Share this
How our New Filament Sensor Improves 3D Printing Accuracy
by Janus Barnard on Aug 5, 2024 10:09:51 AM
Having been active in the 3D printing and filament making game since 2016, we know that in order to print successfully you need to be as accurate and precise as possible. Implementing updated features into our filament-making solutions, such as an enhanced filament sensor, can help ensure the quality of prints is high, creates the opportunity for fast innovations and, most importantly, it prevents frustrations.
Customer-Driven Innovation
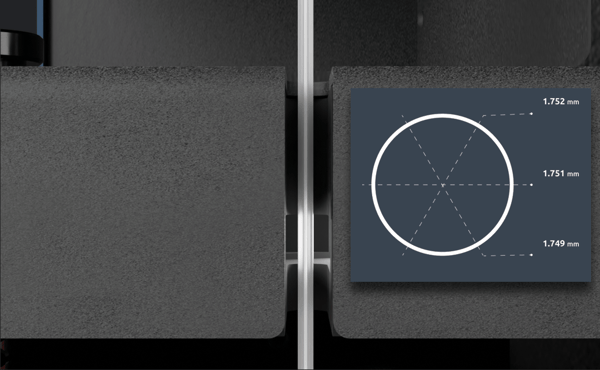
Indeed, the pursuit of perfection is a never-ending task, which is why we are always chasing continuous development, keeping an open mind towards further developing our products. And who can serve better in helping us achieve this goal than the people with the most hands-on experience with filament makers, our clients. Customer experiences and development suggestions are the driving force behind our new Co-Creation projects with our clients.
One of the latest examples of this is our new Filament Sensor TWO which we developed as a direct result of our clients’ input and demand. It is one of the main new features of the Filament Maker TWO launching later this year, and was initially designed to have a greater resolution and the ability to identify filament ovality. However, the innovation didn’t stop there; we decided to further expand on extra features, such as a thermal sensor for non-contact temperature sensing and error capturing. The new Filament Sensor TWO (FS2) can be seen as the eyes of the Filament Maker – it ensures that the extrusion process is strictly monitored, and that early detection can mitigate behavioral changes.
New Extruder Filament Sensor Features
With regards to accuracy and precision, the industry standard of filament making is to have a continuous diameter of (typically) 1.75 mm or 2.85 mm, with a maximum error of 0.05 mm. Most of the industry has become accustomed to these dimensions - the majority of printers have optimized their processes according to these tolerances. The Filament Sensor ONE (FS1) operates on this limit with a resolution of roughly 50-microns, which is exactly on the error margin of the industry standard, but with interpolating and averaging we received acceptable results. The new sensor that we have developed operates at 25 measurements per second and has a resolution precision of up to 10-micron, which means that we are now capturing errors within the 50-micron range, ultimately allowing for much better control of the system.
Let’s put it into a scenario: It’s like having blurry vision while playing darts. You throw a dart, and it hits the board. You adjust your aim a little and it still hits the board. You therefore now have 2 different pairs of settings each with the same result. Now if you put on glasses and you throw again you can see your score. Adjust one of your throwing settings and you can now see how the score changes. This is the same effect you could expect from using a high resolution sensor.
In the image below where it shows the filament diameter measurements of the old generation sensor vs FS2 for the same filament, the diameter fluctuations are much lower on the FS2 due to the higher resolution. It therefore gives a more accurate representation of the filament diameter. Additionally, the red arrow indicates where a parameter has been changed on the instrument. On the FS2, the resulting effect of changing the parameter is far clearer due to the higher resolution. In this case, it can be seen that the parameter change caused a dip in the filament diameter which is typically due to a change in extrusion speed, temperature or puller speed.
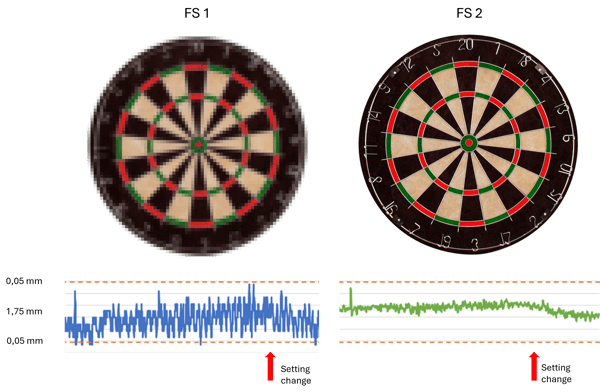
-
Ovality
The sensor also makes use of a 3-axis sensing area, which means that it can effectively measure the filament diameter from 3 directions and thus calculate the ovality percentage. Ovality can occur when highly crystalline material cools at different rates due to inefficient fan cooling. Some materials like PP and HDPE are highly crystalline and tend to crystallize directionally when cooling is non-uniformly dispersed over the filament. This directional crystallization can lead to directional crimping and therefore warp your filament into an oval shape.
Oval or flat filament creates all sorts of trouble when the printing starts, and the early detection of this can prevent various headaches down the line. This makes cooling precision a highly important factor and keeping a close eye on it is crucial. More on this topic can be found here.

-
Real Time Images
The third and final improvement is the ability of the sensor to capture and log real time images using the Filament Maker TWO’s onboard computer. This feature can be used to capture and record any error that it has been instructed to monitor. These errors can then later be traced back to the filament spool, evaluated, and removed if deemed necessary by the user. These errors can include anything such as filament thickness, ovality, contamination (as seen in the figure below) or even temperature anomalies.
-
Optical Heat Sensor
Due to each material having varying thermal properties, an optical heat sensor is incorporated into the sensor to monitor the filament temperature before it reaches the puller wheels. This is important as the material can be deformed by the puller wheels if it is still too hot and malleable when it reaches them. The heaters and cooling fans can now be tuned to perfection to make sure that the filament is not deformed before winding. The figure shows the temperature profile of a filament being tracked by the sensor.
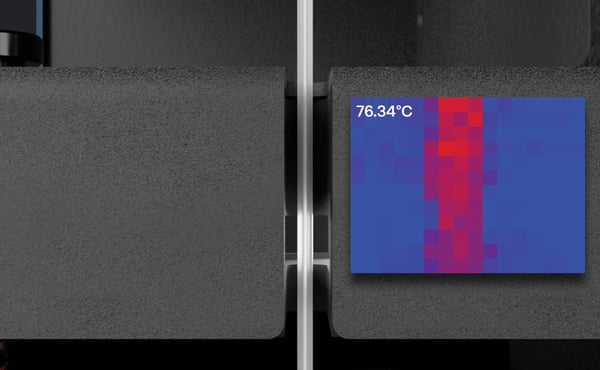
How the New Filament Sensor Helps You
Having this improved sensor allows us to monitor more effectively how changing machine settings influences the extrusion, and allows the user to change the settings with more speed and confidence. Additionally, by knowing that the Filament Maker TWO settings are optimal we can conclude that, for any strange anomalies that we encounter on the sensor, these occurrences must therefore be from inconsistencies in the material. This allows us to gain much more information about the material itself and whether it is extrudable on the system or not, and which steps might be needed in order to make the filament more extrudable. These steps include the incorporation of additives such as processing aids, chain extenders or fillers.
By capturing all these filament data (such as temperature, ovality and contamination anomalies) we can be assured that we are on the best course towards a stress-free 3D printing experience. At the end of the day, a sensor does not guarantee a better result, but it gives more insight into why a result might not be perfect and how we can go about changing it.
This is also the core message that we would like to convey here at 3devo. We might not have all the answers yet, but we love to collaborate with other likeminded innovators in order to find them. If you want to learn more about how we work with our customers as collaborators, take a look at our Co-Creation page.
Discover the Filament Maker TWO
Explore the full list of features available with our new desktop Filament Maker.
Frequently Asked Questions (FAQs)
Although both of our Filament Makers (ONE and TWO) do have a built-in filament runout sensor, this is located in the machine's hopper, monitoring the feedthrough of material. This sensor, located at the extrusion point, is focused purely on the quality of the filament - it measures filament thickness, ovality, and temperature anomolies.
In short, yes! An in-line measurement sensor is a device used in filament making to continuously monitor the diameter and quality of the filament as it is being extruded. This real-time measurement helps ensure the filament remains within specified tolerances, leading to higher quality and more consistent 3D printing results.
While standard sensors, like those from other manufacturers, typically provide sufficient resolution for basic monitoring, our Filament Extruder Sensor features a high-resolution measurement capability of up to 10-microns. This allows for more precise control and early detection of errors, ensuring even higher quality filament production.
The optical heat sensor in the Filament Sensor TWO monitors the temperature of the filament before it reaches the puller wheels. This ensures that the filament is not deformed by the puller wheels if it is still too hot and malleable. By tuning the heaters and cooling fans to perfection, this feature helps maintain the filament's shape and quality, which is a significant advancement over many other in-line measurement sensors.
The Filament Sensor TWO improves the 3D printing experience by ensuring that the filament being used is of the highest quality. With its high-resolution measurement, thermal sensing, and ovality detection, it provides unparalleled accuracy and control. This leads to fewer print failures, higher-quality prints, and a more efficient and stress-free 3D printing process.
Share this
- March 2025 (1)
- January 2025 (1)
- December 2024 (2)
- November 2024 (3)
- October 2024 (4)
- September 2024 (2)
- August 2024 (3)
- July 2024 (6)
- June 2024 (3)
- May 2024 (2)
- April 2024 (1)
- March 2024 (1)
- January 2024 (1)
- November 2023 (2)
- October 2023 (5)
- September 2023 (2)
- August 2023 (1)
- July 2023 (1)
- May 2023 (1)
- December 2022 (3)
- August 2022 (1)
- June 2022 (1)
- May 2022 (2)
- April 2022 (2)
- March 2022 (7)
- February 2022 (2)
- January 2022 (3)
- December 2021 (3)
- November 2021 (3)
- October 2021 (2)
- September 2021 (3)
- August 2021 (3)
- July 2021 (2)
- June 2021 (1)
- March 2021 (1)
- October 2020 (1)
- June 2020 (1)
- May 2020 (1)
- April 2020 (4)
- November 2019 (1)
- July 2019 (2)
- June 2019 (1)
- May 2019 (1)
- March 2019 (1)
- November 2018 (1)
- September 2018 (1)
- January 2018 (1)
- October 2017 (1)
- September 2017 (1)
- July 2017 (1)
- June 2017 (1)
- May 2017 (1)
- January 2017 (1)
- December 2016 (3)
- November 2016 (2)
- October 2016 (1)
- May 2016 (2)
- August 2015 (2)
- July 2015 (1)