Filament Maker TWO Improvements
This webpage provides updates on the progress of the Filament Maker TWO [FM2], detailing its enhanced features and the problems they resolve, in relation to the Filament Maker ONE [FM1].
1. Advanced data monitoring
Reliable data monitoring of all the parameters of extrusion is the key in finding optimal processing settings, exploring the influence on the material properties and being able to achieve reproduceable results.
Why is this feature introduced or improved for FM2?
Situation FM1:
When extruding filament on the FM1 the resolution only gives a rough indication whether the filament is within spec. The resolution of the new filament sensor has gone up to <5 microns of the FM2 instead of 43 microns of FM1.
Most industry standards for 3D-printing filament relies on a diameter tolerance of plus minus 50 microns. This would mean that the FM1 filament sensor would only pick up ‘ filament thickness from one side within spec’ or ‘filament thickness from one side out of spec’ rather than giving an actual representation of the filament diameter. This would not be able to pick up flattened or oval shaped filaments due to uneven cooling.
Situation FM2:
A much better approach would be to measure the filament from three directions (all spaced 120 degrees) and give an actual idea of not only the diameter but also its roundness which is critical for 3D-printing. This is exactly what the new filament sensor does with a resolution of <5 microns. The new sensor is also much less prone to external noise.
Why is this feature introduced or improved for FM2?
Situation FM1:
One of the trickiest problems the FM1 can face is if the temperature creeps back to the hopper and prematurely melting whatever polymer is in the extruder. This often happens when temperatures (especially the heater close to the feeding zone) are set too high for the specific polymer being processed. The entire mechanism relies on the fact that unmelted pellets exert force on the melted polymer creating forward pressure. If there are no unmelted pellets to push the melted polymer forward, the situation gets worse. Since there is no longer any material flow, the material becomes even hotter or degrades even more making it even more difficult to get the flow back.
Situation FM2:
Apart from having the feeding zone farther away from the closest heater compared to with the FM1, the new hopper design actually actively cools the feeding zone to close to room temperature. Does this completely eliminate the premature melting? Almost. One should still be careful when transitioning from a high temperature material to a lower temperature or when flow is obstructed due to other reasons. The hopper has its own temperature sensor that can be read real-time or in the data log any time at a later moment. We also offer an add-on that can be mount on the hopper to reliably get pressure back in emergencies.
Why is this feature introduced or improved for FM2?
Situation FM1:
The motor load is measured in terms of motor current. This metric can give a good enough feeling of the loads at play. However this metric is limited since it is also depending on the rotational speed.
Situation FM2:
The motor load is expressed in actual torque (Nm) independent of rotational speed, giving much better insights in the extrusion process.
Situation FM1:
FM1 comes with Devovision that allows a real-time data visualization together with the option of exporting a data log.
Situation FM2:
Having the FM2 connected to Ethernet allows you to download any time from any specified date and time.
Situation FM1:
FM1 comes with Devovision, a real-time data visualization app, showing graphs of all the relevant metrics of the extrusion process.
Situation FM2
As for now, FM2 uses a slightly different approach being more accepted in the scientific community. There will be a data API [H1.10] available giving more freedom in data analysis. This allows the use of connecting it to InfluxDB.
The machine either has to be connected directly to a computer locally hosting the database or through the companies internet connection.
Situation FM1:
The FM1 controls the filament thickness by physically stretching the filament faster or slower. This is done by holding the filament between two rollers and controlling the speed of the rollers. This is a well proven way in controlling the diameter especially if there are low frequency flow fluctuations. However, for the FM1, there is no way to control how firmly the filament is held so when the filament is still too hot due to for example inadequate cooling, the filament can be squeezed by the rollers. Unfortunately, this remains hard to predict without having the ability to measure the actual filament temperature after cooling
Situation FM2:
In the FM2 the diameter control principle is the same. The filament sensor has a built in infrared thermal camera that measures the actual filament temperature. This is useful for tracking the cooling behaviour or predicting if the puller wheel will likely affect the filament thickness after measurement.
Situation FM1:
The FM1 is able to detect if the hopper is running low on material and give an audible and visible signal preventing unintended loss of material flow.
Situation FM2:
This feature is also integrated in the FM2 but has more potential in future updates like sending notifications through other means.
Situation FM1:
Eventhough we strongly recommend to stay with the machine at all times, we can not expect the user to contantly keep an eye on the produced filament. Having perfect filament when working with a new material from the start is unrealistic but drawing conclusion just from the filament thickness graph remains a matter of guesswork.
Situation FM2:
The new filament sensor uses cameras to measure its diameter and roundness. Having cameras available enable another huge adventage. Whenever the filament sensor picks up QC-failed filament it can take a snapshot and give you insight in what may have gone wrong. This eliminates guesswork and speeds up the process of finding optimal settings.
Situation FM1:
Working with real-time data without an API is doable through DevoVision but may not be the best fit for your application.
Situation FM2:
As briefly explained in [H1.6], we have a REST API available allowing you to process all the logged data from the FM2 into your own data research software. We are already able to control process parameters of the FM2 through the API as well. However, we are still exploring the safety risks regarding this.
Situation FM1:
The FM1 is equiped with a winding system that has an integrated slipper clutch. This protects the filament while keeping some tension. This slipping effect makes the measured winding speed unusable for detecting its own spool fullness.
Situation FM2:
We have changed the way we keep tension on the filament, we measure all the data required to detect whether a spool almost full, a simple notification can actually save an entire spool of filament.
Situation FM1:
The FM1 has the ability to create and edit material presets allowing you to pick up where you left off last extruding session. The FM1 comes with a database of widely used plastics. Having this database may sound useful but can also be misleading considering the wide range of material grades.
Situation FM2:
We still plan to let you create and edit your presets of course but instead of having a database, we much rather help you kickstart your research by assigning a Customer Success Manager to you and giving you tailored advice.
2. Improved stability and control over the extrusion process
Another big focus of the new Filament Maker TWO is to have better control over the extrusion process. This not only means that more parameters can be controlled but also that the most important parameters can be controlled more accurately. This promotes reproduceability of previously obtained results and enables the users to focus more at the research at hand than to fight the instabilities.
Situation FM1:
Like mentioned before, having stable temperature control is very important in having stable filament. The down side of keeping the heaters stable of the FM1 is that it took quite some time to do the initial heating. The longer material is unneccisarily exposed to heat, the more a material starts to degrade.
Situation FM2:
We've made some big improvements in the speed in which the extrusion system heats to its setpoints and in keeping it more stable.
Situation FM1:
The extruder is driven by a DC gearmotor that regulates its speed by measuring its rotational speed and adjusts accordingly. The main downside of this is that load fluctuations, normally due to pushing forward unmelted pellets that have high-friction with the barrel), causes brief drops in speed before the motor can respond to it. This in turn causes uneven flow.
Situation FM2:
Extruder drive hardware changed to a more powerful gearmotor, resulting in a more stable drive and higher torque. RPM fluctuation has been reduced to almost 0, taking away another variable from the process.
Situation FM1:
The cooling path, meaning the distance between the nozzle and the puller wheel, is quite short. For this reason, supplementary fans are added to speed up the cooling process of the filament. The user is able to adjust the fan speed in terms of a percentage. Although this gives some control, it does not guarantee a certain filament temperature let alone reproducable results.
Situation FM2:
The cooling path of the FM2 is extended slightly and cooled with two fans just like in the FM1. As explained in H1.7 can the filament temperature be used to control the fan speed automatically ensuring reproducable results.
Why is this feature introduced or improved for FM2?
Situation FM1:
One of the trickiest problems the FM1 can face is if the temperature creeps back to the hopper and prematurely melting whatever polymer is in the extruder. This often happens when temperatures (especially the heater close to the feeding zone) are set too high for the specific polymer being processed. The entire mechanism relies on the fact that unmelted pellets exert force on the melted polymer creating forward pressure. If there are no unmelted pellets to push the melted polymer forward, the situation gets worse. Since there is no longer any material flow, the material becomes even hotter or degrades even more making it even more difficult to get the flow back.
Situation FM2:
The extrusion screw (more specifically the feeding section of the screw) is extended by 50mm). This acts as a heat-break between the heaters and the hopper. In addition to that, the new hopper design actually actively cools the feeding zone to close to room temperature. Does this completely eliminate the premature melting? Almost. One should still be careful when transitioning from a high temperature material to a lower temperature or when flow is obstructed due to other reasons. We do have a free add-on available that you can 3D-print and mount on the hopper to reliably get pressure back in emergencies. The hopper has its own temperature sensor that can be read real-time or in the data log any time at a later moment.
Situation FM1:
When tuning settings there is sometimes a bit of a urgency to it. It can sometimes be quite a bit of scrolling to change simple settings.
Situation FM2:
We've changed to a touchscreen that enables you to quickly change settings as you go within seconds.
Situation FM1:
As mentioned in [H1.7], The FM1 controls the filament thickness by physically stretching the filament faster or slower. This is done by holding the filament between two rollers and controlling the speed of the rollers. However, for the FM1, there is no way to control how firmly the filament is held so when the filament is still too hot due to for example inadequate cooling, the filament can be squeezed by the rollers.
Situation FM2:
The puller has been improved to ensure more control over the clamping force between the rollers, preventing filament from getting flattened but preserving its grip to effectively full the filament. The clamping force has indication marks to ensure reproducable results. Setting the right tension is a matter of trial and error since it depends on the material and temperature depending friction coefficient between the processed material and the rollers.
Situation FM1:
The puller wheel, responsible for regulating the filament diameter, of the FM1 is made of polyurethane. A perfect fit for most low temperature materials. However, when processing 'sticky' materials like TPU can easily wind around the puller wheel when temperatures are slightly too hot. Especially when there is nobody to intervene this can cause big problems. Another downside of polyurethane puller wheels is their limited resistance to high temperatures causing the wheel to wear out relatively quickly.
Situation FM2:
In additional to our high-grip low temp puller wheel we will now offer a non-stick- high temp puller wheel. This option perfect for materials like TPU as well as for processing materials with high melting temperatures like PEEK.
Situation FM1:
The winding system on the FM1 works using a slipper clutch to set the filament tension when winding. The slipper clutch is adjusted by tightening or loosening a knob on the back of the machine. Since principle does not take into account that the spool is getting full over time and therefore causing the filament to get wound looser than in the beginning. Another problem is the fact that the slipper clutch relies on there being phyisical tension on the filament in the first place that might already be too much for stretchy materials.
Situation FM2:
We addressed these problems for the FM2 by letting the filament pass a light-weight lever measuring its own angle. Whenever the angle changes, the winder speed will change accordingly keeping the lever stable. This way there will be practically no tension at all on the filament. This raises the question: But don't you want the filament the be wound around a spool with at least some tension? That is right but only on the very last section of the filament where the filament has cooled down the most. Equal filament tension throughout the entire spool is now preserved while exerting minimal forces on the filament when they are still hot.
Situation FM1:
The hopper of the FM1 works perfectly for (spherical) pellets. When working with shredded flakes or powders the hopper faces challenges like bridging or rat-holing.
Situation FM2:
Apart from improving the hopper design in terms of thermal performance, we increased its slope, shape and smoothness for optimal material flow.
Situation FM1:
The FM1 has the ability to control filament thickness automatically based on the measured the filament thickness. This compensates for low frequency material flow fluctuations. When all process settings are perfect, there would actually not be a need for this since a fixed pulling speed should be able to do the job.
Situation FM2:
This functionality is implemented in the FM2.
Situation FM1:
Although automatic filament control is really useful for compensating for low frequency material flow fluctuations, it could also be seen as a way of 'symptom relief'. It is actually useful especially during the beginning of your material research project to address the core problem rather than using the automatic filament control as a means to fix it. Setting the puller speed manually is helpful to gain insights in all the action-reactions.
Situation FM2:
Having this functionality available is proven to be very useful and therefor kept in the design.
Situation FM1:
For the FM1 you can enter spool dimensions in order to let the spooling mechanism know how and where to wind the spool.
Situation FM2:
A nice bonus caused by increasing the length of the extrusion system and increasing the size of the gearmotor is that the FM2 can now accept spools up to Ø300mm in diameter and 100mm in width.
Situation FM1:
When purging the filament maker, transistioning to a material or tweaking process parameters, most likely you're not using the winder and puller. Many people including ourselves used to just put a piece of cardboard on top of the filament sensor.
We have even seen cases where the material inside the extrusion system was so degraded that it could really make a mess.
Situation FM2:
We created a simple fix for this problem. Along with the FM2 we'll send a 'purging bib' that can easily be mounted underneath the nozzle. The bib is non-stick so the extrudate can flow nicely out of the machine. This give the user more time to focus on other things and drastically reduce the risk of damaging the machine.
3. More forgiving to mistakes
Extrusion can be satifying process but the with the vast range of different kinds and grades of polymers and the complete freedom of controlling all parameters but can also invite a lot of problems. Knowing how to resolve these problems when they occur is always the most effective. This requires a lot of training and understanding of the process. We invested a lot of effort in making the process more forgiving when something goes wrong. Making mistakes is an important factor in any learning process and should be okay.
Situation FM1:
Purging an extruder is a great way to go from one material to the next but has a major shortcoming; you have no certainty that there are no left over materials stuck anywhere in the extrusion system. Ideally, you would like to remove the screw out of the extrusion system and clean it seperately.Unfortunately, the FM1 does not allow this in an user-friendly way.
Situation FM2:
We have focussed on better replaceability of critical components like the extrusion screw. By following a few steps the screw can now removed for proper cleaning.
Situation FM1:
This point really ties down to the previous point and is the root cause of why the extrusion screw is hard to remove. The design of the die-head is assembled during production by following careful steps to make sure the nozzle is pointing down after the die-head is placed. When the die-head is removed with the FM1 design, the orientation of the nozzle can not be guaranteed when putting the die-head back on. This is a shame because a lot of the contaminations could acutally be residing within the die-head.
Situation FM2:
This has been addressed in the mechanical design of the extrusion system by making the orientation of the nozzle independent from the way the die-head is attached to the barrel.
Situation FM1:
The machine is for the majority designed for correct use. It is not uncommon that the outer casing is removed. The outer casing contributes to its structural integrity making the machine tip over when dissassembling the outer casing.
Situation FM2:
We have simply added machine feet under the FM2's chassis that when plates are removed, the machine stays perfectly stable. The plates are carefully split, each devoted to accessing certain parts.
Situation FM1:
Removing/exchanging a nozzle on the FM1 is reasonably doable. Doing this repeatedly however really runs into the limits of the thermal insulation wool that has be folder open and tied back down.
The insulation wool covers most of the nozzle but leaving the tip exposed leaving it vulnerable for 'die-freeze' and nozzle build up caused by the fans.
Situation FM2:
The nozzle of the FM2 is nicely tucked away making it much less prone for these problems. Secondly, the insulation that is used now allows indefinite nozzle changes.
Situation FM1:
When frequently changing spools it is quite a tedious job of unscrewing and screwing on the spool holder on an empty spool.
Situation FM2:
We decided to improve the user experience that all of this unneccesary work is eliminated.
Situation FM1:
The extrusion system of the FM1 is thermally insulated from the rest of the machine to efficiently heat up the system. The thermal insulation is made of a glass fibre wool that is not really reuseable after it has been removed when removing a nozzle of doing any other maintanance.
Situation FM2:
Since maintainance is a realistic scenario we designed a thermal insulation sleeve that can be removed and put back indefenitely preserving its insulating performance.
4. Future proof design
We provide equipment that serves as a tool to enable innovators to succeed in their research. Since every (research)project is unique, our equipment could still be limited in solving your specific problem. Instead of accepting these limitations we want to be prepared to answer those needs.
Situation FM1:
FM1 is using microcontrollers that make future updates very challenging and is designed just to meet its requirements but realistically not much more than that.
Situation FM2:
A lot of the design changes that have been made in terms of data-monitoring and process control open a new world in solving many kinds of problems. You can expect continuous software updates from us but take your opinion very seriously.
Situation FM1:
Since the electronics are limited, any customizations or add-ons can only be stand-alone systems that do not interact with the machine.
Situation FM2:
The potential is huge to expand on the FM2. That's why we have integrated two CAN bus connectors on the FM2 that allow us or even users to customize the machine that can interact with the REST API. Another design decision that promotes future customization is the way we designed the hopper. It allows itself to easily screw on different attachments that could potentially interact through one of the CAN bus connectors; like for example dosing mechanisms, feeding mechanisms, mixing mechanisms and so on. We have many ideas of potential uses but gladly hear about your needs.
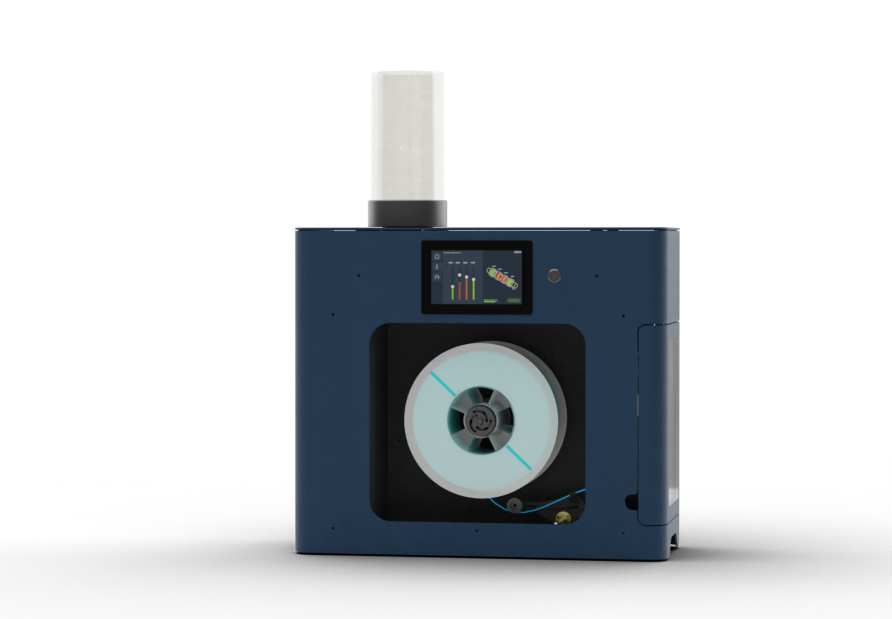
The Filament Maker TWO is here!
Ready to take the next step? Talk to our Material Specialists and see how the Filament Maker TWO can support your research.