Plastic Extrusion
The extrusion process, step by step
Raw Material Preparation
Before diving into the extrusion process itself, the initial step involves pre-processing the thermoplastic material with a variety of additives. These include heat, oxidative, and UV stabilizers along with color pigments, flame retardants, fillers, and lubricants. This crucial mixing phase not only elevates product quality and ease of processing but also ensures that the final product meets the desired property specifications. Drying the material is also crucial to avoid defects in the final product.
Feeding System
The mixture is placed into the feed hopper. Consistency in feeding is essential to ensure uniform extrusion. Dealing with solid substances like polymer powder often presents a challenge in terms of flow. In some instances, the material may bridge within the hopper, obstructing a smooth flow. To counteract this, a targeted solution involves a specially-designed hopper that minimizes bridging, like the one in 3devo's Filament Maker TWO.
Melting & Plastication
The barrels undergo a process of controlled heating, ramping up temperatures progressively along the screw's length. This strategic temperature elevation plays a pivotal role as the polymer blend moves from the initial feed zone to the metering zone, encountering both the force of friction and the heat from the barrels. These conditions soften the material, ensuring it melds into a uniform mixture while being thoroughly kneaded throughout its path.
Melt Mixing
Forming
The die, a crucial component, shapes the molten plastic into the desired profile. Die design varies depending on the product, such as flat dies for sheets or annular dies for pipes. Following this filtration, the molten material is then expelled through the die, adopting its designated shape.
Cooling
After exiting the die, the extrudate is cooled using air cooling, water baths, or cooling rolls. Controlled cooling prevents warping and ensures dimensional stability.
Pulling System
The cooled extrudate is pulled away from the die at a consistent speed by a haul-off system, which ensures uniform thickness and dimensions. It can also be spooled, like this.
Cutting and Finishing
The continuous profile is cut to the required length and may undergo additional finishing processes. Additional finishing processes, such as printing, embossing, or annealing, may be applied to enhance the product’s appearance and properties.
Extruder types
- Continuous extruders
- Discontinuous extruders
-
Screw extruders
-
Disk (or drum) extruders
Single Screw Extruders
The preferred choice in the industry, thanks to their impressive blend of affordability, simple construction, durability and exceptional performance to cost ratio.
Along the screw there are 3 zones:
1. Feed Zone
2. Transition / Compression Zone
3. Metering Zone
While the screw maintains a consistent pitch, the depth of its channels varies, creating the 3 zones. This reduction in channel depth progresses linearly from the feed zone to the metering zone, causing the compression process in between. Furthermore, the variation in the lengths of these zones, along with the maximum and minimum depths of the channels, allows for a diverse array of screw profiles despite identical screw lengths and diameters.
The inside of the extruder also allows the variation of the below factors:
1. Screw profile
2. Temperature
3. Rotating speed
These factors can determine the extruder's internal heat transfer, cooling efficiency, flow dynamics and the duration materials spend within the system.
Twin Screw Extruders
Named for their dual Archimedean screw configuration, twin screw extruders offer a broad spectrum of customization. numerous design parameters available —such as the direction of rotation and the extent of screw intermeshing— allow for a wide array of classifications within twin screw extrusion.
Twin screw extruders can be categorized into 4 types based on the rotation and intermeshing of the screws:
1. Co-Rotating Twin Screw Extruders
Both screws rotate in the same direction. These are commonly used for compounding, mixing, and reactive extrusion because of their excellent mixing capabilities.
a. Intermeshing Co-Rotating
The screws interlock, providing better mixing and heat transfer.
b. Non-Intermeshing Co-Rotating
The screws do not interlock, suitable for applications requiring gentle mixing and conveying of heat-sensitive materials.
2. Counter-Rotating Twin Screw Extruders
The screws rotate in opposite directions. These are often used for profile extrusion and applications requiring high pressure and low shear.
a. Intermeshing Counter-Rotating
b. Non-Intermeshing Counter-Rotating
Each type offers unique advantages and is selected based on the specific requirements of the extrusion process.
Multi-screw Extruders
A prime example of an extruder with multiple screws is the planetary roller extruder, which shares some design elements with the single screw one, especially noticeable in the initial feed section. The distinction lies in the mixing area, where the device showcases its unique configuration: a constellation of six or more planetary screws orbiting the sun screw. These planetary screws mesh intricately with both the sun screw and the barrel's interior, which is specifically contoured with helical channels to snugly fit the twisting paths of the planetary screws. A flange-type connection seamlessly joins this innovative planetary roller section to the feed section, enhancing its operational efficiency.
The planetary roller extruder excels in thorough mixing, which is due to the dynamic interplay of the planetary screws, the central sun screw, and the barrel. A standout feature of this extruder is its gentle handling of heat-sensitive materials, ensuring they undergo minimal degradation during processing.
Planetary roller extruders are frequently used for the extrusion of both rigid and plasticized PVC, showcasing their versatility. Additionally, their incorporation into standard extruders further enhances mixing capabilities.
Disk Extruders
Disk extruders, falling under the category of continuous extrusion machines, diverge from the conventional by using disks instead of screws. Occasionally referred to as screwless extruders, these devices primarily rely on viscous drag transport for operation.
In contrast to their screw-driven counterparts, disk extruders have become less popular within the industry.
Stepped Disk Extruder
The stepped disk extruder, also referred to as slider pad extruder, features a distinct design with a stepped disk positioned almost next to a flat disk. This innovative arrangement creates pressure as the gap between the disks changes size, achieved by rotating one disk while a polymer melt fills the space between, facilitating a unique extrusion process.
Stepped disk extruders are engineered for continuous operation, provided there are sufficient exit channels in the stepping disk. However, a significant challenge associated with these machines is their maintenance. Their complex configuration presents a significant challenge when it comes to cleaning.
Drum Extruder
The drum extruder operates through the coordinated movement of a rotating drum and barrel, facilitating the extrusion process. As the polymer enters the space encircling the drum and barrel, it embarks on a journey along the barrel's perimeter, propelled by the drum's rotation. Just before completing a full circle, a strategically placed wiper bar comes into play, delicately stripping the molten material from the drum. This action steers the melt toward an exit path, guiding it seamlessly into the extruder die.
Diskpack Extruder
The Diskpack extruder stands toe-to-toe with conventional polymer-processing equipment in efficiency, with the best elements of both the single screw and drum extruders. Envisioned as a revolutionary iteration of the single screw extruder, as it boasts a zero helix angle and exceptionally deep flights—this innovative machine redefines the extrusion process.
Material is introduced into the slender gap positioned axially between the rotating thin disks. As the disks turn, the melt advances in unison with them until, just before completing a full rotation, a channel block effectively seals the gap between the disks. This mechanism mirrors the function of the wiper bar in drum extruders, channeling the flow smoothly towards the extrusion outlet.
Elastic Melt Extruder
In contrast to traditional disk extruders that depend on viscous drag transport for functionality, elastic melt extruders leverage the elastic characteristics of polymer melt. This unique approach propels the material and generates the necessary pressure at the die head, distinguishing them from conventional extruders.
As the material undergoes shearing between the static and moving plates, it experiences an uneven spread of normal stresses throughout the melt in every direction. This imbalance in stress triggers a powerful centripetal pumping force, propelling the continuous flow of the material through a central opening. This method is why elastic melt extruders are often dubbed as normal stress extruders.
Ram Extruders
Single Ram Extruder
Ram extruders, also called plunger extruders, are discontinuous extruders. These robust and straightforward positive displacement units are capable of generating exceptionally high pressures.
Ram extruders show advantages in batch processes such as injection and blow molding, but also notably show a restricted melting capability and uneven heat distribution throughout the melt.
Among the various models, the single ram extruder stands out for its versatility in general purpose molding. Additionally, it excels in ultrahigh molecular weight polyethylene extrusion (UHMWPE) and polytetrafluoroethylene extrusion (PTFE), offering precise and reliable performance.
Multi Ram Extruder
Multi ram extruders, unlike single ram, are continuous extruders. Some models feature four plunger-cylinders – a pair dedicated to the plastication process and another pair focused on pumping, all seamlessly connected through a sophisticated shuttle valve system. Alternatively, some multi ram extruders adopt a twin ram configuration, with cylinders arranged in a V-formation for efficient performance.
Extruder Parts
There are several parts that make up a single screw extruder:
Extruder Screw
The most critical element of the extruder is the screw. A cylindrical rod, wrapped in a spiral pattern, which plays a pivotal role in the movement, heating and blending of the materials. Most commonly designed to keep a uniform inner diameter with varying flight sizes, this component is crafted from a variety of robust materials such as low carbon steel, stainless steel and nickel-rich alloys.
Hopper
The feed hopper uses gravity to introduce material into the extruder. Vibrating pads and stirrers can dissolve bridging inside the hopper and aid material flow, addressing issues like:
-
Air Entrapment
Certain materials have a low bulk density, leading to the risk of air becoming trapped within the hopper. Without proper venting, this trapped air can advance into the extruder and ultimately escape through the die, compromising the extrudate's integrity. -
Fast Compression
When dealing with materials that exhibit a wide range of particle sizes, square feed hoppers can encounter issues related to the fast compression of these materials. In such instances, opting for a hopper with a circular cross-section is the ideal choice, as square feed hoppers are commonly used for handling materials with consistent particle size.
Barrel and Feed Throat
The barrel encloses the screw, while the feed throat is where material enters. Usually, a water-cooling system in the feed throat prevents premature melting and flow issues. There are key considerations in order to avoid further problems like melt sticking on the surface and material flow blockage:
- Efficient cooling
- Thermal barrier between the feed entry and barrel
- Large pressure capability
Extruder Drive
The drive system handles the screw rotation, delivering the essential torque needed to the screw shank. There are three kinds of drive systems:
- AC motor drive systems
- DC motor drive systems
- Hydraulic drives
Thrust Bearing Assembly
This assembly is placed to resist axial forces on the screw from die head pressure. It's placed between the screw shank and drive output shaft. Types include ball, cylindrical roller, spherical roller, and tapered roller thrust bearings.
Die Assembly
The die is also a critical part of the extrusion process as it shapes the material into its final form. There are occasions where the extruder barrel’s exit does not align with the die’s entrance, necessitating the use of an adapter to bridge this gap. However, when a die is specifically engineered for a particular extruder, the need for an adapter is eliminated, streamlining the process and ensuring a seamless transition from extruder to die.
Breaker Plate
A breaker plate converts the melt's spiraling movement into a smooth, linear flow. Without this conversion, the melt might continue spiraling all the way to the die exit, potentially leading to deformities in the final product. Additionally, breaker plates serve an essential function by providing a sturdy platform for filter screens.
Filter Screens
The primary function of filters within an extruder setup is to eliminate any unwanted particles from the extrudate. These filters are also instrumental in enhancing the uniformity of the melt within the extruder by contributing to an increase in pressure at the die-head. Typically, a breaker plate supports the initial, coarser screen, which is then succeeded by screens with finer mesh.
Extruders typically utilize one of four primary types of screen media to ensure the purity and consistency of the extrudate:
- Square weave wire mesh
- Dutch twill wire mesh
- Sintered powder
- Random metal fiber
Heating Systems
Heating mechanisms are essential for regulating the extruder's temperature during operations. Electric heating, a popular choice for many setups, ensures each segment of the extruder's barrel is equipped with its own electric heater. These individual units are managed separately, allowing for a consistent temperature distribution throughout the length of the extruder. There are two types of electrical heaters:
-
Electrical Resistance Heater
The generation of heat arises from the resistance shown by the conductor to the flow of electric current. This system leverages the inherent resistance within the conductor to produce the necessary heat for the extrusion process. -
Induction Heater
This system engulfs the extruder barrel with a primary coil. Through this coil, an alternating current flows, effectively heating the barrel from the outside in.
Cooling Systems
The extruding process can lead to localized spikes in temperature within the melt, potentially pushing the process temperature beyond the desired threshold. To counteract this, extruders are equipped with cooling systems designed to moderate the temperature, ensuring it remains within the set parameters. Among these cooling solutions, forced-air systems utilizing blowers stand out as a prevalent choice for maintaining optimal operation temperatures in extruders.
Extruder Screw Zones
1. Feed Zone
Within this zone, the depth of the flight remains unchanged. The flight depth is the vertical distance between the outer edge of the flight and the root (base) of the screw.
2. Compression Zone
In this region, there's a noticeable reduction in flight depth, leading to the thermoplastic material being subjected to compression and initiating its plastication
3. Metering Zone
In this area, the flight depth is again steady, but reduced compared to the feed zone. The force exerted propels the molten material through the shaping die.
Polymer Melting Factors
Heat Transfer
Heat transfer from the motor directly to the shaft of the extruder. Additionally, the melting process of the polymer is influenced by both the screw's design and the process duration.
Friction
This results from the powder's internal friction, the configuration of the screw, the velocity at which the screw rotates, and the rate at which the material is fed.
Barrel Heaters
Multiple independent temperature controllers are integrated to ensure the barrels remain at the desired temperature.
Plastic Extrusion Applications
Compounding
Creating custom polymer blends.
Sheet and Film
Used in packaging, construction, and consumer goods.
Extrusion Coating and Lamination
Coating substrates like paper, foil, and textiles.
Pipe and Tubing
Used in plumbing, medical devices, and industrial applications.
Wire and Cable Coating
Insulating and protecting electrical wires and cables.
3d Printing Filament
Most types of plastic can be recycled into filament. Learn more.
Plastic Extrusion Advantages
Cost-Effective Production
Extrusion is highly efficient for high-volume production, reducing per-unit costs.
Material Versatility
A wide range of thermoplastic materials can be processed, including polyethylene (PE), polypropylene (PP), polyvinyl chloride (PVC), and more.
Customizable
Dies can be designed to produce virtually any shape, allowing for tailored solutions to specific applications.
Continuous Operation
Extrusion can produce long, continuous profiles without interruption, ideal for applications requiring extensive lengths.
Material Efficiency
Minimal waste is generated during the extrusion process, and scrap material can often be reprocessed.
Plastic Extrusion Challenges
Material Handling
Ensuring consistent material flow into the extruder to avoid interruptions and defects.
Temperature Control
Maintaining optimal temperatures throughout the extrusion process to prevent material degradation and ensure product quality.
Die Design Complexity
Designing precise dies to achieve complex profiles requires expertise and precision engineering.
Cooling and Solidification
Uniform cooling is critical to prevent warping, shrinkage, or other defects in the final product.
Quality Control
Continuous monitoring and inspection are necessary to maintain consistent product quality and detect any issues early in the process.
Plastic Extruder Die Types
T-Dies
For sheet and film extrusion.
Crosshead Dies
For coating wires and cables.
Spiral Mandrel Dies
Used in blown film extrusion.
Profile Dies
For creating complex shapes.
Future Trends in Plastic Extrusion
Sustainability and Recycling
Increasing focus on using recycled materials and developing biodegradable polymers to reduce environmental impact.
Advanced Materials
Development of new high-performance polymers with enhanced properties for specialized applications.
Automation and Control
Integration of advanced automation and control systems to improve process efficiency, reduce waste, and enhance product quality.
3D Printing Integration
Combining extrusion technology with additive manufacturing (3D printing) for creating complex, customized products.
Energy Efficiency
Innovations in energy-efficient extruder designs to reduce energy consumption and operational costs.
Conclusion
Plastic extrusion is a versatile and efficient manufacturing process with widespread applications across various industries. Understanding the intricacies of the extrusion process, from material preparation to post-processing, is essential for producing high-quality extruded products. By leveraging the capabilities of plastic extrusion, manufacturers can create a diverse range of products, driving innovation and meeting market demands.
Is Your Material Extrudable ?
Material Flow Index Test
Material Pyramid
Filament Development Analysis
Filament Extruders
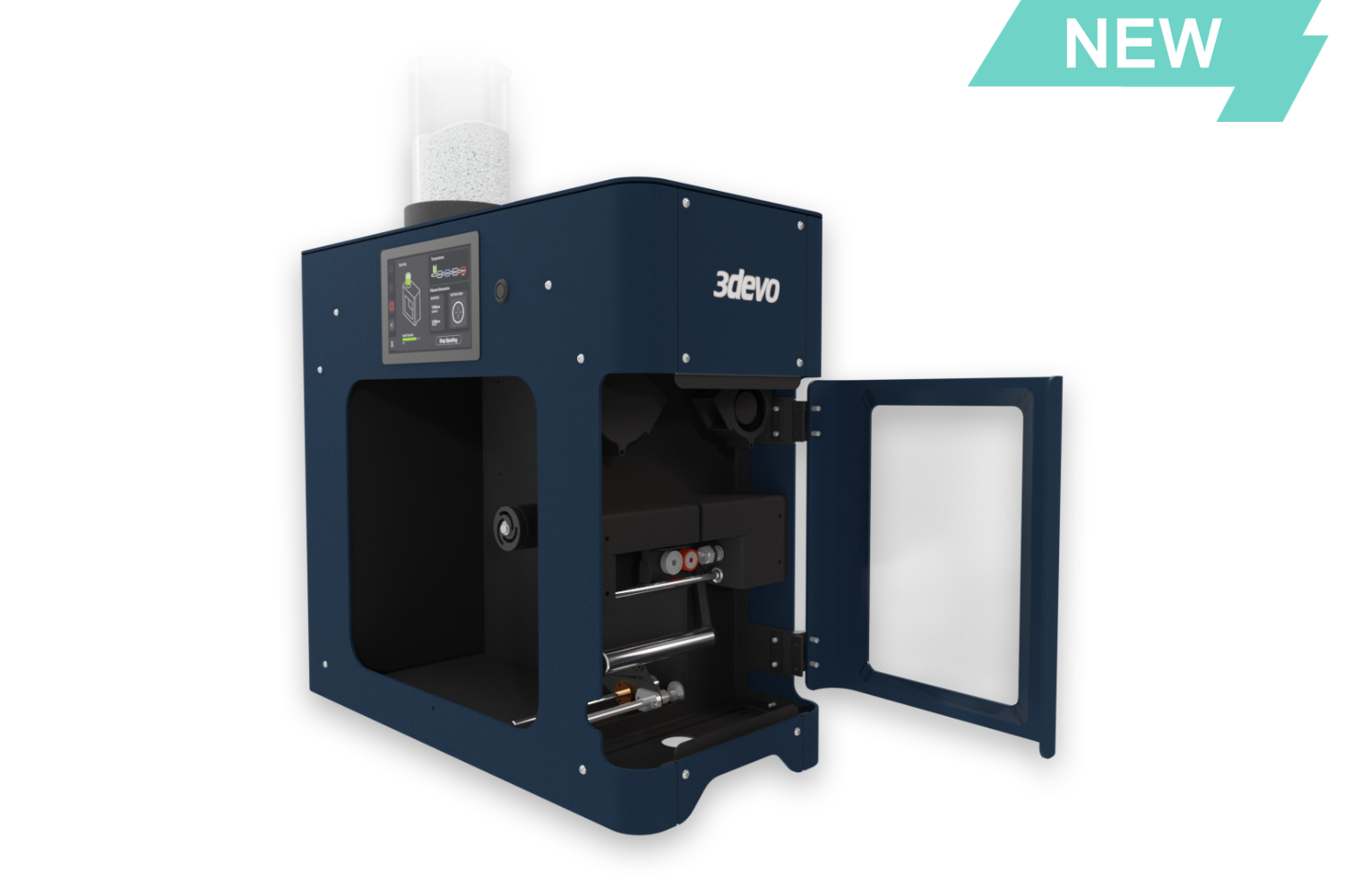
Filament Maker TWO
The Fusion Model introduces cutting-edge technology with advanced material mixing for R&D and custom filaments.
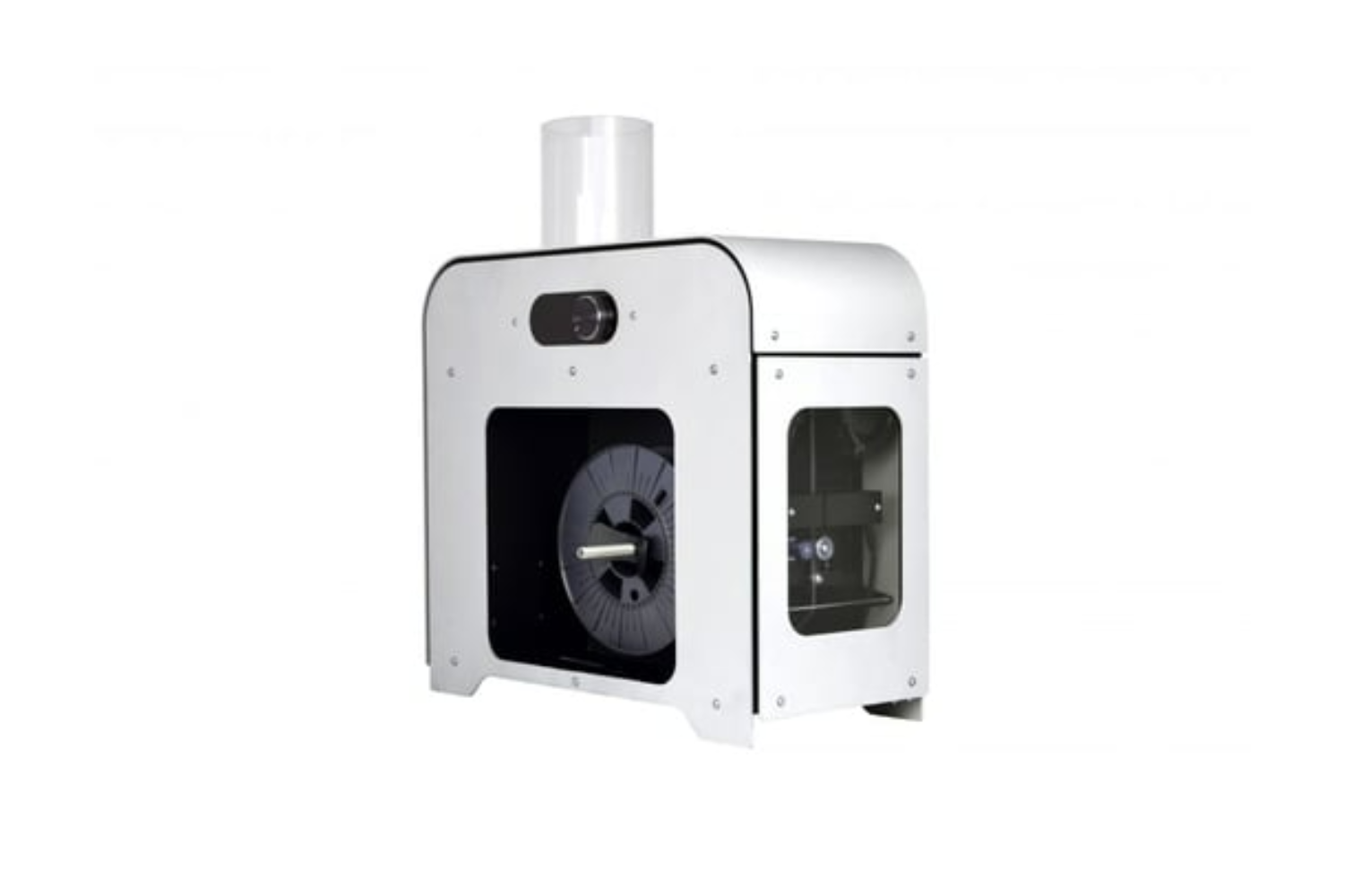
Filament Maker Composer
The Composer offers an easy-to-use and durable solution for creating custom 3D printing filament in a sleek, compact design.
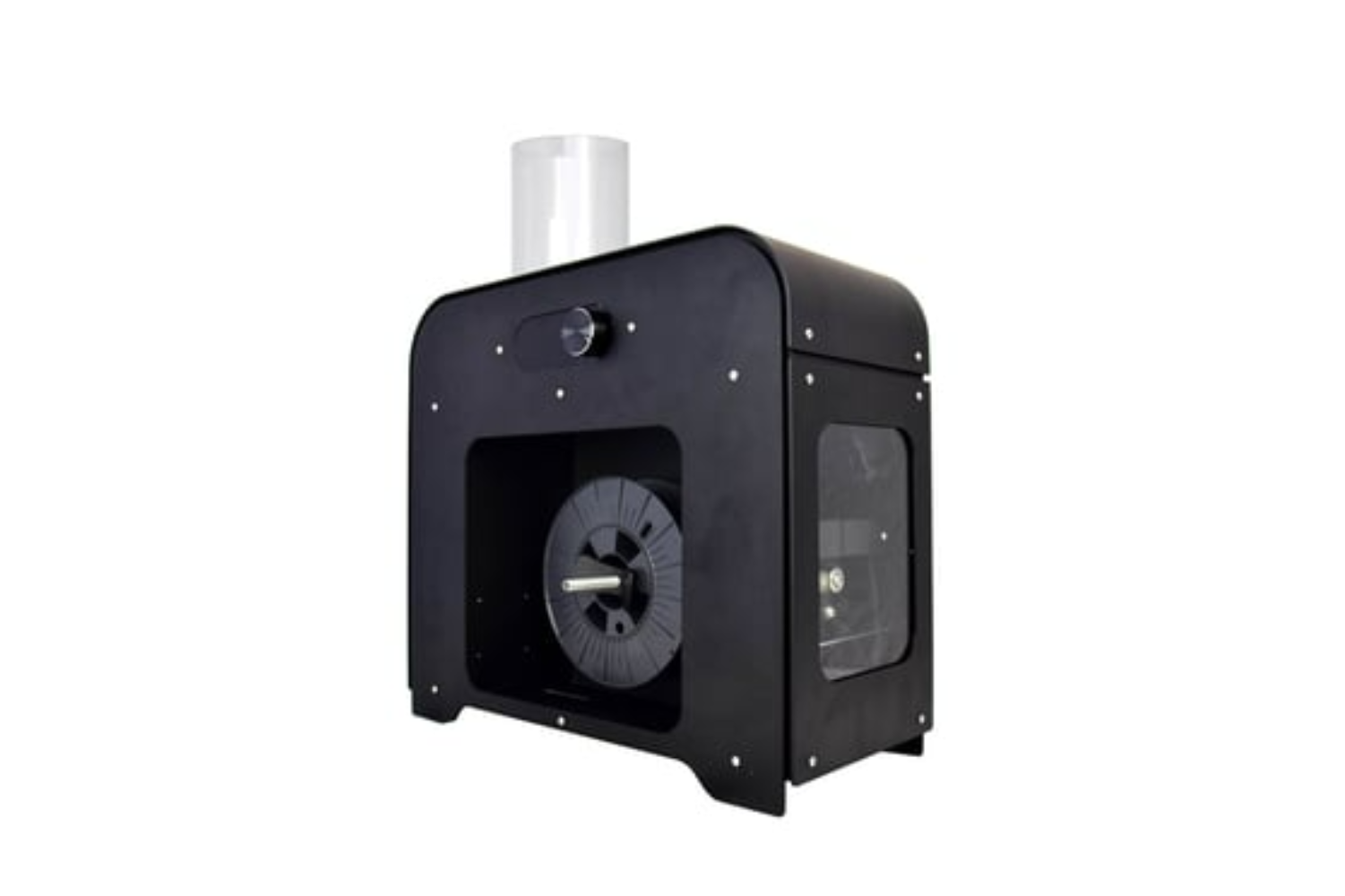
Filament Maker Precision
The Precision model delivers top-notch, high-temp filament extrusion with speed, consistency, and user-friendly operation.
Our Success Stories
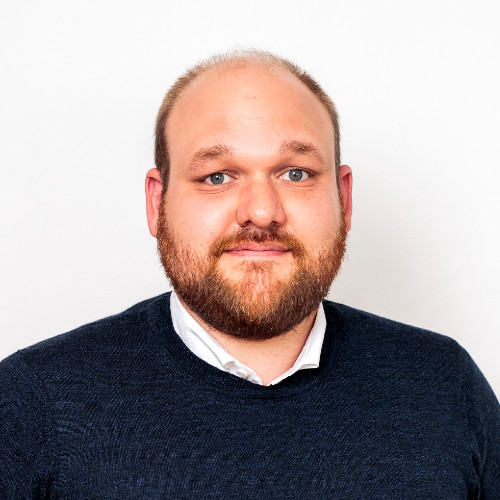
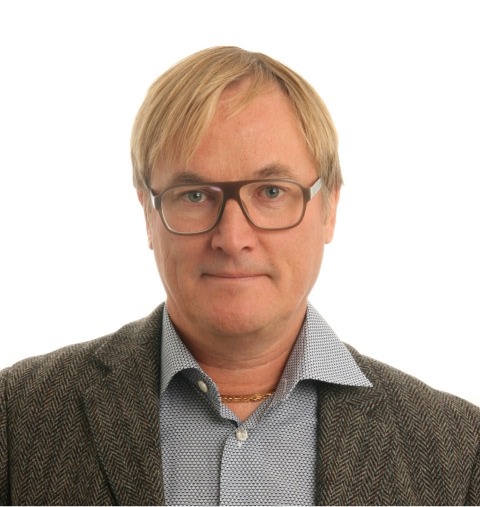
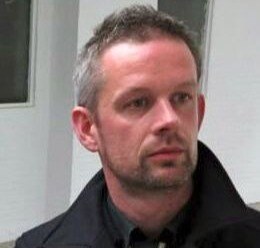
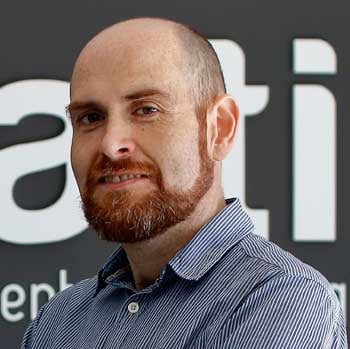
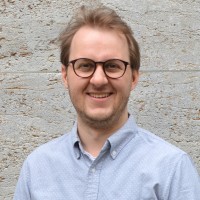
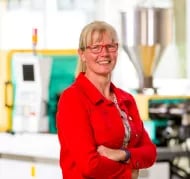