Why View Lattice Medical Case?
Innovative 3D Technology
The Mattise Solution
Lattice Medical's Breakthrough Technology
Overcoming Challenges in Research and Production
"At €5000 per kg, the material is like gold. We needed to make both testing and production cost-effective."
Kevin Roux, Engineer (R&D and Production) Lattice Medical
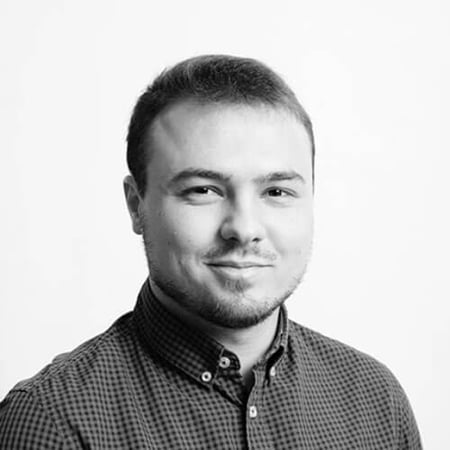
Introduction
Innovating Biodegradable Implants for Post-Surgery Recovery
Lattice Medical, a pioneering biomedical startup, is on a mission to transform the landscape of post-surgical recovery through its groundbreaking biodegradable breast implants. These implants are designed to naturally degrade within the body, significantly reducing the need for follow-up surgeries. This innovative approach aims to provide a safer, more efficient recovery process for patients. The partnership with 3devo has been instrumental in enabling Lattice Medical to advance their research and development efficiently, leveraging cutting-edge technology to meet their precise material requirements.
Background
Founded in 2017, Lattice Medical is at the forefront of post-cancer tissue reconstruction technology. The French company, in collaboration with CHU-Lille France, has developed a patented 3D printing technology that allows for the natural regeneration of breast tissue. Their flagship product, Mattise, is a bioabsorbable implant that offers a cost-effective alternative to traditional reconstruction methods. Unlike conventional approaches, Mattise eliminates the need for multiple surgeries, thereby minimizing patient risk and reducing overall healthcare costs. The implant, made from autologous adipose tissue and a 3D-printed absorbable structure, facilitates the regeneration of fat cells as the implant gradually dissolves, ensuring a seamless recovery process.
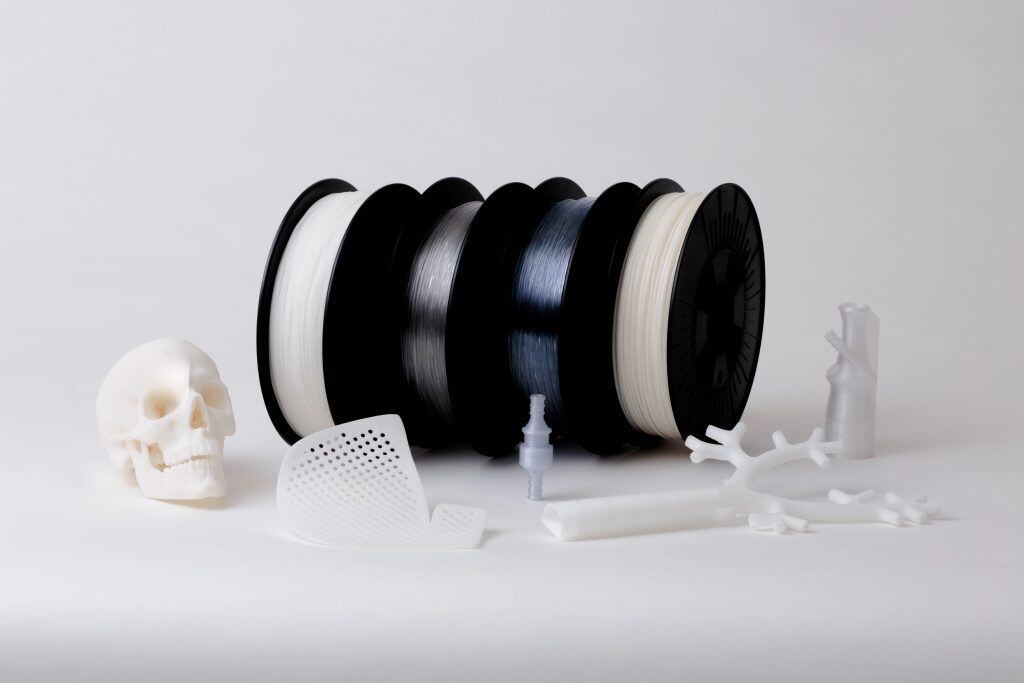
Get the Full Lattice Medical
Customer Story
Customer Story
The Challenge
During its R&D phase, Lattice Medical encountered a major hurdle: their key implant material, a special bioabsorbable polymer, cost €5000 per kilogram. This necessitated finding a cost-effective, precise method for small-scale experimentation without wasting this expensive material. Traditional, high-cost industrial extruders, unsuitable for such meticulous work, prompted the need for an affordable, in-house solution to produce limited quantities of custom filaments, preserving the material's integrity for their groundbreaking implants.
Working with this costly material demanded significant financial prudence and minimal waste during R&D and production. With only 12 kilograms of the final product needed annually, efficiency was paramount. Traditional industrial extruders, though powerful, fell short for such specialized, small-scale tasks. Lattice Medical required a desktop extruder that was both precise and economical to meet their exacting research needs.
Navigating the challenges of an expensive, specialized material, Lattice Medical balanced intensive testing with conservation. Each extrusion step was finely tuned to produce filaments that meet strict medical standards, ensuring their implants are safe and effective for reconstructive surgeries.
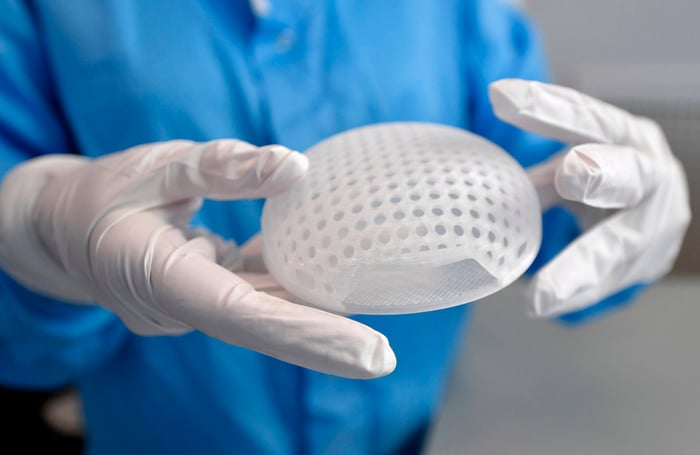
The Solution
In their quest for an efficient and scalable solution, Lattice Medical integrated 3devo’s Filament Maker ONE into their research and production process. This machine offered the precision and flexibility needed to manage their costly material. By allowing in-house production, Lattice Medical could experiment with polymer blends and optimize extrusion parameters, ensuring high-quality filaments for their 3D-printed implants. This approach reduced material waste, accelerated R&D, and minimized dependency on external suppliers.
With the Filament Maker ONE, Lattice Medical conducted numerous extrusion tests to perfect the filament required for their product Mattisse. This process involved addressing the material’s behavior at high temperatures and determining the ideal methods for spooling the extruded filament. The machine’s accuracy and efficient material usage allowed the team to experiment without incurring prohibitive costs. Producing up to 1 kilogram of filament daily, it became central to their monthly production cycle, balancing extrusion and R&D.
The integration of the Filament Mkaer ONE Composer 450 into Lattice Medical’s workflow provided several key advantages. Firstly, it ensured precise control over extrusion parameters, maintaining the bioabsorbable properties essential for safe and effective implants. Secondly, the machine's ability to handle small quantities efficiently was crucial given the high cost of the polymer. The user-friendly interface and advanced features allowed quick adjustments, facilitating rapid optimization of polymer blends, which was vital in the early stages of development. Additionally, systematic data collection enabled the team to analyze and identify optimal conditions for consistently producing high-quality filaments.
Furthermore, the compact size and ease of use of the Filament Maker ONE Composer made it an ideal fit for Lattice Medical’s laboratory environment. Unlike industrial-grade extruders, which are typically large and cumbersome, the machine integrated seamlessly into their setup without requiring significant modifications or additional space. This integration streamlined their workflow and allowed the team to focus on core research activities without logistical challenges.
By producing custom filaments in-house, Lattice Medical gained a significant strategic advantage, reducing reliance on external suppliers and avoiding long lead times and higher costs. This capability enabled quicker responses to research needs and production demands, ultimately accelerating the development timeline. 3devo's Filament Extruder proved to be a transformative addition to Lattice Medical’s toolkit, enhancing their research and development efficiency. Its precision, flexibility, and efficiency helped the startup overcome challenges associated with high-cost, specialized materials, paving the way for the successful commercialization of their innovative implants.

Revolutionary
Revolutionize breast reconstruction with patented 3D technology, Mattise.
Efficient and Cost-Effective
Reduce costs with an efficient alternative to traditional methods.
Streamlining
Learn how to streamline production and research of innovative implants.
Workflow Highlights
The adoption of the Filament Maker ONE Composer 450 brought several key benefits to Lattice Medical’s workflow:
- Customized Material Production
The Composer 450 enabled Lattice Medical to create specific polymer blends tailored to their implant requirements. This customization was crucial for optimizing the implant’s properties and ensuring its bioabsorbability. - Enhanced Research Capabilities
With greater control over material properties, Lattice Medical could conduct more rigorous testing and iterations. The ability to collect data at every step streamlined the development process, leading to more refined and effective implant designs. - Cost and Time Efficiency
In-house filament production significantly reduced costs associated with outsourcing and minimized delays in the R&D process. This efficiency was critical given the high cost of the material - Innovative Freedom
The flexibility provided by the Composer 450 allowed for continuous innovation and prototyping. Lattice Medical could swiftly test new ideas and make necessary adjustments, fostering a culture of innovation and improvement.
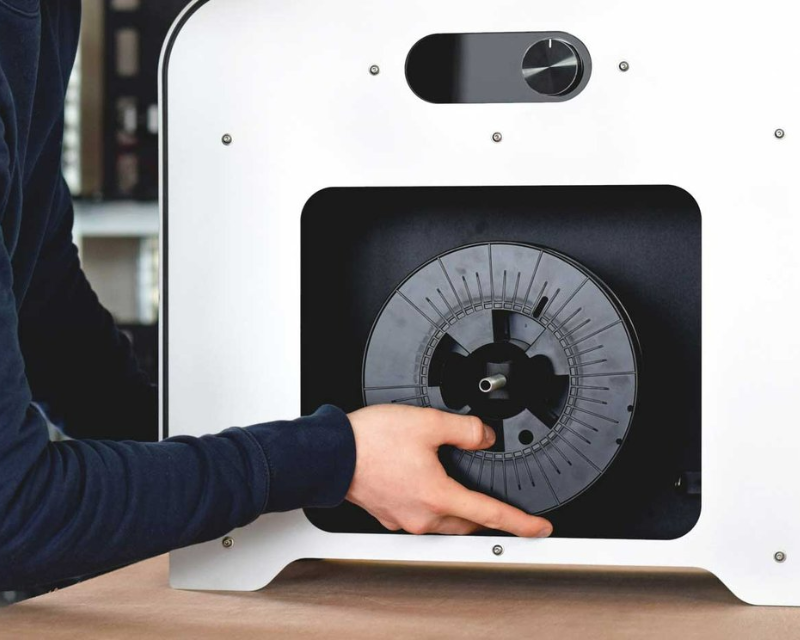
Conclusion
The collaboration with 3devo has significantly advanced Lattice Medical's development of the Mattisse implant. Our Filament Extruder enabled precise, cost-effective in-house production, reducing reliance on external suppliers and accelerating research. This technology facilitated meticulous experimentation with expensive materials, ensuring high-quality, bioabsorbable filaments, and allowed Lattice Medical to maintain high standards of quality and safety.
Moreover, the strategic advantage of in-house filament production has improved operational efficiency and provided greater control over the production timeline and costs. This partnership exemplifies the transformative impact of technological solutions in medical research and production, paving the way for future innovations in biomedical implants and enhancing patient outcomes.
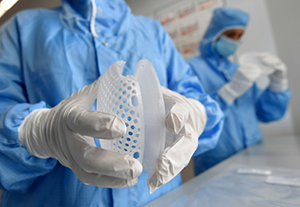
Get the Full Lattice Medical
Customer Story
Customer Story
More Success Stories
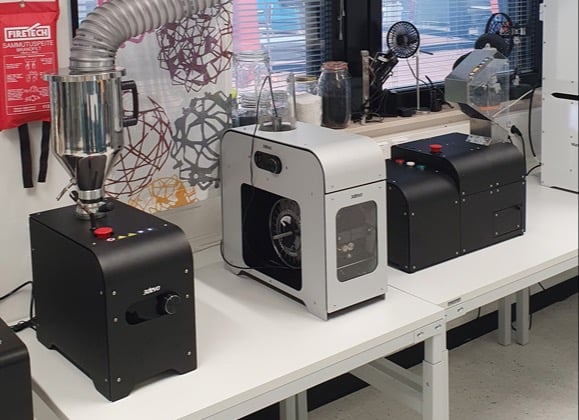
Lapland University
How Lapland University brings a sustainable closed-loop system within their 3D Printing Lab.
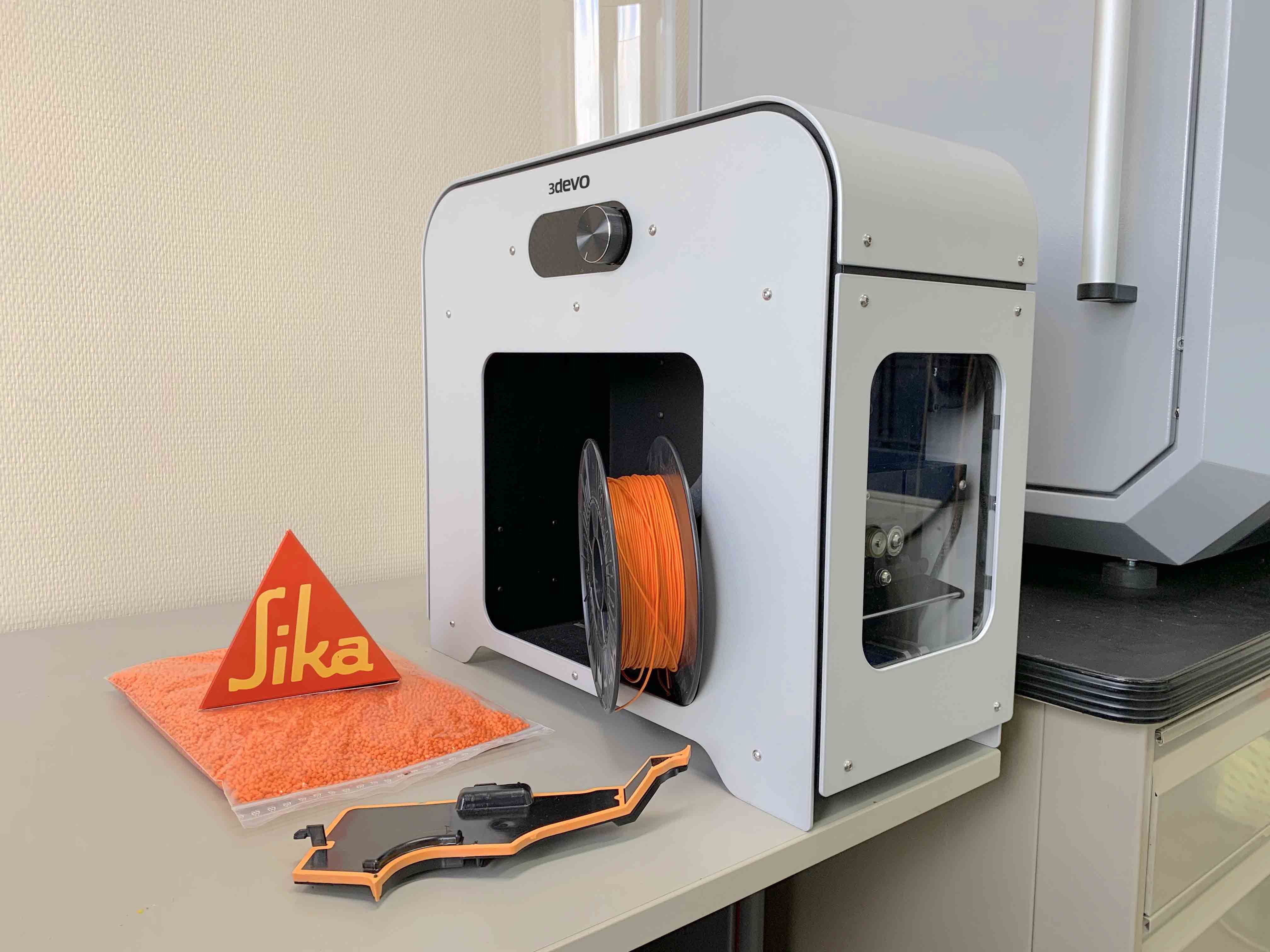
Sika Automotive
How Sika Automotive managed to reduce their production time – for their cavity sealers -from weeks to days.