
Accelerating Ground-breaking Space Discoveries
Introduction
Developing Materials & Technologies
for Future Spaceflight Applications
An agency that explores new materials and technologies for space applications, requires the freedom to experiment and innovate – without wasting resources in the process. The Composer 450 has brought this freedom and efficiency to ESA’s research and development process.
Background
The European Space Agency (ESA) is Europe’s gateway to space, and has been shaping the development of Europe’s space capability since 1975. ESA has 22 Member States and over 5000 employees. Among its many components is the European Astronaut Center (EAC), located in Cologne, Germany. EAC serves as a training center for astronauts, provides astronauts with medical support, and communicates with astronauts in space. Recently, it has also become home to the young and dynamic Spaceship EAC initiative, which focuses on human space exploration beyond the low Earth orbit. The team currently studies the sustainable exploration of our Moon by addressing several challenges, including additive manufacturing for tools and spare parts.
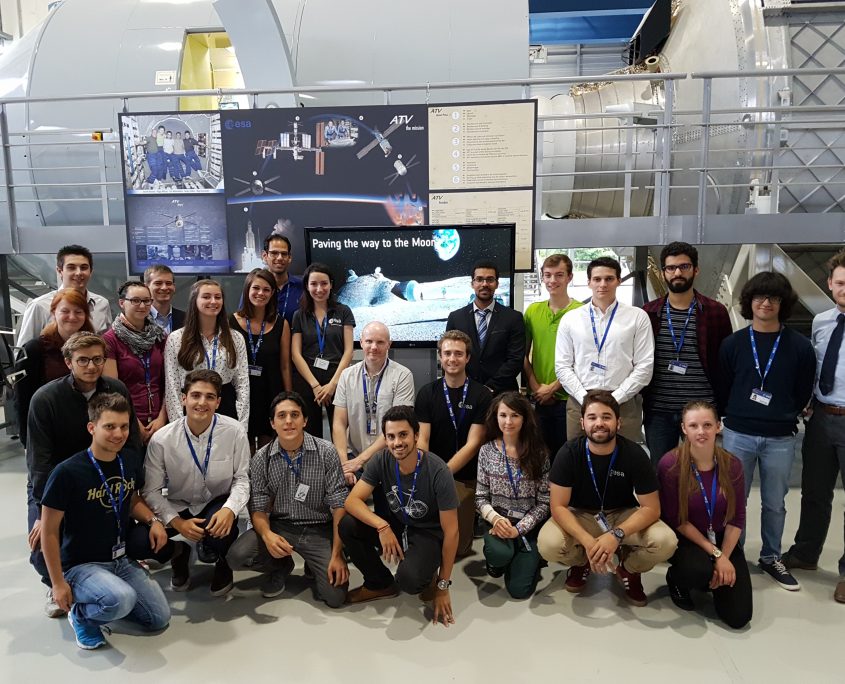
The Challenge
Spaceship EAC researchers work towards enhancing the current capabilities of ESA’s spaceflight programs. They use 3D printing to prototype ideas for different projects, and are exploring its potential as an in-space manufacturing and recycling tool.
To achieve these objectives, Spaceship EAC researchers typically require very small quantities of printing filament, with very specific properties. The low commercial demand for these custom materials would make them difficult to source. Spaceship EAC would thus need to get standard printing filament customized at an external facility – a process that relied on third party expertise and could increase lead times.
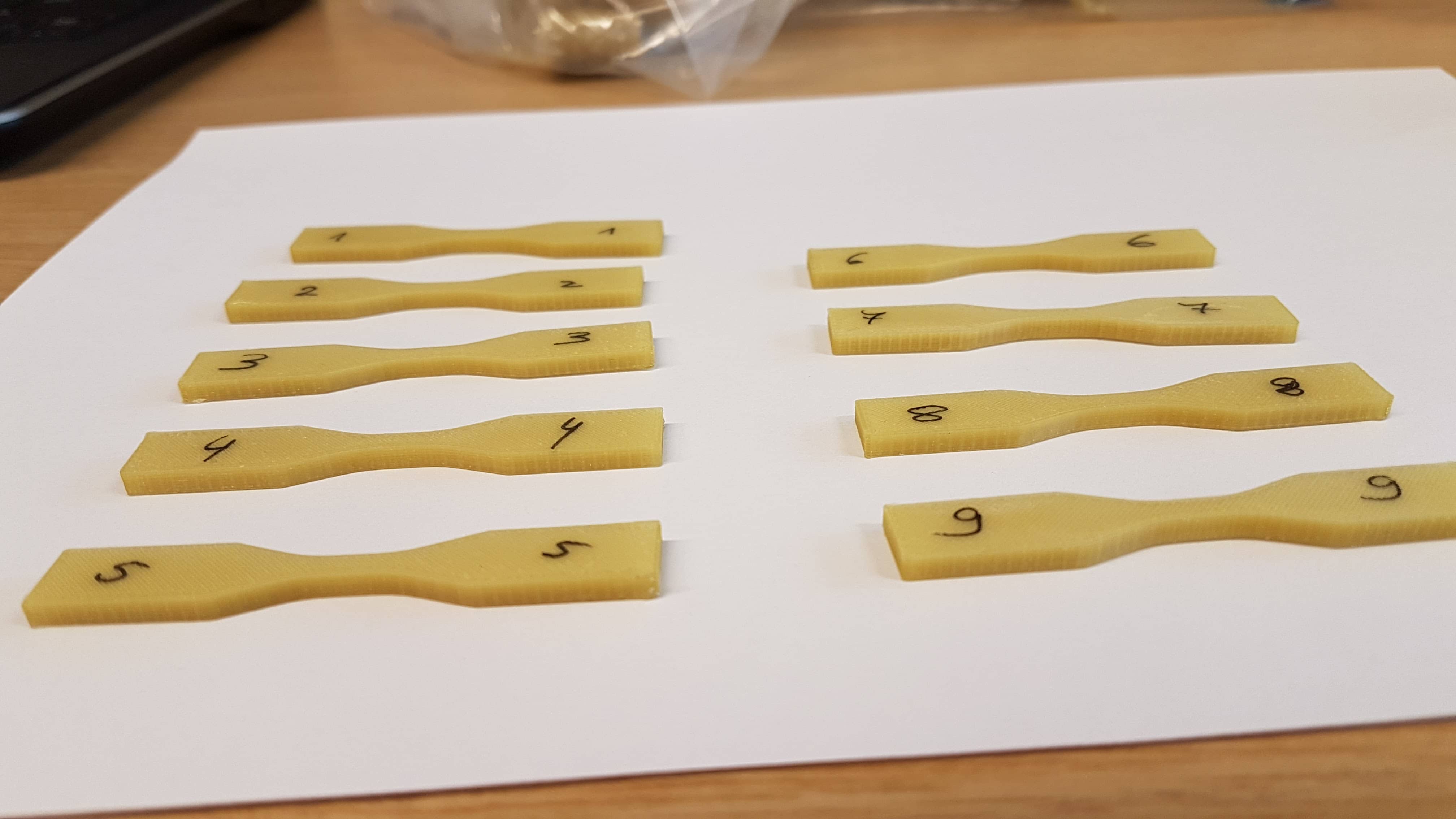
The Solution
Adding the Composer 450 filament maker to their setup gave Spaceship EAC the ability to develop 3D printing filament in-house. The desktop extruder supports experimentation with small quantities (2-5kg) of polymer, thus serving as the perfect solution for ESA’s small-scale testing and prototyping work. It reduced Spaceship EAC’s dependence on the expertise and availability of third-party filament suppliers and gave them the freedom to create new filament by modifying basic materials. This equated to shorter lead times, and greater flexibility to innovate with non-standard materials.
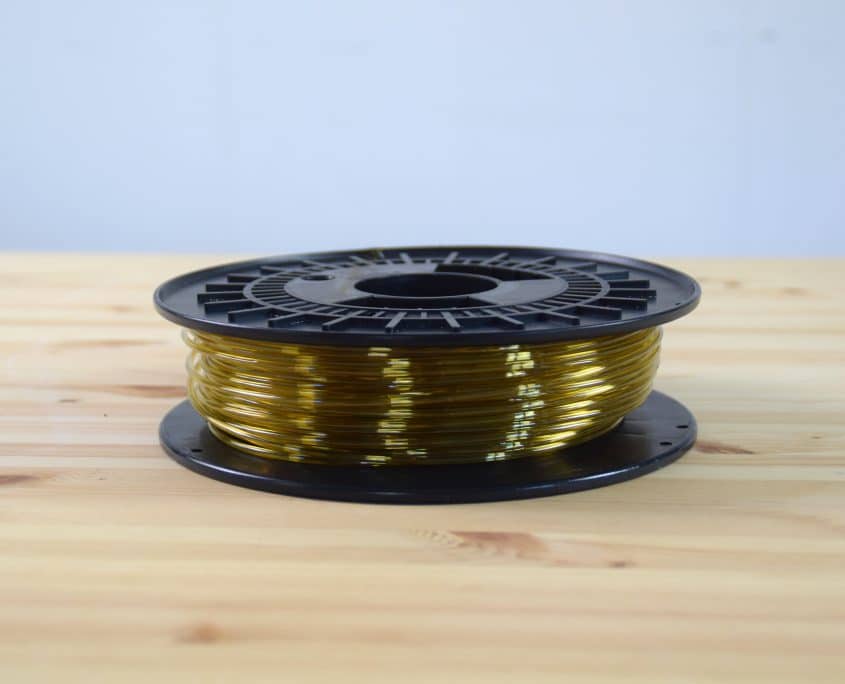
Get the Full ESA
Customer Story PDF
Customer Story PDF
Workflow Highlights
Developing Materials & Technologies for Future Spaceflight Applications
- Freedom to research and explore new material applications
ESA has used the Composer 450 to develop custom quantities of PLA-based filament for research and development iterations, and is conducting trials with other polymers such as engineering thermoplastics. - Ability to extrude small quantities of filament, thus saving resources
The small quantities of custom filament that the Composer allows ESA to develop, allows for quick and cost-effective testing and prototyping. - Greater control over material research and prototyping
The Composer enables ESA to produce filaments in-house. This in turn has minimized the organization’s dependence on external filament manufacturers, letting them conduct material research and prototyping on their own terms. - Flexibility to modify and customize 3D printing materials
The Composer gives ESA scientists the intellectual freedom to create innovative new composites for future space applications. They also retain intellectual property rights to the materials and techniques developed.
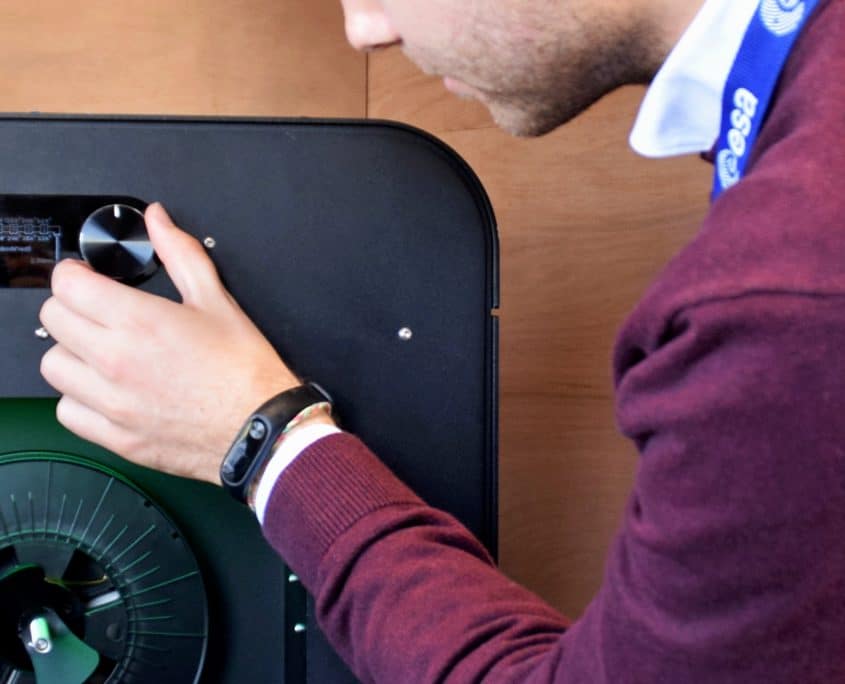
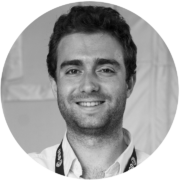
More Success Stories
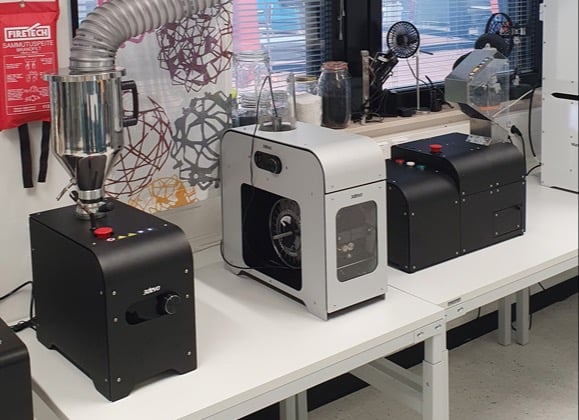
Lapland University
How Lapland University brings a sustainable closed-loop system within their 3D Printing Lab.
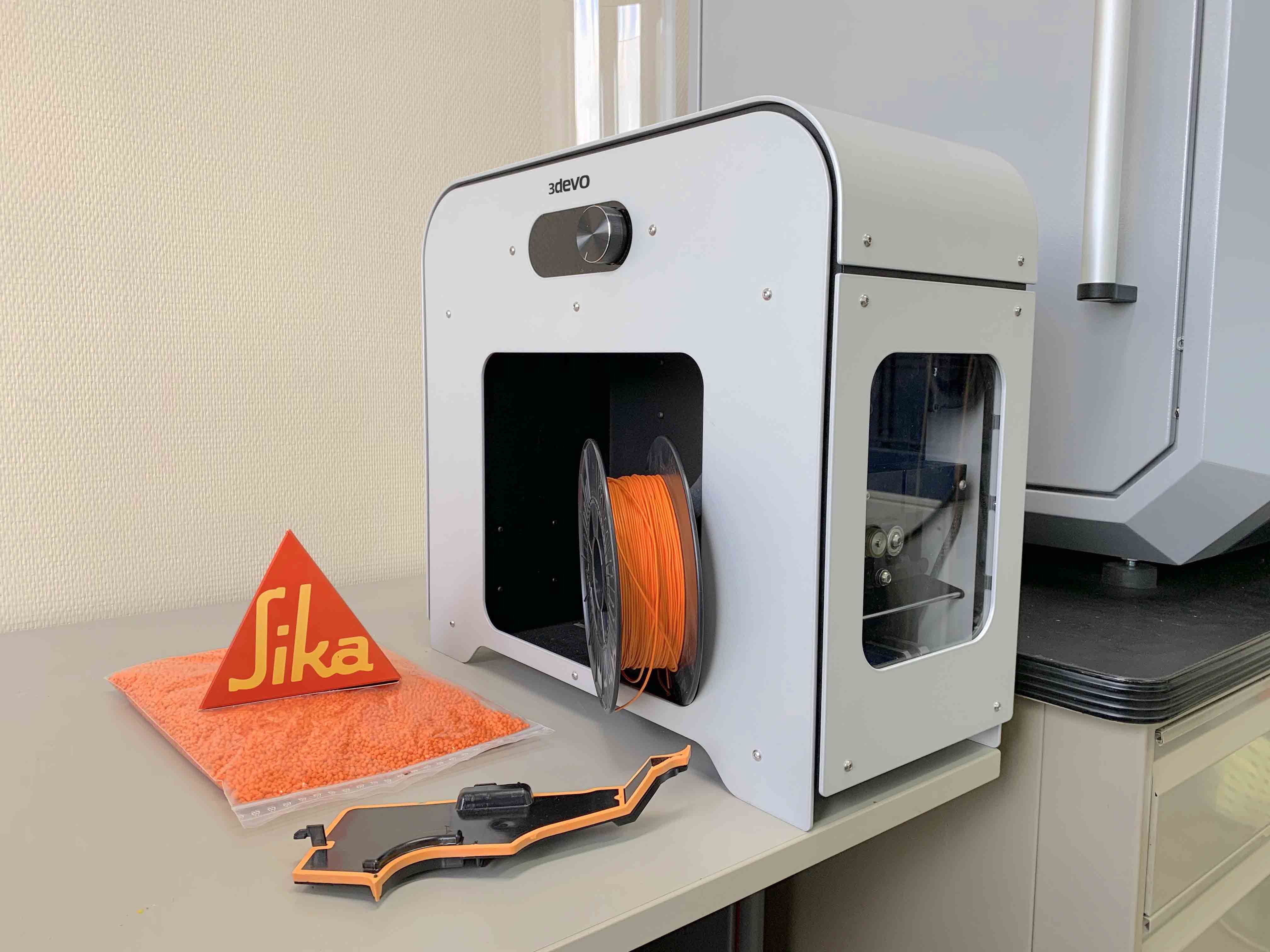
Sika Automotive
How Sika Automotive managed to reduce their production time – for their cavity sealers -from weeks to days.