
Recycling in the Automotive Industry
Introduction
Maximizing efficiency,
while reducing development times
Audi, one of the most successful car makers in history, needed to look within if they wanted to move towards a more sustainable path within the industry. With the excess amounts of plastic packaging, 3devo’s Shr3d It plastic shredder, AIRID Polymer Dryer, and Precision 450 Filament, have helped Audi repurpose their plastic waste into 3D printed tools that assist their employees in their day-to-day tasks.
Background
German car manufacturer Audi has been a global leader in the automotive industry since its establishment in 1909. It recognizes high performance, reliable build quality and progressive design as its key areas of focus. Audi’s sustainability initiative extends beyond electric cars, and now the brand has taken steps internally to introduce eco-conscious practices to its design and production departments. 3devo’s full solution allowed them to establish a three-step solution for the closed-loop usage of plastics.
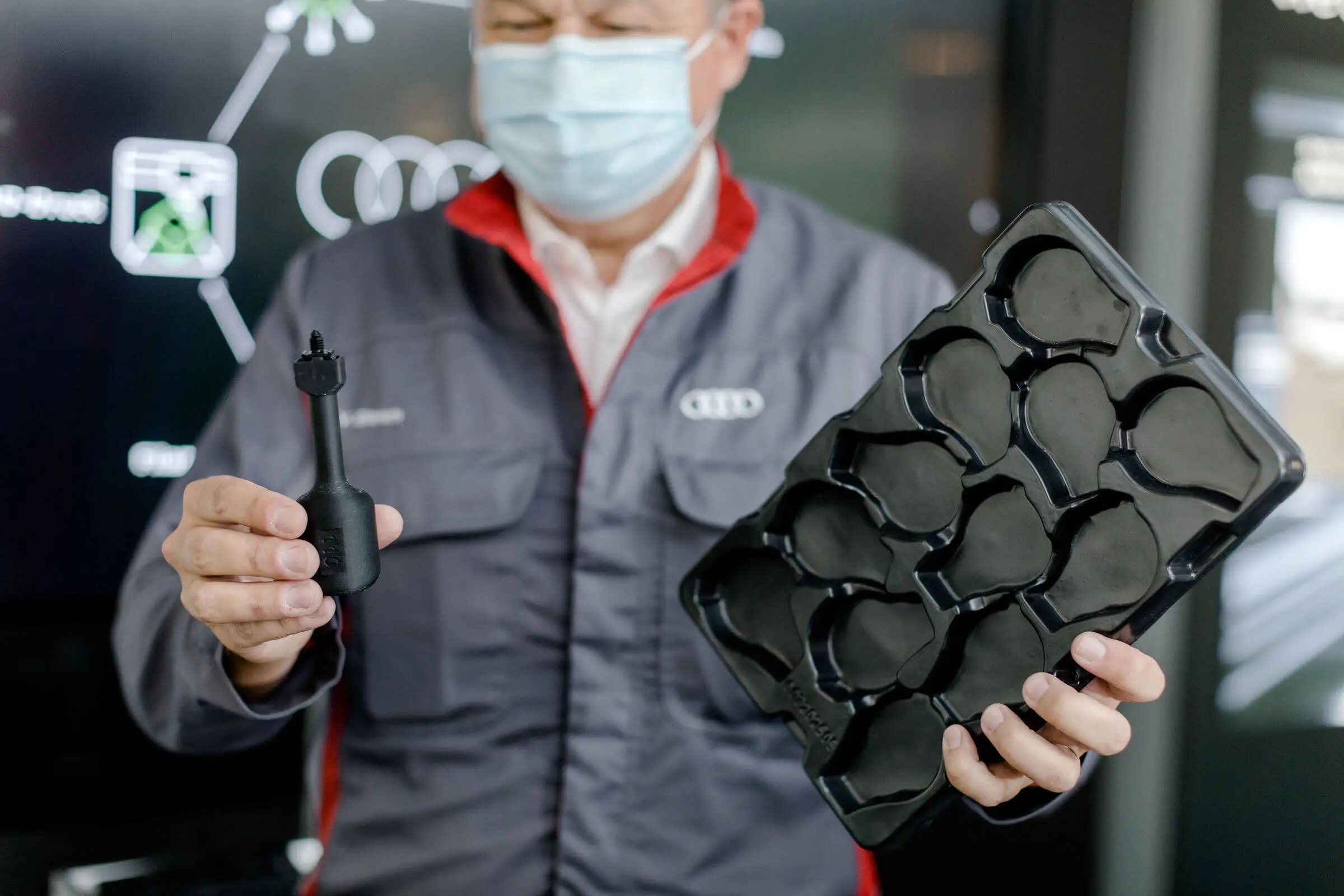
The Challenge
As part of their initiative to strengthen and expand their recycling efforts, luxury automotive brand Audi has been exploring the “chemical recycling of plastics from automotive manufacturing,’’ in ways that are both environmentally and financially viable. Their ‘’Mission: Zero’’ project seeks to encourage minimal or closed-loop usage of plastics, as a step towards net-zero carbon emissions by 2025. The primary challenge was to achieve this without compromising automotive component quality.
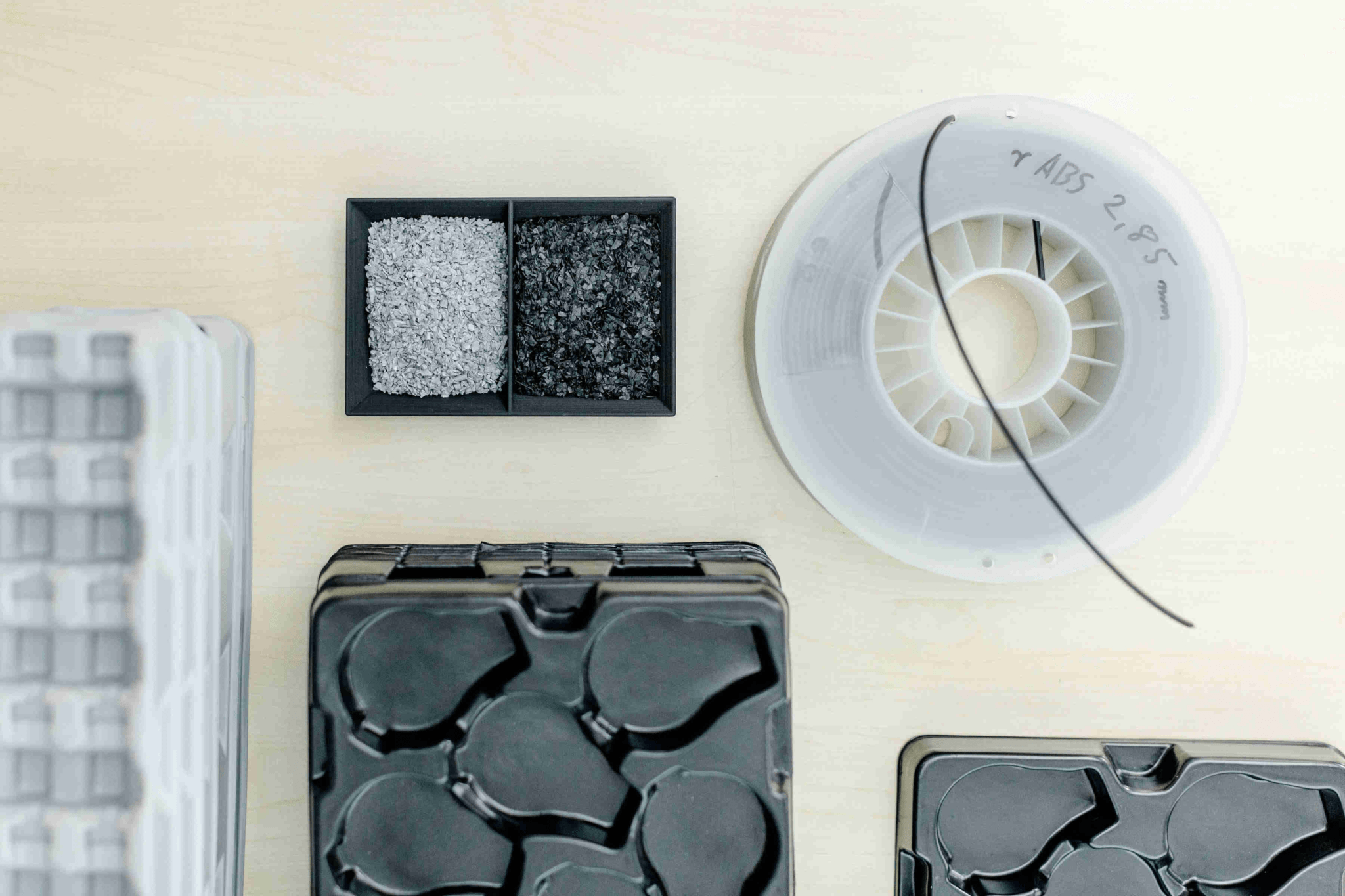
The Solution
After identifying key areas where plastic use and wastage are maximum at most of their sites, Audi saw the potential for a closed-loop plastic usage cycle and purchased 3devo’s full set of three machines. The Shr3d It shredder, Airid dryer and Precision 450 filament maker created an eco-system that could utilize unneeded plastics in a circular manner. This arrangement allowed Audi to evolve a plan for minimizing its usage of new plastics and bringing ‘’Mission: Zero’’ closer to implementation.
%20(1).png?width=2048&height=1365&name=Mission-Zero-Audi-1-2048x1365-min%20(2)%20(1).png)
Get the Full Audi
Customer Story
Customer Story
Workflow Highlights
- Established Three-Step Solution
Audi’s new in-house 3D printing setup facilitated by the full 3devo’s solution allows for excess plastic to be reused and made into new parts and tools assisting in onsite manufacturing. - A Step Closer to their Mission:Zero Goal
Within just a few months, Audi’s A7 and A6 models have components that have been put together with the recycled plastic 3D printed tools. - Reducing Carbon Footprint and Production Costs
With their new circular process, not only is Audi leading the way for other car manufacturers to reuse what they already have and reduce their carbon footprint, but now the cost of production has reduced due to not having to purchase additional tools! Saving resources that can be used to further Mission:Zero.
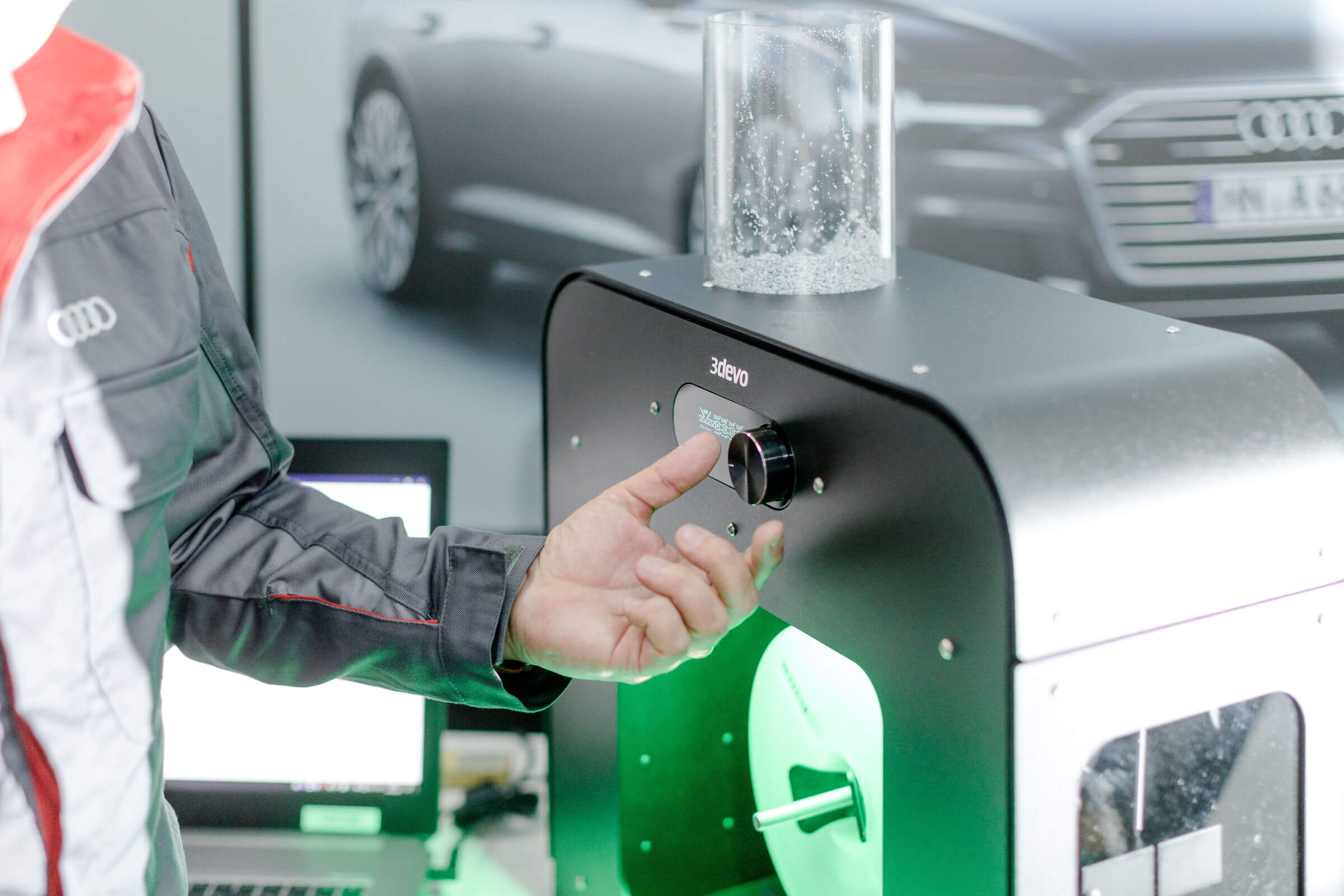
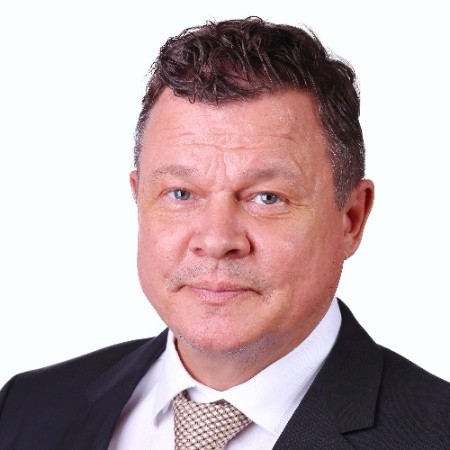
More Success Stories
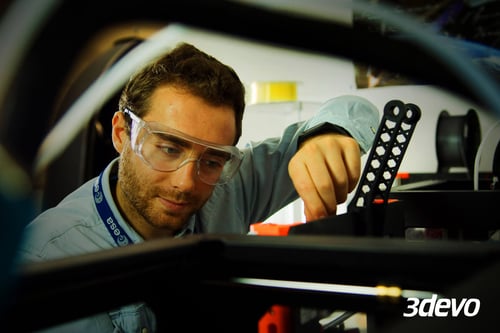
European Space Agency
How do researchers at ESA have the freedom to innovate – without wasting resources in the process.
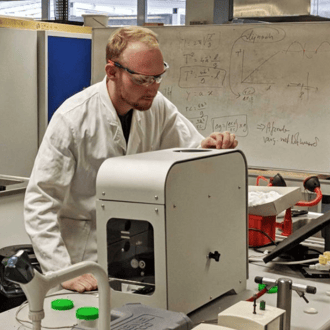
Fontys University
How Fontys gained the ability to expand their polymer development studies – at a fraction of the cost.
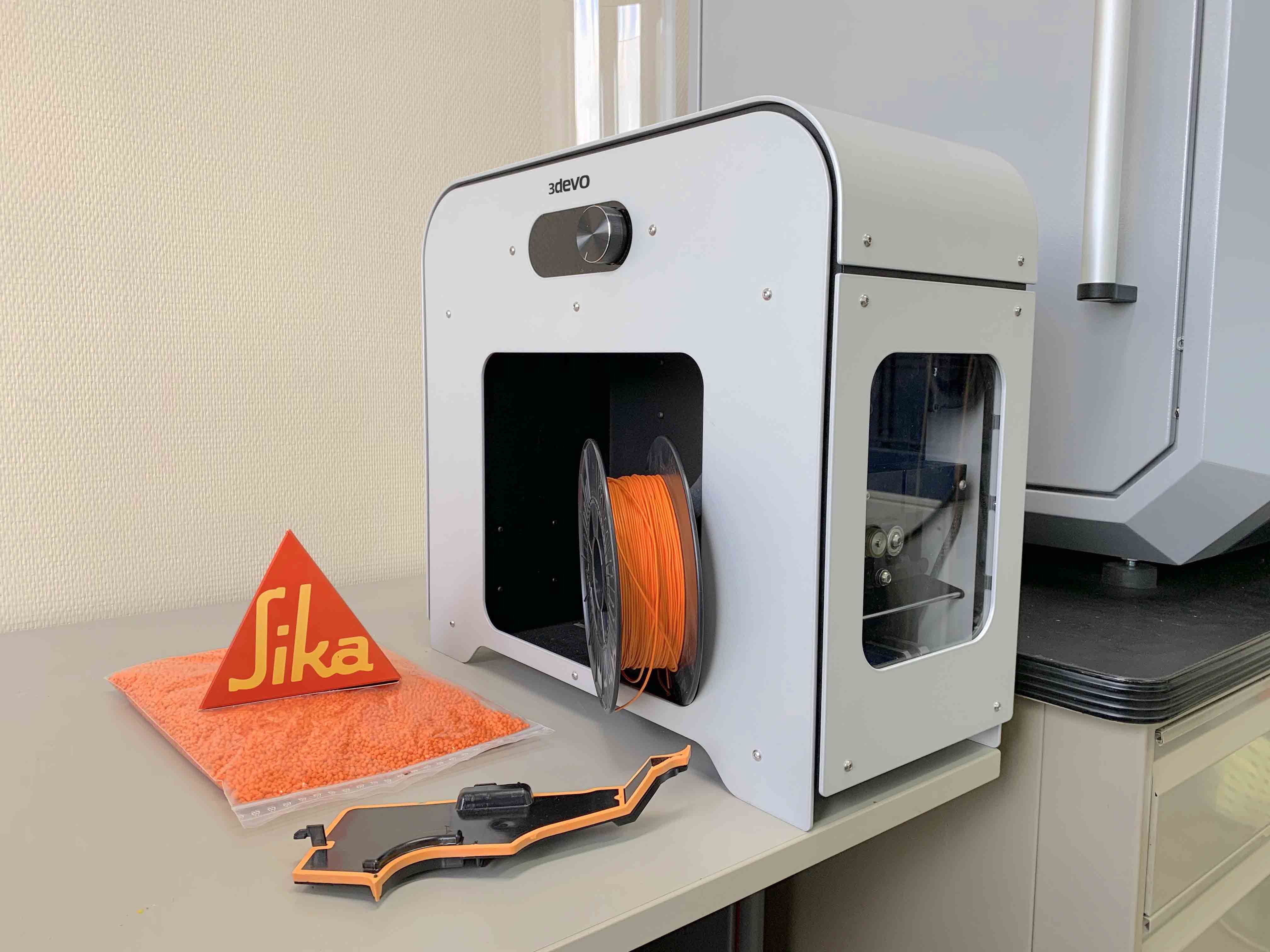
Sika Automotive
How Sika Automotive managed to reduce their production time – for their cavity sealers -from weeks to days.