Share this
Filament Maker TWO vs. Alternatives: Compare Filament Extruders
by Ellie Pritchard on Jan 16, 2025 4:27:15 PM
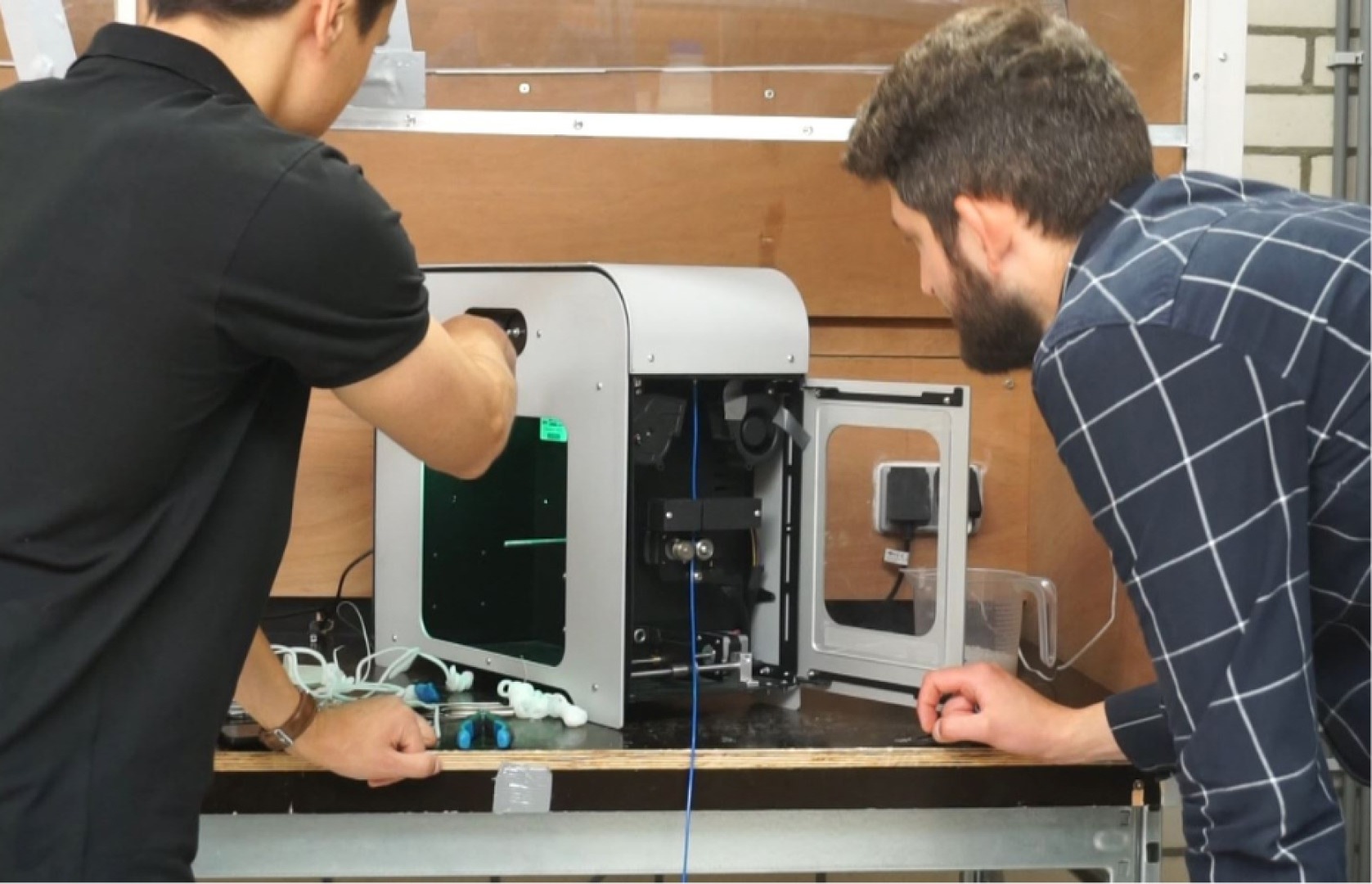
Constantly seeking better tools with which to experiment, develop, and recycle materials, the 3D printing industry moves fast. One critical component of this process is the Filament Extruder - a machine that transforms raw materials or recycled plastics into 3D printing filament. But with so many options on the market, the obvious question is "How do I know I'm choosing the right one for me?"
In this blog, we’ll compare the new Filament Maker TWO from 3devo with other popular machines, including the Filabot EX6 Extruder, Felfil Evo, Felfil Full Extrusion System, Redetec ProtoCycler, and Xplore Micro 3D Filament Line. From advanced sensor technology and user accessibility to superior heating zones and material recycling capabilities, we’ll dive into the features that matter most to educators, researchers, and commercial users.
By the end, we'll have shown why the Filament Maker TWO is redefining the extrusion process for 3D printing, offering unmatched precision, efficiency, and versatility. Whether you’re an innovator or a sustainability advocate, this guide will help you to make an informed decision for your next filament-making project.
Key Features of a Filament Extruder
To begin, let’s take a look at what key features are most important in any 3D Printing Filament Maker. Of course, it can depend on the application and intended use of the filament; is this purely a research project, to explore material parameters and behaviors, or do you know already that you’ll be working with one specific plastic for a more commercial use, for example? It is entirely up to you as the user to decide which factors are the most impactful for you, but we’ve opted to assess some specific features we believe give a good impression across all user cases.
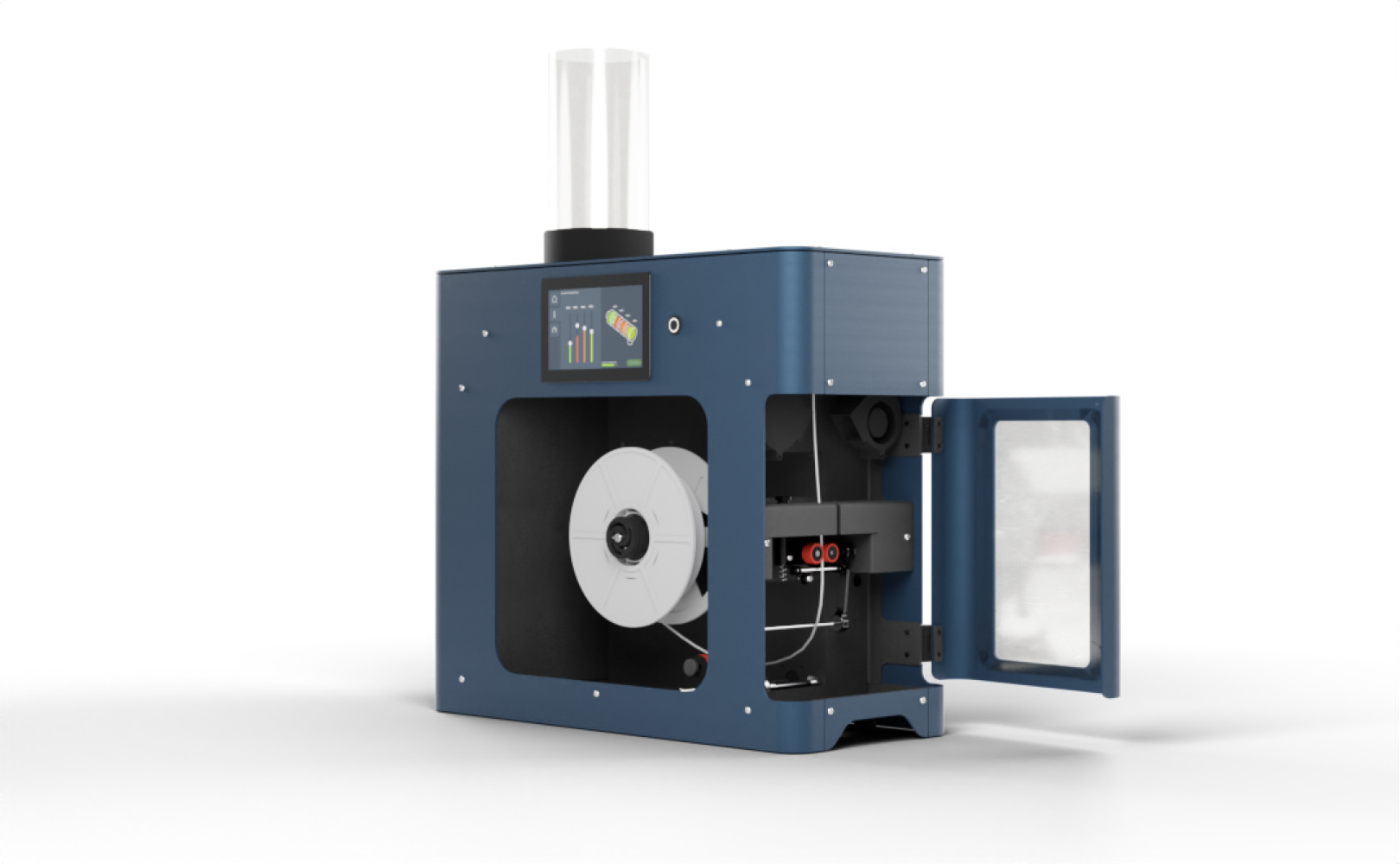
Hopper system:
The hopper system is the entry point for raw materials or plastic granules. A well-designed hopper ensures consistent feeding, which is essential for stable extrusion and high-quality filament. Inconsistent feeding can lead to clogs, uneven extrusion, and material waste.
Key Considerations:
- Capacity: Larger hoppers reduce the need for frequent refilling, ideal for long extrusion sessions – especially useful for filament makers with 3kg spool capability!
- Design: An intuitive and easy-to-load hopper saves time and reduces the risk of material spills.
- Compatibility: The ability to handle a variety of material types—virgin, recycled, or compounded—expands user flexibility.
Heating and Cooling Zones:
The extrusion process relies heavily on precise temperature control to melt and shape feedstock effectively. Having an ability to adjust heating and cooling zones allows for fine-tuning and complete user control, ensuring optimization specific to each material and desired output.
Key Considerations:
- Heating Zones: More zones provide granular control over material melting, which is crucial for high-performance or temperature-sensitive polymers.
- Cooling Zones: Effective cooling ensures consistent filament diameter and smooth surface quality.
- Temperature Range: A wide range accommodates diverse materials, from commodity plastics like PLA to advanced polymers like PEEK.
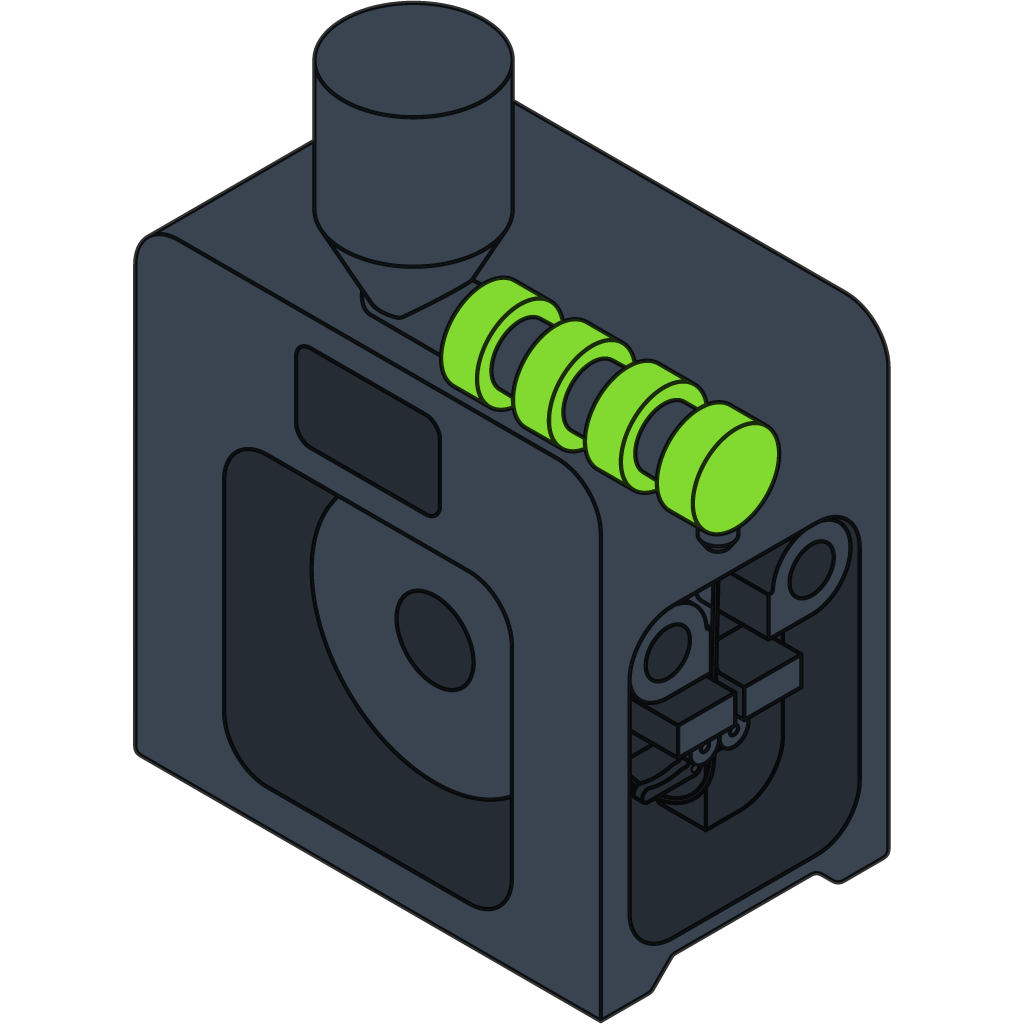
Accessibility and Maintenance:
Filament extruders are tools for innovators, educators, and researchers – and all of these people value efficiency and autonomy. A machine that is difficult to set up, use, or maintain can hinder productivity and discourage experimentation.
Key Considerations:
- User-Friendly Design: Intuitive controls and interfaces make the machine accessible to beginners and experts alike.
- Maintenance: Easy access to parts like the extruder screw, heating elements, and sensors minimizes downtime and ensures longevity.
- Modularity: Modular designs allow users to upgrade or replace components easily, extending the machine’s utility.
Sensors and Data Monitoring:
Reliable sensors and accurate data presentation are crucial to producing stable and print-quality filament. By monitoring critical parameters such as temperature, pressure, and filament diameter, users can ensure a process remains consistent and feel confident that their product meets industry standards and performance goals.
Key Considerations:
- Real-Time Monitoring: Instant feedback helps users make adjustments on the fly to avoid defects.
- Precision: Accurate sensors ensure that data reflects the actual state of the extrusion process, reducing trial-and-error.
These are just a few of the core features we believe to be the most useful as indicators of an impactful filament-making solution. Following these considerations, you can make informed decisions based on your specific needs, whether that be creating custom filaments for prototyping and research or recycling plastic waste for sustainable 3D printing.
Overview of Filament Extrusion Options
When you are exploring the possibilities of filament extrusion, it is essential to consider how different machines cater to specific needs, as some may suit certain applications more than others. Let's explore some of the popular extrusion systems on the market at the moment.
Filabot EX6 Extruder
The Filabot EX6 is marketed as a professional-grade filament extruder aimed at small businesses, labs, and R&D facilities. It can support users who need reliable but straightforward extrusion for a variety of materials.
Key Features:
- 3.2L hopper and a removable screw, allowing for manageable material handling and maintenance.
- 4 heating & cooling zones, providing decent flexibility, though less precise than advanced systems.
- Single-axis filament sensor with 10-micron resolution, offering basic diameter control but lacking advanced monitoring for process optimization.
While the EX6 boasts features such as a removable screw and decent temperature controls, it has been seen to fall short in automation and monitoring capabilities compared to competitors.
Felfil Evo Filament Extruder
The Felfil Evo is a compact and modular filament extruder aimed at hobbyists and small-scale innovators. It offers a cost-effective solution for those looking to produce their own 3D printing filament with minimal investment.
Key Features:
- Modular and open design, allowing for upgrades and customization.
- Supports a range of basic thermoplastics like PLA and ABS.
- Limited temperature control with a single heating zone, making it less suitable for advanced or sensitive materials.
In summary, this option could be suitable for hobbyists, makerspaces, and small R&D labs looking for affordability and flexibility over advanced capabilities.
Felfil Full Extrusion System
Building on the Felfil Evo, the company’s Full Extrusion System integrates a spooler and allows for continuous filament production, making it more versatile for small-scale manufacturing.
Key Features:
- Complete extrusion setup, including filament spooling.
- Larger material capacity compared to the Evo.
- Limited sensor integration, making process monitoring more manual.
This could be a good choice for innovators seeking a budget-friendly, all-in-one extrusion setup but willing to trade off advanced features for affordability.
Redetec ProtoCycler
The ProtoCycler has a focus on sustainability, combining filament extrusion with integrated plastic recycling. It is designed for users who prioritize eco-friendly practices in their 3D printing workflows.
Key Features:
- Built-in shredder for recycling plastic waste.
- Automated diameter control for consistent filament output.
- Simple controls, making it beginner-friendly but less customizable for advanced users.
This machine would most likely be useful for educators, researchers, and small businesses focused on recycling and sustainability but without clear materials project goals.
Xplore Micro 3D Filament Line
Positioned as an industrial-grade solution in a compact format, the Xplore Micro 3D Filament Line caters to users requiring high precision and durability for advanced material processing.
Key Features:
- Advanced heating and cooling zones for precise temperature control.
- High-quality components designed for intensive use.
- Requires more technical expertise to operate compared to hobbyist machines.
As a more advanced machine requiring prior knowledge and competence, this is likely to suit industrial users, high-end R&D labs, and material specialists.
Filament Maker TWO: Feature-by-Feature Comparison
Now that we’ve explored some of the filament extrusion options available, let’s dive into how the Filament Maker TWO stacks up against them in terms of key features like hopper systems, heating and cooling zones, accessibility, and sensor reliability. This detailed comparison highlights what makes the Filament Maker TWO stand out for both innovators and professionals.
Hopper System:
- Filament Maker TWO: Designed with a high-capacity hopper that supports continuous feeding, the Filament Maker TWO minimizes interruptions during extrusion. Its intuitive loading mechanism accommodates a variety of material types, from virgin thermoplastics to recycled granules, ensuring smooth operation for long sessions – ideal for producing the 3kg spools which the Filament Maker TWO is capable of doing.
- Filabot EX6: Equipped with a 3.2L hopper, the Filabot EX6 provides decent capacity for small to medium extrusion sessions. However, its design lacks advanced features such as automated feeding or spill-prevention mechanisms, which may lead to inefficiencies during operation.
- Felfil Evo and Full Extrusion System: The Felfil Evo features a basic hopper, suitable for small batches but requires frequent refilling. The Full Extrusion System improves on this slightly with larger capacity.
- ProtoCycler: While the ProtoCycler integrates a shredder for recycling, its hopper system is more focused on small-scale material input, limiting production capacity for industrial or research applications.
- Xplore Micro 3D Filament Line: Offers a robust industrial-grade hopper system, but its higher complexity can make it less accessible for users outside of advanced manufacturing or R&D environments.
Heating and Cooling Capabilities:
- Filament Maker TWO: Featuring multiple heating zones with independent controls, the Filament Maker TWO allows for precise temperature management, ideal for processing a wide range of materials, from PLA to high-performance polymers like PEEK. The adjustable fan speed at the point of extrusion also helps to ensure consistent filament diameter and quality.
- Filabot EX6: With 4 heating zones and 4 cooling zones, the Filabot EX6 provides reasonable temperature control, enabling users to process a variety of materials. However, the lack of precise adjustability or real-time monitoring means it is less suitable for high-performance polymers or temperature-sensitive applications.
- Felfil Evo and Full Extrusion System: Both systems rely on a single heating zone, which limits their ability to handle temperature-sensitive or high-performance materials. Cooling is also less sophisticated, making filament quality more variable.
- ProtoCycler: The ProtoCycler incorporates decent temperature control but is designed more for ease of use than advanced material processing. It struggles with high-temperature or complex polymers.
- Xplore Micro 3D Filament Line: Offers reliable heating and cooling capabilities but lacks the fine-tuned precision and ease of adjustment found in the Filament Maker TWO. Its focus on advanced manufacturing also creates a steeper learning curve, making it less appealing to users seeking a more accessible machine.
Accessibility:
- Filament Maker TWO: Prioritizes user experience with an intuitive interface, easy setup, and straightforward maintenance. The modular design allows for quick component replacement and cleaning, ensuring minimal downtime. One specific example is the ability for users to perform a screw pull themselves for thorough cleaning, ensuring the machine operates at peak performance. This also gives users a chance to check the behavior of their feedstock as the materials travels through the extrusion screw.
- Filabot EX6: This machine has a removable screw, allowing users to clean or replace it as needed. However, its interface and setup process are less intuitive, requiring more expertise compared to plug-and-play systems.
- Felfil Evo and Full Extrusion System: The Felfil machines are simple and modular, making them accessible to hobbyists and small labs. However, their lack of advanced features limits their appeal for professional applications.
- ProtoCycler: Focuses on user-friendliness with a plug-and-play approach, but this simplicity comes at the cost of customization and advanced functionality.
- Xplore Micro 3D Filament Line: While powerful, its industrial-grade design and complex controls require technical expertise, making it less accessible to beginners or small-scale users.
Sensor Reliability:
- Filament Maker TWO: Equipped with a cutting-edge 3-axis filament sensor that monitors temperature, pressure, and filament diameter in real-time. By measuring the filament from three sides, the sensor can detect any ovality, ensuring the filament maintains a uniform round shape. This results in higher quality and more reliable prints. The Filament Maker TWO also benefits from a thermal sensor, which accurately measures the filament temperature just before it reaches the puller wheels.
- Filabot EX6: Includes a basic filament sensor with a resolution of 10 microns and monitors on a single axis. While this ensures some level of process consistency, it does not detect advanced issues such as ovality or provide real-time feedback on extrusion parameters.
- Felfil Evo and Full Extrusion System: These systems lack advanced sensors, relying heavily on manual monitoring, which can lead to inconsistencies in filament quality.
- ProtoCycler: Features basic automated diameter control, which is sufficient for general use but lacks the precision required for high-performance materials or intricate applications.
- Xplore Micro 3D Filament Line: Incorporates some monitoring tools comparable to the Filament Maker TWO, but its higher cost and complexity may not justify the investment for all users.
Summary
The Filament Maker TWO strikes the perfect balance between accessibility, performance, and versatility, making it an ideal choice for researchers, educators, and businesses. The machine’s ease of use, superior sensors, and flexible design give it the edge in delivering consistent, high-quality results.
Our 3devo Edge
Whilst many filament extrusion systems bring unique features to the table, the Filament Maker TWO distinguishes itself by combining advanced technology, user-focused design, and unparalleled versatility. Here’s why it stands out as the ideal filament extrusion solution:
- Integrated Features for Innovators:
The Filament Maker TWO is engineered to cater to diverse needs, from rapid prototyping to large-scale material experimentation.
- The Filament Maker TWO is engineered to cater to diverse needs, from rapid prototyping to large-scale material experimentation.
- Its multi-zone heating system ensures precise temperature control, enabling users to process a wide range of materials, including advanced polymers like PEEK and PEKK.
- An intuitive hopper system supports uninterrupted extrusion, making it easier to work with bulk materials or conduct long extrusion sessions.
- Enhanced Usability for All Experience Levels:
Designed with users in mind, the Filament Maker TWO balances industrial-grade performance with accessibility:
- Simple Setup: Plug-and-play functionality ensures that even first-time users can get started quickly.
- Ease of Maintenance: Modular components allow for effortless cleaning and repairs, minimizing downtime.
- Intuitive Interface: Real-time feedback from advanced sensors provides clear guidance, reducing the guesswork involved in filament extrusion.
- Superior Sensor Technology for Reliable Results:
The Filament Maker TWO’s sensor suite is a game-changer:
- Real-time monitoring of temperature, pressure, and filament diameter ensures consistent quality.
- Automatic adjustments during extrusion help eliminate common defects like inconsistent diameters or air bubbles.
- Users can rely on the machine to handle both standard and experimental materials with minimal manual intervention.
- Sustainability and Flexibility:
As sustainability becomes a growing priority, the Filament Maker TWO excels in supporting recycling initiatives:
- Capable of processing recycled plastics into high-quality filament, it empowers users to minimize waste and reduce costs.
- Its adaptability to new material formulations makes it ideal for researchers working on eco-friendly or innovative polymers.
- Designed for Collaboration and Growth
3devo goes beyond just providing a machine:
- Project Partnerships: Customers gain access to a team of material specialists ready to assist with unique challenges or ambitious projects.
- Educational Support: Universities and labs benefit from expert guidance to maximize the machine’s potential.
- Future-Proof Design: With modular upgrades and firmware updates, the Filament Maker TWO evolves alongside user needs.
The Bottom Line
The Filament Maker TWO isn’t just a tool; it’s a versatile platform that empowers innovators to push the boundaries of 3D printing and material recycling. Its combination of advanced features, user-friendly design, and sustainability focus sets it apart as a great choice for researchers, educators, and businesses.
Real-World Applications of 3devo Filament Makers
From recycling plastic waste for sustainable 3D printing to advancing material research in aerospace and medical fields, the 3devo filament extrusion process has empowered innovators across industries. For example, Lattice Medical uses our original Filament Maker ONE to create biomedical implants, whilst AZ3D leverages the versatility of the technology to process notoriously challenging waste MJF powder into FDM filament. From a wider scope, organizations such as the European Space Agency trust 3devo’s solutions for advanced material experimentation. Take a look at the full range of our customer success stories on our Case Studies page.
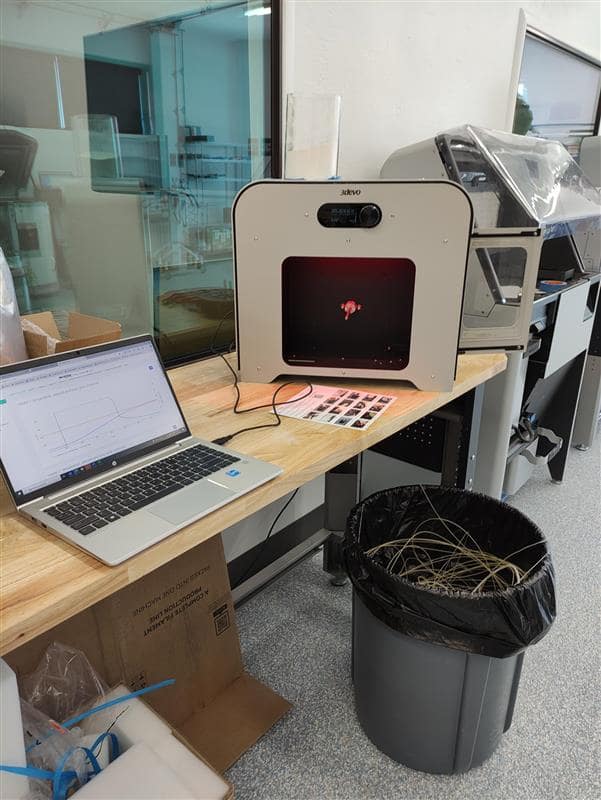
Conclusion
Choosing the right filament extruder is essential for innovators, researchers, and businesses aiming to push the boundaries of 3D printing and material recycling. Whilst there are a few different options available, the 3devo Filament Maker TWO stands out with an unmatched combination of precision, versatility, and user accessibility.
Whether you are creating high-performance filaments for industrial applications or experimenting with sustainable materials, the Filament Maker TWO delivers consistent results backed by advanced technology and a user-centric design.
Discover our new Filament Maker TWO
Learn more about our new FM2 - a powerful filament extruder and filament research platform in one machine.
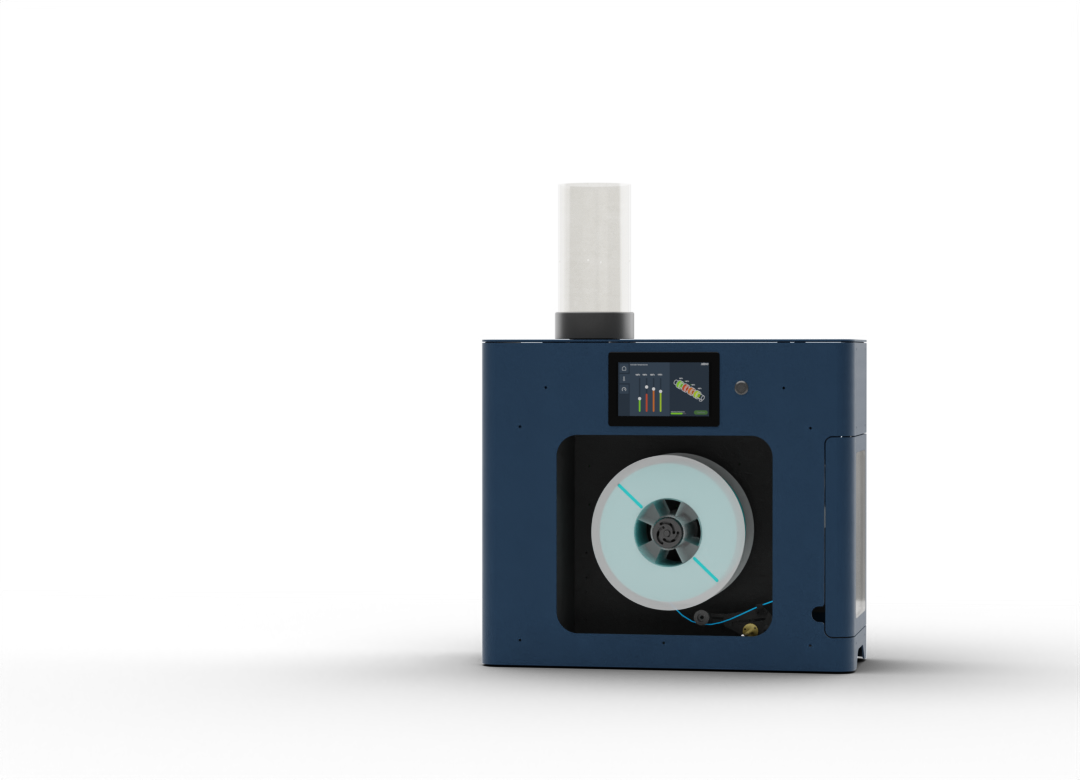
Frequently Asked Questions (FAQs)
The Filament Maker TWO builds on the success of the Filament Maker ONE with improved features, including enhanced extrusion precision, greater compatibility with composite materials, and the ability to produce larger 3kg spools, making it ideal for both research and large-scale production applications.
Absolutely! The Filament Maker TWO is designed to process recycled plastic waste, allowing users to create high-quality filament for 3D printing. It’s part of our full recycling solution, which includes the GP20 Plastic Shredder for on-site material preparation.
3devo offers comprehensive support through our team of Materials Specialists, who provide training, technical assistance, and personalized guidance to ensure your projects are successful. Our experts work closely with customers to optimize materials and processes.
The Filament Maker TWO is versatile and benefits industries ranging from research and development (e.g., composite material innovation) to education, sustainable manufacturing, and creative fields like art and design. Its adaptability makes it suitable for diverse applications.
You can follow us on social media, subscribe to our newsletter, and visit our website for the latest updates, insights, and success stories from 3devo and our customers. Don’t forget to check out our blog for deep dives into our projects and industry trends!
Share this
- March 2025 (1)
- January 2025 (1)
- December 2024 (2)
- November 2024 (3)
- October 2024 (4)
- September 2024 (2)
- August 2024 (3)
- July 2024 (6)
- June 2024 (3)
- May 2024 (2)
- April 2024 (1)
- March 2024 (1)
- January 2024 (1)
- November 2023 (2)
- October 2023 (5)
- September 2023 (2)
- August 2023 (1)
- July 2023 (1)
- May 2023 (1)
- December 2022 (3)
- August 2022 (1)
- June 2022 (1)
- May 2022 (2)
- April 2022 (2)
- March 2022 (7)
- February 2022 (2)
- January 2022 (3)
- December 2021 (3)
- November 2021 (3)
- October 2021 (2)
- September 2021 (3)
- August 2021 (3)
- July 2021 (2)
- June 2021 (1)
- March 2021 (1)
- October 2020 (1)
- June 2020 (1)
- May 2020 (1)
- April 2020 (4)
- November 2019 (1)
- July 2019 (2)
- June 2019 (1)
- May 2019 (1)
- March 2019 (1)
- November 2018 (1)
- September 2018 (1)
- January 2018 (1)
- October 2017 (1)
- September 2017 (1)
- July 2017 (1)
- June 2017 (1)
- May 2017 (1)
- January 2017 (1)
- December 2016 (3)
- November 2016 (2)
- October 2016 (1)
- May 2016 (2)
- August 2015 (2)
- July 2015 (1)