Share this
From Concept to Creation: The Story of Building the Filament Maker TWO
by Benjámin Beregszászi on Nov 14, 2024 2:10:14 PM
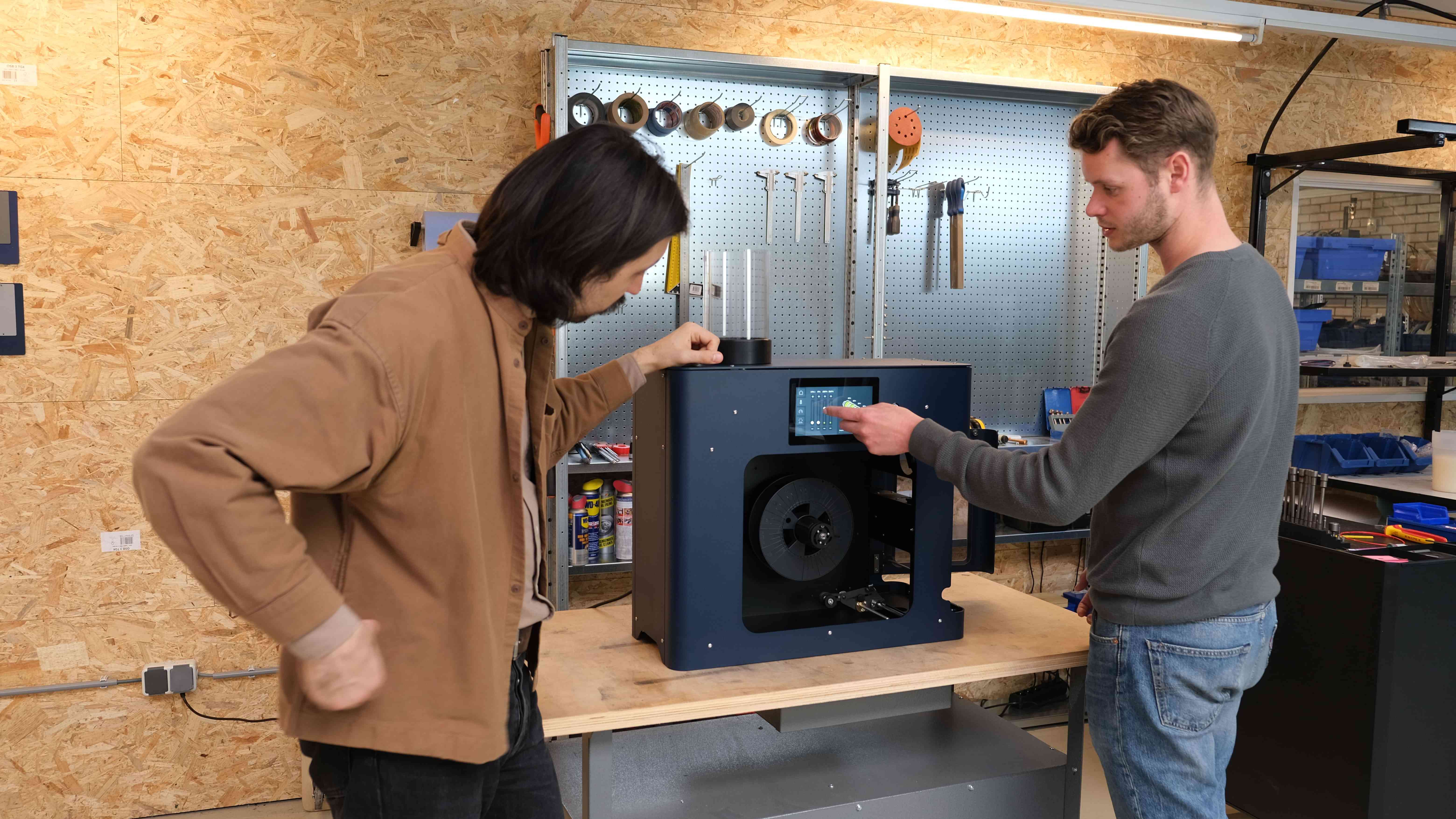
Creating the Filament Maker TWO was no simple refresh; it was a ground-up transformation. What started as a vision to improve on the original Filament Maker ONE quickly became a deep dive into hardware upgrades, new tech, and customized solutions. We weren't just building a machine—we were designing an experience that would empower users with more data, more control, and a whole new level of serviceability.
With a talented team and a touch of "shoot-for-the-stars" ambition, we tackled everything from circuit boards to filament sensors, crafting a machine that’s smarter, stronger, and ready to make a mark in 3D printing.
Rethinking the Core: Filament Maker TWO Development
When we began designing the Filament Maker TWO, it was more than just an upgrade—it was a chance to start afresh. With the original Filament Maker, we’d created a solid machine, but there were constraints we’d had to work around. This time, we wanted to rethink everything, pushing the limits of what a filament maker could be.
With the Filament Maker TWO, each new feature had the potential to influence others, creating a complex web of interconnected components that needed to work seamlessly together. The goal was to level up the machine in every way possible: from data tracking and internal monitoring to improving the precision and repeatability of every extrusion. This wasn’t just about making a machine; it was about building something that could give users a clear view of what’s happening inside, allowing for fine-tuned control and valuable insights.
Customer feedback was a major driver of our design decisions. We drew insights from support tickets, user surveys, and countless conversations with our customers to ensure we were tackling the real-world challenges they faced. From better data tracking to enhanced repeatability, every feature of the Filament Maker TWO reflects the feedback we received, creating a machine that’s as responsive to user needs as it is robust in its capabilities.
As the project scaled up, so did our team. Where the first Filament Maker was developed by a core group of a few engineers, the Filament Maker TWO required a team of close to a dozen, including some of the same minds who had worked on the original machine. Scaling up presented its own challenges—suddenly, we were coordinating a larger team, finding ways to work smoothly and align on the project’s ambitious goals. It was a classic case of aiming for the stars; while we may not have reached every goal right away, we’re incredibly proud of the Filament Maker TWO and everything it’s made possible.
In many ways, the Filament Maker TWO represents the best of 3devo’s journey: listening to users, investing in innovation, and building a machine that’s ready for the future. It’s a powerful step forward for our team and for everyone who’s been part of our community from the start.
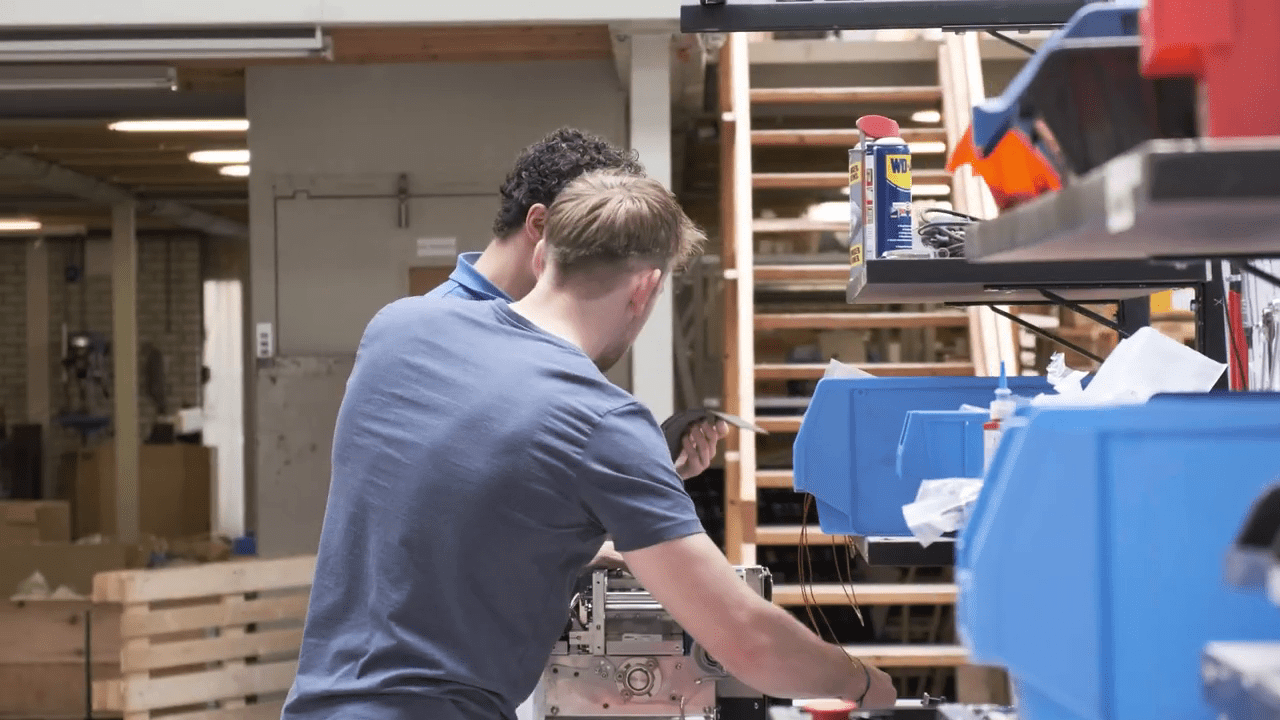
The Brain Behind the Machine: Custom PCBs
The Filament Maker TWO marks a significant upgrade, not just in hardware, but in its digital “brain.” Unlike the original Filament Maker, which used simple microcontrollers, the Filament Maker TWO is powered by an integrated computer system with custom-built PCBs. This shift enables the machine to be smarter, more capable, and prepared to grow with users over time.
Our goals for the Filament Maker TWO required more than just a basic PCB update—we needed a board design with the flexibility and power to handle next-level features. So, we chose to build our own boards in-house, ensuring they could handle increased functionality, including a more intuitive interface, filament sensor, and data capture. Each board was rigorously tested to perform across different scenarios, supporting robust data logging and allowing for future remote updates. This enhanced system provides users with more control over their processes and offers detailed insights they can use to refine their setups.
Data plays a central role in the Filament Maker TWO. The added feature of remote updates means the machine is future-ready, allowing us to push software upgrades and new functionalities as they become available, without requiring hardware changes. This level of adaptability makes the Filament Maker TWO a long-term tool for innovation. This future-proof approach ensures consistency and compatibility with current systems but leaves space for new possibilities.
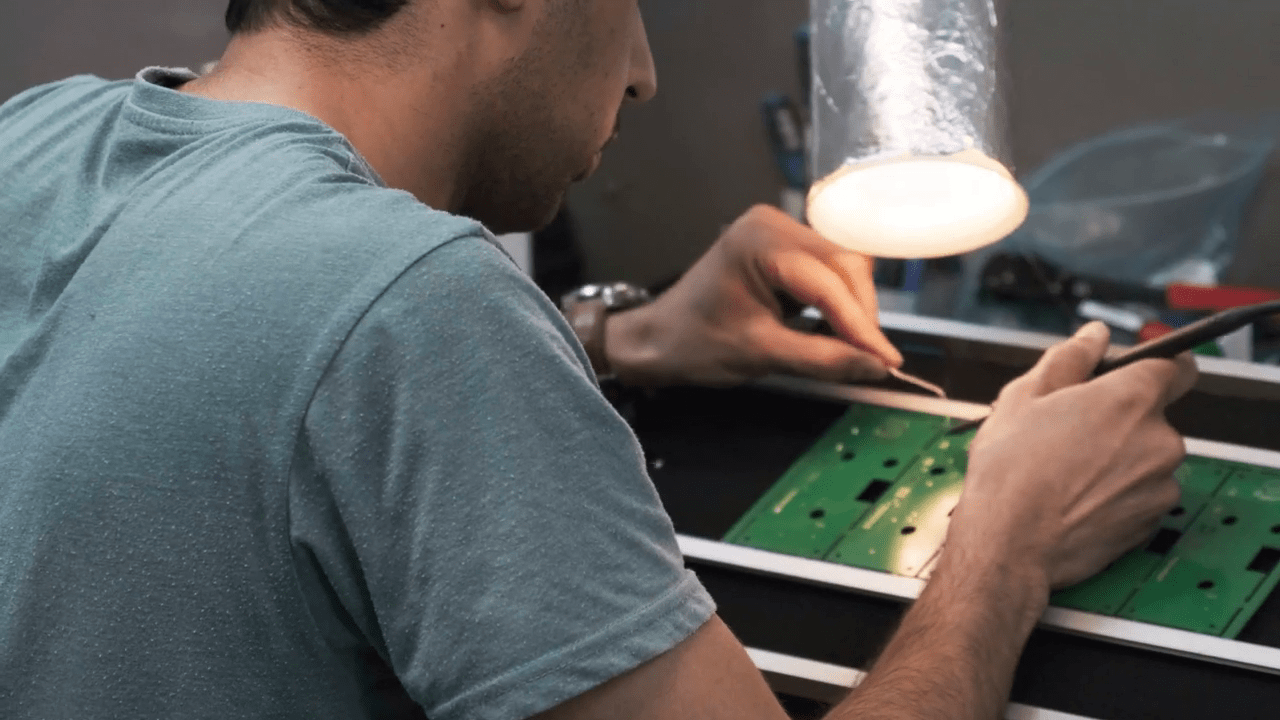
Precision in Every Layer: Crafting the Filament Sensor
Creating the Filament Maker TWO’s filament sensor was an ambitious project. Our team wanted to build a sensor capable of providing precise measurements and real-time feedback, but this wasn’t your typical off-the-shelf setup. Each component of the sensor—from the board to the camera and even the mirrors—was selected and configured by our engineers, with another team member pulling it all together. It was a truly collaborative effort, but it also came with some unique challenges.
In general, camera manufacturers tend to be cagey about their documentation, and the software support available wasn’t exactly comprehensive. We had to get creative, testing various configurations, adjusting software parameters, and studying documentation from similar devices. Since no one had ever used this specific camera, with this board, in this exact way, there were no established methods to follow.
To overcome this, our team dove into research, combing through how other projects had used similar technology and even reviewing open-source code for guidance. Without any standardization to fall back on, nearly every aspect had to be customized. We adjusted angles, fine-tuned the mirrors, and worked with our software engineers to create a system that could reliably capture and process filament data.
The result is a truly custom filament sensor, designed from scratch and optimized for the Filament Maker TWO. While this level of customization was challenging, it allowed us to create a sensor that meets our exact specifications, providing the real-time, high-accuracy data our users need.
-min.jpg?width=700&height=443&name=Sensor%20(1)-min.jpg)
Streamlining Production
Building the Filament Maker TWO wasn’t just about adding new features or giving it a slicker look—it was a whole new set of challenges. This machine was designed to elevate filament extrusion and recycling capabilities for our customers, but to make that happen, we had to revamp our entire production process.
When we started work on the Filament Maker TWO, we knew we’d have to rethink our production approach. 3devo is still a tight-knit company, with a compact Production Team that doesn’t have endless resources or space. To make production efficient and scalable, we redesigned our in-house production line to be streamlined and flexible, without compromising the craftsmanship that goes into every machine. This wasn’t just a matter of rearranging workstations; it was a complete overhaul of our space and workflow.
One big shift was deciding which components we’d build in-house and which we’d outsource. Balancing in-house quality with outsourced efficiency was crucial, especially for a machine that’s both heavier and more complex than the original Filament Maker. With the Filament Maker TWO weighing in heavier than its predecessor, safety became a top priority across the production line. We had to ensure that the space, tools, and sub-assembly flow were organized down to the last detail, leaving no room for hiccups or safety risks. The entire setup—from space allocation to logistics—was designed so each step of production moves smoothly, without interruptions or wasted time.
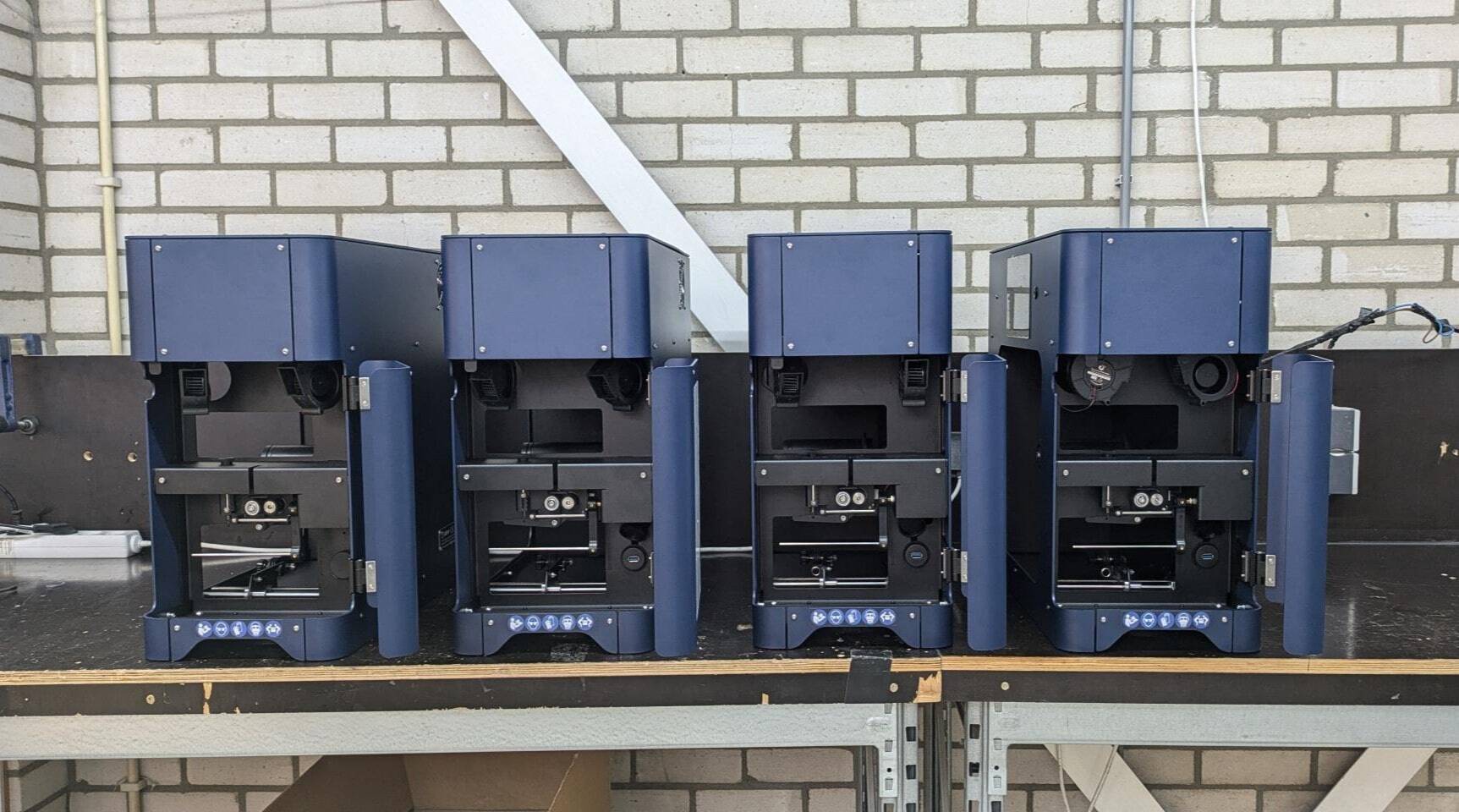
Engineered to Last
Scaling up production for the Filament Maker TWO meant more than just speeding up the assembly line. We had a clear goal: cut production time in half. Achieving that required us to rethink our assembly methods and introduce efficiencies wherever possible. Each sub-assembly step was re-evaluated, allowing us to ramp up production without sacrificing the quality or detail we pride ourselves on.
The assembly process is now built with the future in mind, making it easy to scale as demand grows. Every step is purposeful, from modular components to streamlined workflows, ensuring that each Filament Maker TWO comes together with precision and consistency. The Production Team’s experience has allowed us to develop an assembly process that’s not only faster but also more adaptable to potential upgrades or iterations.
While production efficiency was a priority, we knew that serviceability had to be at the core of the Filament Maker TWO’s design. Customer feedback guided us in making some big changes to how easy the machine is to service and maintain. Through improved inter-departmental communication, we collected real-world insights from users and translated those into features like the screw removal kit and a simplified die head. We wanted users to feel like the machine fit together as intuitively as a LEGO set—no tricky assembly, just smooth operation.
We also developed a standardized quality check for each machine, ensuring that every Filament Maker TWO meets our serviceability standards before leaving the floor. A new alignment fixture and clear quality procedures help us deliver machines that are easy to service right from the start.
Conclusion
The Filament Maker TWO embodies 3devo's commitment to continuous innovation and the needs of our users. This machine is the result of careful planning, collaboration, and an unwavering focus on quality at every stage. From the highly customized PCB system to the smart filament sensor and streamlined serviceability, each feature was crafted to enhance the user experience and support future growth. We see the Filament Maker TWO not just as a product but as a trusted partner for those aiming to push boundaries in 3D printing and recycling. And this is only the beginning of where we can go, together.
Discover our new Filament Maker TWO
Learn more about our new FM2 - a powerful filament extruder and filament research platform in one machine.
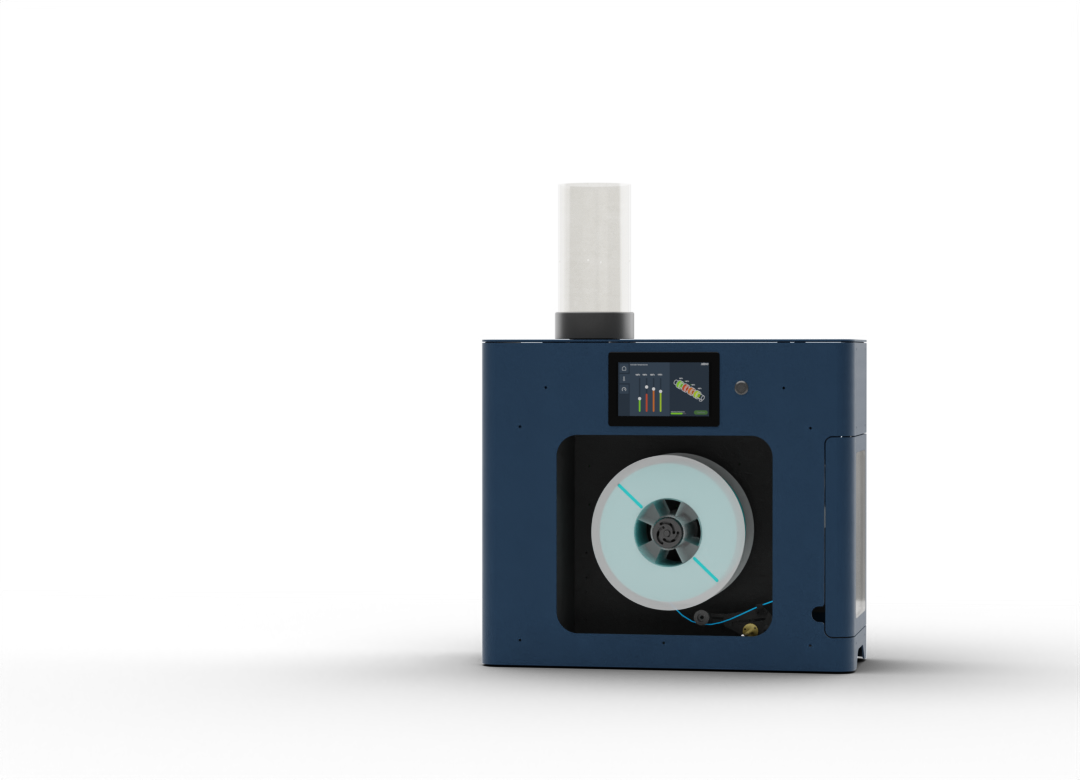
Frequently Asked Questions (FAQs)
The Filament Maker TWO is a complete transformation from the Filament Maker ONE. It features upgraded hardware, including a custom-built PCB system, advanced data tracking, and an integrated filament sensor. These improvements provide users with better control, more detailed insights, and enhanced serviceability, making the Filament Maker TWO a more powerful and user-friendly machine.
The custom-built PCB system acts as the "brain" of the Filament Maker TWO, enabling more precise monitoring and data logging. Unlike traditional microcontrollers, our integrated computer system supports remote updates and future software enhancements, making it a machine that can adapt and grow over time without requiring new hardware.
Customer feedback was central to the design of the Filament Maker TWO. Insights from support tickets, surveys, and conversations allowed us to address real-world challenges. This feedback influenced improvements in data tracking, repeatability, serviceability, and even specific design features, ensuring that the machine meets the practical needs of users.
The filament sensor in the Filament Maker TWO provides precise, real-time measurements that help users monitor and adjust the extrusion process for consistent results. Designed from scratch by our team, this sensor is highly customized, providing the accuracy and data users need to refine their setups and achieve optimal filament quality.
To meet the increased complexity of the Filament Maker TWO, we re-engineered our production workflow to accommodate the machine’s added features and size. This included refining assembly methods to improve efficiency while maintaining high-quality standards. We also optimized our workspace to handle the larger components, ensuring each machine is crafted precisely and consistently.
The Filament Maker TWO is designed with both durability and performance in mind, supporting precise control over the extrusion process and providing data insights that help users fine-tune their setups. Its enhanced hardware and intuitive interface make it a practical choice for long-term use in research, prototyping, and recycling applications, ensuring reliability across diverse projects.
Begin Your Journey Towards Sustainable 3D Printing
Start by transforming plastic waste into recyclable material with our efficient and innovative shredder, designed to empower your filament recycling journey.
.jpg?width=865&height=500&name=GP20-Shredder-Hybrid-1%20(2).jpg)
Explore More on Sustainable 3D Printing Materials
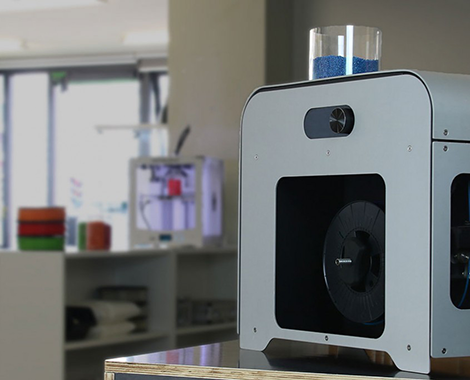
Recycle Plastic Waste
Transform plastic waste into quality 3D printing filament and join our mission for responsible innovation with 3devo's complete recycling solution.
%20-%20instasize.png?width=800&height=640&name=which-plastics-are-recyclable%20(1)%20-%20instasize.png)
Which Plastics are recyclable?
Understand different plastic types and their recyclability to make informed decisions on selecting the right material for your needs.
%20-%20instasize%20(1).png?width=800&height=640&name=PETG-e1494958102567%20(1)%20-%20instasize%20(1).png)
How to recycle PET into Filament?
Discover how PET plastic is transformed into eco-friendly 3D printing filaments on our dedicated Recycling PET page.
Share this
- March 2025 (1)
- January 2025 (1)
- December 2024 (2)
- November 2024 (3)
- October 2024 (4)
- September 2024 (2)
- August 2024 (3)
- July 2024 (6)
- June 2024 (3)
- May 2024 (2)
- April 2024 (1)
- March 2024 (1)
- January 2024 (1)
- November 2023 (2)
- October 2023 (5)
- September 2023 (2)
- August 2023 (1)
- July 2023 (1)
- May 2023 (1)
- December 2022 (3)
- August 2022 (1)
- June 2022 (1)
- May 2022 (2)
- April 2022 (2)
- March 2022 (7)
- February 2022 (2)
- January 2022 (3)
- December 2021 (3)
- November 2021 (3)
- October 2021 (2)
- September 2021 (3)
- August 2021 (3)
- July 2021 (2)
- June 2021 (1)
- March 2021 (1)
- October 2020 (1)
- June 2020 (1)
- May 2020 (1)
- April 2020 (4)
- November 2019 (1)
- July 2019 (2)
- June 2019 (1)
- May 2019 (1)
- March 2019 (1)
- November 2018 (1)
- September 2018 (1)
- January 2018 (1)
- October 2017 (1)
- September 2017 (1)
- July 2017 (1)
- June 2017 (1)
- May 2017 (1)
- January 2017 (1)
- December 2016 (3)
- November 2016 (2)
- October 2016 (1)
- May 2016 (2)
- August 2015 (2)
- July 2015 (1)