Share this
All You Need to Know About PEKK
by 3devo on Jun 28, 2017 11:20:00 AM
Here at 3Devo we really enjoy trying out new polymers. Most of them have different functions and qualities that make them unique. This week we had a look at PEKK, or Polyetherketoneketone. This semicrystalline polymer, shows off both a sound structural performance in high temperature and a strong chemical resistance. These positive qualities make it very useful in various fields, from medicine to aerospace.
Before 2011, PEKK’s main use was for the production of thermoplastic composites. It was sold in limited quantities to a few small compounding companies. These companies offered PEKK in various melting processes, as well as other specialty and composite processes. However, in 2011, Arkema began industrial PEKK production making it more accessible, so let us take a closer look into what makes this polymer so unique.
Overview of PEKK
- PEKK is a part of the High Performance of Polyaryletherketone (PAEK) polymer family.
- Glass transition temperature of 162°C (323.6°F)
- The melting temperature for the PEKK homo-polymer is around 400°C
- Slow crystallization rate
- Manufacturers and distributors: Arkema, Velox, RTP and Cytec
- Brand names: Kepstan and RTP
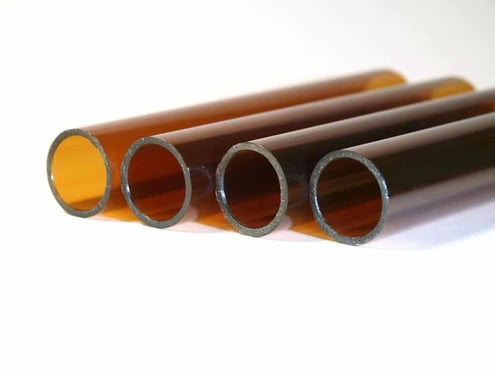
Source: ptonline
PEKK vs. PEEK
- PEKK is a part of the High Performance of Polyaryletherketone (PAEK) polymer family.
- Glass transition temperature of 162°C (323.6°F)
- The melting temperature for the PEKK homo-polymer is around 400°C
- Slow crystallization rate
- Manufacturers and distributors: Arkema, Velox, RTP and Cytec
- Brand names: Kepstan and RTP
Unique Qualities of PEKK
- High strength and toughness
- Chemical resistance
- Easy processing
- Lower moulded-in stresses
- Greater dimensional stability
- Remains transparent even at higher operating temperatures
- Improved flow characteristics (due to an extremely slow rate of crystallization)
According to Tim Spahr of Arkema’s Corporate Research in North America,
“These properties allow for lower processing temperatures and the ability to process the Kepstan® 6000 Series (one of their products) copolymers polymers as either amorphous or semi-crystalline structures, depending on processing technologies and cooling conditions.”
He also added, “They can be injection molded and extruded as an amorphous polymer without the need for quenching.”
Real World Applications
Aerospace
NASA is also not wanting to be left out of the 3D-printing world. They of course have many projects that involve 3D printing, but last year a 3D printed part received a lot of attention as part of their latest ICESat-2 project. The project aims to examine and measure changes in ice-sheet elevations, sea-ice thicknesses, and global vegetation in Greenland and the Antarctic. Stratasys had to develop a bracket for this project for the sole purpose of space travel. PEKK made its debut in space as part of the satellite, allowing for this central bracket component to be only the second 3D printed part to go into space so far.
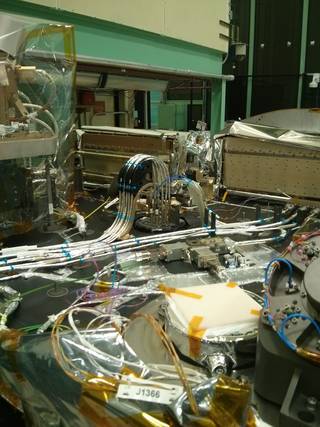
The 3D manufactured part — a black bracket holding the instrument’s fiber-optic cables (Image courtesy of NASA)
Medical
Oxford Performance Materials (OPM), always popular with their advances in developing of applications, are now using PEKK to improve infections related to artificial hips, knees, and other implanted devices. In February 2014, OPM became the first company to receive FDA clearance. This was for the manufacturing of patient-specific 3D printed polymeric implants for a line of cranial prosthesis as shown below.
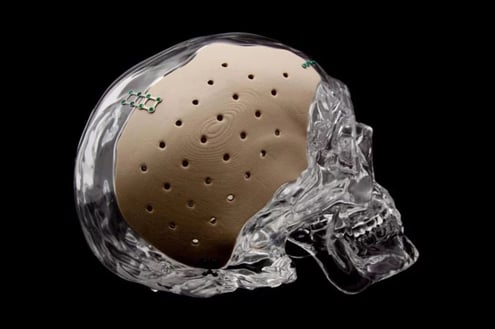
A patient-specific OsteoFab cranial implant 3D-printed by OPM. (Image courtesy of OPM)
Military
The military will also be using PEKK’s heat and chemical resistance and its ability to withstand heavy mechanical weights for various uses out in the field. For example, a plastic guard that prevents light emitted from a flashlight from exposing a soldier’s location.
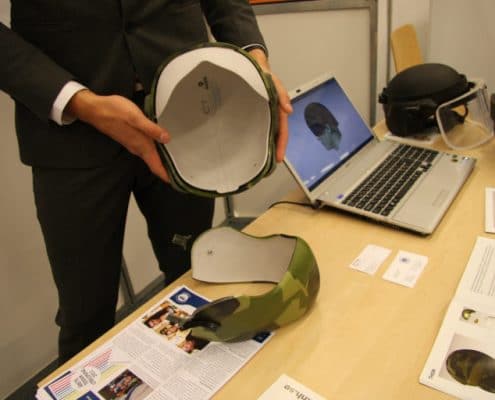
Military uses can be plentiful thanks to its robust structure (image via 3dprint.com)
Our Tests With PEKK
We decided to use a bag of the Kepstan® 6000 series copolymers, as it offers offer a low melting point and has a slow crystallization rate. From the series we used the Kepstan 6001 PF variant.
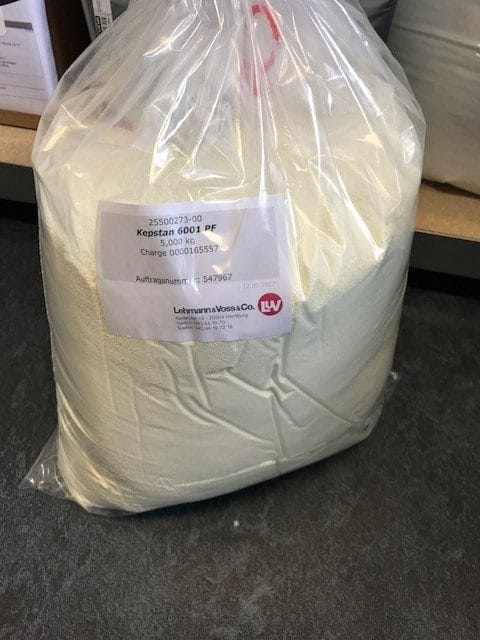
Kepstan 6001 PF powder
Like PEEK, the transition material played a key role throughout the PEKK extrusion process.
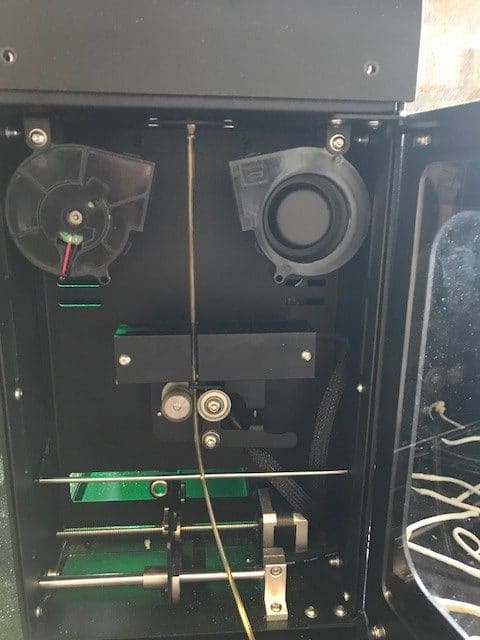
Extruding the filament on the Precision 450
This time we used a different high temperature purging compound: Asaclean PX2 grade (280°C up to 420°C), to reach the desired temperature range for PEKK (330°C up to 345°C).
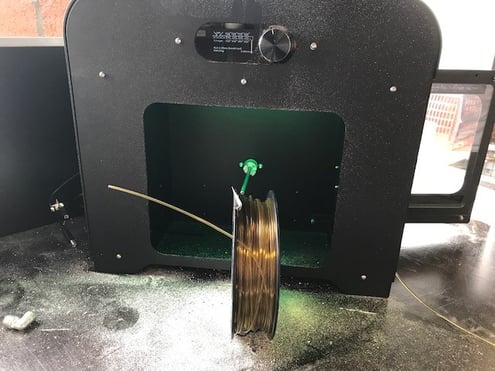
The Finished Result!
By pressure feeding the PEKK powder in the hopper of the Precision 450, the cooling fans at 30% and the screw speed at 7RPM, we had a good time with the unique filament. Successfully we extruded 2.85mm, which will be tested any time soon by one of our clients. PEKK offers a lot of advantages to say PEEK or other polymers, but it truly stands out in real-world applications.
Hopefully more industry sectors can see the potential of this useful polymer.
Share this
- May 2024 (1)
- April 2024 (2)
- March 2024 (1)
- January 2024 (1)
- November 2023 (2)
- October 2023 (5)
- September 2023 (2)
- August 2023 (1)
- May 2023 (1)
- January 2023 (1)
- December 2022 (3)
- August 2022 (1)
- June 2022 (1)
- May 2022 (2)
- April 2022 (2)
- March 2022 (7)
- February 2022 (2)
- January 2022 (3)
- December 2021 (3)
- November 2021 (3)
- October 2021 (3)
- September 2021 (3)
- August 2021 (3)
- July 2021 (2)
- June 2021 (1)
- March 2021 (1)
- October 2020 (1)
- June 2020 (1)
- May 2020 (1)
- April 2020 (4)
- November 2019 (1)
- July 2019 (2)
- June 2019 (1)
- May 2019 (1)
- March 2019 (1)
- November 2018 (1)
- September 2018 (1)
- January 2018 (1)
- October 2017 (1)
- September 2017 (1)
- July 2017 (1)
- June 2017 (1)
- May 2017 (1)
- January 2017 (1)
- December 2016 (3)
- November 2016 (2)
- October 2016 (1)
- May 2016 (2)
- August 2015 (3)
- July 2015 (1)