Share this
MFI Testing: A key validation step for novel filament extrusion
by Ellie Pritchard on Mar 18, 2024 10:48:16 AM
At 3devo, we understand the critical role that a comprehensive understanding of material properties plays in the success of your filament extrusion projects. That's why we emphasize the importance of the Melt Flow Index (MFI) test as part of our Validation Step - a simple yet powerful tool that can significantly enhance the quality and reliability of your 3D printing materials. Here, we’ll explain the MFI testing process, its benefits, and why it's a game-changer for our customers.
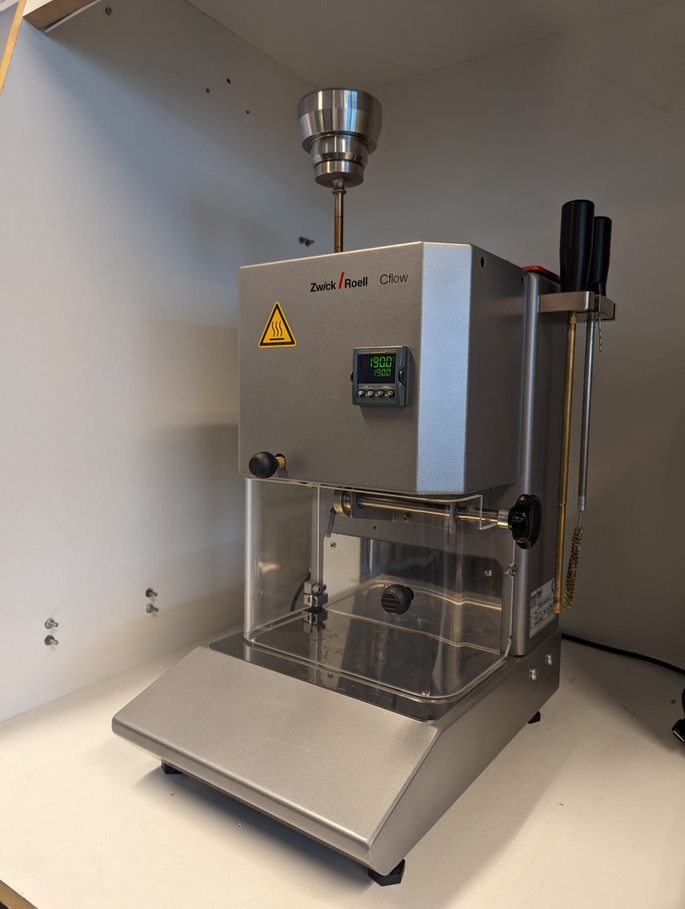
A powerful tool
Selecting the appropriate polymer for your application requires understanding the various grades available, as each grade represents a specific version of a polymer type by a particular manufacturer. For instance, PLA encompasses hundreds of unique grades, each with its own technical data sheet to assist in filament manufacturing for 3D printing. These grades can be categorized based on their flow behavior when molten, which is quantified by a key viscosity indicator known as the Melt Flow Index (MFI), measured in grams per 10 minutes.
The MFI value represents how easily the plastic flows when it is in a molten state, under specific conditions of temperature and pressure. The result indicates the material's viscosity, with a higher MFI indicating lower viscosity and thus a more fluid melt. MFI testing is crucial for determining the suitability of a plastic material for specific manufacturing processes, such as injection molding or extrusion, and for ensuring consistency and quality of the filament.
The testing process
Our 3devo lab is equipped with MFI testing apparatus, meaning we are able to test your materials in-house. As part of our Validation Step, we invite you to send a small sample (between 300-500g) to us and your dedicated Materials Specialist will conduct an MFI test, providing clarity on the likelihood of a successful filament extrusion for your project.
To begin, a small amount of the polymer sample is placed into the pre-heated barrel of the machine to then be extruded through a 2mm die. A piston is inserted to drive the material through the die in a controlled way. As the polymer begins to flow through the die, a sample of the extrudate is collected at predetermined time stamps – the MFI is calculated based on the weight of the polymer that has flowed through the die in a specific time frame. This value gives a direct indication of the material's flow characteristics.
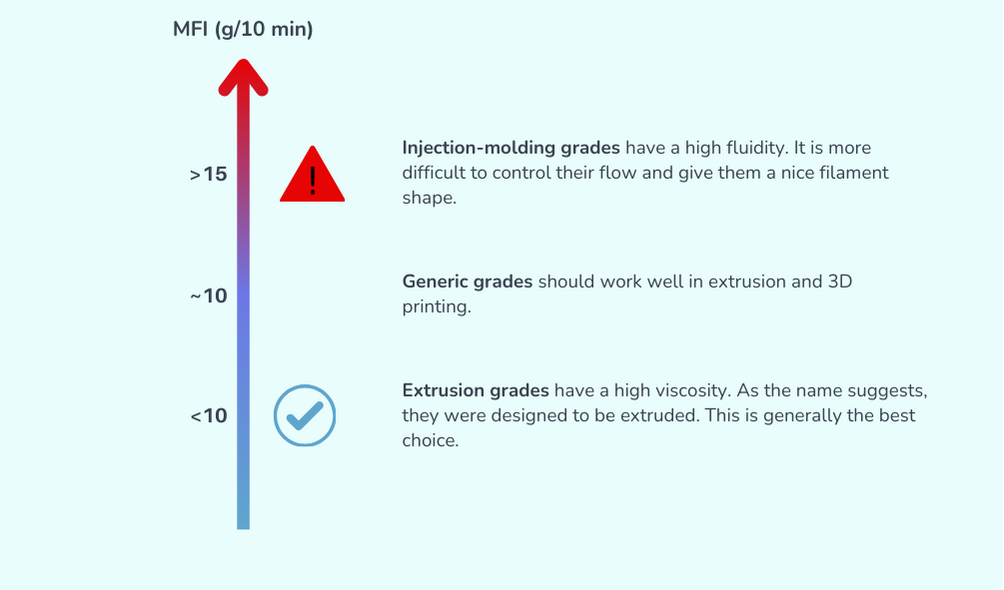
Why is MFI testing important?
MFI testing clarifies a material’s consistency and quality, critical for producing predictable and high-quality prints. By facilitating the optimization of extrusion parameters—temperature, pressure, and speed—MFI testing enables the production of filaments with precise diameter and roundness, essential for optimal print quality. Additionally, it helps in the selection of materials tailored for specific applications, where different flow properties may be required to achieve the best results. The outcomes of MFI testing offer a strong indicator of a material's extrusion viability, equipping our Materials Specialists with the insights needed to accurately assess and advise on the feasibility of your project. With this small commitment, you gain access to a valuable evaluation, a smart but low-risk investment that clarifies the path forward, enabling us to gauge the compatibility of your material with our filament extrusion process confidently.
The compatibility of filaments with a broad range of 3D printers relies on accurate MFI values, ensuring smooth extrusion and consistent layer adhesion, reducing the risk of printer jams. Understanding a filament’s MFI also allows for the prediction of its behavior during printing, such as melting, extruding, and cooling dynamics. As a part of quality control, regular MFI testing guarantees that each filament batch adheres to stringent specifications, maintaining high product quality over time and instilling confidence in users regarding the performance of their purchased filaments. In essence, MFI testing underpins the entire filament production process, from material selection and process optimization to ensuring the success and reliability of 3D printing projects, making it an indispensable tool for manufacturers and users alike.
In essence, MFI testing is not merely a procedural step; it is a strategic tool that enhances our ability to serve you better, ensuring that each project is approached with precision, expertise, and a clear vision for success. It embodies our commitment to fostering innovation and delivering quality, underpinning the trust and reliability we strive to build with every customer.
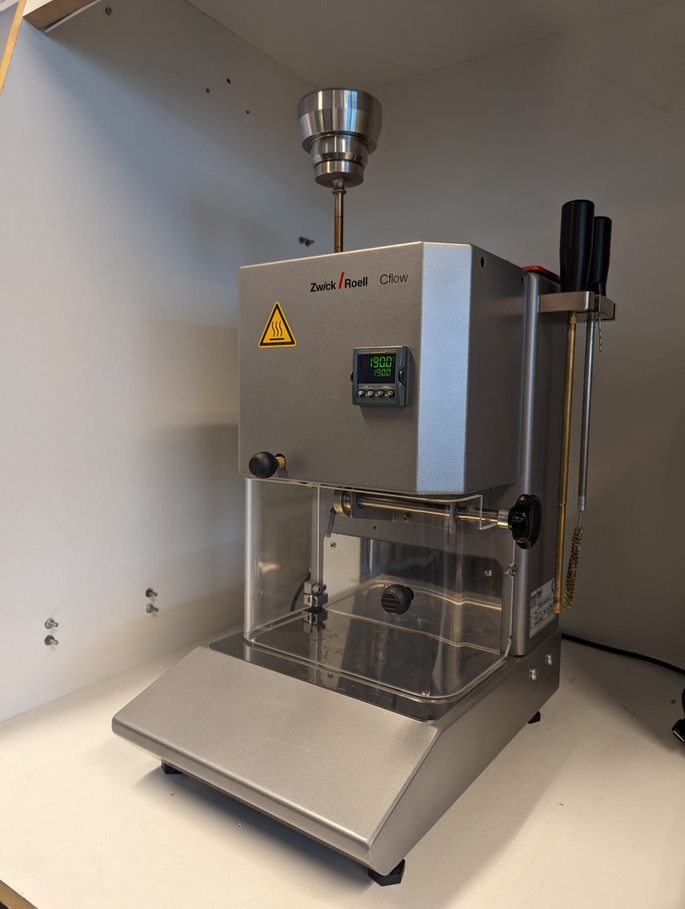
At the forefront of development
At 3devo, we are striving to enable 1 million innovations by 2032 and we carry this intention with us in every aspect of our partnership. By providing a clear, quantifiable measure of a polymer's flow characteristics, MFI testing is a demonstrable part of this intention. Our Materials Specialists can explore new polymer blends, fillers, or additives, and immediately assess how these innovations affect the material's processability and performance. This fosters a more experimental and forward-thinking approach to developing next-generation materials.
Developing new materials often involves iterative cycles of formulation adjustments, testing, and analysis. MFI testing plays a pivotal role in this process by providing immediate feedback on how changes in polymer composition or additives affect the material's flow properties. This enables developers to methodically adjust their formulations to home in on the desired performance metrics, such as improving ease of processing, mechanical properties, or thermal stability. The ultimate goal in material development is to balance performance characteristics with processability. A material may have excellent mechanical properties but if it's too difficult to process because of its flow properties, it's not practical. MFI testing helps in finding that balance, ensuring that the developed material not only meets the application's performance requirements but is also manufacturable on a practical scale.
Through the lens of MFI testing, we can swiftly evaluate the impact of new polymer blends, fillers, or additives on a material's processability and performance. This capability not only accelerates the material development process but also cultivates an environment ripe for experimentation and innovation. It allows us to push the boundaries of what's possible, paving the way for the creation of next-generation materials that meet the evolving needs of industries and consumers alike.
The journey of developing these innovative materials is marked by iterative cycles of formulation adjustments, bolstered by the immediate and insightful feedback provided by MFI testing. This iterative process is crucial, enabling our developers to finely tune the compositions to achieve optimal flow properties, mechanical strength, and thermal stability.
Balancing the dual demands of performance characteristics and processability is at the heart of material development. A material's mechanical properties might be outstanding, but if its flow properties render it impractical to process, its potential remains untapped. MFI testing shines here as well, helping us strike that delicate balance. It ensures that the materials we develop not only meet the stringent performance requirements of their intended applications but are also feasible to manufacture at scale.
In this way, MFI testing is more than just a measure; it's a bridge between the innovative aspirations of 3devo and the practical realities of material science. It empowers us to fulfill our promise of enabling innovation, providing the tools and insights necessary to transform visionary ideas into tangible, manufacturable materials.
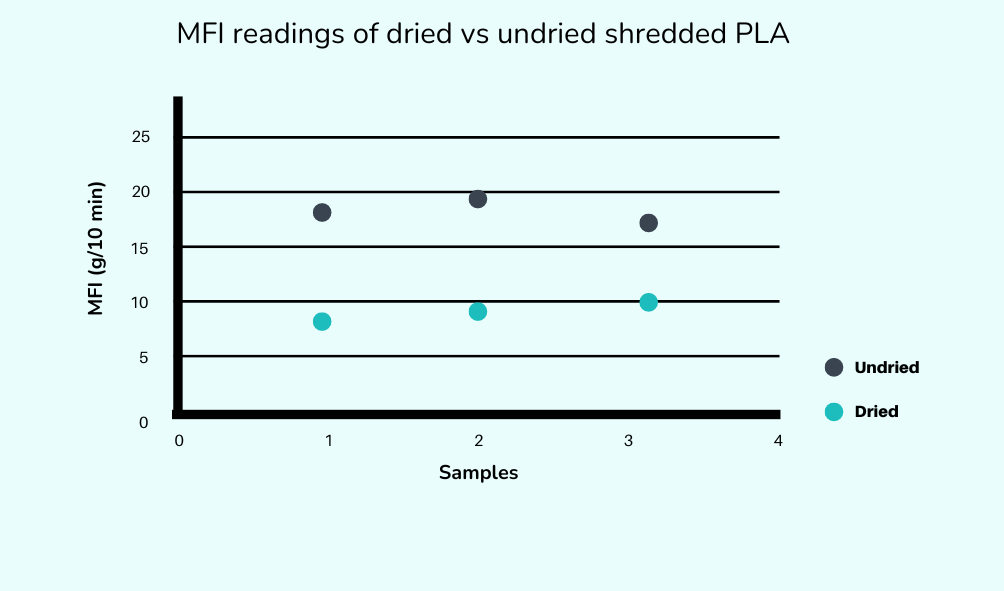
Quality assurance
The use of MFI testing as a quality assurance tool is extremely valuable because it provides a detailed understanding of a polymer's flow properties. This detailed insight is crucial, allowing us to create materials with a known quality, not only in theory but also in practice. Through this careful examination, we can test that each filament produced meets our customers’ standards for reliability and performance.
MFI testing plays a key role in enhancing the reliability of 3D printed projects by guaranteeing the consistency of materials. This consistency is essential for achieving prints that are both predictable and repeatable. By ensuring that the materials used have been thoroughly tested for their flow properties, we can expect more uniform results from one print to the next, reducing the likelihood of errors and increasing the overall success rate of 3D printing endeavors.
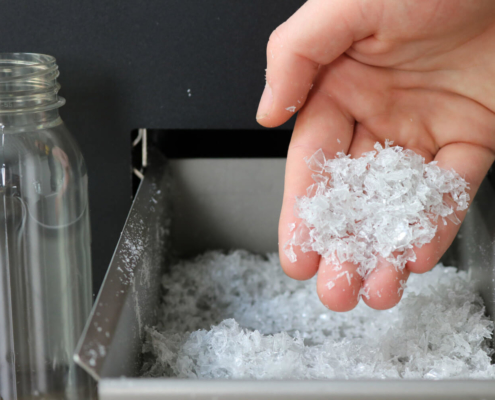
Hear from our Materials Specialist
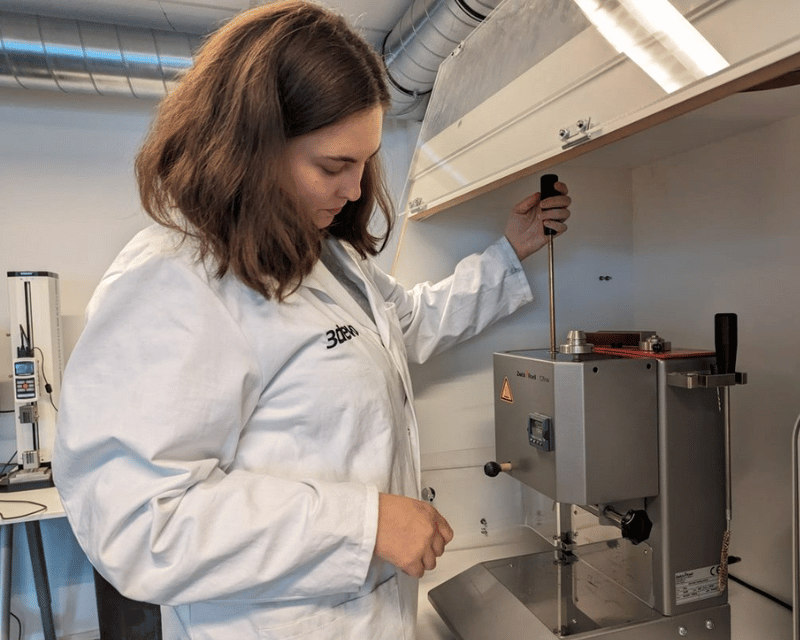
The MFI tests are conducted by our experienced team of Materials Specialists. Here is what Leah Brew has to say about it!
As a Material Specialist at 3devo, my main goal is to guide the customers through their projects with the aim of generating high quality filament for their downstream applications. To do this, I rely on lab experimentation to determine the suitability of a material for further testing.
The MFI test is one of the first steps in understanding if the material can move forward to testing in our extruder. The results tell me if the material is within a window of viscosity that can produce filament but it also allows me to get a loose sense of the sensitivity of the material to heat – I can understand whether it melts quickly and extrudes material readily, or whether it requires a longer residence time in the barrel to reach its melting temperature. I make sure to note these subjective measurements to help with further testing in the extruder. Once the MFI is complete – I also have several extrudate samples – again, I can get a sense of the homogeneity of the sample, a visual indication of the melt behavior/consistency. These observations help me narrow down the range of parameters I need to test once I use the material in the extruder. Sometimes, the MFI also indicates when a material is completely unsuitable for further testing – if a material simply doesn’t melt, this will become apparent during the MFI. I like this approach as it ensures that customers are exposed to the minimal level of risk at each step.
Our MFI instrument is called the Zwick Roell C Flow and it’s a compact but impressive instrument! I like it because the manufacturers of this instrument have thought of everything – there are several types of cleaning tools, sturdy tampers and a cute little funnel that allows me to feed the test material easily. I adjust the temperature using a PID controller and I can monitor the progress of the extrusion of molten plastic through the mirrored panels in the collection chamber.
After I’ve completed the MFI testing, I convert my observations into a report to share with the customer. I find that this report is an excellent basis for discussions with customers, as they have the chances to review and interpret the experimental outcomes before coming to a decision about the next steps.
Conclusion
In the dynamic realm of 3D printing, understanding and optimizing filament extrusion quality is paramount for success, and Melt Flow Index (MFI) testing emerges as a key player in this process. We hope to have highlighted the significance of MFI testing, showcasing it as more than a mere step in material validation but as a cornerstone of innovation and quality assurance in filament production. Through MFI testing, 3devo underscores its commitment to precision, enabling customers to confidently navigate material selection and optimization, thereby enhancing the reliability and performance of 3D printed projects.
As we advance, MFI testing not only serves as a gatekeeper of quality but also as an enabler of material innovation, offering a lens through which the potential of new polymers can be assessed and refined. It bridges the gap between conceptual innovations and their practical application, ensuring materials not only meet performance criteria but are also viable for production. In embracing MFI testing, 3devo invites partners and customers alike to join in forging the future of 3D printing, where every filament extrusion is a step towards new possibilities in manufacturing and design.
Share this
- March 2025 (1)
- January 2025 (1)
- December 2024 (2)
- November 2024 (3)
- October 2024 (4)
- September 2024 (2)
- August 2024 (3)
- July 2024 (6)
- June 2024 (3)
- May 2024 (2)
- April 2024 (1)
- March 2024 (1)
- January 2024 (1)
- November 2023 (2)
- October 2023 (5)
- September 2023 (2)
- August 2023 (1)
- July 2023 (1)
- May 2023 (1)
- December 2022 (3)
- August 2022 (1)
- June 2022 (1)
- May 2022 (2)
- April 2022 (2)
- March 2022 (7)
- February 2022 (2)
- January 2022 (3)
- December 2021 (3)
- November 2021 (3)
- October 2021 (2)
- September 2021 (3)
- August 2021 (3)
- July 2021 (2)
- June 2021 (1)
- March 2021 (1)
- October 2020 (1)
- June 2020 (1)
- May 2020 (1)
- April 2020 (4)
- November 2019 (1)
- July 2019 (2)
- June 2019 (1)
- May 2019 (1)
- March 2019 (1)
- November 2018 (1)
- September 2018 (1)
- January 2018 (1)
- October 2017 (1)
- September 2017 (1)
- July 2017 (1)
- June 2017 (1)
- May 2017 (1)
- January 2017 (1)
- December 2016 (3)
- November 2016 (2)
- October 2016 (1)
- May 2016 (2)
- August 2015 (2)
- July 2015 (1)