Share this
How To Make Polycarbonate Filament
by 3devo on Dec 12, 2016 4:49:00 PM
Polycarbonate (PC) is a widely used strong, tough, stiff and durable thermoplastic polymer. Polycarbonate is used widely in construction, eyewear, consumer electronics, food packaging and the automotive industry (headlights, interiors). It can be transparent, be an electrical insulator and is known to have good thermal resistance and very good impact resistance. There are hundreds of grades of PC varying from filled variants (carbon, carbon fiber, glass, fiber) to blends (PET, PBT) to alloys (with ABS, Acrylics). Inherently polycarbonate may have low scratch resistance and low long term UV resistance but this can be ameliorated by blends or additives (or by applying coatings to the final product).
There are optically clear grades specifically for things such as safety glasses and grades that are flame retardant. If something needs to have high strength and impact resistance while being lightweight polycarbonate is often at the top of everyone’s list. If additionally it needs to be an insulator or have high optical clarity it is often the material of choice. Blow molding, injection molding and extrusion are all done with PC. Controversially polycarbonate is manufactured using bisphenol A. Even though many standards authorities consider the material safe for food contact applications there has been a consumer backlash against products in food contact applications that may contain bisphenol A.
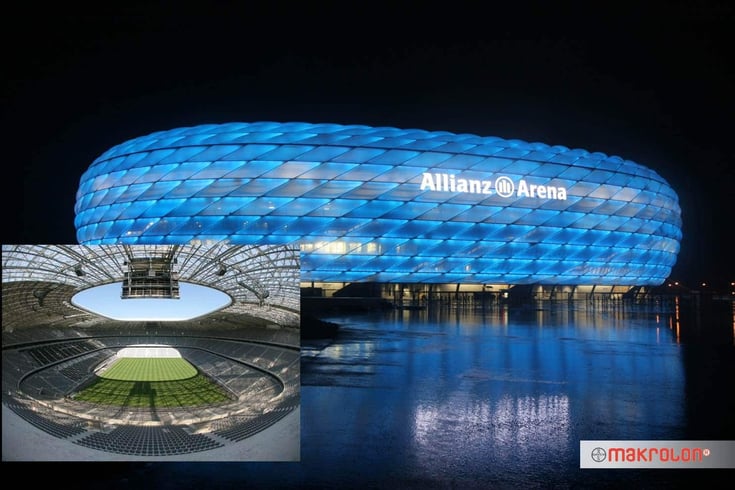
Covestro’s Makrolon polycarbonate sheets are used in outdoor applications such as the cladding for the Allianz Arena.
There are a whole host of polycarbonate manufacturers including Sabic, Celanese, Quadrant, Schulman, ChiMei, Teijin, DSM, Covestro (formerly Bayer Material Science), Ineos, Asai Kasei, Lehmann & Voss, Mitsubishi and many others. Due to this polycarbonate is known under many brand names such as Lexan, Makrolon, and Cycoloy.
For many industries PC is a mainstay of their industrial plastics usage. With many grades being made and developed (because the material is so compatible with many other plastics) there is continual development in the Polycarbonate market as well. We’ve noted a high interest in PC from certain customers due to their high usage of the material. Due to this we’ve been dialing in the material and extruding it on the 3devo Next Filament Extruder.
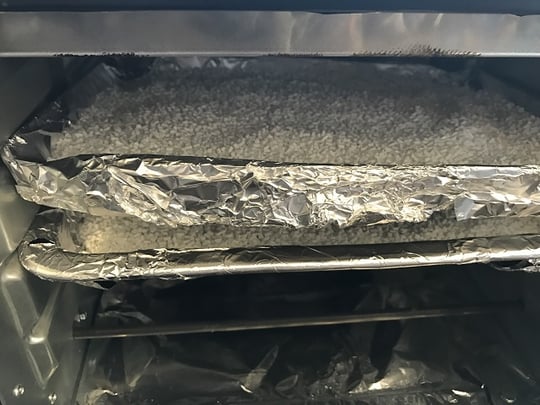
Drying polycarbonate granules is an absolutely essential step when trying to make filament.
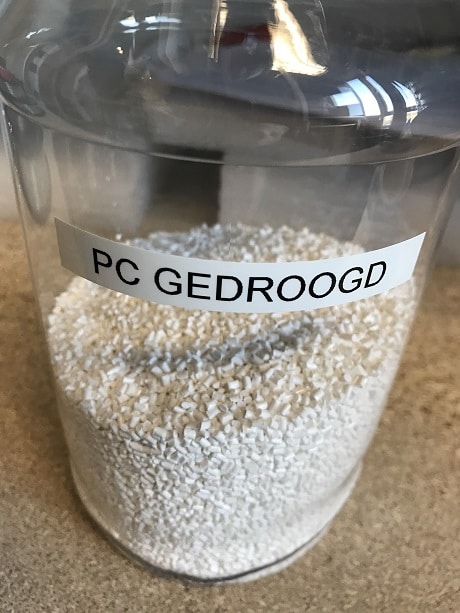
We store our polycarbonate granules in airtight containers.
What we’ve found is that drying out polycarbonate before use is absolutely essential. Drying has a huge impact on the process-ability of the material. The surface and the brittleness of the material are adversely affected if the material is not sufficiently dry. Depending on the grade an additives five hours at 110 Celsius is recommended. With some grades longer drying times or drying times at a higher temperature such as 120 may be better.
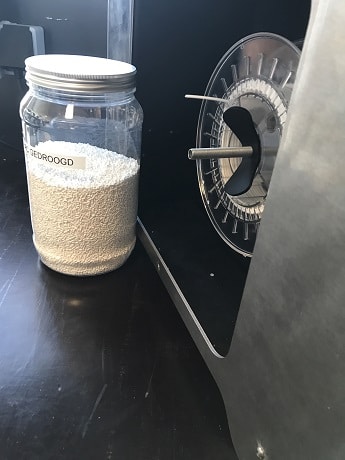
One of our test filament extruders while making polycarbonate filament.
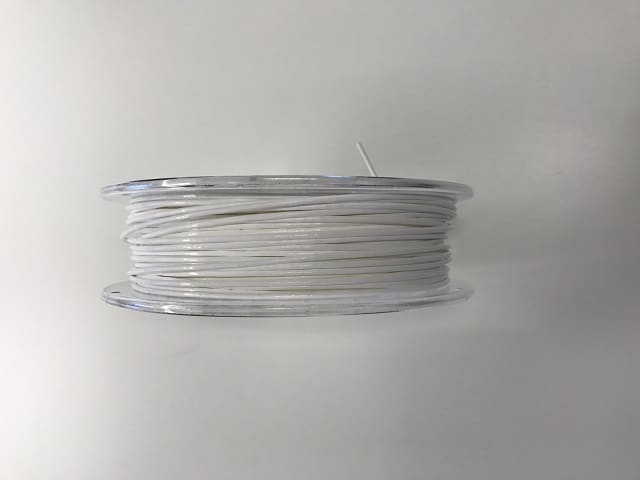
A roll of poly-carbonate 3D printing filament made on a 3devo filament extruder
Our Polycarbonate filament performs well and are waiting to see what our customers will develop with this material.
Share this
- March 2025 (1)
- January 2025 (1)
- December 2024 (2)
- November 2024 (3)
- October 2024 (4)
- September 2024 (2)
- August 2024 (3)
- July 2024 (6)
- June 2024 (3)
- May 2024 (2)
- April 2024 (1)
- March 2024 (1)
- January 2024 (1)
- November 2023 (2)
- October 2023 (5)
- September 2023 (2)
- August 2023 (1)
- July 2023 (1)
- May 2023 (1)
- December 2022 (3)
- August 2022 (1)
- June 2022 (1)
- May 2022 (2)
- April 2022 (2)
- March 2022 (7)
- February 2022 (2)
- January 2022 (3)
- December 2021 (3)
- November 2021 (3)
- October 2021 (2)
- September 2021 (3)
- August 2021 (3)
- July 2021 (2)
- June 2021 (1)
- March 2021 (1)
- October 2020 (1)
- June 2020 (1)
- May 2020 (1)
- April 2020 (4)
- November 2019 (1)
- July 2019 (2)
- June 2019 (1)
- May 2019 (1)
- March 2019 (1)
- November 2018 (1)
- September 2018 (1)
- January 2018 (1)
- October 2017 (1)
- September 2017 (1)
- July 2017 (1)
- June 2017 (1)
- May 2017 (1)
- January 2017 (1)
- December 2016 (3)
- November 2016 (2)
- October 2016 (1)
- May 2016 (2)
- August 2015 (2)
- July 2015 (1)