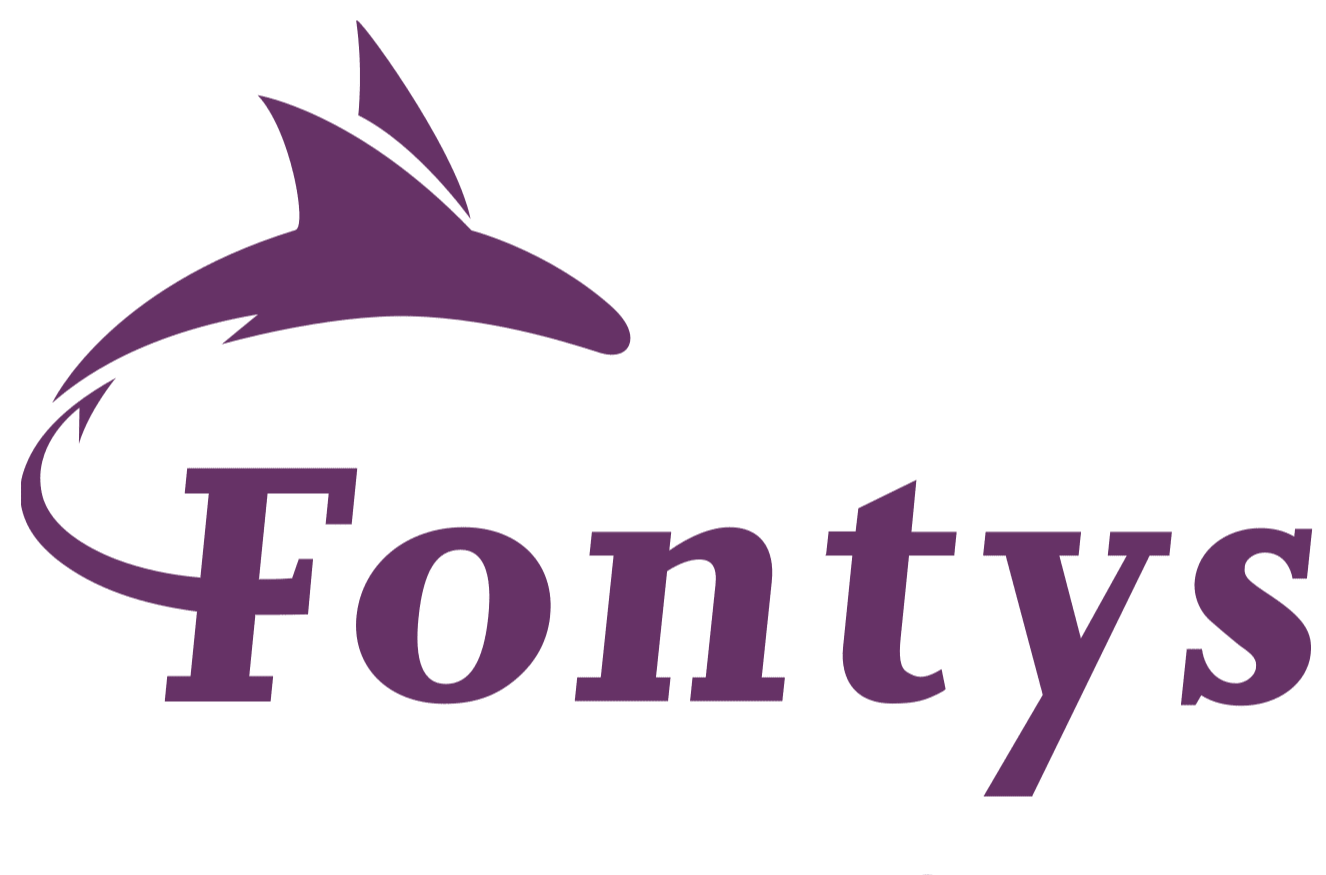
Diving into Hands-on Polymer Research
Introduction
Training Future Scientists
Fontys is an institute with a proactive approach to education. Its polymer studies wing needed a simple, small-scale setup to provide students with hands-on training in material extrusion and recycling, without running up unnecessary costs, or wasting time and resources in the process.
Background
One of the largest educational institutes in the Netherlands, Fontys University of Applied Sciences offers bachelors’ and masters’ programs in fields ranging from engineering and technology, to social sciences and healthcare. Future-oriented courses in polymer studies are offered at the university’s Natural Science wing, located in Eindhoven. Here, students use 3D printing to enhance polymers and develop sustainable solutions for the rapidly evolving additive manufacturing industry.
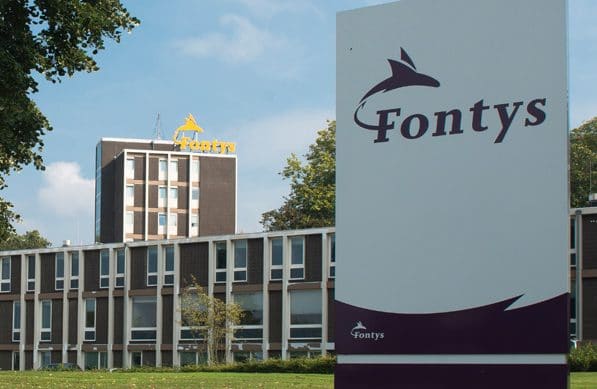
The Challenge
To provide effective, hands-on training to polymer studies students, Fontys needed an accessible, user-friendly device that offered more flexibility than large-scale extrusion machinery, without leading to steep learning curves for both the faculty and the students. By extension, the university was also looking to minimize the drain on its time and resources.
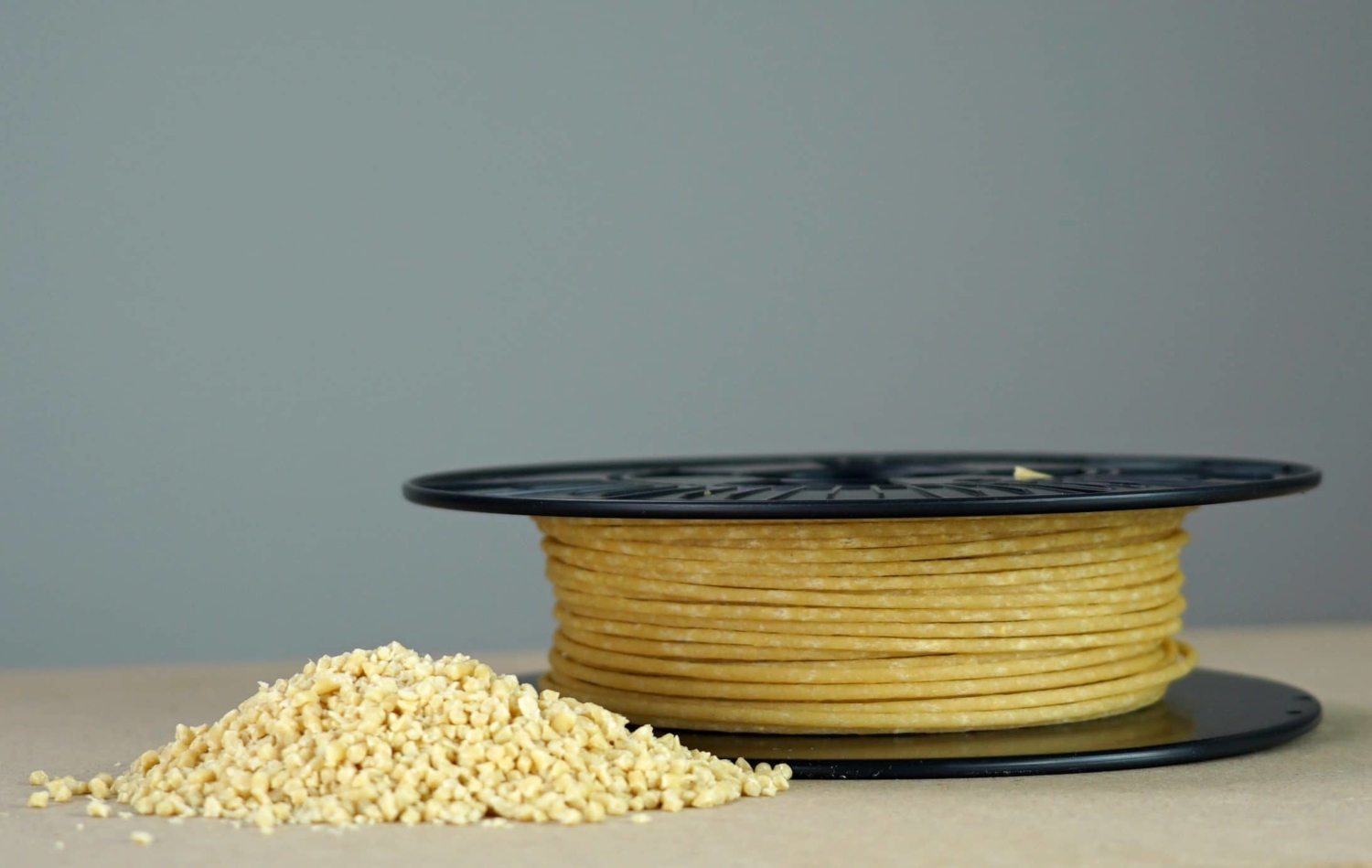
The Solution
The Composer 450 offered Fontys the ability to train students in the specifics of polymer development, by allowing them to extrude small batches of custom filament. The desktop filament maker could serve as an effective research tool, without leading to wastage of time or material. Using the Composer 450 filament maker would also be cheaper than relying on industrial extrusion equipment.
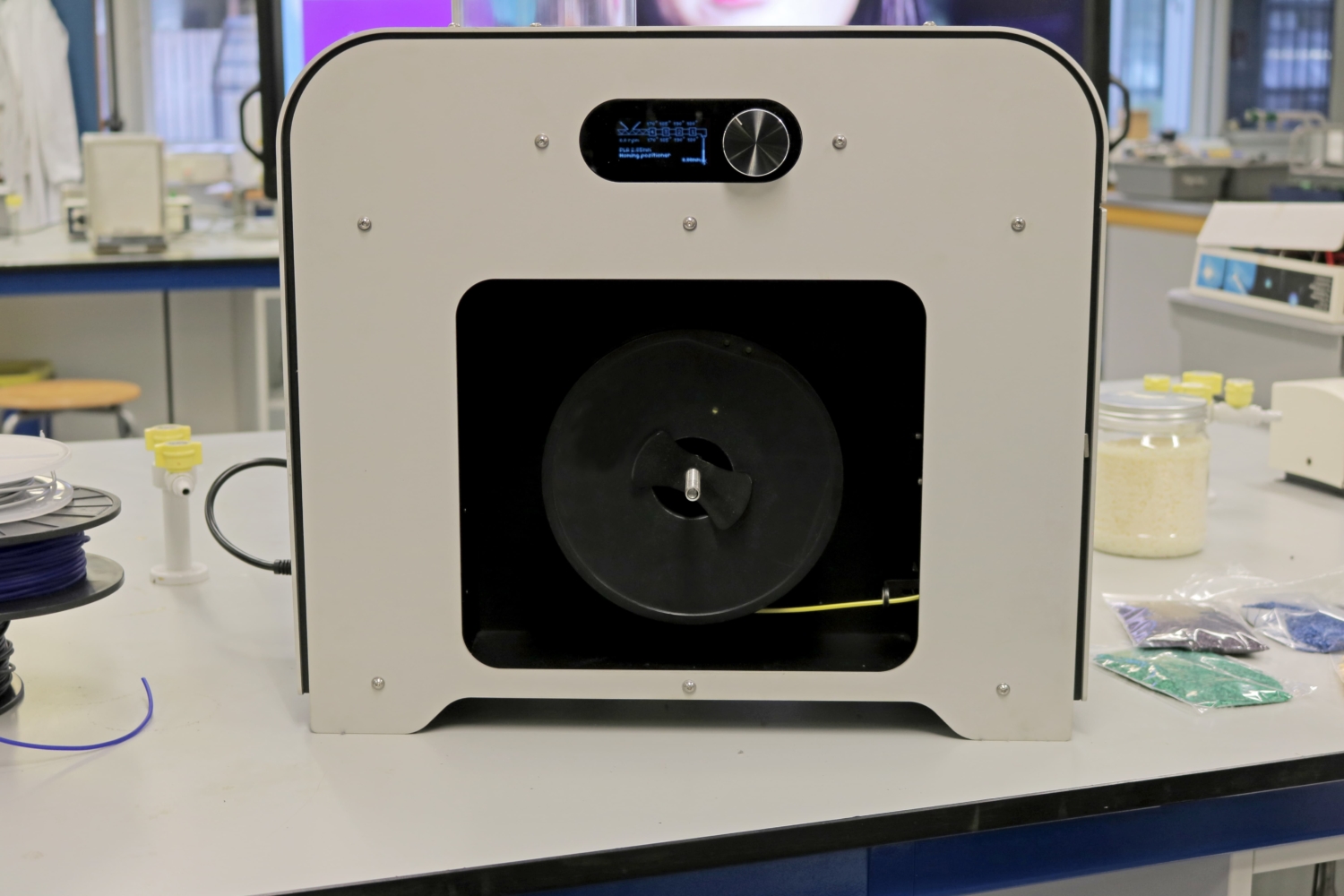
Get the Full Fontys
Customer Story
Customer Story
Workflow Highlights
From nanotubes to sustainable polymers – developing new materials
- Ability to study recyclability with small batches of material
Using the Composer 450, students have been able to study the properties and recyclability of polymers like PLA and PET, using as little as 1kg of material at a time. - Flexibility to research a wide variety of polymer composites
The Composer 450 has already allowed students extrude innovative materials for 3D printing nano tubes, and will be a part of their efforts to develop sustainable polymer-cellulose composites. - Lower training time and costs; reduced material wastage
Students at Fontys find the small-scale setup easier to understand and work with than complex extrusion machinery. This has sped up research at the university’s polymer studies lab. - Effective, hands-on training with a simple, in-house setup
Thanks to the Composer 450, Fontys no longer depends on large-scale extrusion machinery to train its students. Over 20 students have successfully used the extruder for a variety of projects.
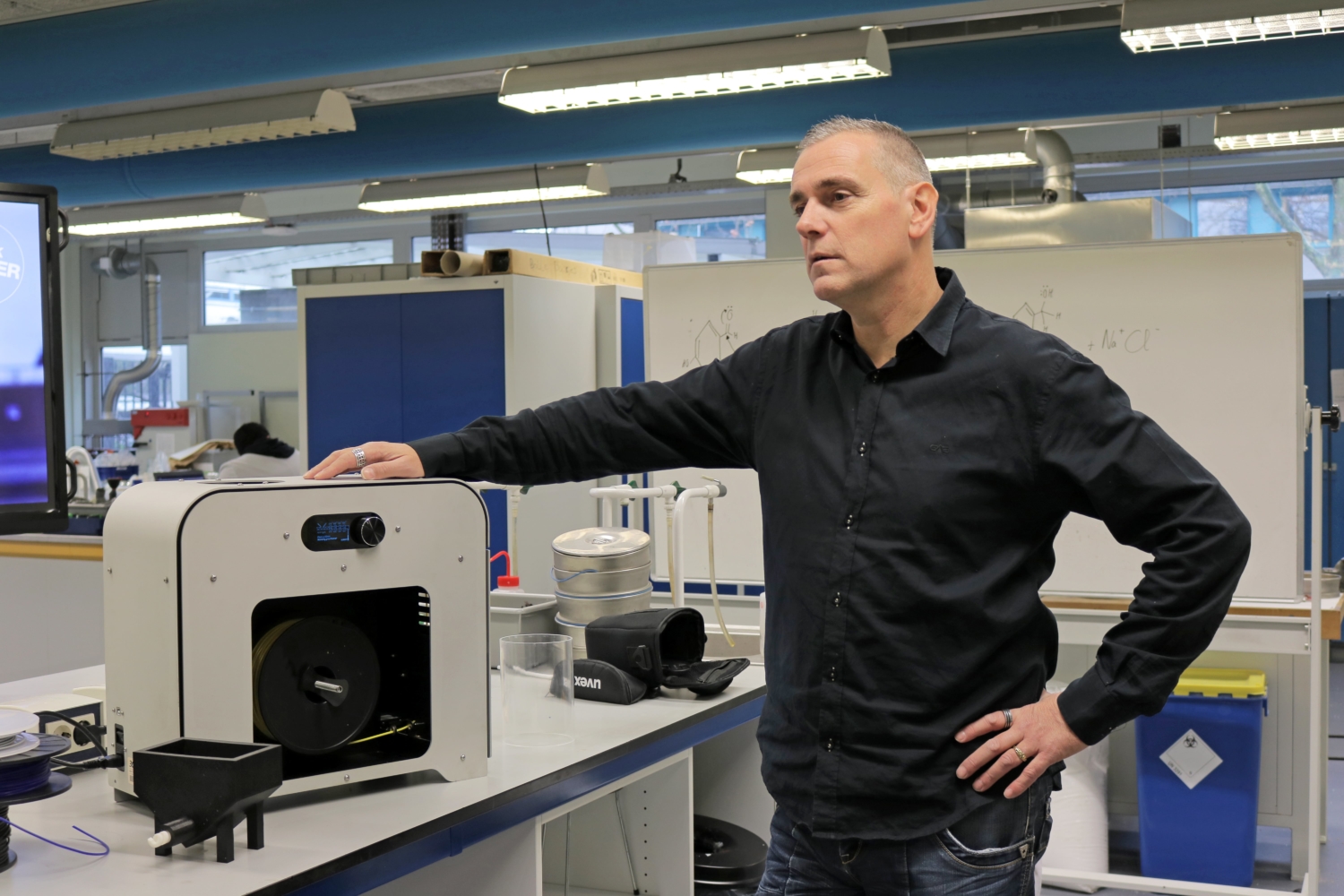
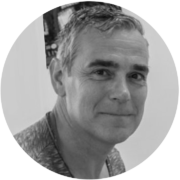
More Success Stories
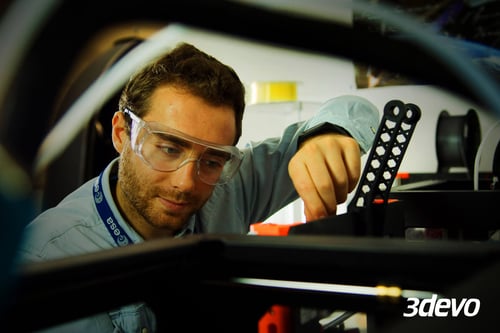
European Space Agency
How do researchers at ESA have the freedom to innovate – without wasting resources in the process.
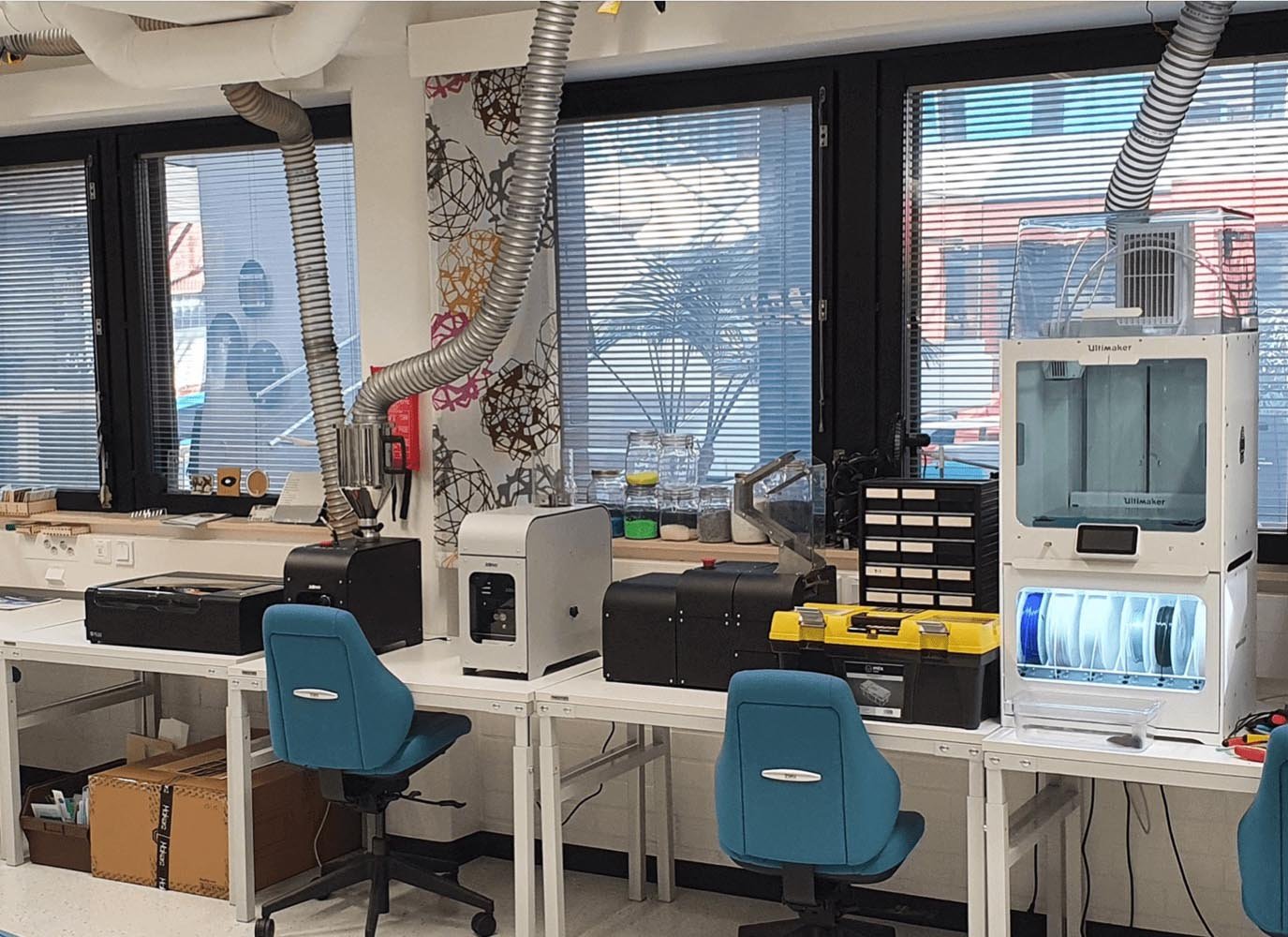
Lapland University
How Lapland University brings a sustainable closed-loop system within their 3D Printing Lab.
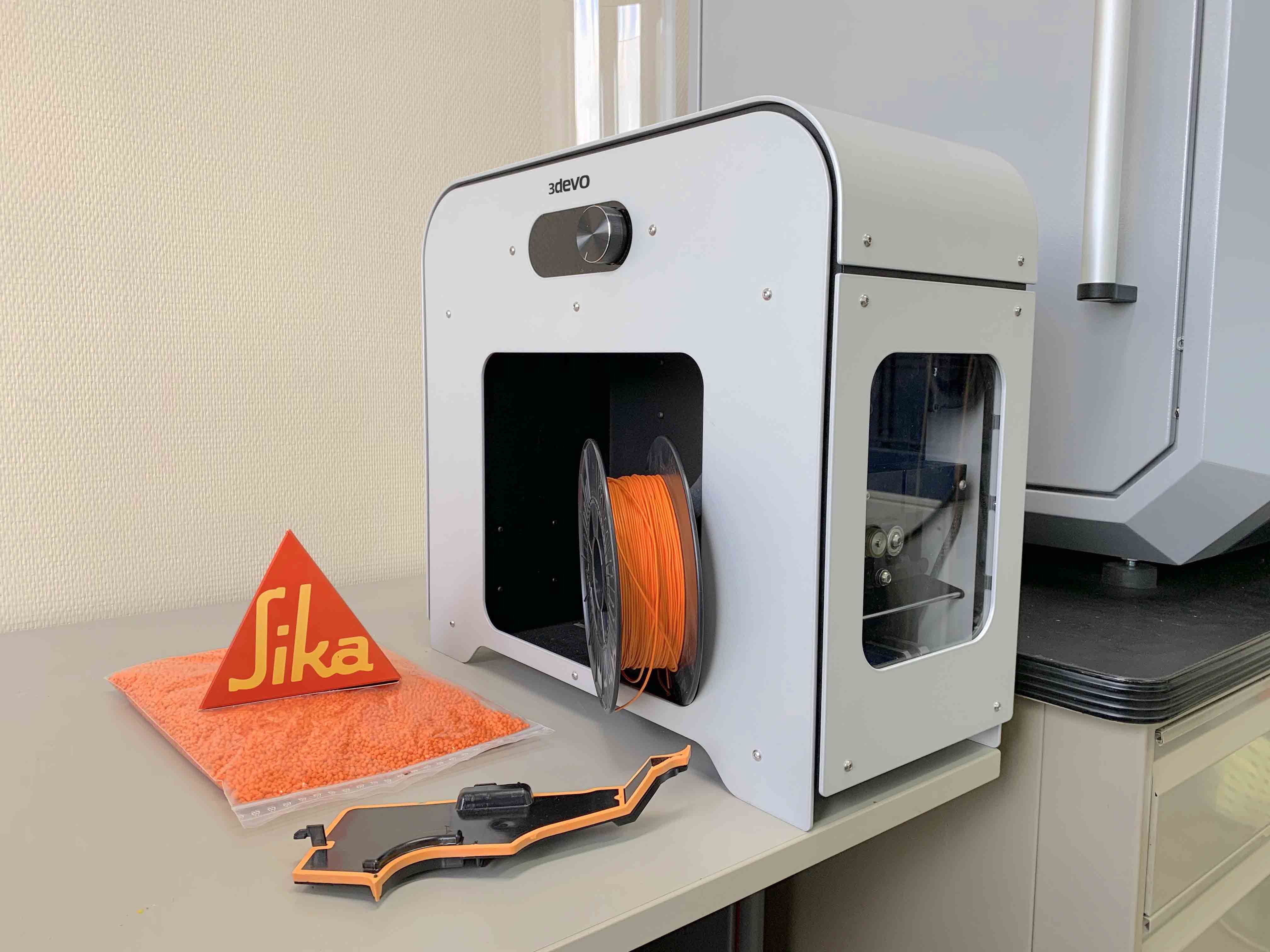
Sika Automotive
How Sika Automotive managed to reduce their production time – for their cavity sealers -from weeks to days.