Share this
Filament Extrusion: A Beginner's Guide to Mastering Extrusion
by Benjámin Beregszászi on Jul 4, 2024 10:30:00 AM
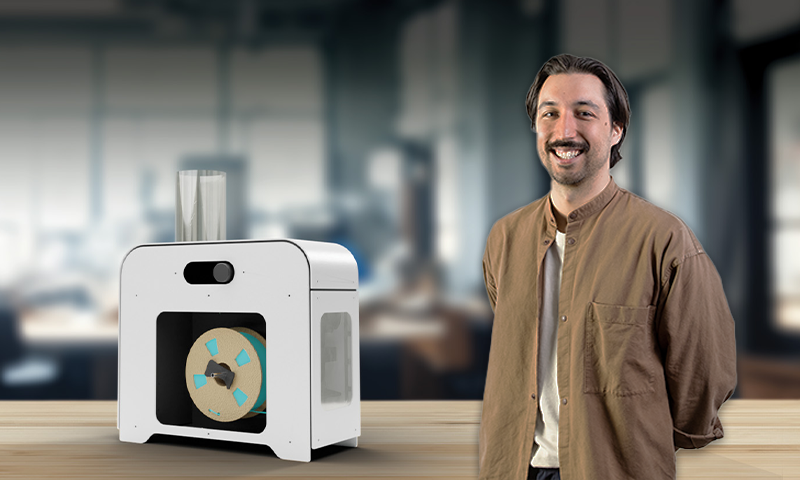
Ben is one of our Customer Support Agents at 3devo. He specializes in solving materials issues, refining Service content, and identifying knowledge acquisition for users. In this blog, Ben offers his perspective on approaching the world of filament making from a non-technical background. Drawing from his own experience and that of his colleagues, Ben explains the successes, challenges, and learning opportunities that come with use of our Filament Makers ONE and TWO.
Personal Experiences, Unique Insights
There are very few 3devo staff members who have not worked on the machine at one point or another. Our in-house fleet of Filament Makers are regularly used for testing, research, troubleshooting, trainings, and if there's a bit of a gap in our schedule, for fun experiments, too. What is surprising is that everyone has their own insight into the extrusion process and understanding of the Filament Maker ONE.
When colleagues were briefly quizzed on their opinions of the machine, the variety of answers provided was unexpected. To some, the beauty of the machine lies in its compactness, in its simple dedication to melt, extrude, and spool material all in a single desktop machine. For others, it is the Filament Maker’s versatility and flexibility that is most prized. When the collection of answers differ, they offer exciting new angles to the machine, and when the answers align, they reinforce its most cherished qualities. Here’s my favorite example:
"What is one thing that most people overlook or underestimate about the Filament Maker ONE?"
→ "It’s not that difficult, you don’t have to be an engineer."
As someone who is relatively new to the 3D printing industry, and is not an engineer, this answer resonated with me. In hopes of encouraging others like me, I’d like to share some of my colleagues’ insights and my personal experience entering the world of filament making.
Everyone’s Context is Different
3D printing is a vast field, and filament making in itself is still only a burgeoning niche. This makes it all the more exciting and boundary-pushing. At 3devo we strive to put as much information and educational content out there as possible to aid customers and, in my case, beginner users. My roles and responsibilities at 3devo go beyond a mere title. As Customer Support Agent, the most important skill I need to have is understanding and empathizing with users and their issues. This means consistency and honesty in our communication.
It is important to note, however, that we have clients all over the world and from industries small and large, public institutions and private companies, engineering experts and material science students. The range is wide and the challenge of providing the right information for every individual is formidable. On top of this, we need to consider that everyone's personality and goal for their experiment is different. What data they collect, what research they carry out before and after, what results they need to achieve, is all pertinent. Our new business model underpins this approach, taking a client's context into consideration and meeting them where they are at. It is about providing the best support possible that aims to help users move past roadblocks that might limit their progress and innovations.
This is arguably most interesting when the discussion is about the methodology and the approach to extrusion. I regularly refine content, visualize concepts, and restructure our knowledge database to provide an organic learning process. This knowledge acquisition comes in stages, and it is something I had to learn for myself through practice.
/SP%20Extrusion%20Essentials-minCOMP.png?width=1164&height=711&name=SP%20Extrusion%20Essentials-minCOMP.png)
Successes
"What was the most surprising or unexpected aspect of the FM ONE (when first used)?"
→ "Feels a bit like magic. Coarse (shredded) material goes in and smooth filament comes out."
When I first used the Filament Maker ONE, I had no idea what I was doing. As a person involved in Communications and Humanities for the better part of my career, it was daunting to even consider operating a high-tech machine. My extent of practical resources rarely extended beyond pen and paper, so I was introduced to the compact machine with some trepidation. Though I was assured that I don't need a degree in engineering or extensive material science background to be able to create filament with the FM ONE, I was skeptical. Curious and excited, sure, but also skeptical.
When faced with anything new, I turn to research. Scouring through the Support Platform articles, I outlined my approach, read up on possible issues I might encounter, and hoped for the best while being prepared for the worst. I then had available knowledge articles as my aid, and our Materials Specialist Timo van der Laak as my guide, though he was (worryingly) happy to leave me alone with the machine.
However, after hours of research and planning, I still had to turn the machine on. To its benefit, the FM ONE was and still is inviting in its sleek simplicity. It was immediately intuitive to use. The features, the interface - the machine as a whole is almost deceptively simple in its presentation. Except it wasn’t deceptive, as I had no issue achieving the baseline 1.75mm PLA filament. My first extrusion was a success, as was the second and the third. Then I was introduced to TPU.
"What has been your worst experience with extrusion or with a material?"
→ "I extruded surprisingly good filament. I mean, I need things to go wrong, so I can learn."
/TPU%20Extrusion%20Run%20set%20up-minCOMP.jpeg?width=4032&height=3024&name=TPU%20Extrusion%20Run%20set%20up-minCOMP.jpeg)
Challenges
For me, extruding TPU proved too elastic to turn into filament in a single 5-hour session. It wasn’t until later that I found out that the grade of TPU I had been using actually had a significantly lower shore hardness than what we recommend. This grade is not validated on our machine and its shore hardness is far from ideal for single screw extrusion. It was not the first mistake I would make, but each extrusion provided more and more data for me to succeed in my endeavors.
"What has been your worst experience with extrusion or with a material?"
→ (from multiple colleagues) "PEEK clogging the nozzle, molten PLA spurting, I transitioned to HighTemp too soon, HDPE cooling, shredded rPET melting too early."
Knowing what can go wrong, and how to rectify it when it does, is a cornerstone of the Customer Success Team. Each of these mentioned extrusions are experiences our 3devo staff went through. Now they are useful points of reference and data to study so that we can help our customers, update our knowledge content, and re-design our machines.
"What was the most surprising or unexpected aspect of the FM ONE (when first used)?"
→ "As a new user, I got advice and tips from one of our Material Specialists. It wasn’t until much later that those warnings sunk in."
After repeatedly scraping off the molten TPU with its honey-like sticky consistency, I realized that the machine was still extruding without an issue. It did not malfunction. After a thorough purge, it was clean and extruding, with consistent pressure visible on DevoVision, no mysterious spikes on the datalog, and no error messages. It was then necessary for me to fully understand how to utilize this machine and understand the process inside out.
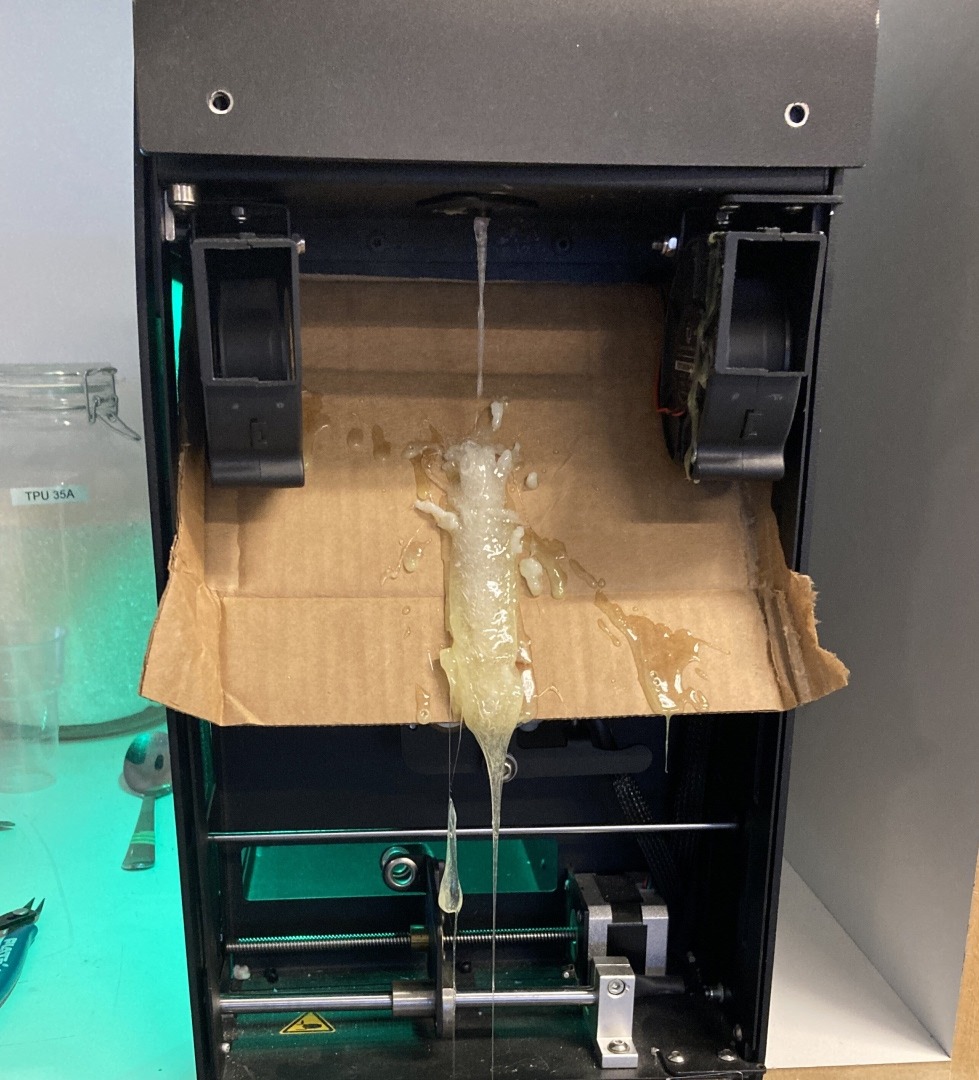
As with everything, using the FM ONE comes with its own learning curve. Things work very fast and very well, until suddenly they don't. This is the moment where research, planning, and refining one's approach is most crucial. Clearly, I had a lot to learn.
Learning Curve
Even within our small and specialized company, our machines are constantly put to the test. Our Material Specialists, Production Staff, Service staff, even our Marketing Team – we all use the machines on a regular basis. Material validations, purging procedures, MFI tests, and customer trainings, too.
In fact, every 3devo staff member has their own preferences of extrusion approach. There are colleagues who prefer to carry out an extrusion run by themselves while others collectively discuss and make decisions on the go, benefiting from the live feedback given by differing viewpoints. Some are overthinkers, some are planners, some trial-and-error enthusiasts, and some just improvise on the spot. Though I have my preference, there is no wrong approach if: the user understands the machine, the methodology is sound, and the data is systematically analyzed.
"What is one thing that most people overlook or underestimate about the Filament Maker ONE?"
→ (from multiple colleagues) "Importance of Purging, importance of Transitioning time, DevoVision, DevoVision, DevoVision…"
As the answers point out, it is difficult to underestimate the value of DevoVision. Though a simple platform with a somewhat limited interface, it is still one of the best tools for learning about any single extrusion run. The data collected from the Filament Maker process settings is visualized live in graphs, helping users gain an insight into what is happening inside the machine. It is especially useful when comparing data sets with one another. For example, the drop in Motor Current corresponding with high Heater settings (for the processing material) might indicate low pressure. Or the difference between how a Puller Wheel set on manual affects the Filament Thickness as opposed to a Puller Wheel set on automatic.
In my role, I rarely encounter a Service case where a datalog is not essential to understanding a customer’s journey. It is that important. Throughout my time at 3devo, I have collected dozens of datalogs that showcase examples of extrusions going extremely well and horribly wrong, too. Recognizing patterns is a key way of not just diagnosing mistakes once they have happened, but more significantly identifying and predicting changes in the extrusion. Then the user is equipped with the tools and knowledge to act on it during the experiment, minimizing processing time and avoiding annoying delays, or worse: repairs.
It is then even more exciting when considering the type of increased data analysis that we are developing for the next iteration of the Filament Maker.
The following screenshots have been taken from DevoVision readings during filament extrusion:
/H1%20vs%20H2%20Heating-min%20COMP.png?width=1186&height=732&name=H1%20vs%20H2%20Heating-min%20COMP.png)
/Oscillating%20MC%20plus%20RPM-minCOMP.png?width=677&height=831&name=Oscillating%20MC%20plus%20RPM-minCOMP.png)
/PP%20overworking%20pullers%20PW_FT-minCOMP.png?width=1702&height=894&name=PP%20overworking%20pullers%20PW_FT-minCOMP.png)
Looking Forward
We have a stable history of continuously updating and refining our products. The Filament Maker ONE has been through various iterations, which included a new chassis frame, better nozzle design, as well as continuous software updates. It has definitely come a long way from the initial cardboard and toy brick set up that was once our CEO's passion project. However, there is only so much we can add on to an existing product. So instead, we made an improved one.
"What is the most exciting change from the Filament Maker ONE to the Filament Maker TWO?"
→ (from multiple colleagues) "Added Hopper cooling (to avoid early melting), more powerful motor (gives more range), updated data analysis (huge potential), screw removal (more user friendly), advanced sensor, newly designed UI…"
Needless to say, 3devo staff and myself included are excited for the release of the FM TWO, and the possibilities it will open up. Of course, the inviting and sleek design stays similar with a more stable foundation and accessible system of panels. The new and advanced features are exciting and just like the ONE, this next generation of FM TWOs are designed to keep evolving and growing with the clients and partner's feedback and input, too. This detail alone makes it a worthy successor to the much loved ONE series.
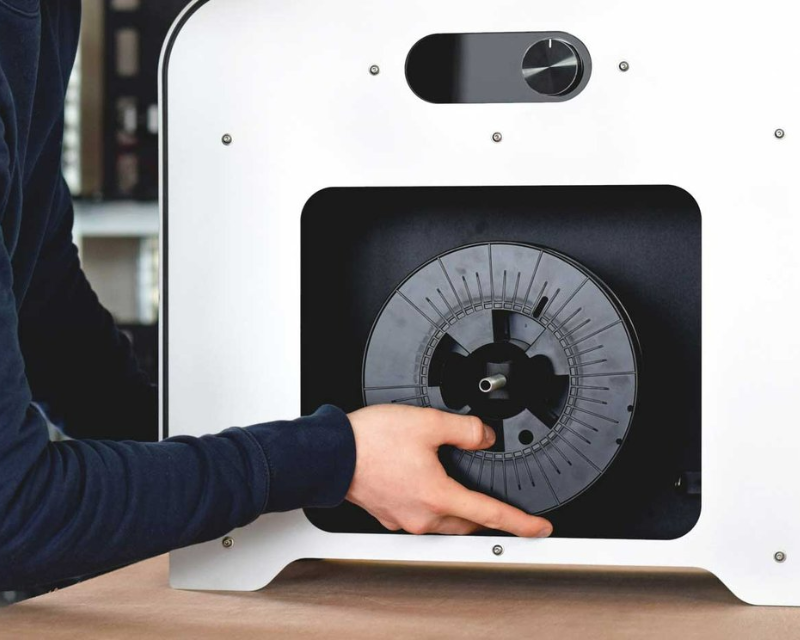
Conclusion
Since its humble beginnings the FM was simply known as ‘the’ Filament Maker. It has only recently been dubbed the ‘ONE’, considering the much-anticipated arrival of its bigger and shinier sibling. However, the Filament Maker still remains the first, the original, and the standard from which all future iterations will evolve.
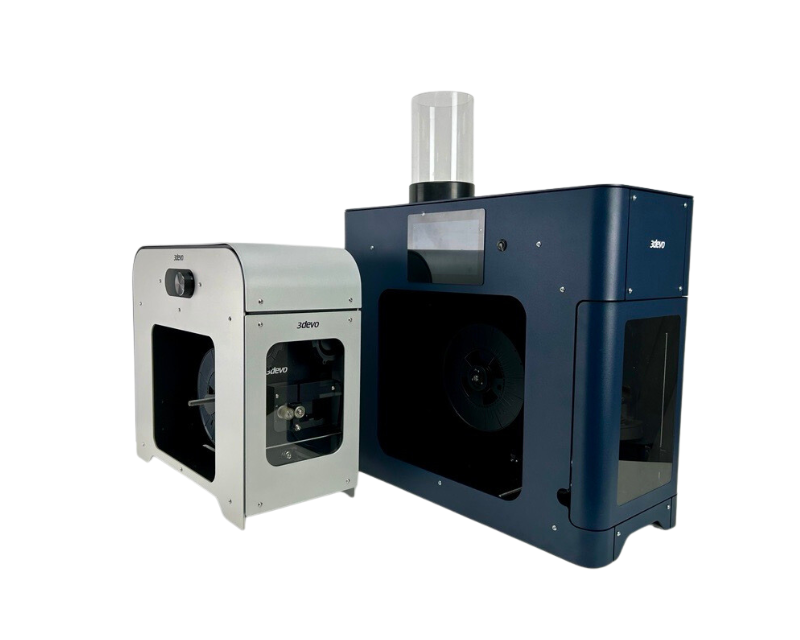
Frequently Asked Questions (FAQs)
DevoVision is an essential tool used in the filament extrusion process. The desktop platform provides live data visualization of the extrusion process, allowing users to monitor key parameters such as temperature, pressure, and motor current in real time. This data helps users understand what is happening inside the machine, diagnose issues, and optimize their extrusion settings for better filament quality. By comparing different data sets, users can identify patterns and make informed adjustments to improve their extrusion runs.
The Filament Maker TWO introduces several key improvements, such as:
- Hopper Cooling: This helps prevent premature melting of the feedstock, ensuring a smoother extrusion process.
- More Powerful Motor: The upgraded motor provides a wider range of extrusion capabilities, allowing for more diverse materials and higher precision.
- Updated Data Analysis: Improved data analysis tools offer greater insights into the extrusion process, aiding in better quality control and troubleshooting.
- Screw Removal: This new design makes maintenance and cleaning easier and more user-friendly.
- Advanced Sensors: Enhanced sensors provide more accurate monitoring of the extrusion process, including filament ovality.
- Newly Designed UI: A redesigned user interface makes the machine easier to operate and navigate, improving the overall user experience.
The new business model at 3devo is designed to offer more personalized support by considering the unique context and needs of each customer and project. This approach involves:
- Tailored Information: Providing customized educational content and support based on the user's specific situation, whether they are from a large corporation or an individual researcher.
- Empathy and Understanding: Emphasizing consistent and honest communication to better understand and address user issues.
- Comprehensive Support: Offering a holistic approach to customer service that includes troubleshooting, training, and ongoing assistance to help users overcome roadblocks and achieve their goals.
To successfully extrude filament using the Filament Maker ONE, we recommend users to consider the following:
- Understanding the Machine: Familiarize yourself with the machine's features and interface, and explore our Support Page.
- Proper Materials: Pay special attention to material grades and ensure they are compatible with the machine's specifications.
- Temperature Control: Set the correct temperatures for the heater and the extrusion process to avoid issues like clogging or inconsistent filament.
- Purging Procedures: Regularly purge the machine to maintain cleanliness and prevent contamination of different materials.
- Data Monitoring: Utilize DevoVision to monitor the extrusion process in real time and make necessary adjustments based on the data. This is also very useful to provide to our Service Agents when they assist you.
- Experimentation and Learning: Be prepared to experiment with different settings and learn from each extrusion run to improve your technique and filament quality over time.
Share this
- March 2025 (1)
- January 2025 (1)
- December 2024 (2)
- November 2024 (3)
- October 2024 (4)
- September 2024 (2)
- August 2024 (3)
- July 2024 (6)
- June 2024 (3)
- May 2024 (2)
- April 2024 (1)
- March 2024 (1)
- January 2024 (1)
- November 2023 (2)
- October 2023 (5)
- September 2023 (2)
- August 2023 (1)
- July 2023 (1)
- May 2023 (1)
- December 2022 (3)
- August 2022 (1)
- June 2022 (1)
- May 2022 (2)
- April 2022 (2)
- March 2022 (7)
- February 2022 (2)
- January 2022 (3)
- December 2021 (3)
- November 2021 (3)
- October 2021 (2)
- September 2021 (3)
- August 2021 (3)
- July 2021 (2)
- June 2021 (1)
- March 2021 (1)
- October 2020 (1)
- June 2020 (1)
- May 2020 (1)
- April 2020 (4)
- November 2019 (1)
- July 2019 (2)
- June 2019 (1)
- May 2019 (1)
- March 2019 (1)
- November 2018 (1)
- September 2018 (1)
- January 2018 (1)
- October 2017 (1)
- September 2017 (1)
- July 2017 (1)
- June 2017 (1)
- May 2017 (1)
- January 2017 (1)
- December 2016 (3)
- November 2016 (2)
- October 2016 (1)
- May 2016 (2)
- August 2015 (2)
- July 2015 (1)