems, users can trust that their recycled HDPE is extruded to the industry standard. This precision ensures your filament maintains high quality and consistency, even when starting with recycled materials. No more worrying about uneven prints or filament that doesn't quite match up.
-
User-Friendly Design: We know not everyone is a tech expert, so 3devo’s filament makers are designed to be super user-friendly. With intuitive interfaces and step-by-step guides, users find it easy to set up and start recycling HDPE into new filament. It's a great way to dive into sustainable practices without needing a technical background.
-
Efficiency and Speed: Time is precious, and with the Filament Maker TWO’s high extrusion speeds and efficient cooling systems, you can quickly produce spools of recycled filament in-house. This is especially handy for educational institutions and public labs where it can be necessary to maximize output in limited time.
HDPE as a Flush/Purging Material
HDPE is an excellent flush/purging material for filament makers due to its chemical properties, which allow it to effectively clean out residual materials in the extrusion system, preventing contamination and ensuring the purity of subsequent filament productions. This is particularly useful when switching between different types of plastics.
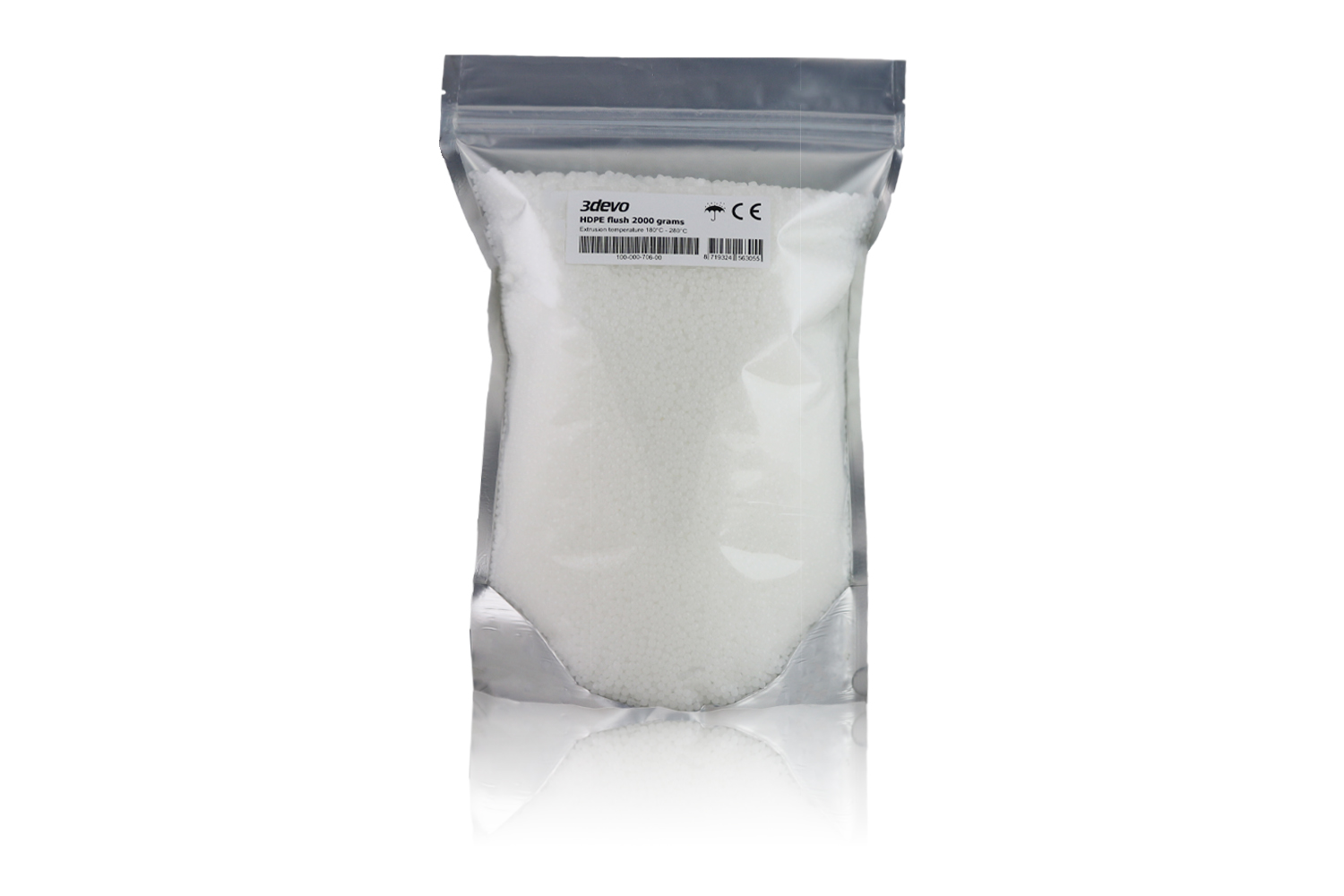
Why Use HDPE for Flushing?
-
Cost-Effective: HDPE is relatively inexpensive compared to other purging compounds.
-
Compatibility: Compatible with most thermoplastics, HDPE effectively purges the system without reacting adversely with other materials.
-
Ease of Use: HDPE’s properties make it easy to work with during the flushing process, flowing well through the extruder to ensure thorough cleaning.
-
Efficiency: HDPE quickly and efficiently removes residual materials from the extruder, minimizing downtime and improving overall production efficiency.
How to Use HDPE for Purging:
-
Prepare the Extruder: Ensure the extruder is at the appropriate temperature for HDPE extrusion (typically around 205°C to 240°C).
-
Introduce HDPE: Feed HDPE pellets into the extruder, allowing them to push out the residual material until the extruded HDPE is free of contamination.
-
Monitor the Process: Keep an eye on the extrusion process to ensure HDPE effectively removes all residual material, adjusting the temperature and feed rate as necessary.
-
Switch to New Material: Once the extruder is clean, switch to the new material you wish to extrude, ensuring a smooth and contamination-free transition.
Practical Applications of HDPE Filament
HDPE filament is versatile and can be used in various applications:
Prototyping: Ideal for prototyping due to its durability and ease of processing, HDPE allows designers to create robust prototypes for real-world testing.
Functional Parts: HDPE is suitable for producing functional parts such as containers, piping components, and industrial tools due to its strength and chemical resistance.
Educational Projects: HDPE’s ease of use makes it a great choice for educational projects, allowing students to explore its properties and applications.
Environmental Benefits of HDPE
Using HDPE for 3D printing has several environmental benefits:
Recyclability: HDPE is highly recyclable, and using it for 3D printing helps reduce plastic waste. HDPE waste can be reprocessed into new filament, promoting a circular economy.
Lower Carbon Footprint: Producing HDPE filament from recycled materials requires less energy compared to producing virgin plastic, resulting in a lower carbon footprint. This reduction in energy consumption helps decrease greenhouse gas emissions, contributing to environmental sustainability.
Durability and Longevity: The durability of HDPE means that products made from this material have a longer lifespan, reducing the need for frequent replacements and thereby minimizing waste.
Challenges and Considerations
While HDPE offers many advantages, there are some challenges to consider when using it for 3D printing:
Warping and Shrinkage: HDPE tends to warp and shrink during cooling, affecting the dimensional accuracy of printed parts. Proper temperature control and heated build platforms can mitigate these issues.
Adhesion: HDPE can be challenging to adhere to the print bed. Using adhesives or specialized build surfaces can help improve bed adhesion and prevent warping.
Case Study: Embry-Riddle Aeronautical University
Embry-Riddle Aeronautical University is a leading institution known for its innovation in aviation and engineering. The university’s Mechanical Engineering Department has been using 3devo’s Composer Filament Maker to create high-quality filament by mixing HDPE with phase-change materials (PCM). This effort aims to design 3D printable heat sinks for electric car batteries, replacing conventional cooling systems with lightweight, self-contained solutions.
Embry-Riddle’s Mechanical Engineering Department, led by Associate Professor Sandra Boetcher, embarked on an ambitious project to innovate cooling systems for electric car batteries. Traditional cooling systems are often bulky and complex, requiring significant space and energy to operate. The team at Embry-Riddle envisioned a more efficient solution using 3D printed heat sinks made from a mixture of HDPE and PCM.
The Challenge: Creating high-quality, shape-stabilized PCM-based filament presented several challenges. PCM, while effective at absorbing heat, is difficult to contain within a set shape due to its phase-change properties. The team needed a solution that would stabilize the PCM, allowing it to be mixed with HDPE and extruded into filament suitable for 3D printing. Their previous filament extruder could only achieve 20% PCM in their filament, which was insufficient for their needs. Additionally, the extruder lacked the quality control and customization options required to produce high-quality filament with consistent diameter and properties.
The Solution: The team turned to 3devo’s Composer Filament Maker, a high-performance, and cost-effective solution. The Composer Filament Maker met all their criteria, offering excellent diameter control, flexibility to work with non-typical materials, and the ability to easily adjust settings for different ratios of PCM and plastic. Using the Composer Filament Maker, the team was able to produce filament with up to 60% PCM, three times the level they could achieve with their previous extruder. This significant improvement allowed them to create high-quality filament that met their requirements for producing 3D printed heat sinks.
The Impact: The Composer Filament Maker has had a profound impact on the team’s research and development efforts. The ability to produce filament with higher PCM levels has significantly enhanced the performance and efficiency of their 3D printed heat sinks. These heat sinks can absorb and dissipate heat more effectively, making them an ideal solution for cooling electric car batteries. Additionally, the flexibility of the Composer Filament Maker has allowed the team to experiment with different materials and filament compositions. This has opened up new possibilities for innovation and further research, as they explore ways to optimize their filament for various applications.
Thomas Freeman, a PhD student in Mechanical Engineering at Embry-Riddle, highlighted the benefits of using the Composer Filament Maker: “3devo’s filament maker allows us to easily shift between materials, without the limitation of complex polymers holding us back. We have mixed various material together such as phase-change materials mixed with HDPE and PLA.” The success of this project has positioned Embry-Riddle as a leader in the development of advanced cooling systems for electric vehicles. Their work with HDPE and PCM-based filament is paving the way for more efficient, lightweight, and cost-effective solutions in the automotive industry.
Read the full case study here!
HDPE Filament Production Process
Producing HDPE filament with 3devo’s Filament Makers involves several key steps to ensure optimal quality and performance:
Material Preparation: Begin by thoroughly cleaning and drying the HDPE pellets to remove any moisture. This step is crucial to prevent defects and inconsistencies in the final filament.
Extrusion: Set the Filament Maker to the appropriate temperature settings for HDPE extrusion. For the Filament Maker ONE, this typically involves heating the extruder to around 220°C. The Filament Maker TWO, with its advanced temperature sensors, allows for more precise control, ensuring a consistent extrusion process.
Cooling and Spooling: As the HDPE filament is extruded, it is cooled using a controlled cooling system to ensure uniform diameter and quality. The filament is then wound onto spools using an efficient spooling system, ready for use in 3D printing applications.
Advanced Features of 3devo’s Filament Makers
3devo’s Filament Makers come equipped with several advanced features that enhance the filament production process:
Enhanced Temperature Control: Advanced temperature sensors provide precise control over the extrusion temperature, allowing for consistent and high-quality filament production.
Efficient Cooling System: The integrated cooling system in 3devo’s Filament Makers ensures uniform cooling of the filament, preventing warping and ensuring dimensional accuracy.
Conclusion
HDPE filament offers numerous benefits for 3D printing, including strength, chemical resistance, and flexibility. With 3devo’s advanced Filament Makers, producing high-quality HDPE filament is both efficient and reliable. Whether you’re prototyping, creating functional parts, or engaging in educational projects, HDPE filament provides a robust and versatile solution.
By incorporating our solutions, companies can effectively extrude and recycle HDPE and contribute to a sustainable future. Explore our products to start your recycling journey today!
Frequently Asked Questions (FAQs)
HDPE filament offers numerous benefits, including high tensile strength, excellent chemical resistance, and flexibility. These attributes make it suitable for various applications, from creating durable and robust prototypes to manufacturing functional parts that need to withstand significant stress and strain. Additionally, HDPE is lightweight, making it ideal for applications where weight reduction is crucial without compromising strength and durability. Its recyclability also promotes sustainable 3D printing practices by reducing plastic waste.
HDPE stands out due to its flexibility and chemical resistance, which are superior to PLA and ABS. While PLA is known for its ease of printing and biodegradability, it lacks the strength and flexibility of HDPE. ABS, on the other hand, is strong and durable but emits harmful fumes during printing and can be challenging to adhere to the print bed. HDPE combines the best of both worlds with its strength, flexibility, and ease of processing, although it can present challenges such as warping and bed adhesion issues.
HDPE filament is versatile and can be used in various applications. It is ideal for prototyping due to its durability and ease of processing, allowing designers to create robust prototypes for real-world testing. HDPE is also suitable for manufacturing functional parts such as containers, piping components, and industrial tools, given its strength and chemical resistance. Additionally, its flexibility makes it perfect for educational projects, allowing students to explore its properties and applications, and for creating flexible joints and components that require elasticity.
Printing with HDPE filament can present several challenges. Warping and shrinkage during the cooling process can affect the dimensional accuracy of printed parts, which can be mitigated through proper temperature control and heated build platforms. HDPE can also be difficult to adhere to the print bed, requiring adhesives or specialized build surfaces. Additionally, maintaining the structural integrity of intricate designs can be challenging due to HDPE's flexibility.
Improving bed adhesion when printing with HDPE filament can be achieved through several methods. Using adhesives such as glue sticks or specialized printing adhesives designed for HDPE can help. Employing a heated build platform can reduce warping and improve adhesion. Applying a build surface material specifically designed to enhance adhesion for HDPE, and ensuring the print bed is clean and free from dust or oil that could affect adhesion, can also help improve bed adhesion.
Yes, HDPE is an excellent purging material for filament makers. Its chemical properties allow it to effectively clean out residual materials in the extrusion system, preventing contamination and ensuring the purity of subsequent filament productions. This is particularly useful when switching between different types of plastics, as HDPE helps maintain the integrity and quality of the new material.
HDPE filament offers several environmental benefits. It is highly recyclable, allowing for the reduction of plastic waste and promoting a circular economy. Producing HDPE filament from recycled materials requires less energy compared to producing virgin plastic, resulting in a lower carbon footprint and reducing greenhouse gas emissions. Additionally, the durability and longevity of HDPE products reduce the need for frequent replacements, minimizing waste and promoting sustainable 3D printing practices.
To ensure consistent quality when producing HDPE filament with 3devo’s Filament Makers, thoroughly clean and dry HDPE pellets to remove any moisture before extrusion. Set the extruder to the appropriate temperature settings, typically around 220°C to 240°C for HDPE. Use the advanced temperature sensors and cooling systems of the Filament Maker TWO for precise control, and monitor the extrusion process closely to maintain uniform filament diameter and quality.
3devo’s Filament Makers come with several advanced features that enhance HDPE filament production. Advanced temperature sensors provide precise control over the extrusion temperature, allowing for consistent and high-quality filament production. The integrated cooling system ensures uniform cooling of the filament, preventing warping and ensuring dimensional accuracy. Customizable settings allow for adjustments to extrusion speed, temperature, and other parameters to optimize filament production.
In real-world applications, HDPE filament excels in areas requiring durability, chemical resistance, and flexibility. It is particularly effective for producing parts that need to withstand impact and stress, such as containers, piping components, and industrial tools. HDPE’s performance is often superior to PLA and ABS in harsh environments due to its chemical resistance. However, it may require more careful handling during printing to address warping and adhesion challenges.
Share this
- March 2025 (1)
- January 2025 (1)
- December 2024 (2)
- November 2024 (3)
- October 2024 (4)
- September 2024 (2)
- August 2024 (3)
- July 2024 (6)
- June 2024 (3)
- May 2024 (2)
- April 2024 (1)
- March 2024 (1)
- January 2024 (1)
- November 2023 (2)
- October 2023 (5)
- September 2023 (2)
- August 2023 (1)
- July 2023 (1)
- May 2023 (1)
- December 2022 (3)
- August 2022 (1)
- June 2022 (1)
- May 2022 (2)
- April 2022 (2)
- March 2022 (7)
- February 2022 (2)
- January 2022 (3)
- December 2021 (3)
- November 2021 (3)
- October 2021 (2)
- September 2021 (3)
- August 2021 (3)
- July 2021 (2)
- June 2021 (1)
- March 2021 (1)
- October 2020 (1)
- June 2020 (1)
- May 2020 (1)
- April 2020 (4)
- November 2019 (1)
- July 2019 (2)
- June 2019 (1)
- May 2019 (1)
- March 2019 (1)
- November 2018 (1)
- September 2018 (1)
- January 2018 (1)
- October 2017 (1)
- September 2017 (1)
- July 2017 (1)
- June 2017 (1)
- May 2017 (1)
- January 2017 (1)
- December 2016 (3)
- November 2016 (2)
- October 2016 (1)
- May 2016 (2)
- August 2015 (2)
- July 2015 (1)