Share this
Bio PE - Extruding the Renewable Polymer
by 3devo on Jan 22, 2018 11:23:00 AM
Last year saw a huge surge in the varieties of different 3D printing materials. However, with the world’s focus on saving the environment, not many are coming from biological sources. Even though 3D prints can be recycled into other 3D prints, it is not a zero-sum outcome. With the increase in biological materials though, the end result would be just carbon dioxide and water. In this article we focus on one of these biological materials – Bio PE – and if it can be extruded using our Filament Maker.
Bio PE Summary
By definition, bio-plastics and biopolymers are the type of plastics and polymers which come from renewable biomass sources. These sources include: vegetable oils, sugarcane, starch and wheat grain. Depending on the products; the global bio-plastics market includes bio-PET, starch blends, PLA, bio-PA, bio-PE and others. Bio PE, or biopolyethylene, is simply polyethylene made out of ethanol. After a dehydration process, it becomes ethylene using these biomass sources. The final product is polyethylene, which properties mimic those of conventional polyethylene.
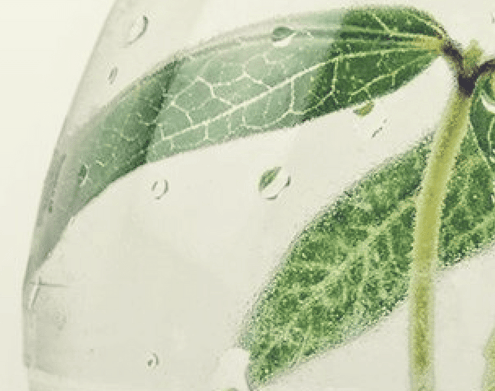
Applications
The main application for biopolymers is packaging, which makes up around 28% of the total volume shown in 2016. This includes shopping bags, food packaging, bottles and many other uses. Other uses include blow-molded hollow parts such as automotive fuel tanks, injection molded parts, tubes and other applications used in the automotive and consumer-goods industries.
Advantages & Disadvantages
According to Braskem, the world-leading supplier of Bio PE, a production rate of 200 kilo ton/year of Bio PE would require approximately 450 million liters of ethanol. This would utilize 65 million hectares of Brazilian sugar cane land to produce enough sugar to enable Braskem’s production capacity. This represents 0.02% of the Brazilian arable land. Clearly, the impact to the sugar cane food supply is quite small.
Another great advantage is that the chemical structure, applications, and recycling are identical to fossil-fuel based PE. Also do not forget that Bio PE is 100% recyclable.
All these advantages do come with one main drawback. Currently, the price of Bio PE is about 50% higher than fossil-fuel PE. In upcoming years though it should see a decrease in price when volumes increase.
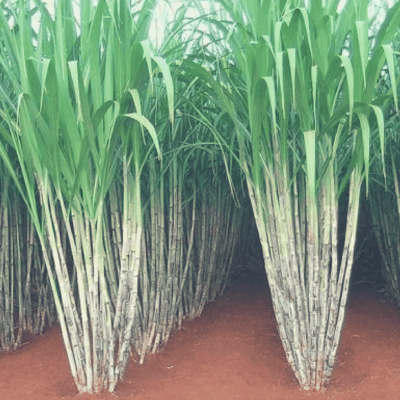
Extruding Bio PE + TMP + MAPE
Here at 3devo we were able to acquire some Bio Polyethylene (PE) SHD 7255 LSL, including 20% thermomechanical pulp (TMP) and 6% maleated polyethylene (MAPE). Take note this is just a short summary of our testing. Please visit our contact page for more information.
Preparation and Extrusion
Cleaning your filament extruder is crucial. Either a purging compound or HDPE can be used. Drying the materials was also critical. After 7 hours of drying the material doubled in moisture content over 48 hours (stored in a closed container with silica gel), it was finally ready. Three tests were conducted, using various temperatures and settings. It was interesting to see how quickly the material heated up, and fast fan cooling was vital it to handle more stress. Low temperatures also helped improve the results.
Extrusion Summary
After multiple tests, we can conclude that a Bio PE + TMP + MAPE combination can be successfully extruded with the Composer 450. Some issues include the TMP particles causing the material to get easily torn apart and the ease at which the material heats up. Cleaning also determines the best results for the final filament.
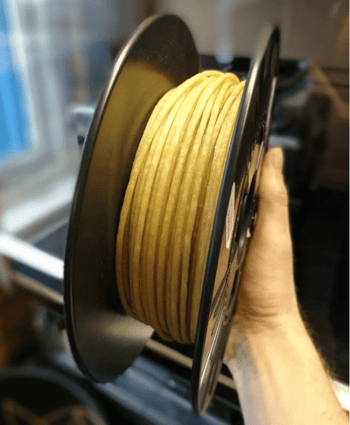
The end result of the extrusion tests
Conclusion
In the end, bio-plastics and biopolymers are definitely something to focus on in the future of 3D printing. Their unique characteristics make it great for sustainable development. Also now that extruding materials like this is possible, it will be great to see what upcoming projects will be rolling out in the years ahead.
Share this
- March 2025 (1)
- January 2025 (1)
- December 2024 (2)
- November 2024 (3)
- October 2024 (4)
- September 2024 (2)
- August 2024 (3)
- July 2024 (6)
- June 2024 (3)
- May 2024 (2)
- April 2024 (1)
- March 2024 (1)
- January 2024 (1)
- November 2023 (2)
- October 2023 (5)
- September 2023 (2)
- August 2023 (1)
- July 2023 (1)
- May 2023 (1)
- December 2022 (3)
- August 2022 (1)
- June 2022 (1)
- May 2022 (2)
- April 2022 (2)
- March 2022 (7)
- February 2022 (2)
- January 2022 (3)
- December 2021 (3)
- November 2021 (3)
- October 2021 (2)
- September 2021 (3)
- August 2021 (3)
- July 2021 (2)
- June 2021 (1)
- March 2021 (1)
- October 2020 (1)
- June 2020 (1)
- May 2020 (1)
- April 2020 (4)
- November 2019 (1)
- July 2019 (2)
- June 2019 (1)
- May 2019 (1)
- March 2019 (1)
- November 2018 (1)
- September 2018 (1)
- January 2018 (1)
- October 2017 (1)
- September 2017 (1)
- July 2017 (1)
- June 2017 (1)
- May 2017 (1)
- January 2017 (1)
- December 2016 (3)
- November 2016 (2)
- October 2016 (1)
- May 2016 (2)
- August 2015 (2)
- July 2015 (1)