Introduction
Developing Sustainable Solutions for Prototype Manufacturing
AZ3D, a prototype manufacturing company based in Tucson, Arizona, sought to manage and repurpose their used MJF (Multi Jet Fusion) material in an environmentally friendly way. The nylon-based powder is notoriously difficult to dispose of and cannot be used again in the MJF/SLS process. It is therefore often necessary for companies to store large quantities of the waste powder for years without a better solution.
Background
Founded by Rocky Parkerton, a CNC machinist by trade, AZ3D supports its customers with SLS and SLA additive manufacturing in-house. The company helps customers realize their end-use products through rapid prototyping and quick iterations, leading to a faster testing and final production schedule.
AZ3D faced the challenge of ethically disposing of seven 55-gallon drums of used MJF material, each weighing approximately 130 kg.
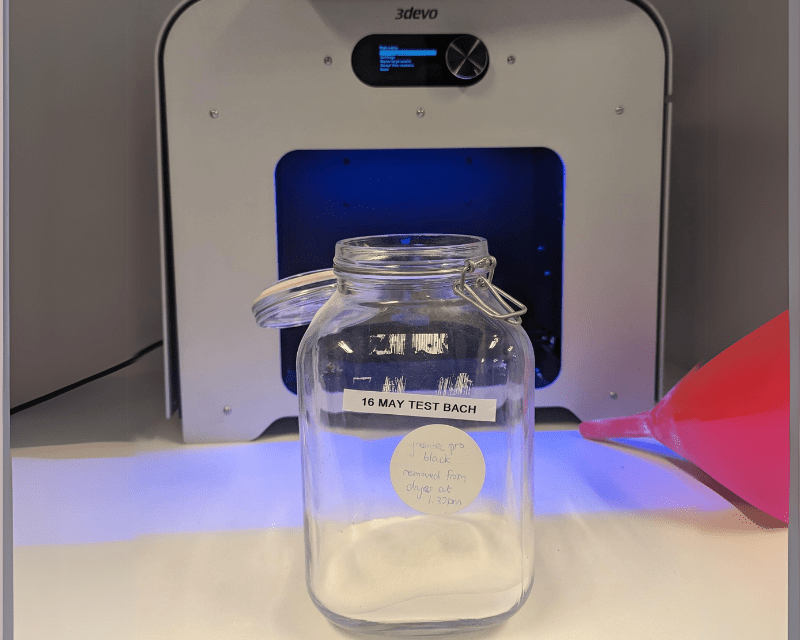
The Challenge
AZ3D needed a method to recycle its MJF material without contributing to microplastic pollution. Traditional plastic pelletization companies rejected the material, leaving AZ3D with limited options. The goal was to find a way to transform this waste into usable filament for 3D printing. After 3 years of consistent research, Rocky Parkerton finally discovered 3devo. Our team was enthusiastic about the challenge and agreed to commence testing.
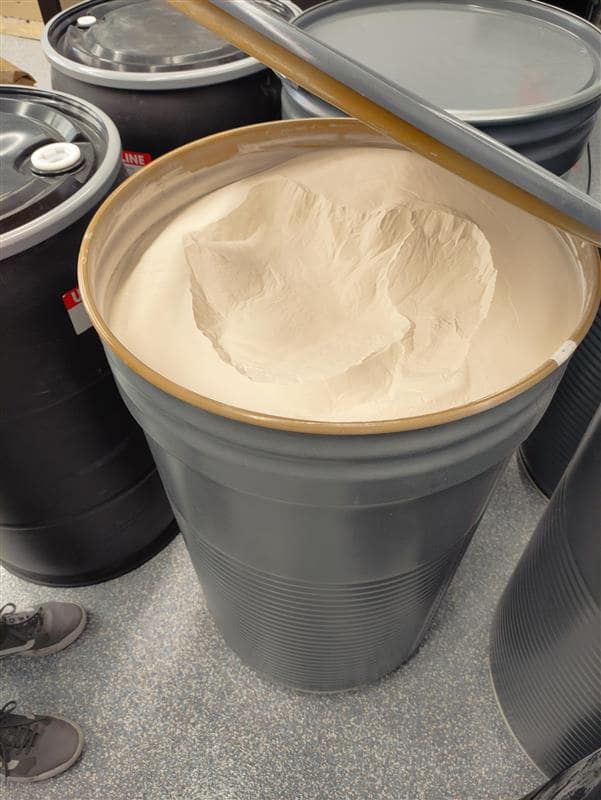
The Solution
AZ3D sent a large sample of MFJ waste powder to 3devo's facility in the Netherlands, where it underwent several phases of testing. 3devo's team of Materials Specialists performed a test extrusion of the customer's powder in the onsite Innovation Lab. After optmizing the settings for the most efficient extrusion process, the team successfully produced a spool of MJF filament for FDM printing.
The final setp was for Lead Materials Specialist, Timo van der Laak, to visit Rocky Parkerton at the company's facility in Tucson, Arizona, for a comprehensive onboarding and implementation of the machine.
AZ3D can now produce two spools of filament per day, with intention to increase this output.
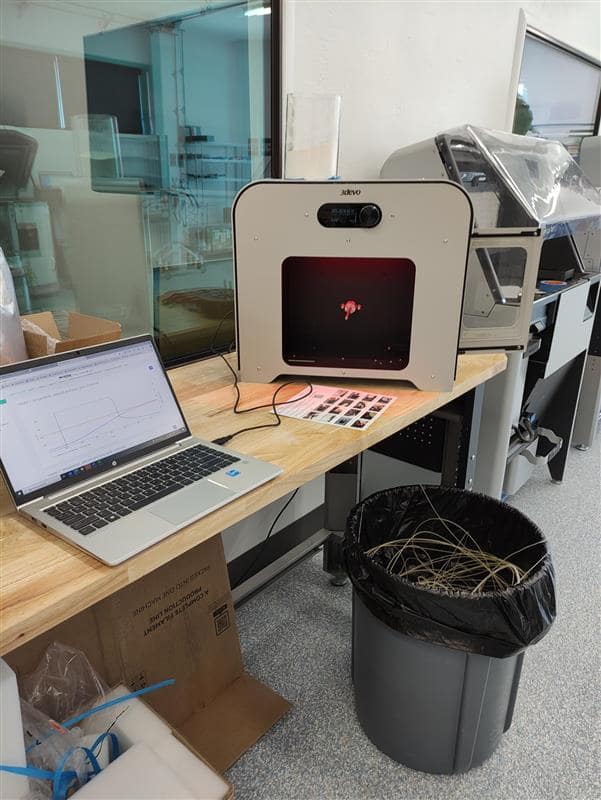
Get the Full AZ3D
Customer Story
Customer Story
Workflow Highlights
Increasing Sustainability and Efficiency
- Sustainable Practices
With an in-house filament extrusion system, AZ3D can now manage the large quantities of MJF/SLS powder waste ethically and prevent microplastic pollution. - Future Developments
Thanks to 3devo's Co-Creation initiative, talks are underway for AZ3D and the 3devo R&D team to collaborate in the development of a closed system for processing material directly from the storage barrels to the extruder.
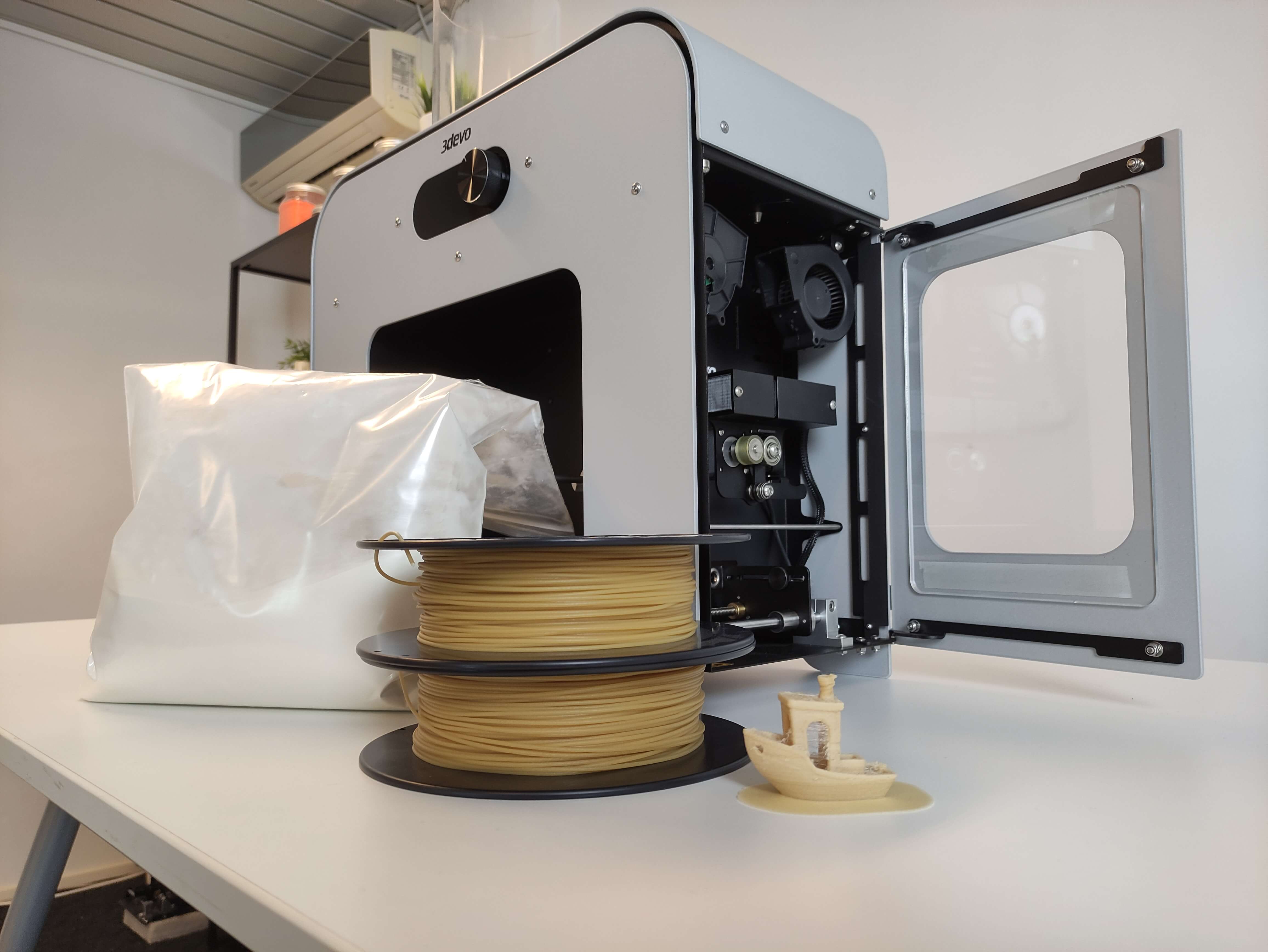
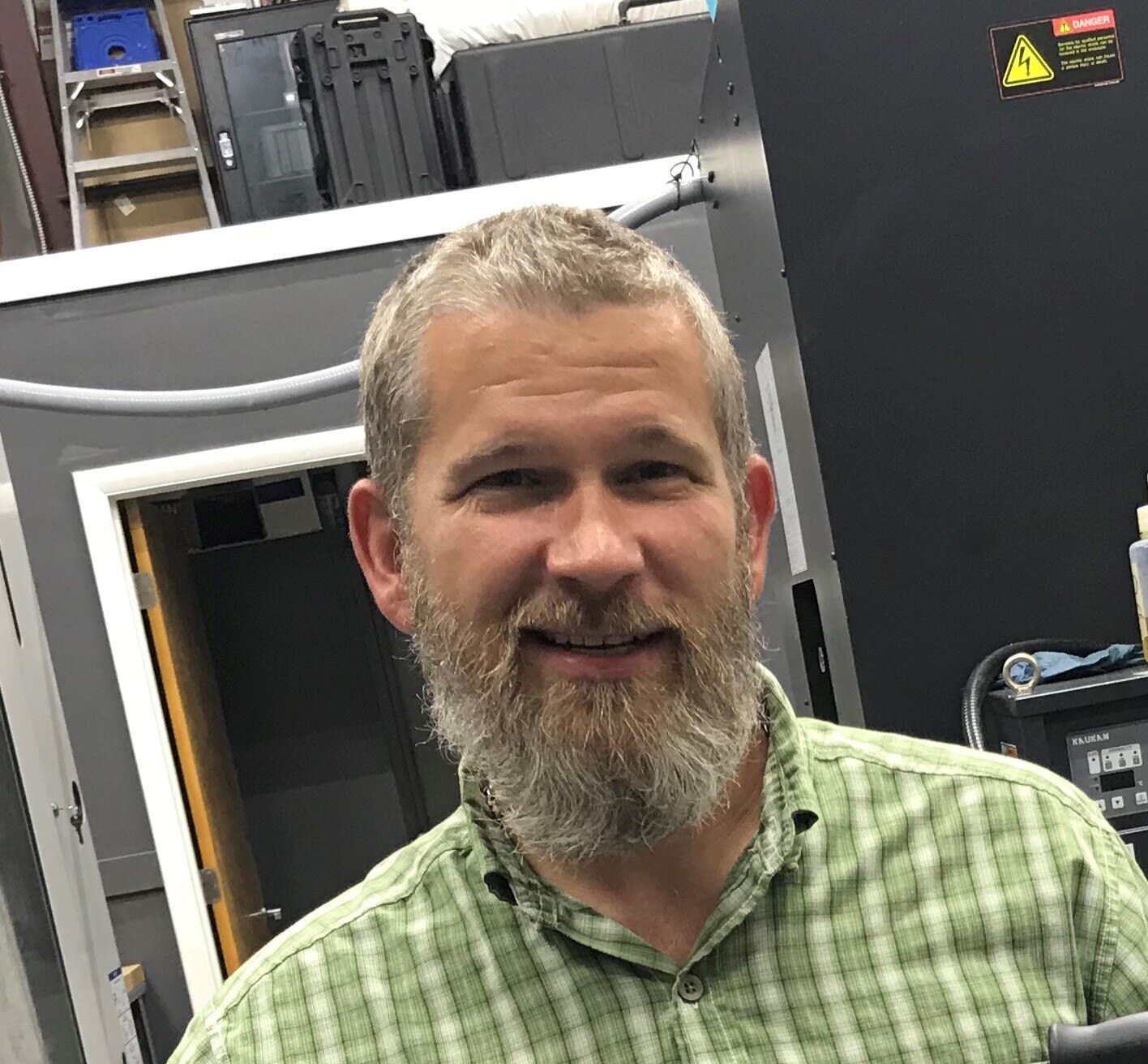
More Success Stories
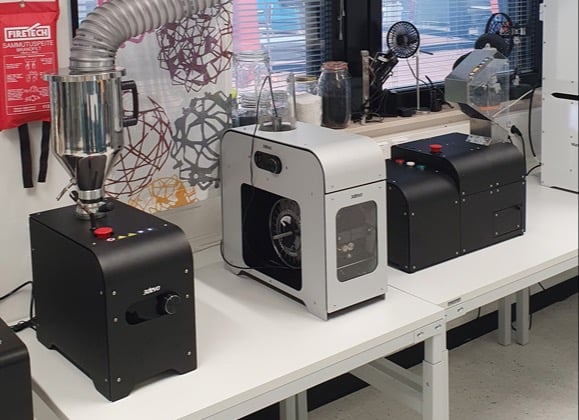
Lapland University
How Lapland University brings a sustainable closed-loop system within their 3D Printing Lab.
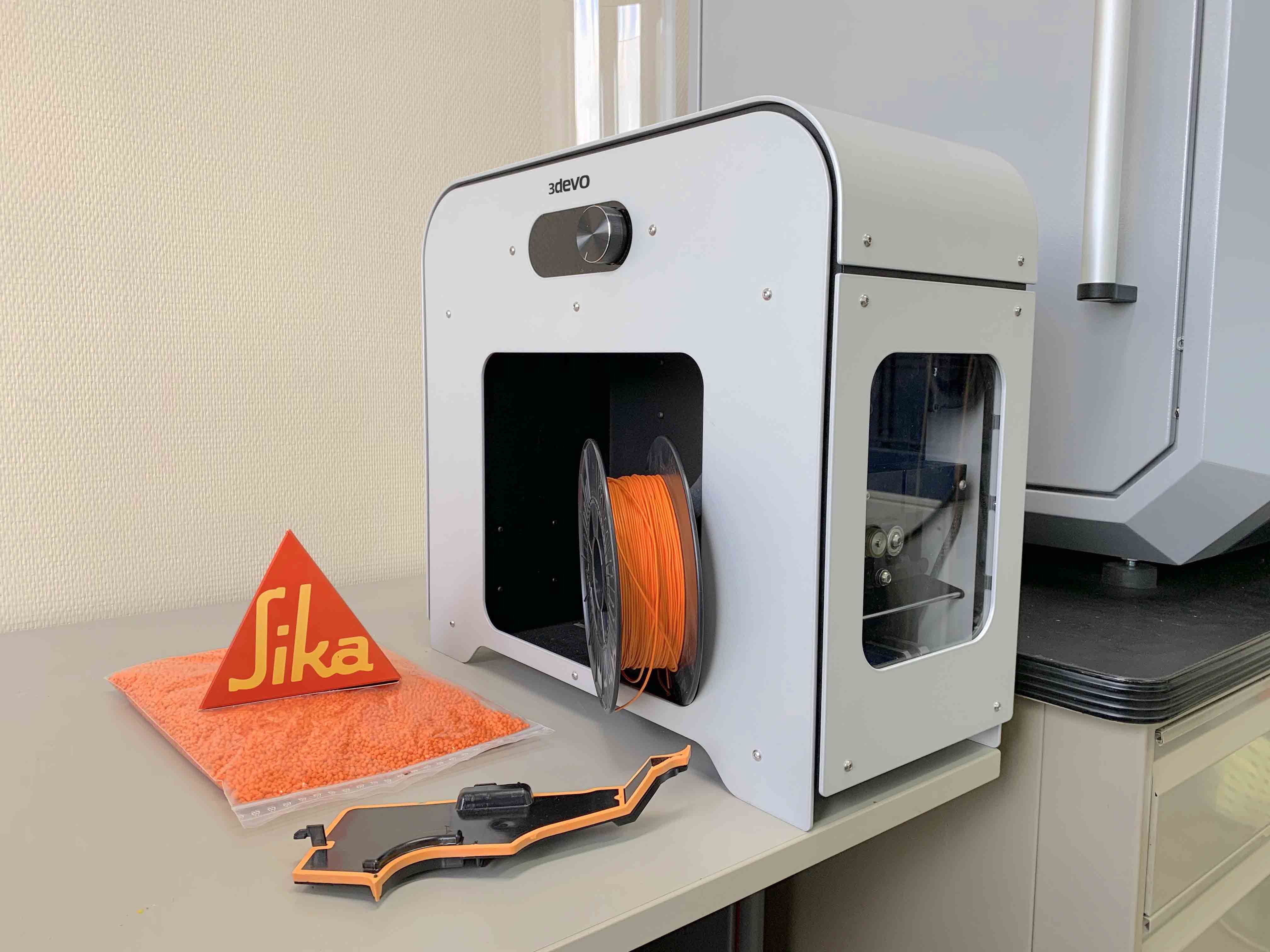
Sika Automotive
How Sika Automotive managed to reduce their production time – for their cavity sealers -from weeks to days.
Get the Full AZ3D
Customer Story
Customer Story